Trey Turner and Quentin Turchette, REO Inc.
Building efficient, reliable DPSS lasers requires optics with low loss and excellent stability – but these optics can’t drive up the cost. Reduced demands on pump power, thermal management systems and environmental controls can offset the cost of high-quality optics. Understanding such trade-offs is an important part of successful laser design.
Building efficient diode-pumped solid-state (DPSS) lasers requires a careful balance between price, performance and stability of the cavity optics. In particular, a number of optical components critically affect laser operating and output characteristics, and their specifications must therefore be properly understood and managed. We will discuss the most important of these, specifically for DPSS lasers operating at their fundamental wavelength, and in which ones damage due to high peak powers is not a significant concern. This will help specifiers and buyers of coated optics for DPSS lasers understand how to obtain the performance they require in the most cost-effective manner.
DPSS laser components
Figure 1 shows the major components typically present in a DPSS laser cavity. The first is the laser gain crystal, which usually has antireflection coatings on its end faces, optimized to pass both the fundamental lasing wavelength as well as the pump light. For end-pumped designs, there are usually one or two pump-through mirrors. These are dichroic mirrors that pass the pump light and reflect the laser fundamental. The two other essential elements are a high-reflecting end mirror and an output coupler, usually designed to pass a small percentage of the laser fundamental. Often also necessary may be cavity folding mirrors, Q-switch components, various polarizing elements and low-reflectivity “pickoff” beamsplitters for power monitoring.
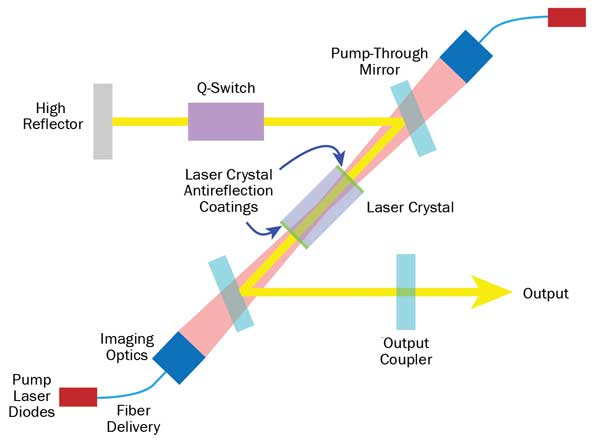
Figure 1. A schematic overview of one configuration of a DPSS laser cavity, showing the major components typically present in such a laser.
Understanding sources of loss
Each of these components is a possible source of loss. But which are most critical, and how does the designer determine the necessary specifications for each? These questions become increasingly important as laser builders attempt to maximize the efficiency (the conversion of input electrical energy into laser output) of their designs, to build systems that offer lower power consumption, less waste heat and longer lifetimes, without dramatically increasing costs.
It is important to realize that the process technology used to produce the optics can have a dramatic impact on the loss performance. Although the major mechanisms of loss in optics – including scatter, absorption, unwanted reflectance of some components and unwanted transmittance of others – are determined by design, they also are critically dependent on the manufacturing processes used to make them. Polishing processes, thin-film coating technologies, cleaning processes and inspection techniques all play a role.
Table 1 shows typical estimated loss values for each resonator component for two performance grades. “Standard-performance optics” are those that are widely available through many catalog sources, and “high-performance optics” are those manufactured using technologies and practices specifically developed for laser applications.
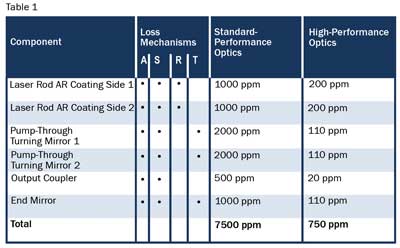
Table 1. AR = antireflection; A = absorption; S = scattering; R = unwanted reflectance; T = unwanted transmittance.
A key element of overall laser efficiency is the power-extraction efficiency, denoted as ηE, the ratio of the laser output power at optimal output coupler transmission (P) to the maximum available power for a given laser under given pump conditions (Pmax), as described by Walter Koechner in Solid-State Laser Engineering (Springer, Berlin, 1996) and shown in Equation 1.
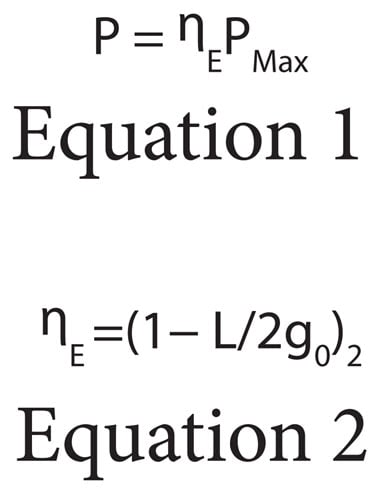
The power-extraction efficiency depends on the loss and gain in the cavity according to the relationship shown in Equation 2, where L is the sum of all resonator losses except for the transmission of the output coupler (e.g., scatter, absorption and transmission or reflection losses) and g0 is the unsaturated gain of the laser medium.
