A nitride-based coating extends the lifetime of molds by preventing abrasive wear and averting glass adhesion, promising to reduce the cost of manufacturing infrared optics.
MARCEL FRIEDRICHS AND HOLGER KREILKAMP, FRAUNHOFER INSTITUTE FOR PRODUCTION TECHNOLOGY IPT
Today, infrared optics are mainly used in relatively high-priced technical devices. Thermal imaging cameras, for instance, help builders and surveyors identify leaks and thermal bridges in buildings, while night vision systems are used by police and military forces to monitor areas in darkness or twilight. Cost-effective infrared systems could open up many new markets, especially in the field of consumer products where thermal imaging cameras might one day be integrated into commercially available smartphones and provide users with information about energy losses in their homes. Further use of inexpensive infrared technology is conceivable in building automation, in climate and brightness systems without conventional motion detectors, as well as for the anonymous recording of lines in supermarkets. Moreover, advanced presence detector systems in cars enable drivers to recognize people and animals under poor lighting conditions at night. However, the high costs of infrared systems hamper their penetration of the mass market.
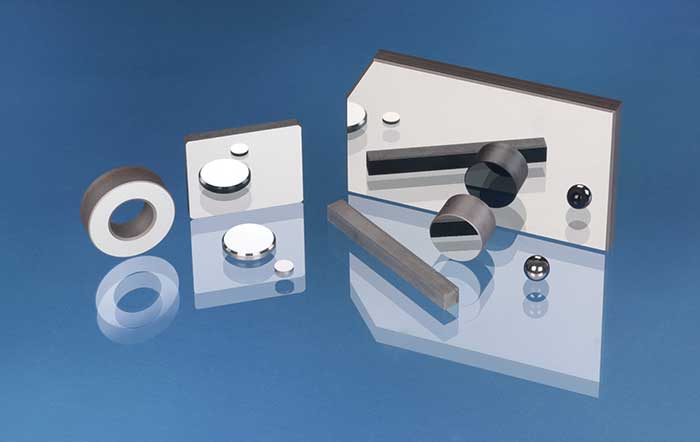
Chalcogenide glass blanks of different geometry are used for industrial molding processes and scientific investigations. Courtesy of Fraunhofer Institute for Production Technology IPT.
The challenge in reducing costs for infrared systems is the manufacturing process for infrared transmitting optics. Conventional optical glasses are transmissive within the visible range of 380 to 780 nm but have absorbing optical properties in the infrared range of 780 nm to 20 µm. Therefore, identifying cost-efficient, easy-to-handle infrared-transmissive materials is a crucial step regarding the integration of infrared optical systems into consumer products.
Currently, crystalline materials such as germanium are still predominantly used for many infrared optical applications. However, spherical optics can only be produced by means of grinding and polishing processes; crystalline materials with aspherical surfaces, on the other hand, are produced by employing single-point diamond turning. Due to the high costs of crystalline raw materials and the fact that the manufacturing technology is already highly developed, the possibility of bringing price points down further is nearly exhausted. In contrast, infrared transmitting chalcogenide glass is a suitable alternative to crystalline materials like germanium. Chalcogenide glass is obtainable at moderate material prices and offers a high potential for cost saving with respect to glass molding and manufacturing technologies. Glass molding is a replicative technology, which allows the production of thousands of glass lenses by using only one single molding tool. Consequently, costly single-point diamond-turning processes are shifted to mold manufacturing and do not have to be applied to every single lens produced. Chalcogenide-based infrared optics allow for new price points and offer high-volume consumer applications.
