Alana Achterkirchen, Rad-Icon Imaging, a Division of Dalsa Corp.
Current events have spotlighted the deep-sea
oil and natural gas industry and have drawn attention to the importance of nondestructive
testing (NDT) of critical oil and gas field equipment. For many reasons, leaks can
occur over time if the infrastructure is not monitored carefully. There is an inordinately
high cost of cleanup in the event of an oil leak or spill.
Until this point, the industry has relied largely on film-based
radiographic systems to monitor the integrity of its equipment. However, many companies
are beginning to adopt digital imaging technologies that have a long service life
and a high degree of accuracy in taking high-resolution images of their pipes during
the manufacturing process, during in-service operations above water and, eventually,
underwater.
However, the process of gaining acceptance for a new testing method
can be lengthy. One of the biggest challenges lies in validating the quality of
the digital radiography panel. Often, the new approach must be qualified by three
or four constituencies, including the company that performs the inspection, the
company that manufactures the tubing, the company that buys the tubing and, ultimately,
the company that insures the project.
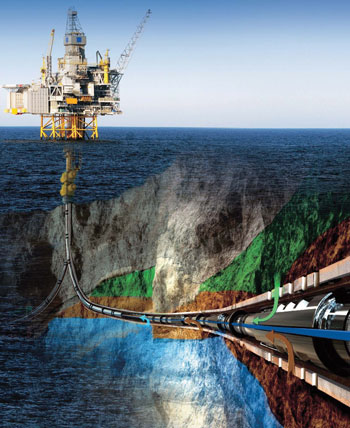
As proven petroleum reserves continue to decline and worldwide oil demand continues
to increase, most growth will be based upon improved recovery efficiencies from
increasingly complex oil reservoirs such as this. Courtesy of Roxar.
The risks in this industry, which run high, are the result primarily
of pipe manufacturing, joint welding, and pipeline corrosion or fatigue. From a
metallurgical perspective, there is no such thing as a flawless part, so the question
is whether the defects are at such an insignificant level that they will not eventually
propagate a problem. Changing an NDT inspection system is not easy to accomplish,
even if there are time, efficiency and inherent safety benefits in leveraging digital
imaging versus film. However, the oil and gas industry has made progress, much of
which is based on the pioneering work of the medical industry.
According to Jack Zsakany, general manager of Draka Engineered
Specialties, digital radiography has had to overcome not only industry resistance
to change but also fundamental resolution concerns and file storage standardization.
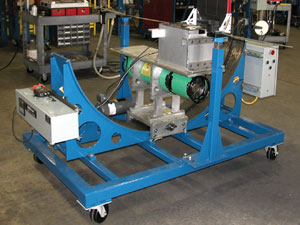
A subassembly of the CMOS x-ray imaging system is shown. Courtesy
of Draka Cableteq PTM.
“With new technology such as digital x-ray panels, resolution
can be much higher than traditional film,” Zsakany said. “This is tuned
by one’s ability to see the same wire image quality indicator as film –
no more and no less for purposes of product certification to a design standard.
To counter any concern that radiographers might digitally alter images, DICONDE-formatted
database storage includes the unaltered base image and applies the radiographer’s
filters on top of that. One can always return to the original source image. DICONDE
standardization of information fields and file storage has done a lot to gain credibility
for digital radiography and also demystify the process.”
Increasing efficiency
Draka Engineered Specialties (formerly Pressure Tube Manufacturing,
or PTM) of Bridgewater, N.J., is a wholly owned subsidiary of Draka Holding NV of
Amsterdam, the Netherlands. Draka Holdings, a €2 billion enterprise, is the
third-largest cable manufacturer in Europe and the eighth largest in the world.
Its New Jersey facility produces austenitic and duplex stainless steel and nickel-base
seam-welded tubing in outside diameter sizes from 1/8 to 5/8 in. Since 1910, Draka has manufactured wire products and, with the acquisition of PTM, the company now integrates these products into corrosion-resistant tubing in
lengths up to 50,000 ft or more.
One of the company’s distinguishing capabilities is the
manufacture of tube-encapsulated cable and pressure tube bundled together with multiple
tubes to create a polymer-encapsulated “flatpack.” These flatpacks can
be many miles in length and are installed in a gas or oil well for system monitoring
and control (for example, communicating with downhole pressure and temperature sensors,
controlling hydraulic valves and injecting chemicals).
Although the company has a long history of using film-based imaging
for oil and gas well infrastructure, it sought to leverage digital x-ray imaging.
The Draka team understood that the benefits of digital x-ray imaging would go beyond
gaining efficiency and reducing expenses. On the plant floor, digital imaging also
would simplify database cataloging and improve customer and supplier communications
due to the ease of sending digital images versus film.
The Draka team sought bids from four digital x-ray suppliers,
ultimately choosing Envision CmosXray LLC of Anchorage, Alaska. Envision knows the
oil and gas business, has extensive technical expertise in digital imaging and understands
the trade-offs in custom automation applications.
