Optical mirrors made of floated borosilicate glass installed at the Hobby-Eberly Telescope Dark Energy Experiment will help paint a more detailed picture of dark energy and the universe’s expansion.
TINA GALLO, SCHOTT NORTH AMERICA INC.
Large telescopes all across the world stare into the sky day and night, waiting to uncover the secrets of the cosmos. For the Hobby-Eberly Telescope, the world’s third-largest optical telescope, located at The University of Texas at Austin’s McDonald Observatory, that means setting its sights on one of the most mysterious forces in the universe — dark energy.
Contrary to earlier beliefs that the universe is static, it is now assumed that it expands. The force driving this expansion, which seems faster than many scientists once thought possible, is dark energy, and though we don’t know much about this force, we do know that dark energy and its counterpart, dark matter, make up close to 95 percent of the universe (about 74 and 21 percent, respectively). Only about five percent of the universe is made up of normal matter — the stars, planets, and the gases that we can more easily observe.

The mirror of the 9.2-meter Hobby-Eberly Telescope (HET) is visible through the open louvers in this twilight view. Courtesy of Marty Harris/McDonald Obs./UT-Austin.
Specialized optical mirrors installed at the Hobby-Eberly Telescope Dark Energy Experiment (HETDEX) will help advanced equipment paint a more detailed picture of the universe, which scientists hope will explain the nature of dark energy and the universe’s expansion. The performance requirements for these optical mirrors are extremely rigorous, as slight deviations can have significant impacts on research results. That’s why scientists use mirrors made with a specialized floated borosilicate glass that can meet the strict demands of the telescope.
Looking back to the Big Bang
Astronomers once believed that, following the Big Bang 13.7 billion years ago, the universe would go through rapid expansion but would then slow down. However, recent research shows that parts of the universe continue to expand at faster-than-expected rates. The theory is that dark energy contributes to this fast expansion, but it’s a force we know little about. Therefore, scientists measure the expansion of the universe by studying light, which moves at a known and constant rate, in hopes that it adds to our understanding of dark energy.
The research at HETDEX is being conducted by dozens of scientists affiliated with a number of higher education institutions and public research branches from around the world. The telescope’s mission is set to explore dark energy, massive black holes and the earliest stars in the universe.
One of those research projects is called the Visible Integral-Field Replicable Unit Spectrograph (VIRUS), which is comprised of 150 individual spectrograph mirrors made from specialty borosilicate glass and almost 40,000 optical fibers. Both its number of mirrors and fibers are greater than in most spectrograph arrays. The 150 spectrographs will measure the light from distant galaxies, breaking it down into individual wavelengths. The spectrograph’s sensors will then analyze the light emitted from more than 1 million galaxies between 9 to 11 billion light years away.
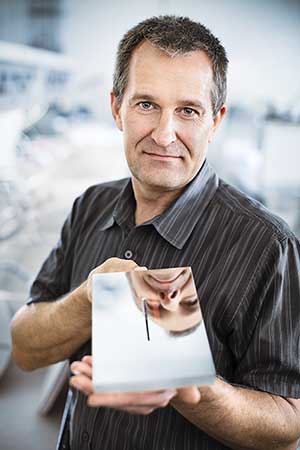
Specialized borosilicate glass was used in the 150 individual spectrograph mirrors in the Visible Integral-Field Replicable Unit Spectrograph (VIRUS) project, part of research at the Hobby-Eberly Telescope Dark Energy Experiment (HETEX). Courtesy of Schott.
By analyzing these wavelengths, researchers hope to better understand the chemical composition and temperature profiles of those galaxies. In addition, the spectrograph array will help determine how fast the galaxies are moving, data that will be used to create a 3D map of the universe. VIRUS is still being tested and installed, but its mission is slated to begin this year.
