Laser experts from Germany and Israel are testing a laser for industrial use at the Fraunhofer Institute for Material and Beam Technology IWS. The laser is part of the Saxon-Israeli research project ShapeAM, which began in July 2021, part of the European network program M-era.Net.
Fraunhofer is currently investigating the beam shaping, which is accelerated by 1000×, for the first time for additive manufacturing, alongside project collaborators Civan Lasers and A. Kotliar Laser Welding Systems.
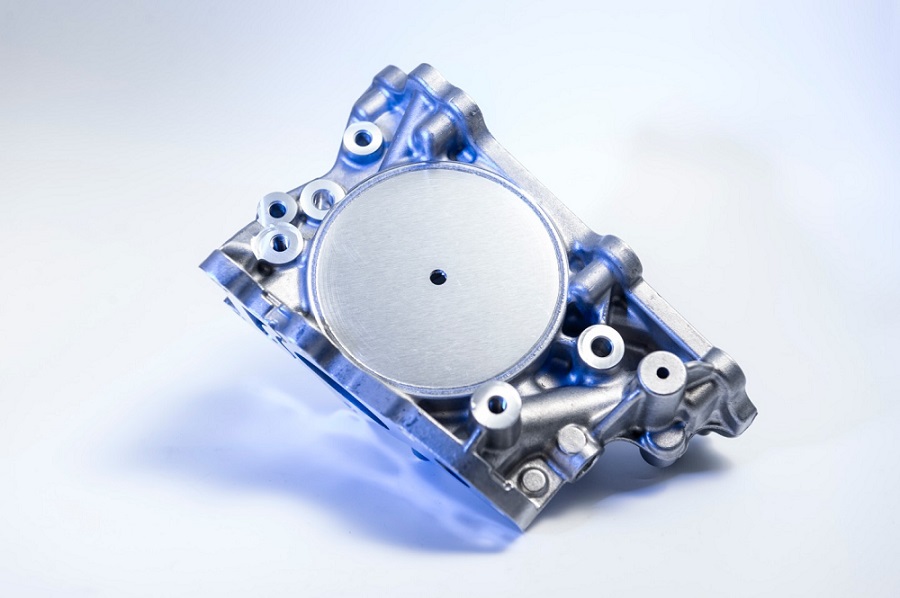
The international team of researchers will investigate welding applications, including how to use the new laser system to achieve advantages in terms of processing speed and quality for comparable components such as the one pictured. Courtesy of René Jungnickel/Fraunhofer IWS Dresden.
The 13-kW laser is based on the coherent beam combining (CBC) method. Here, the Dynamic Beam Laser from Civan Lasers combines tens of individual beams into a powerful laser beam with high quality. Through small phase shifts (optical phased array, or OPA) of the wave troughs and peaks in the partial beams, the laser can quickly generate completely different energy distribution patterns in the resulting processing laser beam.
A classic laser releases most of its energy only in the center of the beam. The system used in the work can generate energy patterns on the workpieces, for instance in the form of a ring or a horseshoe.
Though this was already possible in principle with beam-deflecting optics or fast oscillating mirrors, even the fastest oscillating mirrors still need milliseconds to realign the energy patterns in the beam.
The Dynamic Beam Laser accomplishes this 1000× faster, within microseconds. In generating different energy distributions quickly, it is able to precisely and quickly process demanding high-tech materials. The laser can additionally generate energy distribution patterns thousands of times faster during operation compared to conventional mirror-based methods.

This speed makes it possible to use dynamic beam shaping for additive manufacturing of metals.
“We plan to use novel beam shapes and control frequencies that are not achievable with other methods to overcome challenges in crack-sensitive materials,” said Elena Lopez, department head of additive manufacturing at Fraunhofer IWS.
The joint project is expected to develop into a scientific and personnel exchange between Israel and Saxony. Fraunhofer will be forwarding the test results to Jerusalem, along with exchange scientists. Laser experts from Civan are expected to conduct tests in the laser lab in Dresden.
The tests are intended to determine the possibilities and limitations of the Dynamic Beam Laser and will begin with basic tests of various beam profiles, materials, and processes. Subsequent tests will focus on specific applications, such as cutting, joining, and additive manufacturing of diverse materials and composites that are otherwise difficult to process.
“This laser will push the limits of materials processing, for example in medical technology and aerospace,” said Andreas Wetzig, head of the cutting and joining technology field at Fraunhofer IWS.
Fraunhofer will present the laser to partners interested in the project on Sept. 14. It seeks to make the technology available to companies worldwide in the near future to test its use for their own applications.
First findings from the test series will be presented to a broader expert audience at the combined online event Laser Symposium/ISAM 2021 in Dresden Dec. 7-9.