Omega Optical: Manufacturing ‘Green’ Optical Filters
BRATTLEBORO, Vt., Dec. 29, 2006 -- Since 1969, Omega Optical has built its technical reputation on defining the state-of-the-art for
optical interference filter performance, manufacturing optical filters for scientists and instrument manufacturers worldwide. From biotech to astronomy, fluorescence microscopy to color imaging, environmental monitoring to semiconductor manufacturing, Omega Optical is a leading supplier worldwide of custom filters for research, clinical and point-of-care fluorescence-based instruments and applications. Omega Optical filters have been used in the Hubble Space Telescope, the Human Genome Project and the filming of Star Wars.
Cutting-Edge Technology and Environmentally Friendly Practices
But for Omega Optical, nestled in the verdant hills of Brattleboro, Vt., a stone’s throw from the beautiful Connecticut River Valley, making state-of-the-art optical filters and being environmentally conscientious are not mutually exclusive concepts. In fact, the company’s new headquarters is one of only nine buildings in Vermont, and just the second manufacturing facility, to register with the US Green Building Council (USGBC), an organization that sets national standards for minimizing the environmental impacts of buildings.
Omega Optical was founded by Dr. Robert Johnson in 1969, and since then he has initiated a number of environmentally conscious endeavors in the Brattleboro area. His interest in alternative energy led to experimentation with thin-film “photoelectronic conversion sheets” that could be installed on building roofs, as well as the development of a thin-film photovoltaic solar-powered urban transport vehicle. In the community at large, he founded Friends of the Sun, an alternative energy product and service company that is still in business, and Solar Hill, which began as an alternative energy education institution and has evolved into an alternative health center. With the new Omega Optical headquarters, Johnson saw his environmental philosophy become reality once again.
A Building Al Gore Would Love
Omega Optical’s new, 32,000-square-foot facility is the first building on The Delta Campus, a 137-acre parcel that is planned as a unique combination of business, educational and residential facilities built according to sustainable practices. The property was formerly an auto junkyard, qualifying the land as a “brownfield” site. The cars were removed, the soil tested, and certification granted according to stringent environmental standards. A small stream that once passed under the hoods of rusted cars is now a reestablished stream bed with wetland flora.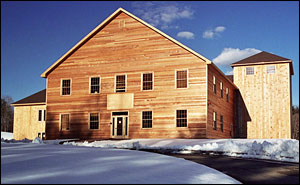
Omega Optical's impressive environmentally friendly headquarters is perfectly suited to its setting in the green hills of Vermont.
While being specifically designed for state-of-the-art optical filter production, the facility is also designed to create a small environmental footprint, sustainable and “off the grid.” The building design demonstrates the company’s long-term commitment to a healthy environment, and is demonstrating that sustainable design is good business.
The building is off the power grid and is designed to realize energy savings of 30-50 percent from a variety of features. A tri-generation system produces electricity, heating and cooling through the use of three diesel generators. The generators use a 20 percent biodiesel mix made from soybeans, and will eventually use gasified wood, both renewable fuel sources. The building is constructed of structurally insulated panels (SIPs). The ventilation system uses air-to-air exchangers to recycle heat. Photovoltaic panels are used to generate renewable electrical energy from the sun to power the parking lot lighting. Also, 30 percent of the lighting in the building is comprised of LEDs, not yet a common lighting choice in the construction of new buildings.
Additional environmentally friendly features include the use of recycled construction materials, lumber harvested from the site, bicycle storage (employees are encouraged to take alternative forms of transportation) three parking spaces for recharging electric cars and three spaces for those who carpool. Employees who bike to work or exercise during the day have access to showers and changing rooms on the first floor. Omega’s parking lot is covered in crushed limestone instead of blacktop, and reflects substantially less heat during hot summer days while minimizing storm water run-off.
The process of manufacturing optical filters requires the cooling of vacuum chambers while the coatings are being deposited. In the past, water used to cool manufacturing equipment was flushed down the drain following the cooling step. In the new facility a closed cooling system is used in which the cooling water is recycled in a continuous loop to an industrial chiller where it is repeatedly recooled. In addition, the facility uses superlow-flow toilets and sinks and water system controls. As a result, while Omega used to be one of the largest consumers of water in Brattleboro, the company has reduced its overall water consumption more than 90 percent.
The new facility is seeking certification from the USGBC, an organization which sets national standards for minimizing the environmental impacts of buildings. The USGBC, which represents all sectors of the building industry, has established the Leadership in Energy and Environmental Design, or LEED, certification process to encourage sustainable building design.
LEED provides a complete framework for assessing building performance and meeting sustainability goals. Based on well-founded scientific standards, LEED emphasizes state-of-the-art strategies and awards points in six major areas, including: sustainable site development, water savings, energy efficiency, materials selection, indoor environmental quality, and innovation in design. Omega Optical’s facility will qualify for points in all six areas. Omega is expecting the facility to be certified at either the Gold or Silver level.
Humble Beginnings
Omega Optical founder and President Robert Johnson grew up in 1950s Brattleboro on his family’s farm. After working for five years in Boston for an optical filter manufacturer, Johnson started his own company in a garage in 1968 with just $10,000 in his pocket and bits and pieces of obsolete equipment salvaged from high-tech Beantown companies. The scrap was reassembled into four high-vacuum reactors capable of manufacturing interference filters and a Vermont corporation was born. Johnson chose the name Omega Optical for its symbolic meaning of resistance, relating to an alternative approach to business.
