Mauro Mosca, Fulvio Caruso, Leandro Zambito, Roberto Macaluso and Claudio Cali, University of Palermo; and Eric Feltin, Novagan
Low-cost Lumogen dyes can give white LEDs high quantum yield, reduced environmental impact and more.
Many analysts agree that the global lighting market is close to a real revolution: the LED revolution. In fact, the global lighting market is expected to produce profits of around €100 billion in 2020; currently, applications of the LED lighting market are commercial and/or industrial (33 percent of global market applications), replacement lamps (27 percent), architectural (16 percent), retail display (9 percent), outdoor area (6 percent), consumer portable (3 percent), entertainment (2 percent), residential (2 percent), emergency lighting (1 percent) and off-grid (1 percent).1 While lighting is not the only application of solid-state lamps, it is expected to cause significant growth in the global market, followed by signage and automotive applications.
This revolution may be ascribed to the great efficiencies of LED lamps, which offer less energy consumption. It is astonishing that 20 percent of electricity is consumed by lighting and that 70 percent of this is consumed by very inefficient lamps.2 Nowadays, humankind is eager for energy in any form (and, therefore, more receptive to energy-saving issues), so the availability of efficient and cheap energy sources is first of all a big business, one that has a big impact on the environment.
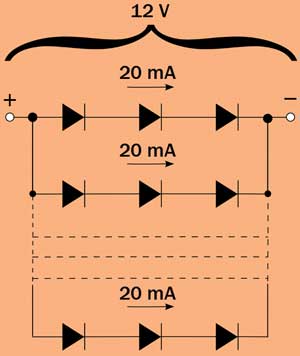
Figure 1. Connections among LEDs in an LED lamp. Each LED is
connected in series with two other LEDs, and each series is connected in
parallel. Typical current in each series is 20 mA, and the power supply
is 12 V.
To understand the savings in using LEDs instead of traditional incandescent lamps, a simple calculation can be “illuminating”: A 220-V, 100-W incandescent lamp gives a luminous flux of 1200 lm, while a single low-power white LED driven at 20 mA gives approximately 5 lm.In an LED lamp, several series of three LEDs are placed in parallel (Figure 1); since the driving voltage of each LED is around 3.2 to 3.5 V, the whole lamp can be supplied with a 12-V source. To produce the same luminous flux of the 100-W incandescent lamp, 1200/5 = 240 LEDs are needed, which means 80 series of three LEDs. As each series consumes 20 mA, the total current consumption is 80 x 20 = 1600 mA, which, in terms of electric power, is equivalent to 12 V x 1600 mA = 19.2 W. Compared with an equivalent incandescent lamp, about 80 percent of the energy is saved.
White LED technology
One of the most widespread solutions for the production of white LEDs is the conversion of a part of the light, coming from a known source, by exciting one or more materials that emit at a longer wavelength. The result is an emission spectrum given by the superposition of the single source and the photoexcited material; the big advantage is that the phenomenon of photoluminescence replaces the further integration of other solid-state devices of different colors.
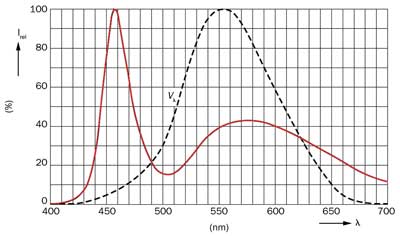
Figure 2. Typical emission spectrum of a commercial white LED, together with the eye sensitivity function V(λ).
The most common solution, developed by Shuji Nakamura,3 is to use the Ce:YAG phosphor, a mixture of Y3Al5O12, doped with small amounts of cerium. The emission peak of the phosphor can vary between 510 and 570 nm simply by changing the composition of YAG (Figure 2). Because of its high efficiency, this technology is one of the most widely adopted by major manufacturers of light-emitting devices (Nichia, Osram, Philips Lumileds and so on).