VIRUS is a special application that has unusual demands. Provided with sophisticated tasks and exposure to rough environments, these optical mirrors must possess a number of characteristics: high thermal stability, excellent transmission and a low refractive index. Plus, the mirrors must be extremely flat and have an exceptional surface quality so a thin, film-like coating can be applied. The material that meets such stringent requirements is Schott’s patented BOROFLOAT glass, a high-quality borosilicate glass, which was further machined and specialty coated.
Added strength through the fifth element — Boron
Borosilicate’s namesake is the element boron, which serves — similar to silica — as a glass network former and adds to the glass’s high chemical durability and superior mechanical strength. During melting, boron and alumina are mixed with traditional silica and other components commonly used in glass production to create a stronger, more rugged glass. The high amount of boron oxide in the glass composition strengthens the chemical bonds within its network and is responsible for the exceptionally low thermal expansion behavior and low refractive index (nd = 1.471). Together with the material’s superior transmission, these characteristics are key requirements for precise spectrometer measurement results required for the HETDEX project.
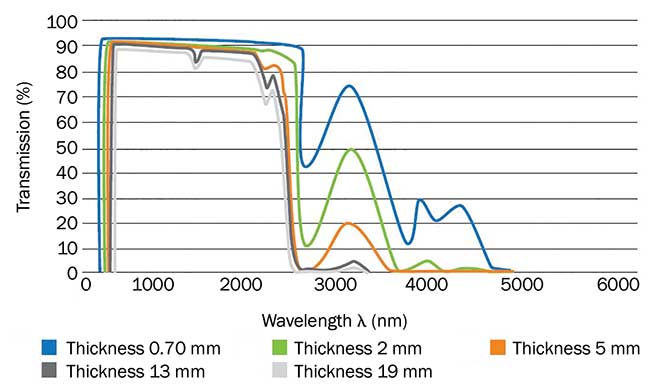
Figure 1. Low iron impurity levels result in BOROFLOAT glass’ excellent optical transmission. Courtesy of Schott.
The chemically resistant glass is traditionally utilized wherever excellent resistance to high or changing temperatures is required, such as sight glasses for the chemical and petroleum industry. However, due to its outstanding transmission it is also used as a substrate in many optical applications, such as optical filters, hot and cold mirrors, or the VIRUS specialty spectroscope mirrors. As its thermal expansion coefficient of 3.25 × 10−6 K−1 is perfectly matched to that of silicon, it is also the glass of choice for anodic bonding or as a carrier wafer for temporary wafer processing. The low, nonbridging oxygen holes in its glass network are responsible for a high radiation resistance (low glass darkening) making it a good candidate as a component in x-ray radiation technology.
Optical characteristics
Light transmittance is significantly impacted by the impurity levels of the raw materials used and depends on the thickness of the optical glass panel. BOROFLOAT glass is offered as thin as 0.7 mm and up to 1 in. thick and is the industrial flat glass with the lowest iron impurity level allowing for transmission values of over 90 percent (Figure 1) and reduced solarization tendency in the UV range (Figure 2). The glass was machined and coated by Precision Glass & Optics.
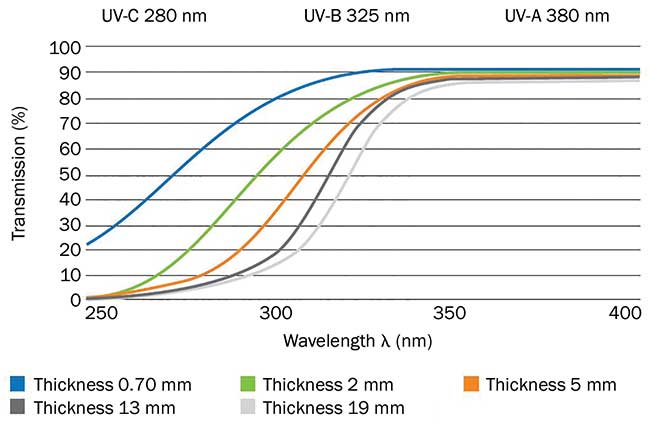
Figure 2. Exceptionally high UV transmission is a key benefit for low wavelength applications. Courtesy of Schott.
