Project DIPOOL Yields Updated Laser Blanking System
In modern production processes, especially in the automotive industry, blanks from coils need to be cut precisely and efficiently. As the requirements for these cuts become more and more demanding, traditional methods like punching are reaching their limits.
At the same time, the industry has to reliably and safely monitor continuous production processes to avoid system downtimes and production losses. Additional sensors and control mechanisms could detect and avoid malfunctions caused by cutting interruptions.
As part of the joint project DIPOOL (Digital Process Online Optimizer for Intelligent Laser Machines), the Fraunhofer Institute for Laser Technology ILT and its project partners are developing solutions to improve the efficiency and safety of laser cutting and welding processes.
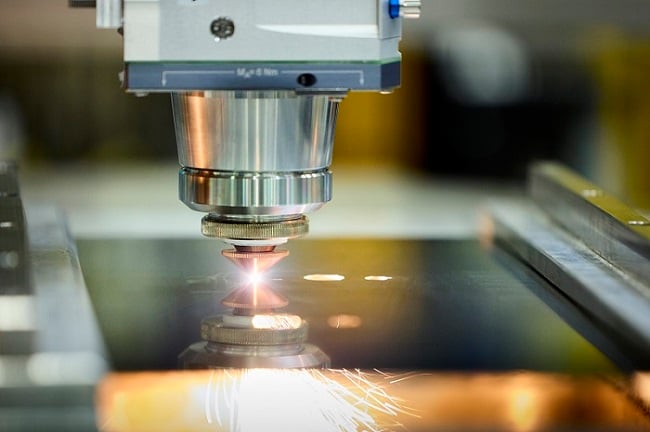
As part of the DIPOOL project, Fraunhofer ILT’s Frank Schneider and his team are using AI and minimally invasive laser modulation (MILM) to optimize process monitoring and control in sheet metal processing. Courtesy of Fraunhofer ILT/Ralf Baumgarten.
Funded by the German Federal Ministry of Education and Research, the project seeks to use AI and minimally invasive laser modulation to optimize process monitoring and control in sheet metal processing, with a particular focus on thin sheet metal and laser blanking.
“These technologies make it possible to detect process deviations in real time and make immediate adjustments to sustainably increase production reliability and speed,” said Frank Schneider, DIPOOL project manager and cutting group leader at Fraunhofer ILT.
The functional principle of the monitoring system is based on a “minimally invasive” laser modulation pattern (MILM). Minimal disturbances are imposed on the machining process, to which the process continuously responds with particularly characteristic, condition-dependent signals. AI can analyze these patterns particularly well.
Automatic-Systeme Dreher, Fraunhofer ILT, and a pilot customer have cooperated on building an industrial-scale laser blanking demonstrator system and integrating system monitoring with AI and MILM. For this pilot customer, the Aachen-based institute has been developing the process over many years.
“By combining a new type of system design, the high-speed cutting process developed by Fraunhofer ILT and innovative process monitoring, we are now able to machine blanks dynamically with extremely short cycle times,” Schneider said.
The system, which will be used to process cold-rolled strip products among other things, is specially designed to maximize process reliability when processing coils. The AI-based systems analyze the process signals in real time and detect even the smallest deviations before they lead to problems. MILM ensures that the cutting process remains continuously stable, an advantage that minimizes scrap rates and significantly increases the overall productivity of the system.
“The new concept of overlapping work areas of two processing heads with continuous belt transport in the system enables maximum flexibility and resource-efficient production,” said Hasan Sarac, managing director of Automatic-Systeme Dreher. “This means that each laser can process exactly what is required. This way, we can optimize nesting and process large components. This is a decisive advantage that makes manufacturing in automotive production more cost-effective."
Fraunhofer ILT and Dreher Automation will present the demonstrator system at EuroBLECH 2024. Following the presentation, the results of the DIPOOL project will flow into the first industrial implementation. In cooperation with the BILSTEIN GROUP as a pilot user, optimizations and extensions will then follow that are necessary for use in series production.
Published: September 2024