From Hurricane Katrina’s shutdown of oil refineries in the American South to the tsunami-induced nuclear emergencies in Japan, manufacturing facilities have recently faced one disaster after another, but they also face – every day – the threat of something seemingly less catastrophic: oil and grease.
Spill some salad oil into a bowl of water, and you can easily see the sheen of the tasty dressing atop the surface. But salad oil is not a troublesome pollutant, and detecting far more minute droplets of fuel oil, gasoline, asphalt and various lubricants inside the labyrinthine plumbing of a nuclear power plant’s water-cooling tower or an oil refinery’s wastewater system is nowhere near as easy a task.
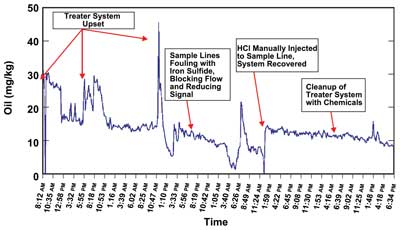
Fluorescence detection can provide continuous monitoring of the amount of oil in a water sample. In this example, the sample was examined on-site at an offshore oil platform in the Gulf of Mexico. Courtesy of Power Plant Chemistry.
Industrial facilities use a lot of water every day. Gulf-based oil platforms, desalination and wastewater treatment facilities, nuclear power plants and many other settings use the versatile liquid to feed boilers and to transfer heat from one area to the next. But oil, grease and fuels such as gasoline and diesel can get into rainwater, sewer systems and, eventually, cooling tower intake systems.
Mechanical separation devices, such as filters, collect such hydrocarbon-based pollutants over time, without much supervision, but can be overwhelmed by too heavy concentrations in a span of time, leading to accidental discharges. Volatile organic compounds also can be released into the atmosphere, leading to fines. Federal and state regulators determine how much of any given pollutant is permitted to escape industrial facilities into the environment. Permissible discharges can vary from zero tolerance to about 200 mg/l.
Whenever a subsystem – such as a section of pipes inside a water-cooling tower – within a facility is fouled by accumulated oils, costly chemical cleaning is needed. Depending upon the size and complexity of the systems involved, significant downtime will be needed to take it apart, clean it up, put it back together and report the process to the authorities.
Water that moves through a facility should be free of pollutants, which can foul mechanical systems or escape into the atmosphere, soil or groundwater. Cleaning up oily pollutants is a costly process involving remediation of large areas, possible fines and downtime while the plant is closed for cleanup and retooling.
Especially to blame are hydrocarbons such as fuel, lubricating and hydraulic oils, plus gasoline, methane and related chemicals that may be used in various parts of the facility where water flows to and from. Spilled motor oil that ends up in a storm drain eventually may find its way into the water-cooling system at a wastewater treatment facility, causing time-consuming fouling of pipes, valves and other structures as it collects and passes through.
In a cooling tower, which acts as a heat exchanger, water is on one side and oil (heat transfer fluid) is on the other. “Therefore, potential issues will be similar to all cooling processes, where oil from the heat exchanger can contaminate the water,” said Vadim Malkov of Hach Co., a water-analysis specialist in Loveland, Colo. “The only difference is what kind of oil is used for the heat exchangers. However, when oil leaks out of the heat exchanger, it won’t provide the intended service anymore. Therefore, the earlier the leak is detected, the faster [the] heat exchanger is repaired and potential loss to the process is minimized.”
Traditionally, the path to detecting small amounts of oil, gas and grease in process water has been to take a large sample (a liter or more) and bring it to a lab for analysis. This is a time-consuming, costly and at times dangerous undertaking. One lab method once used extensively is light scattering, in which a beam of visible light scans the surface of the sample and a technician looks for telltale glints from tiny oil beads.
Fluorescence detectors, on the other hand, can detect hydrocarbon pollutants in clean water in the range of 5 µg/l to 10,000 mg/l. Generally, suspended solid materials, such as dirt, soot or rust, that make water murky, don’t inhibit the detection process because only the hydrocarbon materials that might be within fluoresce under UV light. If more biotic material is present, as is the case with water that hosts living microbes, for example, then detection becomes more problematic.
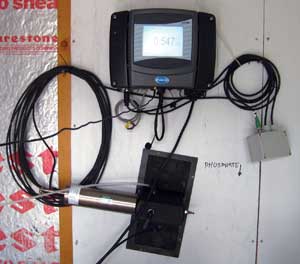
UV fluorescence-based sensors are relatively small and simple to install inside cooling towers. Courtesy of Vadim Malkov, Hach Co.
If river water is involved, “all bets are off,” said Gary Bartman of Turner Designs Hydrocarbon Instruments (TDHI) Inc. in Fresno, Calif.
The typical excitation wavelength to induce fluorescence in hydrocarbons falls within the range of 254 to 300 nm. Some pollutants respond to 400 nm, however, while others fluoresce only under near-IR excitation. Mercury and xenon flashlamps are still the most commonly used excitation sources. UV-range LEDs sometimes are used, said Chip Westaby, an industrial sales engineer at TDHI, but these tend to have a short service life, with rapid deterioration in lamps that emit below 300 nm. This is problematic with detectors installed in hard-to-access places.