Solarization is a “glass-darkening phenomenon,” which typically occurs in multicomponent glasses and depends on the glass structure, the emitted light spectrum, the radiation source and the radiation exposure dose. High energy doses can generate structural micro- and nano-electronic defects, which are then absorbed at short wavelengths resulting in a UV-cutoff shift in the light transmission curve. Such radiation-induced defects tend to solarize depending on impurity levels of polyvalent ions, such as iron (Fe2+/Fe3+) in the glass composition. Technical glasses usually have iron impurity levels of several hundred ppm. Pure raw materials were used in manufacturing the glass for the VIRUS mirrors, resulting in extremely low iron impurity levels (approximately 85 ppm Fe2O3), which tend to solarize much less intensely than other flat glasses (Figure 3).
The optical mirrors used in VIRUS capitalize on the glass’ high transmission, allowing VIRUS sensors to read and record the incoming light more accurately, adding to the mission’s precise data collection.
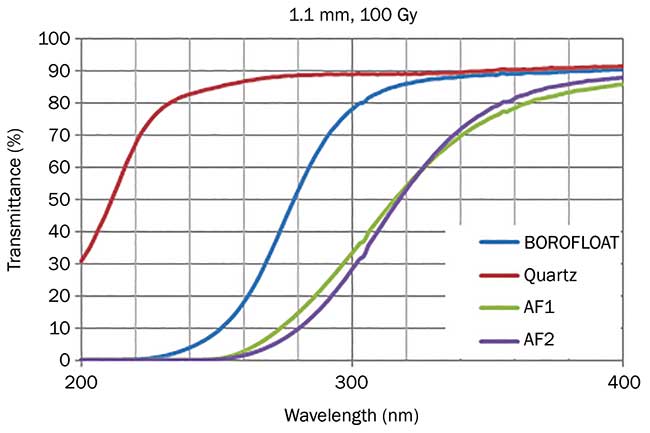
Figure 3. A comparison of UV transmission after radiation exposure. Gy = gray unit. Courtesy of Schott Nippon K.K.
Thermal properties
An optical mirror with high thermal stability was an especially important requirement for the HETDEX project because of its location; the Hobby-Eberly Telescope sits 6,600 ft above sea level and experiences seasonal temperature and weather fluctuations, including snow in the winter and hot sunshine in the summer. Borosilicate glass’ higher concentration of silica, fewer alkali oxides, added boron trioxide and alumina create a much more compact glass network compared to regular soda-lime glasses, resulting in borosilicate glass’ extraordinarily low thermal expansion behavior (Figures 4 and 5).
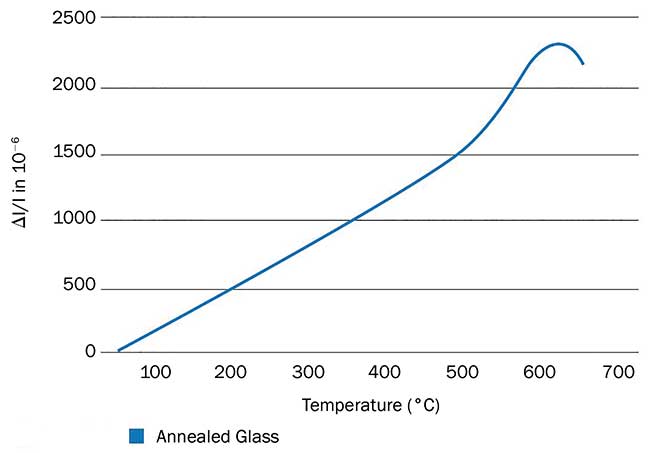
Figure 4. The low thermal expansion coefficient results in superior resistance to thermal gradients. Courtesy of Schott.
Boron again plays the key role in the performance of the glass, as it allows the specialty glass to easily resist the expansion and contraction stresses that temperature changes would typically cause. Hence, this borosilicate glass ensures high resolution and consistency in researchers’ observations as it does not warp and delivers undistorted measurements even under the harshest environments.
