Mass production of high-resolution displays utilizes ever-larger substrate panels, placing unique demands on the excimer laser systems used in their production.
RAINER PAETZEL and RALPH DELMDAHL, COHERENT INC.
Low-temperature polycrystalline silicon (LTPS) is increasingly used as the thin-film transistor material on the glass backplanes of high-performance displays, particularly for smartphones. These thin films are fabricated on large glass panels that then are singulated into hundreds of individual screens. Mass production of LTPS on these panels is uniquely enabled by excimer lasers, moreover excimer lasers with extremely high pulse energies. These high pulse energies are needed in order to reach the requisite high process threshold intensity over a large area.
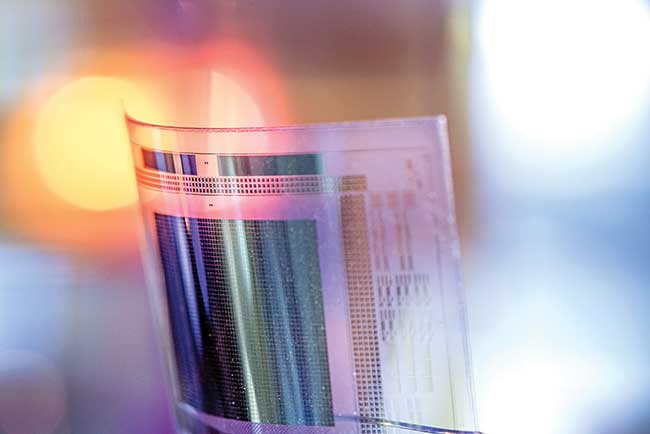
Excimer lasers enable high-volume manufacturing of flexible displays; a key step is laser lift-off where high-duty cycle excimer lasers are used to release the flexible displays from a rigid temporary carrier. Courtesy of Coherent Inc.
There is a fast-growing interest in extending LTPS to process larger area panels for several reasons: greater economy of scale, better and brighter mobile LCD screens, and the adoption of active-matrix organic light-emitting diode (AMOLED) smartphones and tablets. But as processes evolve to support ever-larger panels, new requirements are placed on the ultrapowerful excimer systems and the associated beam delivery and beam shaping optics used in the process. In what follows, the authors examine why excimer systems (laser, optics and internal diagnostics) are using modular architecture to deliver higher and higher energies with improved pulse-to-pulse stability and beam uniformity. For display manufacturers this means faster process throughput (screens per minute) and even better process consistency.
Polycrystalline silicon vs. amorphous silicon
The backplane of both active-matrix liquid crystal displays (AMLCDs) and AMOLED displays can be regarded as a type of large-scale integrated circuit, which starts as a 50-nm-thick film of amorphous silicon deposited on a thin glass sheet. For both display types, this is transformed into a network of thin-film transistors (TFTs) to enable each subpixel (red, green or blue) to be individually addressed.
Solid silicon can exist in three forms: single-crystal silicon, amorphous silicon (a-Si) and polycrystalline silicon (poly-Si). In single-crystal silicon, all the atoms are arranged in one giant, extended regular lattice. Large area, single-crystal silicon — as used in integrated circuit (IC) chips — is neither economically viable nor necessary for display applications. Rather, a-Si or poly-Si is used.
In amorphous silicon, the atoms are irregularly located with a high degree of disorder, resulting in the lowest electron mobility. In polycrystalline silicon, the atoms are arranged in microcrystals or grains, with discontinuities between the grains. The atoms can be highly ordered at the microscopic level, for instance, but disordered at the macroscopic level. This type has intermediate electronic properties, with the electron mobility and other parameters being highly dependent on the grain size and degree of order (e.g., grain size uniformity).
