Thirty years after the discovery of organic LED (OLED) electroluminescence, OLEDs still have not fully penetrated either the display or lighting markets. With the exception of a few handheld mobile devices, OLED displays can be found in very few products in the consumer marketplace today – mainly one expensive wireless picture frame and one even more expensive 11-in. TV. But both analysts and industry say that could change very soon.
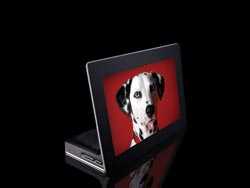
Eastman Kodak’s wireless picture frame is AMOLED-based, with a 7.6-in. diagonal screen. It features the wide viewing angle, vivid colors and thinness associated with OLED panels, but also the hefty price tag of larger screen sizes. Courtesy of Kodak.
OLEDs – solid-state devices that are about 200 times thinner than a human hair – are seen as a replacement for silicon-based LCD technology in displays because they can emit red, green, blue or white light without any other source of illumination, allowing them to display bright, clear images that are easy to see from almost any angle. OLEDs also don’t require a backlight, making them attractive because they use fewer materials and require fewer processing steps than LCDs.
Once they can be manufactured in high quantities outside of expensive cleanrooms, they have the potential to become a less expensive, superior performing alternative to LCDs and to compact fluorescent lighting, which contains mercury and emits only about 15 percent of its power as light.
OLED, SMOLED
In 1979, while working on solar cells, researcher Dr. Ching Wan Tang of Eastman Kodak Co. in Rochester, N.Y., discovered that sending an electrical current through a carbon compound caused the cells to glow. Tang and Steven van Slyke continued the research, producing the materials that became the foundation for Kodak’s OLED displays in 1987. Green was the first color generated, and over the years, improvements in the efficiency and control of color output have been made at Kodak using fluorescent dyes.
The first OLEDs were created using small molecules (SMOLEDs); Cambridge Display Technology in the UK later developed POLEDs using polymers – long chains of organic molecules – that allowed the organic material to be placed in a liquid and applied by spin coating or through ink-jet printing. These POLEDs could be cheaper to produce for displays, but first their picture quality must be improved. Today, two basic types of OLEDs are used in displays: active matrix (AMOLED) and passive matrix (PMOLED).
AMOLEDs are created by stacking several extremely thin layers of organic semiconductive materials – such as polymers – and passing electricity through them. The layers are sandwiched between two other layers, one negatively and one positively charged, then attached to a substrate, such as glass or another transparent material, that contains circuitry. When current is applied to the negatively charged – cathode – layer via a thin-film transistor, it is conducted to the positive – anode – layer through the organic film, which then emits light through the outermost transparent layer. The materials in the organic films can be doped or enhanced to help control the brightness of the light and to make them emit different colors of light.
PMOLEDs, instead of having full cathode and anode layers, have strips of these materials in perpendicular layers, in addition to the organic layers. The current is supplied by external circuitry, which makes PMOLEDs easier and cheaper to make than AMOLEDs – but they are more power-hungry. PMOLEDs are more efficient at displaying text, so they are used on very small screens, such as in cell phones and other portable electronics.
AMOLEDs control the light output of every pixel continuously, while in PMOLEDs, the light output is pulsed with high currents just once per refresh cycle. Thus, AMOLEDs provide a faster refresh rate – the pixels turn on and off more than three times faster than a movie’s speed – and are more suitable for larger, full-color displays such as computer screens, large-screen TVs and electronic billboards.
Full-color OLED materials deliver a brighter, richer range of colors than LCDs. They also offer much faster response times, a wider viewing angle and “blacker” blacks. Because OLEDs don’t require a backlight assembly, displays made from these materials also can be much thinner and more lightweight, and can consume much less power.
In lighting applications, silicon chip-based LEDs are better at providing directed light, including spotlights, but OLEDs have the potential to allow entire walkways or walls, even windows, to glow with light.
So, with all these advantages, you may ask why, decades after the technology was discovered, you can’t head to Best Buy and purchase a 42-in. OLED TV or to Home Depot and pick up OLED wall or ceiling panels.
The answer lies in three significant remaining obstacles to OLED commercialization: illumination power, material lifetime and the ability to mass-produce them affordably, especially for higher resolution formats.
Making OLEDs
The most critical part of making an OLED is applying the layers of organic materials to the substrate. The most inefficient and expensive way is via a vacuum chamber, in which the molecules are heated, then allowed to condense as thin films onto the substrate. In organic vapor phase deposition, a more efficient and cheaper method, a carrier gas transports the evaporated organic material onto the substrate, where it condenses into thin films.
