Trey Turner, REO, and Patrick Casnedi, Consultant
Activated covalent bonding overcomes the optical performance and laser damage limitations of traditional adhesive techniques and also can be used with mid-IR components.
Optical components and assemblies in which elements are bonded together using UV-curing adhesives are widely employed in many laser applications. But traditional adhesive bonding technology does have some significant limitations in terms of the optical performance, laser damage characteristics and environmental attributes it delivers.
A novel technique called activated covalent bonding (ACB) responds to the need for an optical bonding technology that overcomes these disadvantages; it also is applicable for use with mid-IR components.
The ABCs of ACB
Traditional bonding relies on the introduction of an adhesive fluid at the interface between two components. The adhesive forms a relatively thin layer between the optical surfaces, but it is viscous enough to fill gaps or mismatches between them of tens of microns in size. Once proper positioning of the individual components has been achieved, then the adhesive is set, typically by exposure to ultraviolet light.
In contrast, ACB does not introduce a third material to the two components being bonded. Rather, it employs a chemical process in which hydroxyl (OH) radicals are activated on both surfaces to be joined. After this occurs, the two surfaces are brought into physical proximity, and covalent bonds are formed between them. The net result is a bond that has essentially the same strength and mechanical characteristics as the bulk materials themselves (Figure 1).
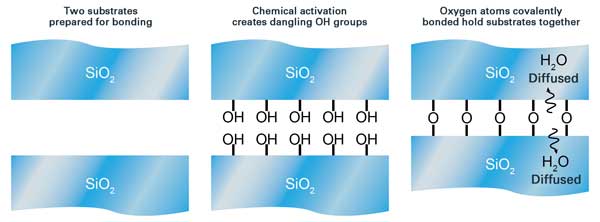
Figure 1. In the technique ACB, or activated covalent bonding, a chemical process activates OH radicals on the component surfaces, which are brought together to create strong, permanent covalent bonds. Images courtesy of REO.
It’s important to distinguish ACB from optical contacting, another technique commonly used to join components.
As with ACB, optical contacting is performed by bringing two highly polished surfaces into close contact. However, optical contacting relies on molecular bonds (specifically, van der Waals forces), while ACB is based upon much stronger, covalent atomic bonds. The net result is that ACB produces a substantially more robust assembly than optical contacting.
Several aspects of the ACB process merit further discussion. First, of course, both of the materials being bonded must be chemically capable of forming hydroxyls. In particular, the embodiment of the new process works specifically with oxides or materials that can form oxides. This doesn’t represent a particularly significant limitation, since virtually all optical glasses are oxides, as are fused silica (SiO2) and sapphire. Additionally, various metal oxides are used extensively as thin-film coating materials, standout examples being magnesium oxide and titanium dioxide. This is critical in beamsplitters, for example, because a bare substrate on one element must be bonded to a coated surface of a second element.
The strength of the ACB interface depends also on creating surfaces that physically match well, on both macroscopic and microscopic scales. For example, REO internally specifies that bonded surfaces match to within λ/10; that is, that gaps between the surfaces are no larger than about 60 nm. On the microscale, the roughness for surfaces intended for ACB must be at a level of approximately 1.5 Å or better. This doesn’t necessarily require superpolishing techniques (which deliver subangstrom surface roughness values), but it’s better than is achieved using most conventional polishing techniques, which usually yield surface roughness levels (on glass or fused silica) of only 3 Å or above.
This same roughness criterion also applies to the surfaces of thin films for ACB. Specifically, they must exhibit smoothness at the 1.5-Å level or better, as well as no (or minimal) porosity. In particular, coating porosity reduces the bonded surface area and allows a space for contaminants to enter, both of which reduce bond strength. Ion-beam-sputtering coating technology is used in conjunction with ACB because it produces a fully densified film, beyond what can be obtained through traditional evaporative or even ion-assisted methods. Furthermore, the need to rigorously eliminate possible contaminants necessitates the use of advanced cleaning protocols and careful design of the production work flow, so as to minimize the opportunity for contamination to occur.
This requirement for high-quality surfaces that are contaminant-free places a practical limitation on the maximum size of elements for ACB. Usually, ACB can be used for optics of up to about 250 mm.
ACB benefits
A primary benefit of ACB is that it enables the construction of components with improved optical performance over that achieved with adhesive bonding. For example, refractive index variations in the adhesive itself can produce a noticeable degradation in the transmitted wavefront of assembled components.
Adhesives also have a larger absorption coefficient within their transmission band than most bulk substrate materials, or thin films produced by means of evaporation or sputtering. This absorption is often the limiting factor in terms of laser damage threshold for assembled optics. Furthermore, the adhesive layer also scatters light more than the substrate materials or coatings do. Even for systems in which laser damage is not a factor, this loss due to scattered light can compromise performance. Plus, adhesive layers sometimes contain small bubbles that show up as optical defects.