For AMLCD, the choice is a trade-off between performance and cost: The higher electron mobility of poly-Si maximizes circuit efficiency, enabling smaller area TFTs and narrower circuit traces. Reducing the size of these backplane components minimizes blocking of the backlight (which passes through this circuitry), making the display more efficient. In fact, poly-Si is key when it comes to AMLCD with a pixel density of more than 300 ppi. This holds true for most of today’s smartphones, where the
smaller screens and short viewing distances necessitate higher pixel densities (between 400 and 900 pixels per inch) to provide a crisp and brilliant appearance of the screen. Plus, electrical efficiency is even more critical in portable devices as it directly influences battery life.
AMOLED pixels emit light directly, so there is no backlight to block with control circuitry. However, stable, low impedance control circuitry is critical because each pixel draws current, making electron mobility and TFT current stability even more important for these displays. This makes poly-Si the only choice, and it is hence used for all small- to medium-sized AMOLED displays.
Reshaping the output beam for a narrow profile
When silicon is vapor deposited on the glass backplane, it naturally assumes the amorphous form. High-temperature annealing to create poly-Si is not viable as it would require temperature-stable panels made of expensive quartz. Therefore, the key enabler for low-cost, mass production of displays using conventional display glass was the 308-nm excimer laser for selective low-temperature polysilicon recrystallization. The excimer laser process to form poly-Si is commonly referred to as excimer laser annealing (ELA).
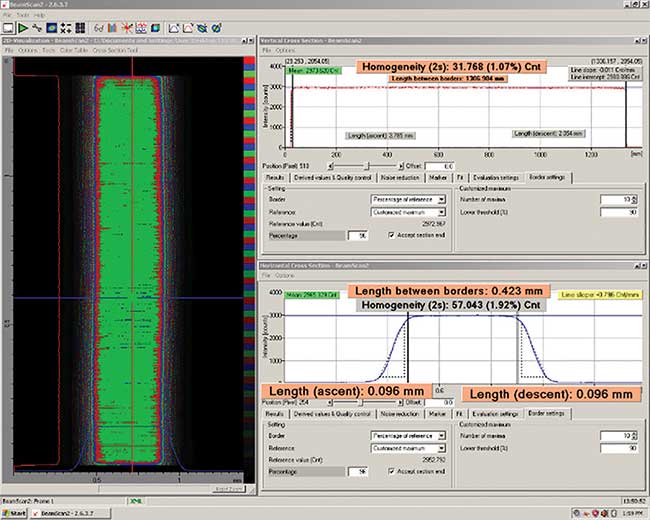
Anatomy of a 1300-mm process beam measured right in front of the display substrate. Courtesy of Coherent Inc.
In ELA, the excimer output beam is reshaped into a long narrow line profile. The length of the line ideally matches either the half or full width of the panel; hundreds of smartphone displays are eventually diced from each panel. The panel is translated under the line beam inside an ambient controlled chamber, ideally in a single-pass or in a two-pass scan process. The panel motion is matched to the 600-Hz laser repetition rate so that every part of the panel is irradiated by about 20 pulses.
The microcrystalline structure of the polysilicon determines the electron mobility and, hence, is very important to the quality of the final display. In turn, it is controlled by the laser pulse parameters, including the pulse energy, the number of pulses per location, the line beam profile (along both the long and short axes), the temporal profile of the laser pulse, and the pulse-to-pulse energy stability. For these reasons, display manufacturers buy a line beam rather than a laser; they need a complete system that delivers the precise line beam parameters their process requires. This necessitates a high degree of beam delivery system expertise by the laser vendor, including multiple levels of internal diagnostics and system monitoring at every stage of the enabling beam path.
Multi-oscillator = high-power excimer
Although LTPS is well-established in mass production, it is a very dynamic field. From the perspective of a laser beam supplier, the key trend is to support ever-larger panels. Specifically, the challenge is to provide a line beam profile that matches the width of these larger panels without sacrificing intensity (fluence) or any of the other system performance parameters that affect the quality of the final poly-Si.