“The key benefit to fluorescence is early detection,” Westaby said. The technique offers higher sensitivity than scattered-light detection, which allows earlier detection of small but still costly leaks.
Some fluorimeters used in oil-in-water applications are handheld, while others are installed in-line wherever access to personnel is limited, such as tight spaces and hot zones.
According to Westaby, protecting boilers from fuel oil that seeps into return condensates is a classic example of fluorescence-based monitoring systems. Because some fuel oils can be detected down to 5 µg/l in this situation, facilities that use boilers have the option of purging the condensate to protect the boiler or of redirecting the steam to recapture some of the heat.
In a paper published in Power Plant Chemistry in 2010, Malkov and his colleague, Dietmar Sievert, also of Hach Co., focused their attention on polycyclic aromatic hydrocarbons (PAHs). They set out to show how well UV fluorescence would provide a correlation between oil concentration and the sensor readings they acquired. They compared the results of the UV probe with those from a device using visible wavelengths.
PAHs, such as derivatives of naphthalene and other similar compounds, have a chemical bonding system different from monocyclic aromatic hydrocarbons such as benzene. When excited, PAHs reliably emit in the 360-nm range.
The UV probe fired a xenon flashlamp at 254 nm, and the visible-range device used an LED to provide excitation at 370 to 460 nm. The researchers tested the probes using phenanthrene as the key standard to help determine the concentration of diesel fuel, gasoline, gear oil and motor oil in a water sample.
They found that the LED-based probe did not respond at all to the diesel fuel, whereas the UV sensor picked out diesel at less than 1 mg/l and was sensitive to all of the other potential pollutants as well.
Overall, they determined that the fluorescence emissions acquired by the probe were linearly proportional to the concentration of diesel or other PAHs in water, and that fluorescence detection offers more selectivity and sensitivity than UV absorbance techniques.
Increasingly challenging applications are cropping up for fluorescence detection of oil in water. TDHI often is approached with requests to use its technology to find infinitesimal quantities of hydrocarbons in nonliquid materials, such as large soil samples.
“The biggest challenges [are] that UV sensors are too specific to PAH and therefore won’t see natural oils in water, while [visible] sensors are not specific enough and will suffer from interference provided by natural organic matter in water,” Malkov said.
Other challenges include the fact that fluorescence is not commonly used to detect organic contaminants (largely because not all organic compounds fluoresce), while UV absorbance, being a characteristic of the majority of organic substances, is neither specific nor sensitive enough for this purpose. Another challenge is fouling of the sensor, but Hach addresses that issue with appropriate accessories when possible, Malkov said.
If it can meet these challenges, fluorescence detection looks to continue ensuring that hydrocarbons don’t become the next disaster waiting to happen.
The Trouble with Boron:
An Interview with Jack Roberts, President of Symphotic TII Corp. in Camarillo, Calif.
Oil products are only one set of potential materials that can get into places where they aren’t wanted. In nuclear power facilities, boron is used to control fission. A corrosive byproduct of boron, boric acid, can seep through leaking seams, harming most objects that it contacts. As with oil-in-water issues, remediation is time-consuming and costly but carries an extra risk to workers because of potential exposure to radiation. Further complicating matters, boric acid residue is stark white, matching several possible materials that aren’t corrosive, not as dangerous and not necessarily even indicative of a leak.
Using the principles of Raman spectroscopy, Roberts and his colleagues devised a standoff method of determining whether any white residue that appeared was in fact boric acid.
How did your research on boric acid residues come about?
This was a request from power plant engineer Troy Wilfong (of Arizona Public Service Co. in Phoenix). The residues in question were in the reactor primary coolant vessels, which contain boric acid. The boron acts as a neutron moderator to help control the nuclear reaction in pressurized water reactors. If there were ever a small leak of the primary coolant, a white residue of dried boric acid would appear at or near the site of the leak.
The problem is that these reactors are old, and there are many types of white residues, such as paint, duct tape adhesive, etc., that look like boric acid, and the power generator needs to prove that this is not boric acid.
What led you to use Raman spectroscopy to differentiate boric acid from other materials?
Until the time of our study, our customer had never considered Raman. They were using expensive lab tests that required samples to be removed and taken to a lab. I suggested Raman because we had just finished developing a new portable system in cooperation with Enwave Optronics in Irvine, Calif. Symphotic TII has been working with Raman since we started in 2002.
Did your work incorporate any improvements in existing Raman technology? Can Raman be used to detect other signs of leakage?
We developed a remote technique allowing us to use a special telephoto lens to measure the Raman signal from several feet away, making it more convenient to determine the presence of boric acid in inaccessible locations.
The secondary coolant in a pressurized water reactor is what drives the turbines. This coolant contains molybdates, and we can easily distinguish molybdate from boric acid, making a determination if a suspected leak is primary or secondary coolant.
What improvements are you working on, if any?
We are continuing to make our systems smaller and more sensitive. This allows the systems to be more flexible and offer more potential uses.