Alan Chachich, Gentec Electro-Optics Inc.
Lasers, like other technologies, are continuously changing and progressing as a result of developments in other areas, such as in new solid-state or fiber technologies. As a result, power meters have had to keep pace with the technology and with the challenges brought on by new applications. Some of the advances have been slow and incremental, and others have been revolutionary.
• Evolving detectors. One example of evolving technology is progress in inertial-confinement fusion lasers, which concentrate unprecedented energies in a small space. This is a case of steady incremental improvement in vacuum-compatible, precision calorimeters in an effort to keep up with these lasers. These enormous lasers contain multikilojoules of energy density in beams that are perhaps 40 cm in diameter. Previous segmented absorber approaches seem to have reached their limit. In these devices, divisions between segments block the heat flow that builds up too high and cracks the absorber. But a 40 × 42-cm calorimeter using a monolithic absorber has been able to keep up (Figure 1).
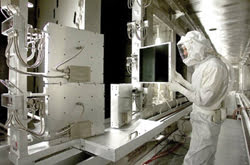
Figure 1. A technician at the National Ignition Facility tests four large calorimeters from Gentec Electro-Optics Inc. Courtesy of Lawrence Livermore National Laboratory.
• Evolvable detectors. In other cases, users’ needs change more rapidly. Instead of providing a new product each time, another approach is to build products that can evolve with those needs. An example is a handheld power monitor that uses the Windows CE operating system. As their needs change, users can download a new version of the monitor’s software from a Web site to get new capabilities, instead of buying a new monitor. The customer’s investment can remain on the cutting edge for a long time. A standard operating system requires less programming than a proprietary system, and that keeps costs down.
A similar development is software and hardware that let the customer use a computer as the monitor. That is ideal for users who want to control the measurements from a distance; for example, in a factory using high-power lasers for cutting or welding, where you don’t want people too close. The ability to monitor many detector heads from the same place is another advantage for the plant.
• Revolutionary absorbers. An example of an application that has accelerated absorber technology is semiconductor manufacturing that uses diode-pumped solid-state lasers under 100 W that put out extremely high average power density in relatively small beams. It is difficult for the absorber to withstand average power densities like that. Typical power detectors withstand maximum power densities of 200 W/cm2 to 20 kW/cm2. The highest was designed for this application and is capable of handling 100 kW/cm2. Even so, lasers are outgrowing it as they increase in power. Higher power means higher temperature. A material that withstands high power density at a low laser power may get into trouble as it heats up. To adapt, Gentec Electro-Optics developed proprietary materials to improve the capability of its higher-power detectors. Some detector head categories have seen an order of magnitude improvement in the last two years.
Robust, revolutionary
New disk thermopile technology employs an array of thermocouples that function at higher temperatures and so withstand higher laser powers in a smaller package. The smaller package is important to companies that make desktop laser manufacturing systems and medical equipment for doctors’ offices, and to people who service manufacturing equipment with tight optical trains.
Another innovation is a new modular cooling approach. Until now, the industry standard has been to integrate the cooling into the detector package. To the manufacturer, each design means more engineering expense and more stock to inventory. Consequences to users are higher costs and a smaller selection of capabilities. An alternative is to decouple the cooling from the detector. Users can mix and match existing detectors and cooling modules to save money and better meet their unique requirements from the larger set of possible combinations.
The power limit is set by the highest temperature the thermopile can reach before the thermocouples melt. More cooling allows the detector to measure higher powers. With the appropriate interchangeable cooling module, a detector’s range can be expanded by an order of magnitude. For example, one detector that tops out at 40 W standing alone can go to 100 W with a heat sink, 300 W with a fan and 400 W with a liquid-cooling module. Each module is easily swapped for any other (Figure 2). The detector standing alone is great in an optical train where there is not much room. The cooling modules trade off the space advantage for higher power capability.
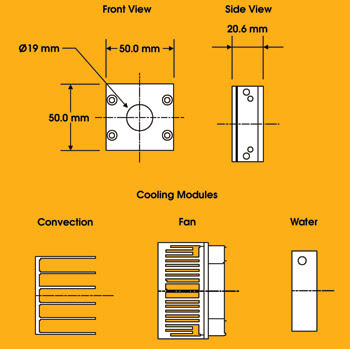
Figure 2. Appropriate interchangeable cooling modules can expand a detector’s range by an order of magnitude.
Stand-alone OEM applications demonstrate the leverage provided by the modular cooling approach. These applications often use closed-loop cooling systems that recirculate the same coolant internally, like in your automobile. This means that every component, including the laser and detector, is exposed to the same coolant, making contamination a problem.
This is a concern for newer diode laser systems. Formerly, a tube or plate transferred heat to the coolant. To achieve higher powers, the coolant now flows directly through the diode stacks. Most power meters are made from aluminum for its great heat-transfer property. Unfortunately, the aluminum leaches ions into the coolant that can damage the laser diodes. The modularity worked well when adapted for a medical equipment manufacturer using clean deionized water cooling. Instead of designing a whole new detector, only a stainless steel cooling module was needed — a far less costly solution.
Meet the author
Alan Chachich is director of product management at Gentec Electro-Optics Inc. in Quebec City; e-mail: [email protected].