James Deardorff, Superior Coatings Co.
The highest-quality, longest-lasting coatings available to consumers are installed at the factory. Factory finishes are applied in a controlled environment using quality materials and highly specialized equipment. Also, prefabricated metal will never be cleaner or in better condition than when it is used to manufacture new products. The longer the original coating lasts, the higher its value to the asset and the owner.
The benefits of engineered maintenance programs have proved highly successful for extending coating life and reducing life cycle painting costs; however, inspecting, evaluating and repairing aged coatings is costly and complex. Another problem is that modern coatings aren’t specifically formulated for long-term maintenance support.
The protective coatings/nondestructive testing (PC/NDT) process is a complete life maintenance program designed to improve the durability of protective coatings. PC/NDT is based on the application of permanent foundation primer coats overcoated with expendable finish coats. Upkeep focuses on the repair or replacement of the finish coats, leaving the primer coats intact.
Recoating is scheduled by black-light-activated fluorescence, a type of nondestructive testing. This integrates an efficient “early warning” defect detection indicator (fluorescence) into the original coating formulation. Fluorescence produces an enhanced visual indicator that allows workers to monitor large or complex surfaces in relatively short periods of time and to perform proactive repairs before complete coating failure occurs and irreversible corrosion damage begins.
PC/NDT has been designed to remove the cost, production and technical barriers that historically have limited industries’ acceptance of planned maintenance. By taking care of corrosion elements on an individual basis, the process reduces the number of major coating operations and the volume of recoating materials used over the lifetime of an asset.
The development of the PC/NDT process began at Superior Coatings in 1991 under my direction. Spectronics Corp. of Westbury, N.Y., supplied a variety of UV lamps for testing and evaluating the process. Ciba-Geigy Corp. of Tarrytown, N.Y., supplied fluorescence materials and offered advice about producing the optical effects for various coating formulations. Lastly, the University of Missouri-Rolla provided formulation testing, and Rust-Oleum Corp. of Vernon Hills, Ill., supplied paints and coatings.
PC/NDT incorporates design maintainability to achieve sustainability for protective coatings. Maintainability is defined as the measure of time and effort required to return an asset to a predetermined state of performance after a failure event has occurred. Design maintainability is performed during the concept phase and is used to integrate inspection and service-ability into new products. The advantage is the improved efficiency and effectiveness of subsequent maintenance operations.
The PC/NDT maintenance program is designed with durability in mind and divides the responsibility of corrosion management between the design engineer, the manufacturer and the asset owner. Each plays a critical role.
• The design engineer develops thespecifications for the program.
• The coating manufacturer formulatesthe coatings to meet the engineer’s requirements.
• The manufacturer applies the coatingand confirms quality.
• The owner/manager has the ultimateresponsibility for the program, developing asset inventories, andscheduling and recording all maintenance operations.
The permanent foundation primer coat is formulated to respond to quality control inspection with UVA black light. During the initial application, black light ensures that the primer coat has completely covered and saturated the prepared surface. Standard intermediate and finish coats, which are not responsive to black light, are then applied. Again, coverage and proper film thickness are checked using black light. Workers test whether fluorescence emissions are shining through defects in the finish coat. If voids are found, repairs can be made before the product leaves the painting facility.
Extended service life relies on scheduled black-light monitoring to determine areas of premature coating wear. The timetable depends on the type of coating and its service environment. If low-intensity fluorescence is detected during black-light inspections, maintenance can be delayed. If high-intensity fluorescence is found, complete coating failure is imminent, and repairs should be performed as soon as possible.
Fluorescence modification
Protective coatings can be formulated or modified to produce fluorescence in several ways. Fluorescent dyes (optical brighteners) can be added to conventional coatings at recommended levels. These additives, which produce a blue-white fluorescence, are widely used in plastics and fabrics to improve appearance. Fluorescent pigments in a variety of shades can also be used. They usually are incorporated during the drawdown phase of coating formulation.
To further improve the fluorescence inspection process, light stabilizers (UV blockers) can be incorporated into the finish coats to block the fluorescence of the modified primer coat. By using the proper concentration of the fluorescent additive in the primer coat and the corresponding concentration of the light stabilizer in the finish coat, it is possible to accurately monitor the correct dry film thickness of each coat by fluorescence intensity.
Black-light UVA
The type of luminescence used in the PC/NDT program has been specifically selected to produce a strong fluorescence response when exposed to UVA energy. Black light, also known as Wood’s light, or near-UV, covers the range between 320 and 400 nm (Figure 1).
