Dr. Barbara Stumpp, Freelance Science Writer
Efficient use of a laser beam is dependent not only on the power of the laser source and beam quality, but also on its precise guidance.
Short- and ultrashort-pulse lasers are used to remove materials on an atomic level for high-precision applications such as extremely fine carving and cutting. Solar cells are one application where this kind of high precision is needed: Electrical contacts are placed in a small excavated area. The smaller this area is, the greater the output of the solar cell.
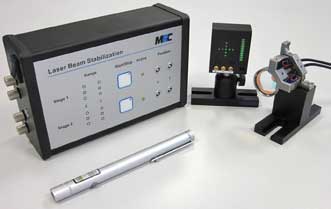
Piezoactuators enable high-precision, exact reproducibility and fast
control in beam stabilization for lasers. This stabilizing system from
MRC relies on piezoactuators. Courtesy of MRC.
Lasers also are used in the manufacturing of electronics. Wherever lasers are applied, flexible handling and high resolution – as well as optimal automation of processes without long setup times – are the basis for high throughput in production. Lasers are typically surrounded by machinery and robots, systems that vibrate and oscillate, respectively – which means that lasers cannot be used in an industrial setting without a beam-guidance system. The true benefits of laser production really exist only when the beam hits exactly where it should. Where extremely fast correction and precise control are required, piezoactuators are needed. Compared with motor or inductive drive systems, piezo technology offers almost unlimited resolution and an extremely short time delay from when the control signal is applied to when the position is reached.
Piezoactuator-based beam stabilization for lasers is characterized by high precision, exact reproducibility and fast control of the beam position. It compensates for distracting influences such as laser pointing, thermal beam fluctuations, collisions, environmental vibrations or vibrations from any other equipment.
“Actuators have to be very fast – real-time correction of the beam position is necessary, depending on the nature of the disturbance, and with an accuracy of less than 1 µm,” said Dr. Marcus Goetz, CEO of MRC Systems. A real-time detector with integrated signal processing determines the fluctuation of the laser beam with highest spatial resolution.The principle even allows measurement of individual laser pulses.

This schematic shows a working principle of laser beam stabilization. Courtesy of MRC.
The stabilization base for a laser beam is the detection of the drift with respect to the optical axis. MRC uses a four-quadrant diode (QD-4) as a detector, which can be mounted behind a highly reflective mirror and which achieves bandwidths >100 kHz. It detects deviations of the laser from the desired position and sends a signal to the controller, which transfers the signal to the tilting system – which, in turn, corrects the mirror position.
For the piezoactuator, MRC uses a mechanically prestressed, ultrafast tilting system from the PSH series made by piezosystem jena. This stage positions the mirror in two mutually orthogonal axes and an additional diagonal axis. The speed of the tilting system is very high, even under a load. The high-control bandwidth compensates for the dysfunction seen in real time. Because of the high control rate, this solution could be used with both CW and pulsed lasers. Using additional electronic circuits, even lasers with very low repetition rates or irregular pulse trains can be stabilized.
The system automatically adjusts the laser beam in a predetermined direction, counterbalancing the fluctuations in the beam direction and stabilizing the optical axis in real time. This enables active control of internal and external vibration as well as swift and automatic correction of misalignments or pointing.
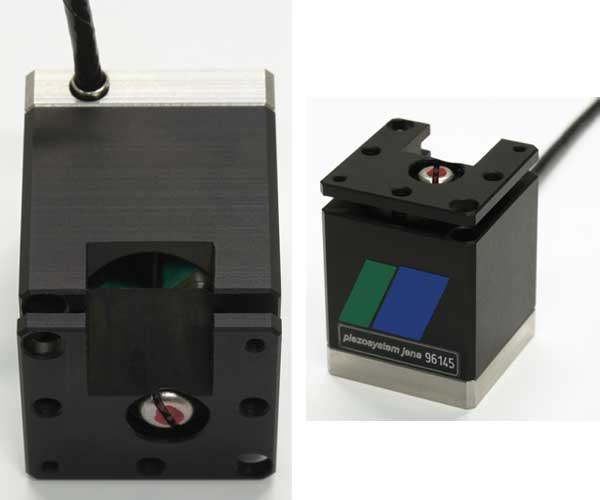
For its piezoactuator, MRC uses a mechanically prestressed, ultrafast tilting system from piezosystem jena’s PSH series. Here, the modified design of the piezo drive for the tilting mirror. Courtesy of piezosystem jena.
“The piezoactuators, which operate together with position detectors in a closed loop, enable fast adjustment of laser beams, to compensate [for] disturbances in the laser beam position and/or direction in real time,” Goetz said. The adjustment is done over a control range of 2 mrad, corresponding with the angular displacement of the piezoactuators.
“The tilting mirror systems of our series PSH are based on the principle of the piezoelectric direct drive,” said Elmar Elbinger, who is responsible for marketing at piezosystem jena. “Three separate controllable piezoactuators (tripod structure) move the centrally prestressed head plate. Therefore, these tilting mirror systems have a very high stiffness and an extremely high resonant frequency.” The systems are designed for the rapid positioning tasks needed in an active beam stabilization application or beam tracking in a scanning application. Thanks to very low settling time, any angle constellations can be approached dynamically. Systems with integrated position sensors also allow for precise repeatable control of defined positions.
A special feature is the temperature-compensated design of these tilting mirror systems. The piezoactuators are also mechanically prestressed and, therefore, particularly suitable for dynamic applications. They also are available for use in vacuum and at low temperatures.
Slight footprint
With laser-stabilization applications, real-time capability is important, but so is compact construction – which is true for many industrial systems. MRC required the placement of the mirror to be far away from its tilt axis, but this would cause too large moments of inertia, causing problems for the actuators. An alternative would have been additional optical elements in the beam path; however, this would not have improved the beam quality. The developers at piezosystem jena found a simple solution: adapting an existing design. This was also the most economical solution: Standard components could be used, and the assembly position of the PSH in the MRC system could be accomplished horizontally.
By introducing an appropriate notch in the actuator, the mirror could stay close to the tilt axis, and the torque required to tilt the mirror would be sufficiently low. Therefore, the proven reliability of the drive concept was guaranteed even during continuous use, and the dynamic parameters of the PSH system remained.
“The horizontal assembly position of the piezoactuator is parallel to the beam path. Thus, there is no beam deflection needed in the system,” Elbinger said. “The PSH – with a resonance frequency of 5.4 kHz – can be used up to 80 percent of its resonance, which means the piezo-system can work up to a frequency of 4.3 kHz. With a high frequency, dysfunctions that appear in this range can be eliminated. The high resonant frequency makes the system less susceptible to external oscillations.
“Also, low-frequency dysfunctions have less of an impact on piezos with high resonance. Lastly, disturbing oscillations even in the higher frequency range can be eliminated.”
The quality of the stabilization is defined by the speed and precision of the control. Without the piezoelectric drive elements working in real time, the following processes could be neither optimized nor realized: thermal stabilization of a femtosecond laser, high-resolution position correction, fast position correction of a laser, vibrations in lithography, or scanning 100 lines of an area in less than a second. For all these applications, laser-beam stabilization is needed to maintain performance and to increase scope.
Meet the author
Dr. Barbara Stumpp works as a freelance journalist in Europe and does public relations work for enterprises from the business-to-business areas; email: [email protected]. A version of this article appeared in German in Laser+Photonik in May 2013.