Perhaps the most inexpensive way to make OLEDs today is via ink-jet printing, in which OLEDs are simply sprayed onto substrates – similar to how printers spray ink onto a piece of paper. This method holds promise for creating very large, even billboard-size displays.
The lifetime of the organic materials is something researchers are trying to overcome. Red and green films reportedly can last between 46,000 and 230,000 h – as long as 78 years at 8 h per day – but blue OLEDs average only about 14,000 h – less than five years at 8 h per day. Blue OLEDs also are the most energy-intensive of the three colors, although chemists and engineers at Pusan and Seoul national universities in South Korea announced in November that they had created an efficient “true blue” material that could accelerate OLED development.
“There’s a misconception by many out there that OLEDs don’t live long enough for consumer electronics, and that’s just not the case,” said Janice K. Mahon, vice president of technology commercialization for Universal Display Corp. of Ewing, N.J. “Do folks want it to get better? Absolutely, but OLEDs are very long-lived for a variety of products.”
Because the organic materials can be ruined easily by exposure to water, air or a single dust particle, glass has been the see-through material of choice for encasing OLEDs. But plastics also are being pursued to lower the cost and increase flexibility.
The glass used to encase the OLEDs represents more than 90 percent of the thickness of the device. Dresden, Germany-based Novaled AG and Vitex Systems Inc. of San Jose, Calif., announced last summer that they are working to combine Vitex’s Barix thin-film technology with Novaled’s doping technology to create very thin, highly efficient, long-lived OLEDs.
The future is flexible – and transparent
According to industry analyst DisplaySearch, although the economic crisis is resulting in declines in established segments of the display and electronics industries, revenues from AMOLEDs surged 100 percent in 2008. The company also expects OLED display revenues will exceed $6 billion in 2015, up from $591 million in 2008.
“AMOLED is making up for the slowdown in PMOLED over the past year,” said Dr. Jennifer K. Colegrove, DisplaySearch’s director of display technologies. “Going forward, it will be important for OLEDs to find a niche market where it will be difficult for LCDs to compete, such as flexible or transparent displays, or lighting. OLED developers should also look for opportunities to combine their technology with other hot technologies, such as touch screens.”
Once OLEDs can be made impervious to the elements easily and cheaply using plastics, flexible light panels will become a real possibility. One day, panels could be printed like wallpaper on large rolls – homes literally wallpapered with light.
Fraunhofer Institute for Photonic Microsystems (IPMS) of Dresden announced in June 2008 that it was working with Fraunhofer Institute for Electron Beam and Plasma Technology (FEP), also of Dresden, to develop a roll-to-roll production process for OLEDs, which would substantially lower their production cost. The work is part of the Federal Ministry of Education and Research-funded Rollex project, which began in 2007 and which aims to develop the technology to produce high-efficiency, low-price OLEDs.
Fraunhofer IPMS’ OLED work is now organized under the Center for Organic Materials and Electronics Devices Dresden (COMEDD), which opened in November.
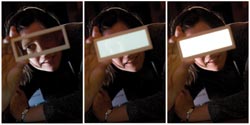
Transparent OLEDs can be as clear as glass one minute, then glow with light the next. Courtesy of Philips Research.
Scientists at Philips Research Laboratories, part of Koninklijke Philips Electronics NV of Eindhoven, the Netherlands, are progressing toward developing transparent OLEDs, panels that could look like ordinary windows or transparent glass walls during the day, then, after dark, morph into lighted panels that cast simulated natural or warm interior lighting. The company says those panels may emerge onto the market within five years.
“A transparent OLED over a window in a roof would be able to allow natural light in during the day and provide fascinating illumination for the room at night,” said Dr. Bernhard Stapp, head of solid-state lighting at Osram Opto Semiconductors GmbH in Regensburg, Germany.
Transparent OLEDs also could be integrated into a car’s back windshield to provide rear lighting.
To market, to market to buy an OLED
OLEDs began rolling off production lines in 2007, destined for mobile phones, MP3 players, auto displays and headsets. In January 2008, Sony Electronics Inc. of San Diego released the first OLED TV available in the US. The 3-mm-thick XEL-1, which had been in development for 10 years, has an 11-in. screen and retails for about $2500.
Kodak’s OLED wireless picture frame is AMOLED-based, with a 7.6-in. diagonal screen. Although it has computerlike features, such as 2 GB of memory and the ability to wirelessly connect to the Internet or to a computer, it also costs as much as a computer. Debuting on the market in November for $1000, it now can be bought for about $750. But that’s still a lot of money for a picture frame, albeit one that stores 10,000 images.