Omega Optical was created to pursue research and development in optical thin-films, which are used to control the flow of light and are produced by condensing the vapors of elements and compounds on glass of all kinds. The most common product of this process is the interference filter. Omega began making filters for researchers almost from day one. An interest in alternative energy stimulated research into thin-film photovoltaics and ultimately led to the creation of spinoff businesses Friends of the Sun and Solar Hill.
At this time the science of using light as an analytical tool was relatively new and the company directed its research toward the creation of filters for analytical instrument makers. Early applications were in the biomedical and agricultural sciences, with universities and researchers the primary customers. As part of this growth, the company saw a possible future in an analytical tool -- the detection of fluorescence -- a technique which was first being discussed in the scientific literature.
Omega Optical’s success led to its relocation from space on the Johnson family farm to a former Unitarian Church in downtown Brattleboro. The company formed other business ventures during the 1980s, such as Omicron Eye Safety Corp., which did R&D of protective goggles for laser applications.
A World-Class Company
By the mid-1980s Omega’s development work in fluorescence paid off commercially. The sciences of fluorescence microscopy and flow cytometry, which allow for the visualization of cellular structures and the sorting and analysis of cells, were made possible by design and manufacturing developments invented at Omega. These advances set the state-of-the-art and allowed Omega not only to define the science, but for many years to capture almost the entire worldwide market.
The 1980s also saw the beginnings of Omega’s astronomy work. One of the first projects was the manufacture of a set of filters for the analysis of Halley’s comet. With that success, a number of high profile observational astronomy projects followed.
The 1990s saw the challenge of repairing the Hubble Space Telescope’s Widefield Planetary Camera and projects for NASA’s Martian Lander and the next generation space telescope. Recent explorations into "space" have involved customers from Hollywood, working to perfect the capture of digital high-definition images for the filming of Star Wars and for the feature film industry in general.
Investing in Up-to-the-Minute Research
Research and development are Omega Optical’s foundation, and the company has recently made major capital equipment improvements to increase both its capacity and capabilities. The result is quality improvements and cost-savings passed on to its customers.
Major equipment purchases have been made in coating capacity and technology, cleanroom-capable work and processing areas and CNC metal machining, which allows filter mounting hardware -- such as rings, holders and subassemblies -- to be rapidly customized. All manufacturing equipment upgrades have only complemented and improved the leading technology position that Omega Optical occupies in the optical filter industry.
Coating technology is the heart of Omega Optical’s business, and the company has invested most heavily in high-volume coating systems and an automated manufacturing line to increase capacity. Several sputtering systems have been added with high-capacity large formats for precision durable surface coatings and high-volume protected coatings.
Another addition includes a large capacity, high current, ion-assist e-beam system, which will enhance coating performance as well as improve yields and capacity. The third major addition is an automated assembly line being used for the company’s patented 3rd Millennium product line. This load-locked system produces coatings that combine the benefits of both surface and protected coatings, along with high uniformity, increased yields, lower costs and faster delivery times.
Unparalleled Capabilities
When a customer calls on Omega Optical, they know they are dealing with a technical staff of engineers, scientists and technicians with years of experience, a broad knowledge base and a command of the craft of producing precision interference filters. The company has thin-film filter design and modeling computer programs, as well as proprietary software customized for its specific processes.
With its vacuum coating systems, Omega Optical has the capability for coating a full range of dielectric, metal, and insulation materials. Its glass fabrication shop is equipped with diamond-tooled machines, CNC drills, shapers and saws, and the machine shop provides rapid-cycle prototyping and high speed manufacturing of filter-mounting hardware.
A large number of available spectrometers means Omega Optical is capable of providing a complete range of spectrophotometric measurements. The company offers traceable transmission, reflectivity and optical density measurements in the ultraviolet to near-infrared spectral range and can provide independent measurement of optical density traceable to OD 3, reliable to OD 6.
Omega Optical’s optical capability includes spindle, double planetary and high-speed polishers. Transmitted wavefront (TWF) of the complete filter assembly and individual components is measured at any wavelength from 400 nm to 1.2 µm on a broadband achromatic Twyman-Green (BAT) interferometer. Flatness is measured with certified optical flats; wedge is measured with an autocollimator.
The company has a fully equipped machine shop with the capability of producing jigs and fixtures, as well as a variety of custom filter rings, wheels and holders. Filter components are cleaned ultrasonically and assembled under laminar flow hoods. Nearly all scientific glasses, fused silica and specialty glass substrates are kept in stock and readily available to fulfill customer orders.
For Omega Optical, There’s No End in Light
Omega Optical has grown steadily over its three-and-a-half decade history. What started as a
“one-man” operation in a garage is now a $12 million company with 120 employees and international distributors throughout the world. The company, its founder, and an assortment of collaborators hold a variety of patents. Omega’s filters are used in instruments that have led to scientific advancements in the life sciences, clinical medicine, and astronomy. They have helped unlock the mysteries of the human gene sequence and probe the depths of the universe. While the late 20th century was called the digital age, it’s been said that the next scientific revolution will be in the science of photonics. Wherever that revolution leads, Omega Optical will be there -- where there’s no end in light.
For more information, visit: www.omegafilters.com
/Buyers_Guide/Omega_Optical/c10698