An alternative way to obtain white light from an LED is to use a source (typically, a blue LED) that acts as a pump for the photoluminescence of an organic substance. Why should one use an organic dye instead of a traditional inorganic phosphor? Probably, the main reasons are linked with their environmental impact: In fact, dyes generally are not hazardous for health and are easy to dispose of (many types of phosphors can be extremely toxic). Furthermore, organic pigments often are available at a low price (a few dollars per gram). Cerium’s cost is not high ($3.80 per gram); nevertheless, to obtain a warm-white light, it is necessary to add other phosphors that emit in the red portion of the visible spectrum. Red phosphors are based on rare-earth elements, too, but they are more expensive. Europium is one of the most used (e.g., red phosphor (Sr,Ba)2Si5N8:Eu2), and its cost is $1350 per gram.4
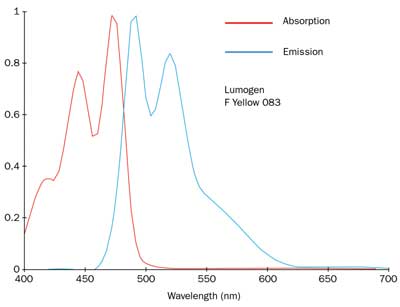
Figure 3. Absorption and emission spectra of Lumogen F Yellow 083, produced by BASF.
Lumogen-based LEDs
Our research team, from the University of Palermo in Italy and the semiconductor foundry Novagan of Lausanne, Switzerland, has developed a simple and less expensive method for fabricating a white-light LED. The photoluminescence of a perylene-based polymer dye turned out to be a good substitute for conventional inorganic color conversion. The dye used was Lumogen, a product commercialized by BASF and often employed in graphic arts; it is available in a large palette of colors from the UV to the IR at the same low cost.
For cold-white light, Lumogen F Yellow 083 exhibits one of the absorption maxima at 450 nm, and a broad fluorescence band between 500 and 550 nm (Figure 3). Standard InGaN-based blue LEDs are fabricated on a sapphire substrate by metallorganic chemical vapor deposition. Peak emission wavelength is centered at 450 nm, and the chromatic coordinates are (0.1477, 0.0338) in the CIE chromaticity diagram.
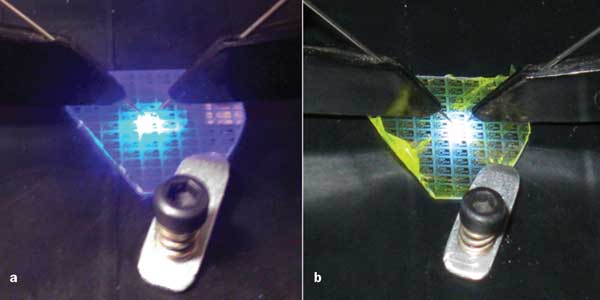
Figure 4. Pictures of a blue LED produced by Novagan (a) before and
(b) after the dipping process in a solution of PMMA and Lumogen F Yellow
083 (0.5 mg/mL).
Lumogen dye is dissolved in a polymethyl methacrylate (PMMA) solution (0.5 mg/mL), which in turn is dissolved in ethyl acetate. A suitable viscosity is obtained with a concentration of PMMA of molecular weight 350,000 from 8 to
16 percent (w/w percent). Although the best results are obtained using chloroform or trichloroethylene as a solvent, it is preferred to use ethyl acetate (which has a low toxicity and acceptable solubility for PMMA) to eliminate the carcinogenic risk. The bare side of the sapphire substrate is coated with the dye solution by either spinning or dipping so that different coating thicknesses can be obtained (Figure 4). The emission spectra and chromatic coordinates are measured by an Ocean Optics HR4000 spectrometer, the LED being driven by a constant current (20 mA, typical); optical power is measured by a Newport 818-UV calibrated photodiode.
