In laser powder bed fusion (LPBF) for the additive manufacture of metal parts, local high-temperature molten metal fits the surrounding solid part as a result of thermal expansion. As a negative byproduct of this process, the molten metal generates a negative thermal stress following solidification, which produces an in-plane residual stress.
This residual stress accumulates toward the upper layer with the repetitive formation process on each layer and often leads to undesirable effects such as delamination, cracking, and warpage.
Moreover, residual warpage and deformation are asymmetric in nature and scale with the size of the fabricated metal part. As a result, the integrated molding of large metal parts, such as rocket nozzles, is extremely challenging.
Schematic of the synergetic optimization strategy for laser powder bed fusion additive manufacturing. Courtesy of Akihiro Takezawa/Waseda University.
To address this issue, a team of researchers from Japan and the U.S. proposed an optimized design strategy for additive manufacturing (AM). The team used multiple, distinct processes in the course of the work, including a numerical methodology called “recurrent formula inherent strain method.” This method allowed the team to analyze the residual deformation. The researchers modeled the lattice based on the effective stiffness and anisotropic inherent strain using a gradient-based optimization algorithm.
According to team leader Akihiro Takezawa, a professor from Waseda University, the team’s advancement is in the development of a method to reduce residual deformation by simultaneously optimizing the internal structure of the fabricated part and the laser scanning direction.
In LPBF AM, the team simultaneously optimized two aspects of the fabrication process: the laser “hatching orientation,” or scanning direction that uses the asymmetry of residual stress, and the internal structure of the fabricated material, or the “lattice density distribution,” by considering layer-wise residual stress stacking.
Accordingly, the team fine-tuned its methodology to ensure the synergetic influence of simultaneous optimization.
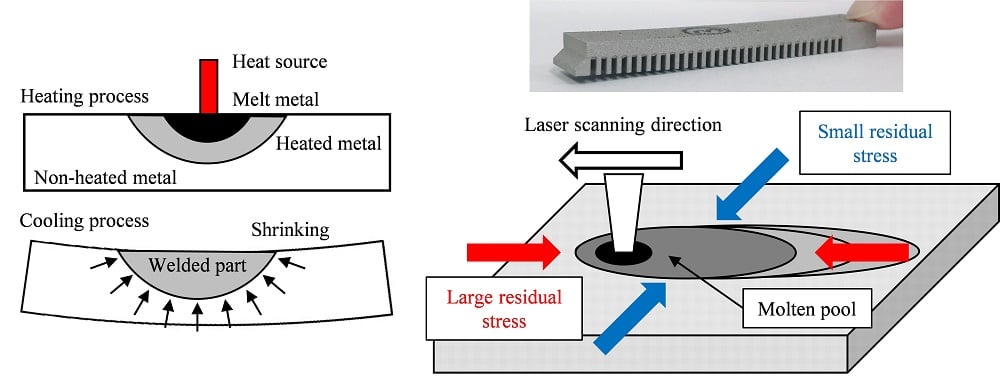
Illustration depicting warpage introduced during laser powder bed fusion additive manufacturing. Courtesy of Akihiro Takezawa/Waseda University.
In addition, the team performed experiments to verify its novel methodology using quasi-2D plates, 3D brackets, and 3D connecting rods. Compared to the standard benchmark designs that are currently used, the team’s design strategy reduced vertical edge deformations by 23% to 39% in quasi-2D plates. In the cases of 3D brackets and connecting rods, the warpage reductions ranged between 13% to 20%.
The researchers believe the methodology could herald a remarkable development in 3D printing using LPBF fabrication. As recent improvements in metal 3D printing technology have made it possible to produce larger molded parts, according to Takezawa, in this light, the team’s methodology supports the ability to enable 3D printing of any large metal part.
The research was published in Additive Manufacturing (www.doi.org/10.1016/j.addma.2022.103194).