To understand this relationship more generally, Figure 2 shows power extraction efficiency as a function of cavity losses for a range of plausible laser parameters, including a range of typical losses for a set of standard-performance optics (L of ~7500 ppm) and a set of high-performance optics (L of ~750 ppm), and for several representative laser gains. Two main points can be made with reference to this figure: First, a high power-extraction efficiency can be achieved by a high-performance optics set with much less gain than with a standard-optics set (~10 times less gain for ηE = 0.9). Second, for a fixed gain, efficiency – and, therefore, output power – increases with decreasing loss. For the lowest gain shown, ηE = 0.9 efficiency can be achieved only with the high-performance optics set. Higher operating efficiency can always be achieved by improving the loss characteristics of the optics.
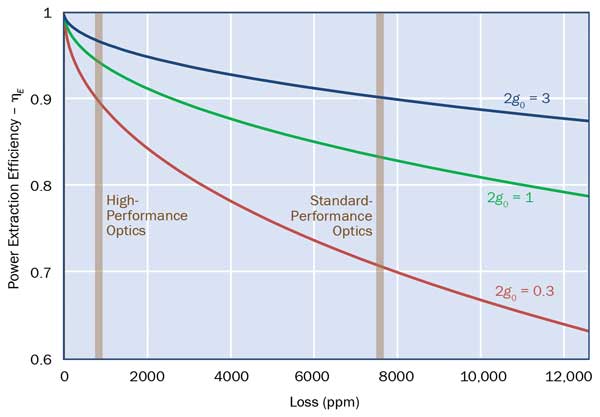
Figure 2. Power extraction efficiency of a laser as a function of loss for various gain values.
Another important element to laser efficiency is the pump-through efficiency, which is equal to the pump-wavelength transmittance of the pump-through mirrors. The quantity Pmax in Equation 1 is directly proportional to the pump-through efficiency and therefore to the transmission of the pump-through optic. To avoid this factor as a limitation to overall laser operating efficiency, it must be maintained at a level well above the desired efficiency specification (e.g., a 90 percent transmission level translates directly into a 10 percent efficiency loss).
Thin-film process performance
One key to achieving the desired loss performance to maintain high overall efficiency is the choice of thin-film process technology used to produce the various mirror and antireflection coatings. A typical specification for a high-performance pump-through mirror would be >99 percent transmittance at the pump wavelength, and >99.99 percent reflectance of the lasing fundamental. Multilayer thin-film designs that achieve this target performance level are certainly possible; however, translating designs like this into actual components, especially on a volume-production basis, can be challenging. Many commercially available pump-through optics provide only >95 percent transmittance at the pump wavelength and >99.5 percent reflectance of the fundamental.
We commonly achieve >99 percent transmittance of the pump, and >99.99 percent reflectance of the fundamental lasing wavelength in volume production, with very high unit-to-unit consistency, primarily by employing ion beam sputtering (IBS) technology. IBS is a vacuum deposition technology in which a high-energy ion beam is directed at a target, causing atoms or molecules to sputter off with high energy and deposit onto the parts to be coated (Figure 3).
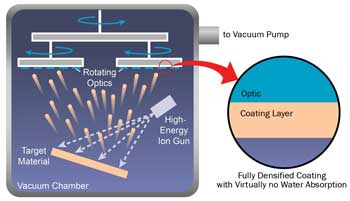
Figure 3. Ion beam sputtering releases highly energetic particles from the target, resulting in the highest-density coatings attainable.
This deposition technology offers three primary advantages over more conventional electron beam (e-beam) evaporation technology: much lower absorption loss, much lower scatter loss and substantially improved accuracy. IBS enables better control of both the index of refraction and the exact thickness of deposited layers, resulting in the ability to more faithfully achieve the target design performance in the actual coating. This high accuracy, in turn, enables the routine production of more complex coatings with higher layer counts, allowing the realization of designs with inherently higher performance. (In contrast, thickness errors can build up very quickly when using evaporative methods).
The impact of limited coating precision can be understood by examining Figure 4, which shows the typical reflectance characteristics of a pump-through optic produced with e-beam evaporation and IBS, respectively. These coatings were nominally designed for maximum transmittance at 808 nm and maximum reflectance at 1064 nm.
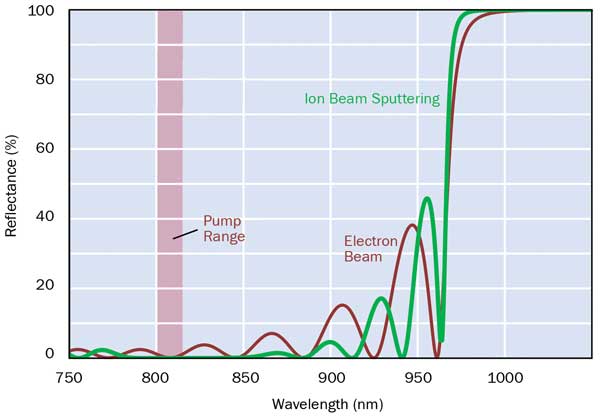
Figure 4. The spectral response of dichroic beamsplitters fabricated using e-beam evaporation and IBS coating methods.