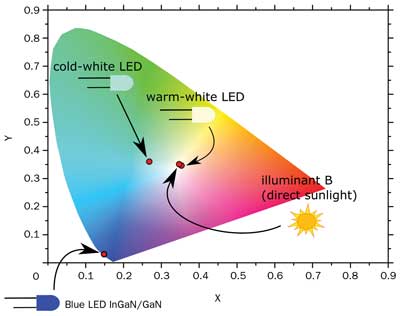
Figure 5. CIE chromaticity diagram of a cold-white LED obtained with
Lumogen F Yellow 083 (0.5 mg/mL in PMMA solution). In the same diagram
are also shown the chromatic coordinates of the blue LED source, a
warm-white LED obtained mixing Lumogen F Yellow 083 (0.5 mg/mL) and
Lumogen F Red 305 (0.05 mg/mL), and the standard Illuminant B lying in
the Planckian locus.
The emission spectrum and chromaticity diagram enable a performance evaluation of the white-light LED and show that record values of 9.37 lm of luminous flux and 118.23 lm/W of luminous efficiency are achieved (with 20 mA of driving current). A pure and intense cold-white light is emitted, as proved by chromatic coordinates of (0.2687, 0.3629) in CIE chromaticity diagram (Figure 5). It is expected that high luminous efficiency can be achieved, given the higher fluorescence quantum yield (91 percent) compared with the one of Ce:YAG (75 percent, typical).
The luminous efficiency decreases with increasing multichromaticity of the light source; in other words, this happens when a number of dyes (other than yellow) emitting in other parts of the spectrum are added. This is necessary to increase the color-rendering capability of the light source and to produce a warmer white light. When only the yellow dye is used, the white light produced by the LED appears to be cold. The solution is to add a red phosphor to the yellow one to move the chromatic coordinates toward a lower color temperature, although the luminous efficiency drastically decreases. This is due both to the human eye’s lack of sensitivity in the red portion of the spectrum and to the coating layer’s increased light absorption.
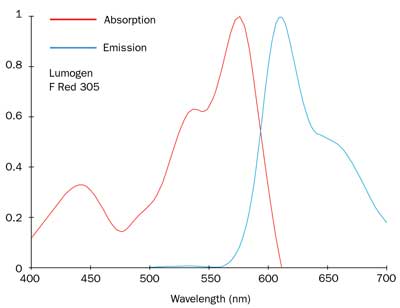
Figure 6. Absorption and emission spectra of Lumogen F Red 305, produced by BASF.
Moreover, part of the fluorescence band generally lies in the IR region, further degrading the efficiency. Lumogen F Red 305 has a luminescence peak of 613 nm, and only a small part of the luminescence band falls in the IR region (Figure 6). By mixing the Lumogen dyes properly, we proved that a very small quantity of red dye is enough to significantly enhance the color-rendering capability (Figure 7). If only 0.5 mg of red dye is added to 10 mL of PMMA solution with 5 mg of yellow dye, the white light produced by the LED appears warm, with a negligible decrease in efficiency (116.11 lm/W) and a luminous flux of 8.03 lm. Chromatic coordinates are located at (0.3554, 0.3483), very close to the Planckian locus of white illuminants (namely, the location of the blackbody radiation in the chromaticity diagram) (Figure 5). With red and yellow dyes, the emission spectrum is broader, as it is enhanced in the red range (Figure 8), releasing a warmer white light.
Polymer weathering
The organic dye-based white LEDs’ weakness is undoubtedly the degradation of the luminous performance. This limitation, mainly the result of polymers’ thermal instability, prevents organic dyes from diffusing in the white LED market segment. From this point of view, Lumogen’s properties seem to be more attractive than other dyes: Their heat stability is 280 °C, and their resistance to weathering is high (the residual fluorescence after 80 days of accelerated exposure in the Xenotest 1200 is higher than 90 percent).
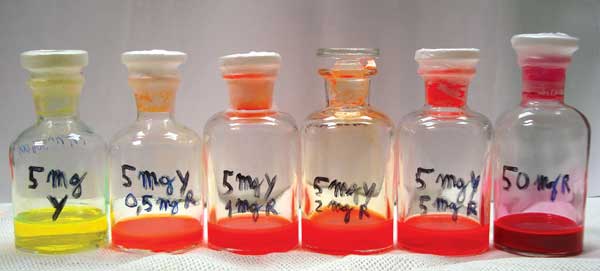
Figure 7. Color palette obtained mixing different
concentrations of yellow and red dyes in the PMMA solution. From left to
right, concentrations of yellow and red dyes in PMMA have the following
pairs of values (mg/mL of Lumogen Yellow; mg/mL of Lumogen Red): (5;
0), (5; 0.5), (5; 1), (5; 2), (5; 5), (0; 50).