Wide transmission in the IR spectrum
Chalcogenide glasses are nonoxide glasses formed by chalcogenides of the element groups III to V. Most chalcogenide glasses are based on sulfides, selenides and tellurides of arsenic and/or germanium. Chalcogenide glasses offer wide transmission from an NIR range of <1 µm up to a 12-µm LWIR range. Crystalline infrared materials with similar transmission are, for example, germanium (Ge), gallium arsenide (GaAs), zinc sulfide (ZnS) and zinc selenide (ZnSe). The substantial difference between these crystalline materials and chalcogenide glass are the possible types of material processing. The amorphous structure, in conjunction with the viscoelastic state at a high temperature, allows for processing of chalcogenide glass by molding. Furthermore, chalcogenide glasses offer additional benefits in terms of optics design. Unlike germanium, which is widely used as an infrared material due to its high refractive index of n4 µm = 4.0 and low dispersion in LWIR, chalcogenide glasses offer significant advantages regarding material costs, a lower temperature dependency of the refractive index (dn/dT), high transmission at elevated temperatures as well as low dispersion in short- and mid-wavelength infrared range. The refractive index of commercially available chalcogenide glasses is in the range of n4 µm = 2.4 - 2.8, which is significantly lower than Ge and GaAs but considerably higher than ZnSe (n4 µm = 2.43) and ZnS (n4 µm = 2.25). Compared to the latter two, advantageously, the chalcogenides have lower dispersion and lower dn/dT. Recently launched glass types such as IRG27 directly offer further improvements regarding their thermo-optical properties (e.g., dn/dT).
Advantages of precision molding
For the design of optical components, the Rayleigh criterion is usually used for specifying production tolerances. The criterion states that the optical path difference of a wavefront after passing the optics must not exceed the value of a quarter of a wavelength. When the criterion is met, the optics have a negligibly small refractive error. Observing this criterion, the shape tolerance of chalcogenide glass lenses for infrared applications is in the range of 0.25 to 3 µm. In addition to shape accuracy, the surface quality, particularly the surface roughness, is decisive for the optical properties. A surface roughness of single-digit nanometers is usually required, while a higher surface roughness may lead to the occurrence of unwanted reflections. However, the required shape and surface tolerance always depends on the application.
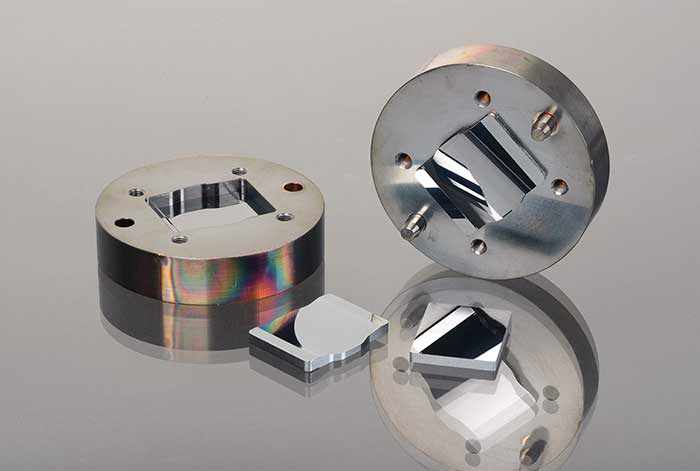
Molded acylindrical infrared lens (front left) with mold assembly (back left and back right) and cuboid glass blank (front right). Courtesy of Fraunhofer Institute for Production Technology IPT.
After the preparation of the geometric design of the infrared lens and the optimized optical design, the selection of a suitable manufacturing process is required. Elementary spherical lenses can be manufactured with minimal effort by using conventional grinding and polishing processes, whereas single-point diamond turning allows for the manufacturing of aspherical optics. However, the disadvantage of direct production by grinding and polishing arises from the individual production of each optics from a blank. The methods are time-consuming and place very high demands on vibration avoidance and temperature control with regard to ambient conditions, especially for infrared lenses with high geometric complexity. Furthermore, this abrasive machining process is accompanied by unnecessarily higher material consumption.