Pristine surface allows for high-performance coatings
For optical mirrors the glass substrate must be extremely flat and without inconsistency or imperfection. Glass produced using a float manufacturing process, in which molten glass floats over a bed of molten metal and then cools, provides highly homogeneous and flat surfaces.
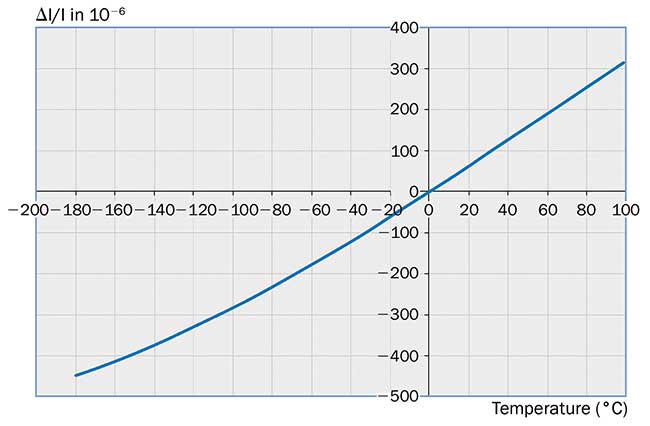
Figure 5. The low thermal expansion coefficient contributes to excellent cryogenic behavior. Courtesy of Schott.
The performance requirements for optical mirrors are also highly dependent on the material’s ability to reflect, absorb, enhance or modify incoming light. This can be accomplished with bulk optical glass materials or through coatings that are applied to a pristine glass substrate. Coatings usually allow significantly more freedom for customized light management design options, which can be developed even further when a flat, homogeneous and temperature-resistant glass substrate like BOROFLOAT glass is used.
The fold mirrors for the VIRUS collimator required an operational wavelength range of 345 to 700 nm and are optimized from 350 to 590 nm with average reflectivity of greater than 99 percent and exceeding 95 percent between 345 to 700 nm. The absolute reflectivity is greater than 98 percent between 350 to 590 nm and greater than 92 percent at 345 to 700 nm. The angle of incidence is 12.5±5°. In order to meet such requirements, a special 57-layer coating using Ta<sub>2</sub>O<sub>5</sub> and SiO<sub>2</sub> was designed using electron-beam evaporation with ion assist. Other optical specifications include a surface figure of λ/8 at 632-nm root mean square (rms) surface quality at 40-20 scratch-dig and surface roughness of 2-nm rms.
This coating, applied by Precision Glass & Optics, has to perform in extreme environmental conditions (−25 °C to 66 °C) and meets Mil-C-48497 abrasion/adhesion durability standards.
Mechanical strength and stability during processing are essential in order to produce high-precision mirrors. Boro-silicate glass’ exceptional surface hardness and abrasion resistance compared to other glass substrates were beneficial for the manufacturing of the VIRUS
spectrograph mirrors.
A mile above sea level, searching for answers
Large-scale, modern research projects require precision instruments and materials in order to guarantee the most accurate results. The data derived from VIRUS and HETDEX could give researchers and scientists a thorough understanding of the early universe and the forces that drive
its expansion.
The spectrograph mirrors in HETDEX must be made of high-precision specialty glass to ensure the longevity of each individual spectrograph in the large mirror array for many years to come. The sum of its properties make floated borosilicate glass the ideal material for such specialized optical mirrors.
The composition of this special borosilicate glass is not only tailored toward excellent optical properties, but it’s also designed to exhibit minimal thermal expansion. The sophisticated coating applied to the extremely flat surface enhances properties in VIRUS spectrograph mirrors that could help researchers to finally uncover the secrets of dark matter and help us to better understand the universe.
Meet the author
Tina Gallo is applications manager for Schott North America Inc. in Louisville, Ky. She earned her master’s degree in materials science from RWTH Aachen University, Germany; email: [email protected]