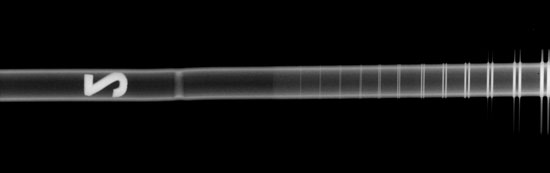
An x-ray image shows a pipeline joint weld. Courtesy of Envision CmosXray LLC.
Greg Davall, plant manager for Draka, said, “We were initially
concerned about the distance between Anchorage and Bridgewater, N.J. However, in
the bidding, design and fabrication processes, we found Envision to be more responsive
than other suppliers on the East Coast.”
When Ky Holland, general manager, and John Cope, vice president
of Envision, got the call from Draka, they arranged for Draka to see an Envision
system installed at Ethicon Inc., a division of Johnson & Johnson, based in
New Jersey. This system performs NDT imaging on laser-drilled microholes at the
end of suture needles used in heart surgery.
The digital solution
Envision provides complete digital imaging solutions and also
film-to-digital retrofits for oil and gas companies looking for semiautomated inspection
systems for their pipelines’ weld joints. The company’s CMOS Tubing
Inspection Cabinet (TIC) is the highest-resolution system available for small tubing
inspection. The mobile shielded system incorporates a computer-controlled, microfocus
x-ray tube; a high-resolution CMOS digital x-ray detector from Rad-icon Imaging;
and a rotational movement system for capturing images between 0° and 180°.
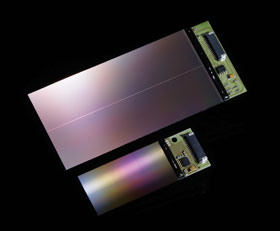
The RadEye1 and RadEye100 CMOS x-ray sensors are shown. Photo by Carter Dow Photography of San Francisco. Courtesy of Rad-icon Imaging.
Rad-icon’s CMOS x-ray detector has a 4 x 4-in. image area,
a 20- to 160-kV response, a spatial resolution of 50 μm (10 line pairs per
millimeter) and a dynamic range of 12 bits. Controlled by Envision’s EnSpect
image-capture software, the detector comprises a matrix of more than 4 million pixels,
each containing a photodiode to collect signal, an amplifier to read out the signal
voltage, and two switching transistors to address and reset the pixel. The image
area is divided into eight segments, which are scanned in parallel to minimize readout
time and increase the effective pixel rate. The image is scanned in a rolling shutter
process, starting at the center of the active area and proceeding simultaneously
to the top and bottom edges. All clock and control signals required to scan the
image are generated on-chip.
Envision’s TIC is designed for imaging weld joints for deep-sea
oil and gas applications. Hookups to wellheads at 5000 to 6000 ft require a massive
infrastructure to control underwater oil and gas facilities. High-pressure specialized
tubing as long as 10,000 ft is used to connect hydraulic controls in oil valves.
These tubes are manufactured from rolls of various grades of stainless steel in
short segments, which are taken out to sea by barge, then hooked up to the oil-drilling
platform. Each segment is welded to form the long pipeline, and these joints require
NDT imaging to ensure the integrity of the joint.
To inspect tubing and valves, the x-ray detector is placed on
one side of the joint weld, an image is taken, and the detector is rotated 120°
to take three views of the weld before moving on to the next weld. All of this takes
approximately 30 seconds. A technician receives the digital images within seconds,
evaluates the weld and, if it’s deemed solid, more tubing is uncoiled.
“Our Tubing Inspection Cabinet produces astounding images
of joint welds leveraging high-resolution CMOS x-ray panels,” Holland said.
“If your operation requires a significant number of NDT inspection images
over several months, a digital inspection system would quickly pay for itself and
would also increase the output of your plant.”
The net result
Draka’s design goals included reducing actual x-ray time
from approximately 1 min each for three shots plus the time to load film packs and
mechanically reposition the source, to less than 30 s to capture three digital x-ray
images with 120° rotation around the joint weld. Within a minute, the images
are displayed on a screen. Technicians can evaluate the image on the spot and either
decide to move to the next joint weld or send the file electronically across campus
for further evaluation.
The more traditional film-based process can take up to 45 min
to load a film cassette, capture an image, develop the film, unhook the entire assembly
mechanism and start the mechanism up again to capture the next image. Technicians
would have to walk across campus with the film if further evaluation were deemed
necessary.
Draka has optimized production focal length and integrated automation,
and it is in the process of production hardening with lead shielding. “In
manufacturing, we’re very excited about the potential for expanding digital
x-ray beyond this initial application,” Davall said. “The oil and gas
industry is recognizing that digital x-ray imaging has its place and can deliver
everything we need at a cost-efficient price. Our customers demand cost-effective
and efficient operations with the highest quality and safety.”
Meet the author
Alana Achterkirchen is the director of business development and
marketing for Rad-icon Imaging, a division of Dalsa Corp. of Sunnyvale, Calif.;
e-mail: [email protected].