Most commonly used UV-curing optical adhesives have excellent transmission throughout the visible and near-IR spectral ranges; however, they show significant absorption in the UV (below 370 nm) and in the mid-IR (above 2 µm). There is typically some transmission in the 4- to 5-µm band, but their use here is less than ideal. ACB doesn’t contribute additional absorption to the system, meaning that it essentially can be employed from wavelengths from the deep-UV through the far-IR. Figure 2 shows an example of beamsplitter cubes produced using ACB for use in the mid-IR.
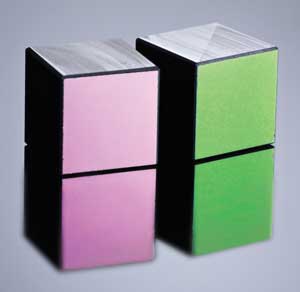
Figure 2. These silicon polarizing beamsplitter cubes for the mid-IR were produced using ACB.
Adhesives also exhibit an environmental sensitivity that is absent with ACB. In particular, they can be sensitive to humidity or moisture, and they can break down when exposed to certain conditions or chemicals. This is especially true in corrosive environments, such as those with organic solvents, or strong acids or bases.
Applications
Optical systems that operate in the mid-IR (3 to 5 µm) have long been used by the military for night vision and airborne countermeasures. Over the past few years, a number of important commercial mid-IR applications in medicine, atmospheric science and industrial sensing have also been developed. For example, mid-IR spectroscopy is being used for measuring trace gases in the atmosphere (e.g., greenhouse gases), for monitoring the progress of industrial fermentation, for mapping specific chemicals in a microscope image, and even for remote sensing of chemical weapons and toxins.
One major driver in the development of these applications has been the advent of practical, reliable mid-IR sources such as fiber lasers, optical parametric oscillators and external-cavity quantum cascade lasers. Unfortunately, all these lasers are very susceptible to feedback problems caused by even weak backreflections from external optics, which can happen whenever a downstream component is used at a near normal angle of incidence, or via reflections from diffuse surfaces. The traditional method for eliminating backreflections in the visible and near-IR is the optical isolator, which often comprises a quarter-wave plate and polarizing beamsplitter cube. But, until now, this approach could not be used in the mid-IR because there was no simple polarizer component with adequate performance characteristics.
While thin-film polarizers for the mid-IR have been available for many years, all these optics were plate-type beamsplitters, which have a first-surface beamsplitter coating exposed to air. Unfortunately, it’s not possible to achieve a wide bandwidth or extremely high extinction ratio with this type of arrangement. In contrast, a cube-type beamsplitter configuration offers a much greater polarization split and wider bandwidth because the coating in a cube beamsplitter is bounded on both sides by a substrate with a much higher refractive index than air. This reduces the internal angles of incidence in the coating, leading to the benefits just stated. However, until now the lack of adhesives that transmit well in the mid-IR has prevented the development of cube beamsplitters for this spectral region.
Using ACB, REO has developed cube beamsplitters that enable a high extinction ratio (up to 1,000,000:1) and linear polarization of mid-IR laser beams (Figure 3). The company’s IR3 series consists of laser optics with high damage resistance and excellent (λ/20 wave) transmitted wavefront, making them ideal components for use in high-rejection ratio optical isolators.
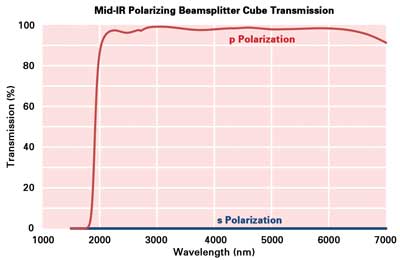
Figure 3. Using ACB, silicon polarizing beamsplitter cubes can be assembled to deliver a high laser damage threshold, high transmission (>95 percent) and a high extinction ratio (>100,000:1) over the 2- to 6-µm spectral range.
The use of ACB has also resulted in polarizing beamsplitter cubes for near-IR applications with a high laser damage threshold and high extinction ratio. One important application area for these is various types of high-power military lasers, such as rangefinding and target-designating lasers operating at either 1064 nm or the eye-safe wavelength of 1570 nm. For these uses, the mechanically robust bond resulting from ACB provides exceptional environmental stability, allowing operation over an extremely wide temperature and humidity range. It also makes the cube mechanically durable and insensitive to shock, vibration and high g forces.
A similar application for ACB is in constructing polarizing beamsplitter cubes intended for optical isolators for high-power industrial fiber lasers. These sources are particularly sensitive to feedback, so it is necessary to have a polarizer with a high extinction ratio, low absorption and a high damage threshold. And, of course, the high laser damage threshold and low scatter of ACB components also make them ideal for intracavity laser
applications.
Meet the authors
Trey Turner is chief technology officer at REO in Boulder, Colo.; email: [email protected]. Patrick Casnedi is a consultant in photonics in Paris; email: [email protected].