During the working time of Lumogen-based LEDs, the optical transmission of the coating tends to increase, and the
chromatic coordinates of the emitted light drift toward the bottom-left corner of the CIE diagram, whose wavelength corresponds to that of a pure blue light source.
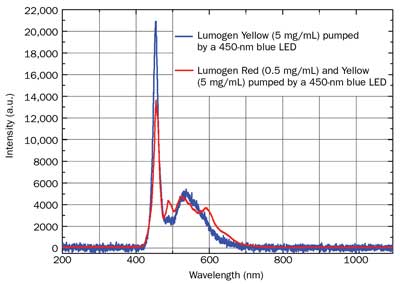
Figure 8. Emission spectra of a cold-white LED (blue plot) obtained by a solution of Lumogen F Yellow 083 in PMMA (5 mg/mL) and a warm-white LED (red plot) obtained by a solution of Lumogen F Red 305 in PMMA (0.5 mg/mL) and Lumogen F Yellow 083 in PMMA (5 mg/mL). Both LEDs are pumped by a 450-nm blue LED.
This observation proves that organic coating heating stands out among the hypothetical causes of degradation in the frequency downconversion effect. When a low-thermal-conductivity material (a glass slide) is inserted between the wafer and a Lumogen F Yellow 083 coating film, and the same stress test is repeated under these conditions, the chromatic coordinates remain unchanged (Figure 9). In conclusion, the local rise of junction temperature, transmitted to the organic coating through the sapphire substrate (which has a high thermal conductivity), is a cause of degradation of the dye. On the other hand, remote dye distribution stops the thermal degradation process and provides a good solution for increasing the LEDs’ lifetime.
Hybrid white LEDs based on Lumogen dyes can pave the way to new and interesting applications in the LED lighting market. High quantum yield, technology ease, low cost and reduced environmental impact are the strong points of the Lumogen-based LEDs. Luminous fluxes and efficacies are comparable (and they could be pushed slightly higher) to the values reported for commercial LEDs, making this technology highly competitive in the lighting market: The most appropriate sectors could be those in which medium-life-span products such as consumer electronics (mobile phone LEDs, flashlights, etc.) are sold.
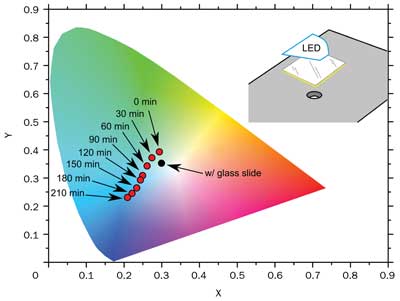
Figure 9. Light-emitted coordinates in CIE chromaticity diagram, without (red dots) and with (black dot)
the insertion of a glass slide. With the glass slide, the black dot does not change its position in the
chromaticity diagram. The inset displays the arrangement of the Lumogen yellow coated-glass slide to test the degradation due to thermal effects. The light is collected from the hole below.
Also, hybrid LED lighting fits perfectly in refrigerated cases and in a low-temperature environment, minimizing the detriment of the thermal effect and extending the device’s life.
Meet the authors
Mauro Mosca is with the University of Palermo in Italy; email: [email protected]. Fulvio Caruso, Leandro Zambito, Roberto Macaluso and Claudio Calì also are with the University of Palermo. Eric Feltin is the managing director of Novagan of Lausanne, Switzerland.
References
1. V. Bhandarkar et al (September 2012). LED lighting market holds steady in 2012. LEDs Magazine, pp. 33-35.
2. M. Freebody (January 2013). Beyond recycling: Using photonics to save the planet. Photonics Spectra, pp. 48-55.
3. S. Nakamura and G. Fasol (1997). The Blue Laser Diode. Berlin: Springer.
4. www.chemicool.com