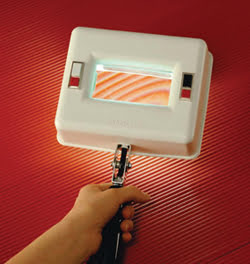
Figure 1. Solid-state black-light lamps are more powerful than traditional lamps and are excellent tools for the inspection of parts up to 50 ft away.
Historically, a major problem with the use of black-light inspection has been the inability to produce a strong fluorescence response in normal ambient light. This difficulty has been virtually eliminated, however, with the introduction of solid-state models. These lamps use transistorized power supplies and micro discharge bulb designs for increased power and intensity (Figure 1).
Solid-state black lights have a UVA projection range of 25 to 50 ft. At this distance, it can be difficult to determine exactly where the black light energy is focused (Black light UVA is virtually invisible until it comes in contact with a fluorescent material). One solution is a laser sight mounted directly on the inspection lamp, enabling long-range inspections by laser guidance.
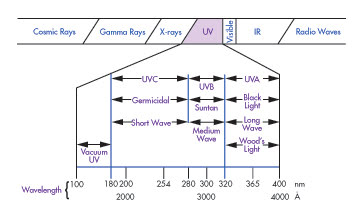
Figure 2. The UVA portion of the electromagnetic spectrum is particularly useful for inspecting coatings on manufactured goods.
Many maintenance operations require that workers inspect components in large structures or reach elevated workstations. New LED black-light flashlights provide excellent NDT inspections at ranges from 4 to 8 ft. The LED lamp is only 8 in. long and comes with a handy belt holster, allowing hands-free access to remote work sites. These lamps use rechargeable batteries that provide up to 90 min of inspection time (Figure 3).
While standard black-light inspection lamps can be used to monitor saturation and coverage of surfaces with fluorescent coatings, noncontact optical scanners can measure dry film thickness. For well over a decade, fluorescent coatings have been used to protect printed circuit boards against moisture, dust and other airborne contaminants. By factoring in fluorescence intensity and inspection spot size, dry film thickness can be accurately measured using the microvolt readings from an optical scanner.
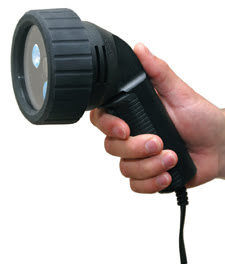
Figure 3. Newer LED black-light flashlights allow inspectors to work in inaccessible places.
Additional PC/NDT advantages
Primary corrosion sites. Virtually all man-made products contain areas that are known as primary corrosion sites. These points include welds, joints, corners, crevices, nuts, bolts and fasteners. PC/NDT performs a dual function for reducing premature failure for these locations. For welds, joints and crevices, black light ensures complete filling and saturation of voids. For joints, corners, edges, nuts, bolts and fasteners, black light shows where coatings have cured away from sharp edges and extra coats are needed to achieve proper thickness.
Conditional coating failure sites. In addition to primary corrosion sites, other areas may be subject to a high rate of corrosion due to their service location. A good example is the American automobile. Areas that are exposed to abrasion from rocks and road debris can be inspected and repaired before corrosion has a chance to start. Another factor is the extensive use of salt to de-ice roads. If manufacturers incorporated fluorescence in automotive finishes, service personnel or owners could reduce salt damage with a regimen of cleaning and recoating.
Training. PC/NDT can offer a valuable training tool for new painters learning basic techniques or for experienced applicators making adjustments for new coating formulations, specification adjustments or varied surface designs. One of the most effective training programs would involve applying fluorescent coatings in a working environment illuminated by black light only. Under true black light, there are only two specific color variations: black for nonreactive surfaces or standard nonreactive coatings, and the particular fluorescent shade of the black-light coatings. Such a working environment would be extremely efficient for applying ultrahigh-performance coatings to critical surfaces when real-time quality control is important.
Maintenance scheduling. PC/NDT provides a tremendous advantage, eliminating visible corrosion as the primary reason for planning maintenance. Black-light evaluation of excessive coating wear (as determined by fluorescence intensity) is the maintenance indicator instead. This provides facility owners with sufficient lead time to schedule maintenance and make the best use of personnel and resources.
Fluorescent cleaning. Another way to reduce corrosion costs is to keep the surface clean. The use of fluorescent cleaners aids in the removal of dirt, dust, grime and chemicals from prefabricated parts or manufactured products. First the fluorescent cleaner is applied to a surface. Coverage and saturation are verified by black light. Then the cleaner is rinsed away until all the fluorescence is gone.
Meet the author
James Deardorff is president of Superior Coatings Co. in Chillicothe, Mo.; e-mail: [email protected].