Friedhelm Dorsch, Trumpf Laser GmbH + Co. KG, member ISO/TC 172/SC 9/WG1
Laser diodes are well-established in both telecom and commercial applications. Semiconductor laser sources emitting power in the milliwatt range are produced in millions. Besides other specific attributes, they are characterized by high efficiency, high reliability and long lifetime. In conjunction with easy modulation, this made the breakthrough for optical communications possible. Large production volumes resulted in standardized housings and test methods, including those to describe lifetime expectations. The appropriate standards for lifetime and reliability testing for telecom applications are described in Telcordia or International Electrotechnical Commission (IEC) documents.
As output power has increased, semiconductor lasers have also entered industrial applications; e.g., as pump sources of solid-state lasers and more recently as direct laser sources for specific applications in materials processing. With increasing output power and brightness, the range of possible applications will expand further.
Many requirements for laser diodes in industrial applications coincide with those for telecom, but some diverge. Telecom installations, especially if they are underground or deep-sea, demand extremely high reliability and long lifetime, which are frequently achieved by operating the devices at reduced output power. For industrial applications, reliability is also very important but on a different timescale. Typical industrial requirements demand tens of thousands of hours.
On the other hand, especially in the market for devices with very high power (several hundred watts and up), the price of the optical power is important. If there is too much of a trade-off of output power for more lifetime, the costs of the usable power rise, making the laser application too expensive.
Another difference between industrial and telecom semiconductor lasers is the required output power — several watts compared with milliwatts or a few watts. The design of the semiconductor as well as the packaging and housing might differ completely. For high-power industrial applications, laser bars are used very frequently. These are typically 10-mm-wide arrays of semiconductor lasers that emit tens of watts of continuous-wave power. To further increase power, engineers often assemble several of them into complex arrangements, which might include micro-optical elements for beam shaping. Those devices are much more expensive than small telecom laser diodes and are not produced in such large quantities. This limits the capability and availability of identical test samples to perform lifetime and reliability tests, as is done with telecom devices.
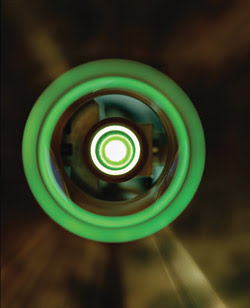
High-power laser diodes can be used to pump Yb:Yag thin-disc lasers, which are perhaps the most advanced class of solid-state lasers.
In the mid-1990s, when industrial applications of high-power laser diodes gained in importance, the vendors were increasingly asked to provide reliability data. However, how these data had been gathered and evaluated varied among manufacturers, and the users were concerned about different information from different sources that could hardly be compared. It was not uncommon to find a discrepancy between lifetime data published by the manufacturers and everyday experience in the industry.
Standardization needs
Therefore, the need for an international standard for lifetime testing of laser diodes was addressed several times by the responsible Technical Committee ISO/TC 172/SC 9 (Optics and optical instruments — Electro-optical systems) of the International Organization for Standardization (ISO), which represents laser manufacturers, researchers and industrial users. After discussion and delineation of telecom laser diodes (in the low-power range), for which standards already existed, an international project team of experts from six countries was initiated in 1999. This team was strongly supported by the Joint Working Group, founded in 1997 to avoid conflicts between the laser diode standards of IEC and ISO.
During the development of the ISO standard, it turned out that, for industrial applications, laser diodes and any other type of laser can and should be handled by the same means. Regarding lifetime and reliability, all types of lasers — including laser diodes — should be treated equally.
In early 2002, the major work of the ISO project team was done and the Draft International Standard was circulated to the ISO member countries for comment and a vote. The comments were incorporated and the final draft accepted in April. Now the standard ISO 17526, called Optics and optical instruments — Lasers and laser-related equipment — Lifetime of lasers, is awaiting publication this summer.
This standard applies to all types of lasers (except telecom applications) that show varied, if not completely different, characteristics. Some lasers, such as the CO2, can be repaired and their main components exchanged, whereas the components of others, such as sealed-tube gas or semiconductor lasers, cannot be repaired. The CO2 is characterized by a mean time to failure, and the latter types more adequately by a lifetime value.
Laser applications require various modes of operation. Consequently, ISO 17526 allows lifetime tests under different modes and conditions, but all parameters and test results must be reported clearly and completely. Modes of operation — CW, repetitive CW and pulsed — distinguish between various temporal characteristics, and operating conditions refer to the conditions of the lifetime test. For laser diodes, a lifetime test can be performed at constant current (automatic current control mode, or ACC) or at constant optical output power (automatic power control mode, or APC) by adjusting the current.
During the test, the course of the controlled value is recorded, and a degradation rate is determined. In both cases, an end-of-life criterion is defined, which corresponds to a power drop to α percent or a current increase of (100-α)/α above threshold current. The lifetime is determined by extrapolation of the recorded degradation curve to the point where the end-of-life criterion is met. But the allowed extent of extrapolation depends on the number of test samples and the variation of the test results.
Extrapolating to lifetime figures of 100,000 hours based on a 3000-hour test of 10 samples, for example, is not allowed.
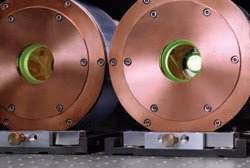
The standard ISO 17526 is awaiting publication this summer. This standard applies to all types of lasers (except telecom).
Of course, this article can give only a short overview of the intention and ideas of ISO 17526. The standard has to prove its usefulness and applicability after publication. It must be adopted by the industrial users. Possible and necessary improvements and extensions that may come up throughout practical use will be discussed within the ISO committee and might result in revisions. For the time being, ISO/TC 172/SC 9 hopes for a broad acceptance of the laser lifetime standard.
Contact: Friedhelm Dorsch, Trumpf Laser GmbH + Co. KG, Schramberg, Germany; +49 7422 515 467; fax: +49 7422 515 140; e-mail: [email protected]. Dorsch also is a member of ISO/TC 172/SC 9/WG 1.