Laser welding is enabling dissimilar materials to be joined with increasing durability, empowering engineers to push the boundaries of technological design.
MARIE FREEBODY, CONTRIBUTING EDITOR
Laser welding finds its place in fields such as electromobility (e-mobility), aerospace, ship and rail transport, construction, the energy sector, semiconductor, consumer electronics, medical device manufacturing, and others. Its flexibility and precision make it a go-to solution even when fusing together different materials that conventional welding techniques struggle to join. This process, often referred to as dissimilar welding, is an essential part in achieving modern engineering goals.
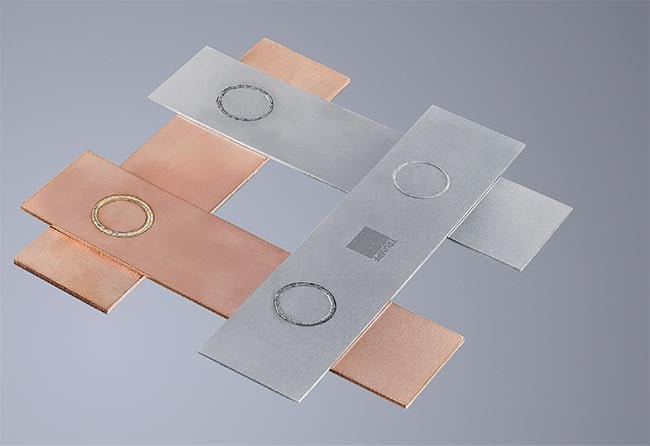
The production of batteries and electrical components for electromobility (e-mobility) applications is driving greater interest in the laser welding of dissimilar materials, such as copper and aluminum. Courtesy of TRUMPF.
Dissimilar welding enables broader design latitudes when selecting different materials that offer favorable properties, such as electrical and thermal conductivity, ductility, relative density, melting point, and hardness, but that traditionally required adhesives or mechanical means to bond together.
Although the technique shares commonalities with conventional welding, it offers unique opportunities to increase freedom of design and enable material combinations that reduce manufacturing and assembly costs, and boost component or system performance.
Welding dissimilar materials, however, involves careful consideration of laser wavelength, average power, beam profile, pulse width, and peak power. Laser system parameters must also be tailored to specific material combinations and applications.
The most significant and rapidly growing application is in the production of batteries and electrical components for e-mobility. Recent demand for electric vehicles (EVs) has surged, and welding dissimilar materials is at the core of making them more efficient and eco-friendly.
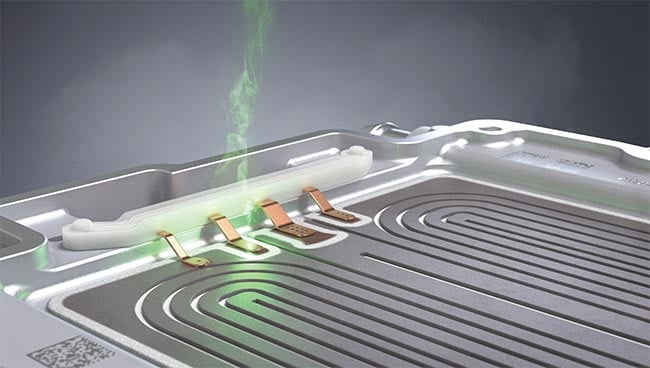
Although dissimilar welding shares commonalities with conventional welding, it is much more challenging to optimize both the quality and speed of the weld. The flexibility of laser welding systems is offering unique solutions to expand access to new applications and opportunities. Courtesy of TRUMPF.
“E-mobility has a forecast in excess of 20% for the next 5 to 10 years and consumer electronics is between 10% and 15%,” said Matthew Philpott, chief marketing and sales officer for NUBURU. The manufacture of lithium-ion (Li-ion) batteries requires the ability to weld aluminum to copper at the foil-to-tab level or for tab-to-tab welds. In cylindrical batteries, copper tabs must be welded to steel cans.
