Brian D’Andrade, Dr. Michael S. Weaver and Julie J. Brown, Universal Display Corp.
The world is coming to the realization that solid-state lighting offers the promise of a green energy-saving technology. And poised to fulfill that promise are white organic LEDs (OLEDs) that offer exciting new illumination forms and functionalities.
White OLEDs first appeared on the scene in the early 1990s. Since then, substantial materials development has resulted in 102-lm/W devices that deliver on the innate efficacy advantages of the technology, which can convert electrical energy efficiently into optical energy, operating at a low voltage and extracting light from organic materials.
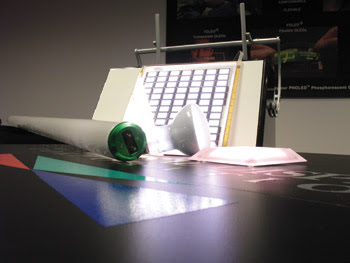
White OLEDs promise to be thin. In this picture, the white OLED dimensions on the right are compared with a fluorescent and incandescent bulb.
Phosphorescent emissive molecules are the key component for the white OLED. Phosphorescent OLEDs (PHOLEDs) were invented in 1997. The importance of this breakthrough technology is the molecules’ ability to convert nearly 100 percent of the electrical current into photons of light when optimally mixed and positioned within the nanometer-thin layers of a white phosphorescent organic LED. Optimization and precise positioning are important because these molecules must effectively capture all electrons – injected from the metallic electrodes into the organic materials – and convert their electronic energy into light, whose wavelengths and spectral power distribution are intimately affected by the white OLED optical cavity. Hence, careful selection of materials is required to ensure that electronic and optical properties work in sync to enable near 100 percent conversion of electrical energy into optical energy.
Color challenge
One hundred percent conversion efficiency is more readily achieved with monochromic devices because all light is generated by a single type of emissive molecule. However, because a white OLED typically contains three emissive molecules, balancing the charge and light within a 100-nm-thick device presents a challenge. Hence, the high-efficacy device structure enables efficient mixing of charge and photons by employing two emissive regions: cyan and orange. The cyan region consists of a host and a cyan emitter, and the orange region, of a second host doped with red and yellow emitters.
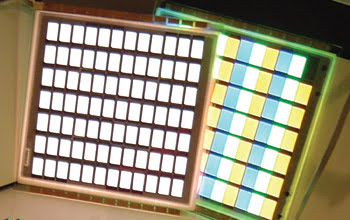
White OLEDs can have adjustable color output if the emissive elements emit different hues. Here, a single white panel is juxtaposed to a panel emitting red, green and blue.
White OLED operating voltage is another key design aspect that was reduced to obtain the highest power efficacies. Voltage losses across a single organic layer or at the interfaces of organic layers had negatively impacted previous efforts to surpass 100 lm/W at usable luminance levels, above 1000 cd/m2. By combining device design and significant chemical advances, a group of materials were matched with a device architecture that has low voltage losses; hence, the high-efficacy white OLED operated below 3.5 V, while new white devices can operate at 2.8 V. These low voltages were obtained without the use of doped transport layers because the nature of the interfaces between the organic layers was modified to prevent charge accumulation.
Hitting the DoE target
More effort is still needed to reduce the average operating voltages to near 2 V at luminance levels exceeding 2000 cd/m2. At such low voltages, one would need the white light to be generated from individual red, green and blue organic LEDs connected in series, or from a single white OLED that absorbs ambient heat. This challenge must be overcome by 2015 to exceed the 50 percent (~150 lm/W) power conversion efficiency target that the US Department of Energy (DoE) has set for solid-state lighting products.
Besides voltage reduction, the efficient extraction of light from the white OLED organic layers and substrate into air must surpass current limitations. The 102-lm/W device had an optical extraction efficiency of ~40 percent. However, other techniques for light extraction have demonstrated efficiencies near 60 percent, which potentially provides a path for 150-lm/W white OLEDs in the near future.
A major limitation to the adoption of the most efficient outcoupling extraction methods is cost. For example, a high-index (n~1.8) glass substrate is substantially more expensive than soda-lime glass, but the former enables much higher outcoupling extraction efficiencies than does soda-lime glass, which is typically used in white OLED fabrication. Eventually, economies of scale may help push the cost of specialty glass or other outcoupling fixtures to low levels, but glass manufacturers and others need incentive to produce large quantities of white OLED parts. Another route being investigated to lower cost is manufacturing on flexible thin plastic or metallic substrates.
Outstanding efficacy performance is one part of a puzzle whose pieces must fit together to drive market forces toward white OLED products. The lumen depreciation over time, or the lifetime, of white OLEDs should be sufficiently long to make them competitively priced with regard to other lighting technologies. Additionally, advances in manufacturing are still required to produce the low-cost, large-active-area devices that are necessary to generate the optical output power for illumination applications.
Nevertheless, the lighting industry is excited by the unique attributes of white OLEDs: transparency, flexibility, emission diffuseness and uniformity, thinness, ruggedness and longevity. These features imbue add-value to white OLEDs and provide convincing reasons for lighting designers to adopt the new technology. Interest in white OLED lighting products potentially extends beyond the traditional players in the lighting industry.
Manufacturers of flat panel displays are considering the technology because they possess some of the core competencies to make white OLEDs. Other companies outside the realm of displays and lighting also may join the illumination field.
Meet the authors
Brian D’Andrade is senior research scientist, Michael S. Weaver is director of PHOLED applications engineering and development, and Julie J. Brown is chief technology officer and vice president, all at Universal Display Corp. in Ewing, N.J.; e-mail: [email protected]; [email protected]; [email protected].