The lasers used in ELA are the most powerful excimer lasers ever commercially developed, with pulse energies as high as 2 joules. This was a good match for creating a line beam profile up to 750 mm in length as needed for Gen 5 panels. But, soon a higher power level was needed to support the step up to Gen 6 panels measuring 1500 × 1850 mm. Moreover, a strategy was needed to scale to even larger panels in the future.
It is simply not practical to make the individual laser oscillator larger and longer ad infinitum. Scaling issues like cooling, discharge uniformity, control of beam quality, etc., preclude this. Instead, we chose a path of combining multiple lasers in a multi-oscillator concept, which resulted in VYPER, a very high-power excimer laser platform. And rather than maintaining the existing performance levels, we are doing this in a way that at the same time improves certain key performance characteristics, like pulse-to-pulse stability. It also provides a unique flexibility in terms of pulsing and temporal pulse shaping.
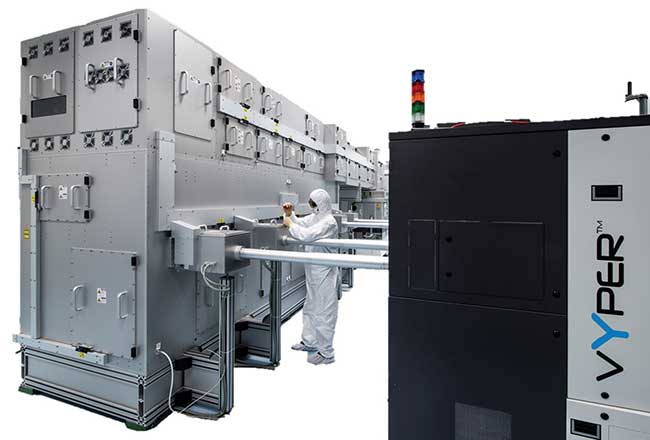
High-power scaling for large format poly-Si annealing shown here with two dual-oscillator VYPER lasers, with all four beams merging into a 1300-mm length processing beam. Courtesy of Coherent Inc.
Excimer laser annealing system with 1300-mm line beam length
Each individual VYPER oscillator can deliver a total power of 1.2 W (2 joules) at a 6000-Hz repetition rate. The first four-oscillator system increased this to 2.4 kW in 2013, providing a line beam length of 1300 mm for large-format LTPS production on Gen 8 display glass panels. Meanwhile the latest three-laser system developed in 2016 provides up to 3.6 kW using the combined power of six oscillators.
The two oscillators of the VYPER are arranged in pairs with a master and slave configuration. Patented synchronization circuitry accurately controls the time delay between the pulses of the slave and master. An active feedback loop is employed to maintain a stable delay between the laser pulses over the running period, with a typical accuracy of 2 ns.
In this way, a two-oscillator system user can overlap the pulses to provide a high energy of 2 J per pulse at 600 Hz. Optionally, the pulse delay can be adjusted to provide longer pulses, with peak power sustained up to twice the normal laser pulse duration (24 ns). This allows exploration of the subtle effects of pulse duration on microcrystalline structure optimization. And, just as important, the concept of using multiple oscillators provides even further scalability of the line length for Gen 8+ glass panel generations.
Uncompromised line beam uniformity and pulse stability
There are two ways in which multiple excimer laser beams could be combined to make a single line profile. First, the laser beams can be combined with near 100 percent overlap and the mixed beam then shaped to the final line profile. Or, the laser beams could be shaped then stitched together end-to-end to form the final line. We chose the former as this maximizes pulse-to-pulse stability at every location along the line.
Pulse-to-pulse stability is a particularly important process parameter impacting poly-Si crystal size uniformity. Specifically, the energy stability of each individual oscillator is between 0.25 and 0.3 percent sigma, well within the LTPS process window — in spite of the inevitable variations in repetitively firing a plasma discharge at tens of kilovolts. But, by combining and mixing the pulses from two oscillators, this random pulse-to-pulse noise is reduced by a factor of √2, for a final value of about 0.2 percent sigma.