In battery pack manufacturing, cells are often already assembled and engineers must implement a design that joins the cells to deliver optimum energy. Current Li-ion cells are constructed of nickel-plated cold-rolled steel. But welding a less resistive metal, such as aluminum or copper, to the standard stainless-steel terminal of a Li-ion battery reduces its resistance and therefore less energy is wasted in thermal loss.
“Enhanced performance of EV batteries is a major factor in the steady increase in electric vehicle sales,” said Mark L. Boyle, senior manager of product engineering and applications at AMADA WELD TECH. “And better performance stems, in part, from recent developments in welding of dissimilar metals, which increases efficiency by increasing energy storage, reducing size, and preserving reliability.”
Shipbuilding offers another example where dissimilar welding is introducing unique value. The sector often uses steel-aluminum joints to optimize weight distribution, which lowers CO2 emissions and enhances stability. In particular, joining a steel hull to an aluminum superstructure reduces dead weight.
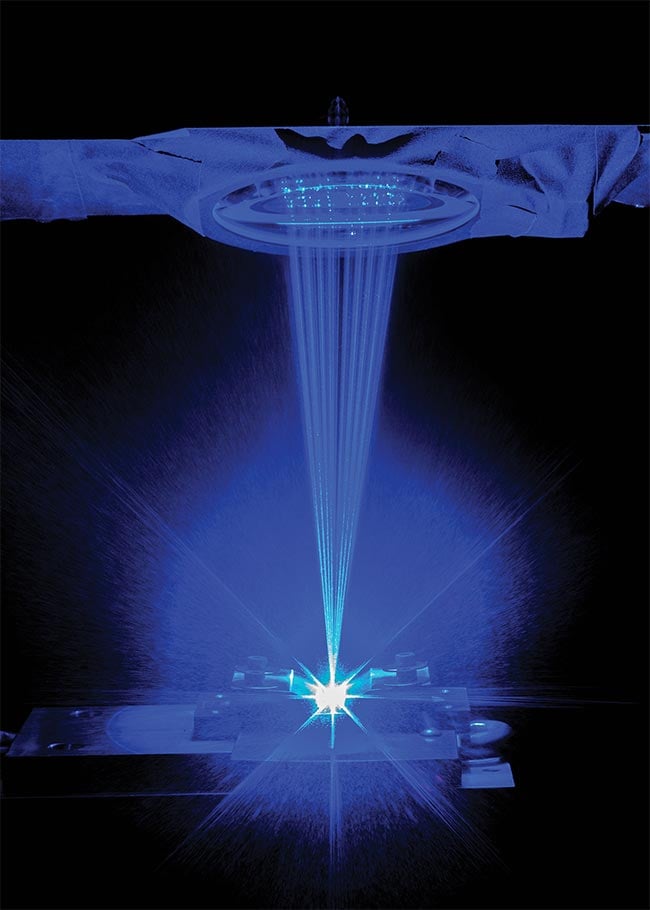
A blue laser welding copper sheets. Green and blue lasers are often more ideal for the welding of highly reflective metals, such as copper and aluminum, offering lower heat input and improved process stability >1 µm. Courtesy of NUBURU.
“In addition to reduced CO2 emissions and energy consumption, the center of gravity of the ship can be lowered through the intelligent arrangement of materials, resulting in increased shipping stability,” said Rabi Lahdo, research associate in the Joining and Cutting of Metals Group at Laser Zentrum Hannover.
Although materials with similar properties generally result in a more reliable weld, major players such as AMADA WELD TECH receive more and more requests to join dissimilar materials.
“Commercially, the choice of dissimilar materials may reduce manufacturing costs and boost the component or device performance,” Boyle said. “When that occurs, the choice of dissimilar metals can be utilized as a competitive advantage in the marketplace, delivering a better product at a lower price.”
Challenges and considerations
When fusing materials such as steel or copper with aluminum, the variations in the materials’ melting points and coefficients of thermal expansion contribute to the formation of intermediate brittle sections that can weaken joint strength.
“Metals have different melting and fusion temperatures, different light-absorption coefficients — especially at certain laser wavelengths — and different heat diffusivities. This makes it difficult to simultaneously melt them to the proper degree,” NUBURU’s Philpott said. “This is most pronounced with highly reflective
metals that may have very different
absorption coefficients in the infrared.”