Sony unveiled its X-series Walkman video MP3 player at the 2009 Consumer Electronics Show (CES) in January. The device has a 3-in. AMOLED touch screen and is expected to be available in the US in the early summer – price still to be revealed.
Samsung Mobile showcased several OLED panels currently on the market at CES 2009, as well as panels slated to appear in future devices, including a 3.3-in. AMOLED billed as “3-D” and a 7-in. AMOLED panel. The company also demonstrated the concept of a “foldable” OLED screen inside a mobile phone as well as a transparent-screened 4.3-in. OLED display that could be used as a head-up display in auto windshields, but there was no word on when, or if, either would appear on the market.
Samsung’s Woo Jong Lee said in November that OLED panels will be used in laptops as early as 2010, and that the company expects 5-in. or larger OLED panels to become mainstream in 2009 or 2010.
Lee, vice president of the Mobile Display marketing team of Samsung SDI Co. Ltd., forecast that 28 percent of all laptops will feature an OLED panel by 2015. He said the image burn-in time on such AMOLED panels is expected to exceed 2000 h by then.
Samsung reiterated its commitment to AMOLED display technology in February at the World Mobile Congress in Barcelona, Spain, stating that the cost-per-unit price of the panels will become more realistic for production sometime during 2009. The company also expects flexible displays to become commercially viable in 2010.
Because OLED displays are so expensive to make in bigger sizes, some companies are turning to virtual reality as a way to provide a bigger OLED bang for fewer bucks.
UK-based MicroEmissive Displays’ eyescreen, a full-color POLED microdisplay, is about the size of a human’s pupil. It is embedded in one of the first commercially available pair of video glasses, iWear, made by Vuzix Corp. of Rochester, N.Y. The virtual-reality glasses give wearers the sense that they are watching a conventional 44-in. TV screen when they use them to access video games and other media.
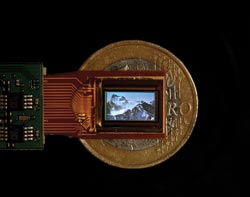
Microoled, in partnership with CEA-Léti, couples CMOS technology with OLEDs for high-resolution, low-power-consumption microdisplays that can be placed in video eyeglasses and camera electronic viewfinders. Courtesy of Microoled/CEA-Léti.
French company Microoled SA, in partnership with CEA-Léti (a Grenoble, France-based laboratory specializing in electronics and IT), couples CMOS technology with OLEDs for high-resolution, low-power-consumption microdisplays.
The company announced in November that it has designed the most efficient silicon-based OLED microdisplay available. Microoled said the 0.38-in. wide VGA microdisplay “opens the door for high-picture-quality electronic viewfinders for cameras, but also enables the market of high-definition video eyeglasses for mobile video applications,” said Eric Marcellin-Dibon, CEO and co-founder of Microoled.
Applications for the display include camcorder and digital still camera eyepieces as well as video or interactive eyeglasses.
“Marrying the capabilities of CMOS and the flexibility of OLED offers a unique route to microdisplays with unequaled resolution and brightness. We foresee a tremendous potential of applications for these devices,” said Laurent Malier, CEO of CEA-Léti.
You light up my … light
OLED lighting offers advantages such as higher energy efficiency and the ability to provide light with products that are thin and lightweight, flexible or rigid, without the heat of a traditional filament lightbulb. Hurdles remaining include high manufacturing costs and the ability to scale up the panel sizes while maintaining energy efficiency and uniformity.
Universal Display’s phosphorescent OLED technology (PHOLED) is used commercially to provide displays for portable electronics, but its white OLEDs hold significant promise for improving lighting.
“One of the benefits of OLEDs is that they are dynamically tunable – you can turn them down for very low brightness or very high,” Universal Display’s Mahon said. “There is interest in tuning them from cool whites [for office lighting] to warmer whites with more pink or red in it for dinner parties. OLED structures would let you tune it from one to another.”
Philips Research, which has been studying OLEDs since 1991, has developed white and “warm white” panels. It predicts that OLEDs will be capable of producing light of almost any color – including mimicking daylight and traditional lighting – in the next three to five years.
Philips now is offering a “starter kit” that contains several OLEDs of various shapes, structures and colors to enable lighting designers, architects and others to experiment with OLEDs for themselves.
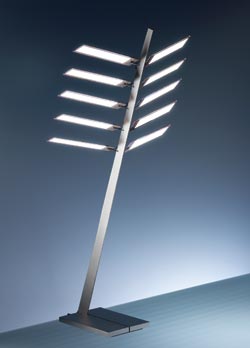
Early Future, a work of art by Ingo Maurer unveiled last spring, is a table lamp made with OLEDs from Osram Opto Semiconductors. Courtesy of Ingo Maurer/Osram.
