The path to successful image processing systems often is difficult because common disturbance variables such as oil or dust can render ‘intelligent’ machine vision systems powerless. Robust system approaches address those disturbances and compensate for deviations caused by the camera, optics or illumination system.
Robert Schmitt, René Hermes, Alexandre Orth and Alberto Xavier Pavim, WZL of RWTH Aachen University, Germany
Many inspection tasks, such as those of displays for the flat screen industry, can be performed only by machine vision systems. And these systems make the performance of tasks such as manual sorting inspection cheaper, easier and more reliable. However, experts emphasize that much of the potential of machine vision is not being used and that an effort must be dedicated to research and development of inspection systems to support the promising field of microsystem technology.
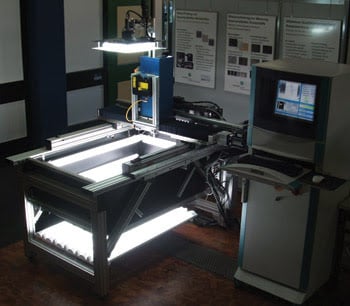
Figure 1. This machine vision system, for the inspection of fibre-reinforced composites, has been used to study the impact of spectral disturbances in the image acquisition process.
Although image processing techniques offer many promising solutions for industrial applications, they are faced with challenges. Anyone who has taken part in the integration/installation of a machine vision system knows that small changes in the environmental conditions, such as an open window or simply a little dirt, can confuse an “intelligent” system, leading to comments such as, “Why doesn’t it work? With tactile measuring techniques, there was no problem.”
Multidisciplinary knowledge is required to determine well-defined working conditions for a successful machine vision system and to solve potential issues. Some important criteria are accuracy and measuring time, leading to the use of adequate hardware and software tools, followed by identification of optimum operating conditions and recognition of potential issues, including the impact from noise or other disturbances during the acquisition process.
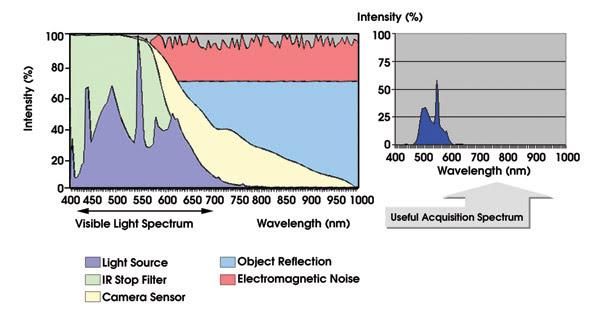
Figure 2. The results of an overview of disturbances found during the image acquisition of fibre-reinforced material show which parts of the applied light (wavelength in nanometres) with which light intensity (in percentage) were produced (light source), were allowed to pass (filter) and were acquired (camera sensor). The combination of such factors, together with estimated reflection behaviour of the object surface and a simulated value for the electromagnetic noise, produce the final useful acquisition spectrum.
External disturbances such as noise or environmental light usually are present during any image acquisition process. They sometimes can have such a strong influence that the captured image may not represent the inspected object properly, or the image processing algorithm may not produce good results. Therefore, it is important to pay attention. Improper image acquisition can cause the measuring system to become unviable. To identify these influences, a reference image acquisition chain was set up and analysed based on a machine vision system for the inspection of fibre-reinforced composites at the Laboratory for Machine Tools and Production Engineering (WZL) of RWTH Aachen University in Germany.
Identifying disturbances
The results show which parts of the electromagnetic spectrum produced by the light source are affected by filtering elements, by the wavelength transfer function of the object (which is specific to the scenario studied) and by the camera sensor.
First, the light source was analysed in more detail. Because of the 1000 × 750-mm measuring area of the setup, a number of 6500-K fluorescent lamps were used, together with a high-frequency controller. The spectral dispersion of the lamps was measured with a photometer within a step size of 0.6 nm. Although the lamps generate a wide light spectrum, it was found that they behave like a combination of different light sources; i.e., the light intensity is not homogeneously spread over the frequency spectrum.
Applied light is partially reflected into the optical system only by the object under inspection. To incorporate this effect into this study, it was estimated that only 70 per cent from the applied light intensity is reflected by the object surface. Because this parameter depends strongly on the inspected surface characteristics and on illumination conditions, it is difficult to perform a conclusive measurement of its value, especially for objects with nonuniform surface characteristics. Furthermore, such estimation would not be valid for an object with transparent properties being measured through a backlight technique, in which case a filter model would be more adequate.
Monochromatic cameras usually operate with infrared filters to decrease the noise influence from the invisible part of the electromagnetic spectrum and generated by temperature flows. Without such a filter, spurious reflections would appear in the acquired images, which would not be visible to the human eye. An analog three-CCD Sony XC-003P camera was used. While looking at the frequency spectrum at this point, it was interesting to note that the visible light spectrum was not always acquired correctly, even when a high-quality sensor was used.
Finally, the working environment (i.e., operating close to machinery) can introduce electromagnetic noise to the acquired signal, which can affect imaging as well as the data transfer process. For noise analysis, the environmental influence was simulated, and a distribution with a spread of 10 per cent around the mean light intensity was used. Such noise behaviour has less influence in digital cameras with USB, FireWire, Gigabit Ethernet and Camera Link interfaces because they work with the transference of digital data, avoiding the influence of electromagnetic noise.
The combination of all such factors restricts the resultant light spectrum, so all the elements of the image scene that are illuminated by light outside the net wavelength range will not be visible in the acquired image. For other parts of the image scenes, which are covered by the visible light spectrum, a stronger light intensity or a longer exposition time sometimes must be applied.
The influence of external illumination, such as sunlight, unstable illumination or shadings, also may disturb the stability of machine vision systems, which may require a special enclosure against it. Furthermore, the optics may bring distortions to the image, which may be avoided at least partially through the use of telecentric lenses and correct camera calibration procedures. In any case, the optical system configuration plays an important role during the imaging process. It is always important to find an optimal compromise between the light intensity acquisition (lens aperture) and the required depth of field (range of focus) in the image. If the application involves image acquisition of moving objects, progressive-scan camera technology is recommended to avoid image blurring and false interpretation.
Reliable machine vision systems require not only intelligent use of the abilities of each of their components but also systematic analysis of the inspection conditions. Robust strategies against noise and external disturbances are important, and the results obtained here show that a deeper analysis of the light source behaviour can reveal potential causes of disturbance. Although the imaging process generally is restricted to a nonhomogeneous limited-light spectrum range with significantly reduced intensity levels in large regions, these still can enhance many object features if the light source can provide sufficient power and if an appropriate optical system is chosen. The adoption of digital sensing technology is a good first step for avoiding the electromagnetic noise in an industrial environment.
The choice of a stable and homogeneous light source guarantees better acquisition hardware quality. Enclosing the inspection avoids other external light disturbance sources. Finally, the use of modular hardware and rapid prototyping software tools also may speed the evaluation of a machine vision system’s viability.
Contact: Alberto X. Pavim*, WZL of the RWTH Aachen University; e-mail: [email protected]; fax: +49 241 80 22193.
*Scholarship holder from the Brazilian CNPq.