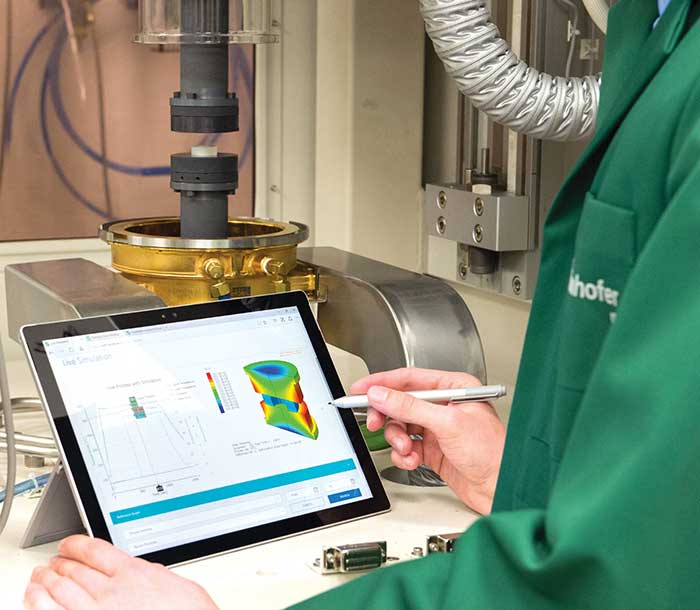
Process monitoring and finite element method (FEM) simulation in a production environment. Courtesy of Fraunhofer Institute for Production Technology IPT.
Precision glass molding is an innovative manufacturing alternative and a well-established process for manufacturing medium to large quantities of glass lenses with high precision. The process of high-precision glass forming involves a complete process chain. Starting with finite element method (FEM) simulation, the molds can be optimized regarding the glass flow as well as the thermally induced expansion or shrinkage of the glass geometry. Geometry data, which is determined in this way, serves as a starting point for the manufacturing of molding tools, which directly follows the simulative tool design. The tool system is designed in several parts, with the actual mold inserts being inserted into a mold die. The glass blank is placed on the lower mold and the entire system is at room temperature. The chamber closes and is then evacuated in order to prevent any tool wear due to the oxygen partial pressure. In a subsequent step, the glass blank and the tools are heated simultaneously and above the glass transition temperature by means of infrared radiation. At the glass transition temperature, the amorphous materials change from a hard and brittle state into a viscous or rubbery state.
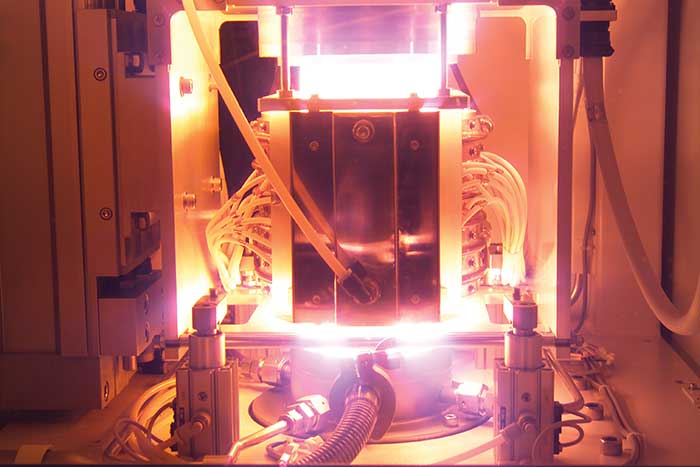
The heating chamber of a glass molding machine during the heating step: The glass blank and the tools are heated simultaneously and above the glass transition temperature by means of infrared radiation. Courtesy of Fraunhofer Institute for Production Technology IPT.
In order to eliminate any temperature gradients, a homogenization phase follows upon reaching the desired temperature. The molding process is conceived by the force- or path-controlled closing of the tools, followed by a holding phase during which the pressing force is changed and controlled nitrogen cooling is induced. After the temperature has fallen below the glass transition temperature, the glass is once again in a rigid state and can be cooled at maximum speed with meanwhile opened mold dies. The molded lens is then to be removed and, apart from possible antireflective coatings, ready for assembly. Additional surface finishing steps after molding are not required.