A futuristic-looking OLED table lamp was announced by Osram in April 2008 and unveiled at the Light+Building Fair in Frankfurt, Germany.
Created by lighting designer Ingo Maurer, the limited-edition lamp, called Early Future, doubles as a work of art. It was made using prototypes of Osram OLEDs.
“It gives us a glimpse of just how versatile organic OLEDs can be in terms of their design options and applications,” said Osram CEO Martin Goetzeler of the debut.
In the future, OLEDs are expected to provide lighting just about anywhere you might want it: on clothing, in purses and on dental instruments – and maybe even in places that you don’t, such as on your driver’s license.
Bright Future for OLEDs
LEDs, solid-state lighting sources that use layers of organic material to generate light when current is applied, are emerging as a candidate to replace conventional lighting systems for illuminating large areas. OLEDs turn on instantly, can be dimmed and produced on stiff or flexible substrates of almost any shape, and use significantly less power than traditional lighting.
Before they can dominate the lighting market, however, ways must be found to make them inexpensively in large quantities and to make them more powerful.
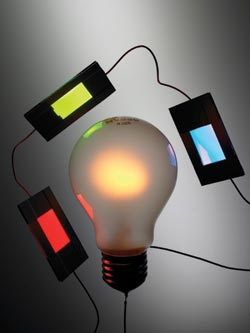
A number of government- and industry-sponsored programs are working to do just that, so that OLEDs can move out of laboratories and into homes.
“There will soon be white OLED products on the market,” said Janice K. Mahon, vice president of technology commercialization for Universal Display Corp. of Ewing, N.J.
White OLEDs are not yet powerful enough to provide full illumination, so early products primarily will provide lighting for architectural features and specialty applications. However, work continues into moving them mainstream.
In February, the US Department of Energy (DoE) honored Universal Display for advances in white OLED lighting performance. The company is known for its PHOLEDs, phosphorescent OLEDs that are up to four times more efficient than conventional fluorescent OLEDs.
Universal Display has received support from the DoE to develop highly efficient white OLEDs for use in a number of lighting applications. In 2008, the company demonstrated a white OLED light source with a record luminous efficiency of 102 lm/W, a significant milestone toward achieving the DoE’s target of 150 lm/W by 2015.
According to industry estimates, electric bills for lighting alone are more than $200 billion per year worldwide. It has been estimated that, by 2016, white OLEDs could generate well over $20 billion in worldwide electricity savings, as well as more than 9 million metric tons of carbon emissions from the US alone.
Universal Display’s PHOLEDs are used commercially to provide displays for portable electronics, but its white OLEDs hold significant promise to improve lighting.
One of Universal Display’s DoE-funded programs is working with ceiling tile maker Armstrong World Industries of Lancaster, Pa., to develop a tile with OLED lights built directly into it, Mahon said.
Europe pushes the OLED envelope
Europe is investing in the future of OLEDs as well. OLED100.eu, announced in October, has received €12.5 million (about $16 million) to develop efficient OLED applications for the general lighting industry in Europe.
OLED100.eu, a consortium of a number of institutions, continues the work of OLLA (Organic LEDs for Lighting Applications), which started in 2004 and ended in 2008. Under OLLA, white OLEDs with efficiencies of 50.7 lm/W and with lifetimes well above 10,000 h were developed.
The five main goals of OLED100.eu are to create OLEDs with high power of 100 lm/W, with a lifetime of 100,000 h, over a large area (100 × 100 cm2), with low cost (€100/m2) and with measurement standardization/application research.
CombOLED, part of a broad initiative by the European Union in the Seventh Framework Programme, targets cost-effective processes for volume production of OLEDs. Osram Opto Semiconductors GmbH is coordinating the work of the numerous project partners.
“The objective of this project, which is being funded by the EU and coordinated by Osram, is to create the necessary conditions for introducing the new light sources into lighting applications,” said Dr. Bernhard Stapp, head of solid-state lighting at Osram. This includes methods for cost-effective printing of new component architectures for large-format transparent light sources.
CombOLED builds on the experience gained in the OLLA project, which began under the EU’s Sixth Framework Programme in 2004.
Under OLLA, 24 partners from eight European countries reached their goal of creating an OLED with power of 50 lm/W and a lifetime of more than 10,000 h at an initial brightness of 1000 cd/m2.
Philips Lighting headed the project, which built upon PIN OLED technology developed by Novaled. Philips, Osram Opto, Siemens, Novaled and Fraunhofer Institute for Photonic Microsystems (IPMS) are now working within OLED100.eu to further improve OLED efficiency, lifetime and size.