The stress fields created through disparate coefficients of thermal expansion during cooling can also weaken welds, and potentially lead to joint failure. Known as intermetallic phases, these hard brittle structures form in the transition zone between the weld metal and the base material. It is a phenomenon that can plague any welding method.

A cross-section of dissimilar joints of steel and aluminum. Courtesy of LZH.
“The formation of intermetallic phases, such as FeAl2, Fe2Al5, FeAl3 for the steel-aluminum system and Cu9AL4, CuAl2, Cu4Al3 for the copper-aluminum system,
is due to the limited solubility of the elements,” said Sarah Nothdurft, head of Joining and Cutting Metals Group at Laser Zentrum Hannover. “Such phases also exhibit a significantly higher specific resistance compared to the base materials.”
Careful selection of a laser’s operational parameters, such as combining high weld speed, low heat load, and precise control over the melting process, enables engineers to mitigate some of these issues.
“While formation of intermetallic compounds is inevitable, their brittle nature is not,” said Alexei Markevitch, market development manager at IPG Photonics. “Proper process recipes can minimize the formation of these compounds and maximize their plasticity to result in structurally sound joints with higher and more stable electrical conductivity.”
Applications of Welding Disparate Materials
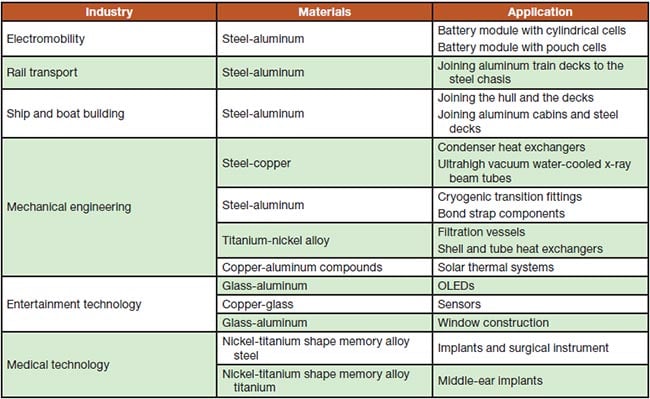
Attention to suitable mixing ratios and appropriate partner arrangement further enhances the properties of dissimilar joints. For example, an I-seam with a lap joint has proved to be advantageous. In this approach, a steel sheet is positioned on an aluminum sheet. With the aim of minimizing intermetallic phases, the weld is made through the steel sheet and only welded into the aluminum sheet.
“The resulting microstructure has a relatively low proportion of such brittle phases due to low aluminum content,” said Oliver Seffer, research associate in the Joining and Cutting of Metals Group at Laser Zentrum Hannover.
Laser parameter considerations
The choice of laser technology depends on the materials to be joined. Dissimilar joints of glass and metal may require a CO2 laser system. Welding alumina-silicate glass and various metals may benefit from a femtosecond laser system, while joining aluminum alloys and technical glasses often find success with a picosecond laser source.
The goal is to minimize heat input, eliminate spatter, improve process stability, and provide a wide process parameter window, all while welding at the highest possible speed.
“While steel alloys absorb well in near IR, even metals with high reflectivity, such as aluminum and copper, are mostly processed by 1-µm lasers,” IPG’s Markevitch said. “This is because absorption rates depend on metal temperature and phase. While at room temperature, copper and aluminum absorb ~5% at 1 µm, 40% to 50% at 515 nm, and even more for blue.”
“All absorption rates increase for heated metals, with IR exhibiting a jump at the melting point,” he said. “Molten metals absorb all wavelengths well. Therefore, a high-enough IR power density overcomes high reflectivity.”
However, in shallow conduction welding of foils or in certain weld geometries involving thicker materials, the use of high-intensity IR may result in overheating, material damage, or process instability at the rapid absorption transition point. This is why in some cases green or blue lasers are more ideal for the welding of copper, offering lower heat input and improved process stability >1 µm.