With precision glass molding, the high effort for machining optical surfaces is shifted from the single lens itself to the mold, which can be used for batch production of lenses. Thus, the more complex the lens geometries, the more advantageous the replicative manufacturing approach will be. Due to the rather low transition temperatures of some chalcogenide glasses (Tg <200 °C), the use of mold materials such as aluminum alloys, which can be machined by single-point diamond turning, has become increasingly common as they enable complex mold designs. Special alloys are used to meet the high demands on surface quality — for example, a fine microstructure and low iron content — and are produced in a melt spinning. In addition, wear-resistant coatings can prolong the lifetime of molds.
Molding small chalcogenide glass lenses with at least one aspheric surface is already state of the art and used by several lens suppliers. Employing diffractive structures superimposed on the aspherical surfaces is also increasingly common in order to integrate functionalities such as chromatic aberration correction. Due to the evolving molding technology for chalcogenide glasses, increasingly complex lens geometries will be available on the market.
Trends in glass molding
Recently, a milestone in establishing chalcogenide glass molding for high-volume consumer products was achieved. A new nitride-based coating extends the lifetime of molds by a multiple by preventing abrasive wear phenomena and averting unwanted glass adhesion. Thus, manufacturing costs of infrared optics can be drastically reduced.
Furthermore, Fraunhofer IPT and two industrial lens suppliers are in the process of upscaling from single cavity to wafer-level molding in a current consortium project. In wafer-level molding, a variety of glass lenses is produced in one single molding process. For this purpose, a chalcogenide glass wafer will fill out a mold and make a large number of cavities available during the molding process. After that, the individual lenses can be further processed following the separation of the individual lenses. However, wafer-level molding places special demands regarding tool concept and shrinkage behavior, which is why it is a key issue of current research projects.
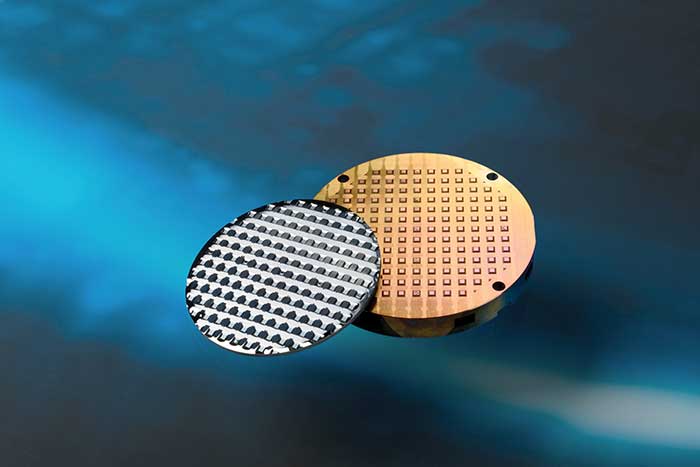
Wafer-level infrared optics made of chalcogenide glass, and its corresponding mold. Courtesy of Fraunhofer Institute for Production Technology IPT.
Another trend in chalcogenide glass molding is the application of “Industry 4.0” in order to optimize the production technology. Currently, “black box” conditions characterize isothermal precision glass molding. The process runs inside a hermetically sealed process chamber and, while the recording of measured values such as temperature or pressure is not affected, direct visual process monitoring is not possible. In order to access the information hidden in the process data, Fraunhofer IPT developed a process database concept — a specified data architecture that collects all process data during the entire process chain of precision glass molding. By analyzing the stored data, complex cross-process interactions can be identified, such as the influence of the mold manufacturing process on the lifetime of the molding tool. This knowledge is useful to devise further molding processes so that the ramp-up phase and ultimately the whole process run much more efficient.
Meet the authors
Marcel Friedrichs studied physics at RWTH Aachen University and received his MSc. degree in 2015. He is a research associate at Fraunhofer Institute for Production Technology IPT, responsible for the precision glass molding technology; email: marcel.
[email protected].
Holger Kreilkamp is group manager of optics at Fraunhofer Institute for Production Technology IPT. His research focuses on technology development for glass optics production with special interests in replicative manufacturing; email: [email protected].