The way in which the discharge is equilibrated between the pair of laser oscillators is another feature contributing to the low pulse-to-pulse variations and excellent timing synchronization of the two oscillators. The two laser tubes and their solid-state pulsed power supplies are, in principle, identical. The supplies are made identical in practice using a patented hardware module called EquiSwitch. This momentarily connects then disconnects the two-power storage systems so that they are equalized, immediately prior to firing the gas discharge. By eliminating any charge deviation on the storage capacitors, the switching behavior and the cycle time of energy through the circuitry is stabilized, resulting in long-term temporally synchronous output beams of nearly identical pulse energy.
Continuing evolution of laser annealing applications
In conclusion, excimer lasers have become essential to the fabrication of all advanced mobile displays we all now encounter on a daily basis. But, the technological needs of excimer laser annealing applications continue to rapidly evolve, concurrent with market pressure to reduce production costs. Excimer laser power and line length scaling have proven capable of meeting the market requirements, and straightforward system scale-up will carry this trend on into the future.
Meet the authors
Rainer Paetzel studied biomedical engineering at the University of Applied Sciences in Giessen, Germany. As director of strategic marketing for Coherent Laser Systems GmbH & Co. KG in Goettingen, Germany, his focus is on lasers systems used in flat panel display and microelectronics manufacturing; email: [email protected]. Ralph Delmdahl is product marketing manager for the Coherent Excimer Business Group. Delmdahl received his Ph.D. in physical chemistry from the Braunschweig University of Technology and his M.Sc. in economics from the Open University in Germany; email: [email protected]
Adapting Laser Lift-Off Technique for Flexible Displays
Excimer lasers optimized for high-energy pulses have applications beyond annealing low-temperature silicon, including mask-based direct patterning of microcircuits for cost-sensitive applications like medical disposables, where every year 20 billion disposable sensor circuits are created in thin metal on a flex substrate in a reel-to-reel process. Another is laser lift-off for next-generation flexible displays.
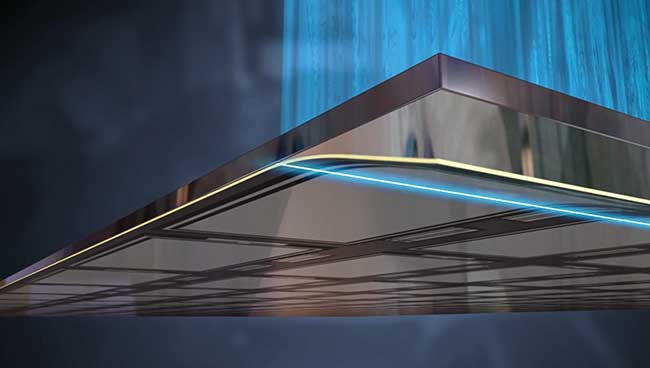
The transition from rigid to flexible display manufacturing is accomplished by separating the glass panel using an excimer laser line beam. Courtesy of Coherent Inc.
Laser lift-off with ultraviolet lasers is well-established in microelectronics. As an example, consider blue laser diodes, where the circuitry has to be created on, then removed from, a durable carrier substrate such as sapphire. The challenge with flexible displays is the sheer size of the product, which is hundreds of times larger than a typical IC chip and needs correspondingly higher laser power to complete the lift-off in an economically practical time.
In flexible display production, a glass panel that serves as temporary carrier for handling purposes is first coated with a polymer film. Display circuitry is then created on top of this layer. Finally, laser lift-off accomplishes the transition to full flexibility by passing an excimer laser beam (one pulse per area) through the glass carrier and vaporizing the top few atomic layers of the polymer. With the appropriate excimer laser line beam system, a Generation-4-size glass carrier (730 × 920 mm) containing 60 five-in. flexible displays is rapidly and gently separated applying only a few thousand laser pulses within seconds.