Reducing the required output intensity can weaken the turbulence in the melt pool, thus increasing process stability, said Lahdo. “Increased process stability is accompanied by a higher quality of the mixed joint, for example in the form of suppressed spatter formation.”
In keyhole welding of thicker materials, starting with micro keyholes of several hundred microns, IR lasers are often more effective than green or blue sources, resulting in smaller heat input while providing superior weld quality and greater speed.
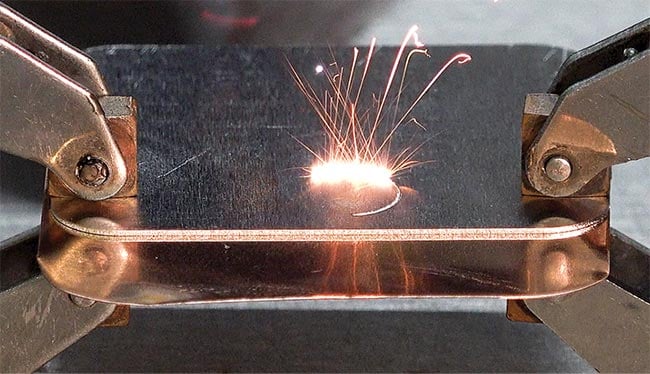
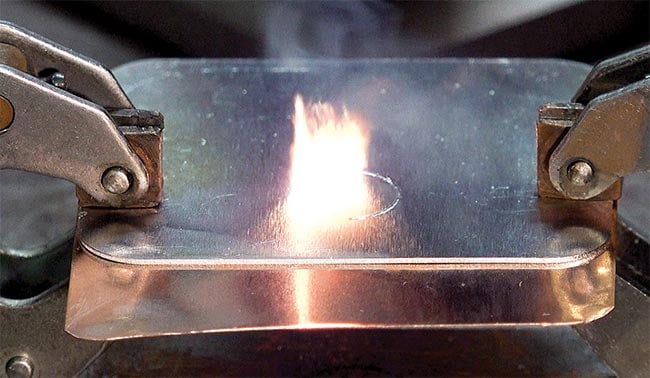
Adjustable mode beam lasers can eliminate spatter while delivering high-quality joints of dissimilar materials at speed. These lasers emit a core beam enclosed within a ring beam that can be controlled separately. Bus-bar welding applications that fuse aluminum and copper are possible with an infrared single-mode beam (top). But an adjustable mode laser (bottom) exhibits complete control of spatter by enclosing the single-mode beam within an exterior ring beam. Such systems are capable of spatter-free copper bus-bar welding at 60 m/min, with penetration >0.65 mm. Courtesy of IPG Photonics.
“The high brightness of the single-mode beam profile up to 2 kW overcomes the reflectivity of bright metals to establish stable keyhole welds, whose penetration depth can be much deeper than the weld width,” said Ken Dzurko, senior global key account manager at TRUMPF’s Laser Technology Center in Santa Clara, Calif.
“Formation of intermetallics is suppressed by rapid oscillation of the beam, which limits the time duration of the melt phase at the joint,” he said. “Moreover, the high beam brightness allows more efficient welding with a greatly reduced heat affected zone, producing high weld volume with lower average power input.”
Another factor affecting the use of laser energy is light scattering off the metal vapor plume, which is proportional to the fourth power of the wavelength. A 1070-nm laser is scattered 18× less than a 515-nm laser, and 30× less than a 455-nm laser. The high scattering of blue and green lasers off the metal vapor plume can easily negate their slightly higher absorption rate in molten material.
Today, most fabricators choose continuous-wave 1-µm lasers, which lead the way in process speed, quality, and cost reduction. But all wavelengths offer advantages depending on the situation. For example, NUBURU’s Philpott believes that a shift in wavelength to blue or green is worth exploring in applications that benefit from the increase in absorption.
“The beam delivery for blue or green lasers — such as scanners, processing heads, beam controls, and other auxiliary components — are similar to those used with near IR lasers,” Philpott said. “It is therefore very easy to convert from infrared to blue or green, with comparable methods to manage the plume so it does not create a problem due to absorption or scattering.”