The most important features to note in Figure 4 are the ripples in reflectance of the e-beam coating around 808 nm, which are caused by errors in the optical thickness of the deposited layers. In contrast, these fluctuations are absent in the IBS coating, which accurately reproduces the target design.
The reflectance ripples in the e-beam coating response affect resonator efficiency in two ways. First, their exact amplitude and position can’t be controlled deterministically (because of the limited-precision problem), so the exact reflectance of the optic at 808 nm varies from batch to batch. This is what limits the maximum transmission that the manufacturer can specify at 808 nm. For the laser builder, this variation makes it more difficult to build a consistent product and reduces design headroom.
The second issue is that the exact wavelength of the pump diodes can vary over several nanometers from unit to unit. This translates into variations in total transmittance, depending upon exactly how the diode laser and pump-through optic characteristics match up. Again, the result is inconsistent unit-to-unit performance in the final, assembled laser. The absence of these ripples in the short-wavelength (around 800 nm) reflectance of components manufactured using IBS means that neither of these problems is present.
Superpolishing and defect control
Scatter losses are another significant mechanism that lowers system efficiency and output power. These losses can arise from point defects on the surface or from the microroughness of the substrate and coating.
One important fabrication tool for reducing the microroughness of a laser optic surface is superpolishing, which can deliver surface roughness values below 1 Å, and, in conjunction with high-quality IBS coatings, can reduce scattered light below the 1-ppm level. In practice, superpolishing encompasses several process improvements relative to conventional polishing methods. For instance, it is typically implemented by submerging the entire polishing spindle and lap assembly in the polishing fluid. Submerging the assembly forms a barrier that helps protect the lap and workpieces from outside contaminants that could scratch the optical surface.
Scatter losses also can be caused by surface defects, which can degrade beam quality, and which become increasingly problematic as resonator energies increase because they act as initiators for laser damage. High-quality polishing is again a critical factor, as is the choice of coating process. Figure 5a shows a laser mirror polished conventionally and coated (by e-beam evaporation) with a high reflector. Figure 5b shows a similar mirror produced using superpolishing and IBS coating. The inspection conditions are identical for these images.
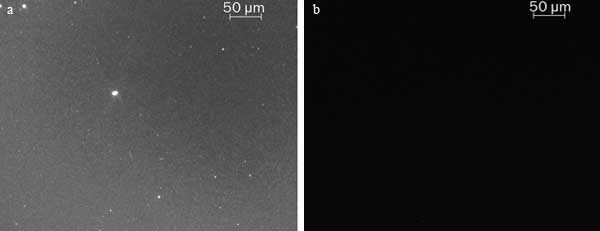
Figure 5. Scatter and defects are very evident in a conventionally polished optic coated using e-beam technology (a), but a superpolished surface coated using IBS shows virtually no scatter or defect (b).
Notice both the sharply decreased level of background light (scatter) and the much lower density of point defects present in the superpolished, IBS-coated mirror. The standard-quality, e-beam coated mirror has approximately 500 ppm of total loss, while the high-performance IBS mirror has approximately 10 ppm of total loss. This lower roughness and reduced defect level translate directly into higher laser operating efficiency, better beam quality and increased damage threshold.
Ensuring operating stability
Besides efficiency, optics specifications also must consider environmental and lifetime requirements. For example, evaporative coatings can reduce the operating stability of DPSS lasers due to their physical characteristics. In particular, these films are relatively porous, and can absorb moisture after they are produced. As a result, fluctuations in ambient humidity can change the optical thickness of the layers and shift coating response, and in turn, affect output. This is shown in Figure 6. In contrast, IBS is a much more energetic process that produces coatings that are fully densified and do not absorb moisture.
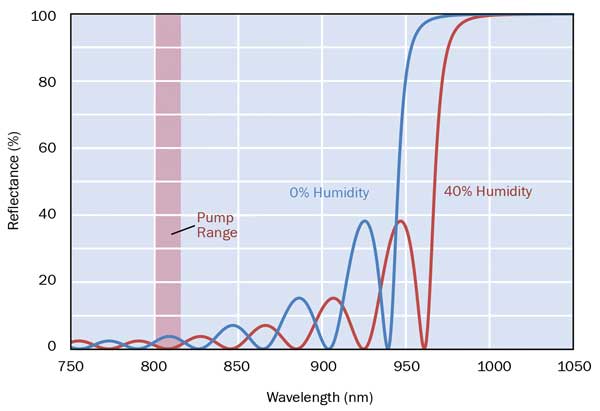
Figure 6. The spectral response of a dichroic beamsplitter produced by e-beam varies with humidity; that of a component manufactured using IBS does not.
This latter characteristic of environmental instability can even be an issue in lasers that are purged of moisture and hermetically sealed during fabrication. Specifically, when the laser is first powered on and heats up, the coating may release moisture, causing a shift in its performance and a change in laser output. Thus, coated cavity optics that appeared to be within specification when accepted by the manufacturer can go out of specification when actually used.
Meet the authors
Trey Turner is chief technology officer at REO in Boulder, Colo.; email: [email protected]. Quentin Turchette is a senior R&D engineer at REO; email: [email protected].