Today’s laser systems are limited to a power of 3 kW at wavelengths of 515 nm, and 4 kW at wavelengths of 455 nm. Because the beam quality of blue lasers is limited, beam focusability and therefore process efficiency is also limited.
“When welding copper with laser beam wavelengths in the visible range, especially in the blue spectrum, there is currently a lack of sufficient laser beam power in combination with the required beam quality,” Lahdo said. “When generating laser radiation using laser diodes, achieving high beam quality is the biggest challenge.” In addition, visible lasers can damage optical elements more easily than IR sources, reducing lifetime and increasing costs.
Despite the challenges, Philpott expects further improvements in welding performance and value to increase as the availability and performance of blue diodes continues to improve.
“Operating a laser within the design tolerance of the optics does not provide a reliability or cost risk,” he said. “That being said, a customer may be experiencing short optic lifetimes with a particular laser supplier; however, this can happen at any wavelength if the manufacturer does not properly validate the optics prior to releasing the product.”
Laser system specializations
Continuous wave fiber lasers can join aluminum and copper by applying proper control over the beam profile. In the last decade, the development of core-ring beam profiles and more capable scanner systems has significantly improved the quality and potential of mixed joints.
During keyhole welding of copper and aluminum, the keyhole can become unstable at high welding speeds. One way to eliminate this instability is to simply weld more slowly, but this is not usually desirable.
Another approach is to use a galvo
mirror to add a wobble to the laser beam to stir the melt pool. This improves convection in the molten flow to prevent keyhole collapse. It typically results in a welding seam with superb quality but can further slow the welding process.
Typical materials thicknesses in bus-bar lap joints are from 200 to 300 µm to <1 mm,” Markevitch said. “Immediately below the thin lap joint is heat-sensitive organic electrolyte that may decompose >60 °C.
Alexei Markevitch, market development manager at IPG Photonics.
A third approach to eliminate spatter at high weld speeds is to use adjustable mode beam (AMB) lasers that emit a
core beam enclosed by a ring beam.
The core beam power and intensity
determine keyhole depth penetration,
while energy from the ring beam stabilizes the keyhole to minimize or completely eliminate undesirable spatter, cracking, and porosity.
The smallest cores are single-mode beams with a 14-µm diameter. Multimode cores are typically 50 or 100 µm in diameter, with ring beams typically measuring up to 300 µm in diameter.
“The use of core-ring fiber lasers is an active area of development in IR dissimilar laser welding, pursued by all major players,” Markevitch said. “AMB lasers with a single-mode core are chosen for their versatility, high welding speed, and inherent ability to minimize formation of brittle intermetallics.”
A 3-kW single-mode core AMB laser with an additional 3 kW in the ring is capable of spatter-free copper bus-bar welding at 60 m/min, with penetration >0.65 mm.
The same processing speed and quality is unattainable for current commercial green or blue lasers, Markevitch said.
But as he points out, welding consistency can still be affected by a variable gap between the materials or by material
contamination. With a trend toward reduced bus-bar thickness, clamping and
fixturing becomes a challenge. A lack of weld penetration may result in higher electrical resistance and low mechanical strength, while over-penetration or puncture can make the cell in an e-mobility batter a fire hazard.
“Typical materials thicknesses in bus-bar lap joints are from 200 to 300 µm to <1 mm,” Markevitch said. “Immediately below the thin lap joint is heat-sensitive organic electrolyte that may decompose >60 °C.”
Aluminum melts at 660 °C, copper
at 1085 °C, and steel alloys at 1500 °C. Two different metals with drastically
different melting temperatures need to
be melted without damaging the underlying flammable organic gel-containing lithium salts or cell elements such as seals, gaskets, and separators.
Inline process controls, based on spectral process emission or OCT can provide real-time nondestructive weld depth measurement. This enables corrective action to be taken to achieve constant penetration depth.
In the end, there is no single optimum solution to tackle all dissimilar welding challenges. “It is important to have a full tool kit of high-brightness lasers with wide parametric control range together with beam-shaping strategies and in-process validation tools, such as OCT, in order to tailor the time, temperature, and spatial control needed to meet the specific weld objectives,” Dzurko said.