A rarely discussed approach to military high-power lasers may also be suitable for commercial applications.
Mark D. Rotter, C. Brent Dane, Scott Fochs, Kai LaFortune, Roy Merrill and Bob Yamamoto, Lawrence Livermore National Laboratory
Under the support of the US Army's Space and Missile Defense Command, and in collaboration with industrial partners Boeing, General Atomics, DRS, Decade Optical Systems and others, we are developing high-average-power (100-kW class) mobile laser technology for applications including humanitarian mine clearing and tactical short-range air defense missions. The ultimate vision is an electrically powered, solid-state laser that can be deployed on a hybrid-electric vehicle.
There are a number of ways to obtain high-average-power operation of a laser suitable for defense applications, and chemical and solid-state lasers are the two leaders. Chemical lasers tend to operate in a high-average-power mode, producing record average powers, but they have a twofold disadvantage: They tend to be large and not very mobile, and the byproducts of their lasing process can be toxic and harmful to the environment.
Solid-state lasers are more compact and environmentally friendly. If scalable architectures without the need for complex beam combining is the goal, the output should be generated in a single aperture. This feature can be achieved in what is known as the heat-capacity mode of operation.1
Operating modes
To understand the concepts behind this process, let’s consider three modes of laser operation. The first is single-shot, in which the time between firings is very long. High-power/high-energy lasers, such as the National Ignition Facility laser at Lawrence Livermore National Laboratory in Livermore, Calif., operate in this mode. Only prompt thermal effects in the solid-state lasing medium are considered, and ambient cooling of the medium occurs after the shot. The prime power source supplies lasing power only, and the beam propagates in the absence of thermal cooling gradients.
The second is steady-state, a typical operating mode for ion lasers and certain solid-state lasers such as Nd:YAG or Nd:YLF. To enable operation, the lasing medium is cooled at the same time it is being pumped. As a result, the prime power must supply both lasing and cooling power, and the beam propagates in the presence of thermal cooling gradients. Unless special precautions are taken, the wavefront quality of these lasers is not very good because thermal effects in the laser medium tend to distort the beam.
The heat-capacity mode of operation falls between these two regimes. Here, laser operation rapidly adds single shots, and the waste heat is allowed to accumulate in the lasing medium. The prime power first supplies lasing and then cooling needs. Because the laser is operated in the absence of thermal cooling gradients, far fewer stresses are induced on the lasing medium, and optical distortions are minimized. If, in addition, the medium is face-pumped, compressive stresses occur at the surface. This minimizes the possibility of fracture in the medium.
Heat-capacity lasers, which are excited by a series of rapid-pump light pulses, emit a series of pulses, each lasting as long as the corresponding pump pulse. The laser’s temperature never reaches an equilibrium value but continues to rise until the thermal population of the lower laser level significantly diminishes the output. At that point, the pump source is shut down, and the temperature begins to drop. Thus, the output consists of a burst of power that contains many shorter pulses.
Scientific proof of principle
In 2001, as an initial scientific proof of principle, and to establish a solid technical basis for the heat-capacity mode of laser operation, we constructed a flashlamp-pumped, Brewster-angle, Nd:glass solid-state heat-capacity laser (Figure 1). The average-power goal was 10 kW (500 J per pulse at a 20-Hz repetition rate). This milestone was significantly exceeded when we obtained an average energy per pulse of 640 J. With the 20-Hz repetition rate, this resulted in an average power approaching 13 kW during the 10-s burst.
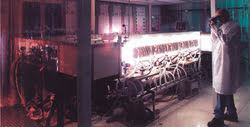
Figure 1. The flashlamp-pumped solid-state heat-capacity laser produced greater than 10 kW of average power during a 10-s burst.
A major milestone in the Solid-State Heat-Capacity Laser Program is the construction of a very high power system that can be cooled rapidly between bursts. To achieve the desired output power and cooling time, several design changes had to be made to the laser. The requirement of a short cooling time forced us to abandon glass as a lasing medium (the thermal diffusivity of glass is relatively low) and to replace it with crystalline media.
In a heat-capacity laser, the path to higher average power is not through the conventional method of increasing the energy per pulse, but rather by increasing the pulse repetition rate. Thus, a 100-kW-class laser will still operate at 500 J per pulse, but the pulse repetition rate will be increased from 20 to 200 Hz. Therefore, laser diodes must replace the flashlamps.
Both of these changes resulted in a laser system that is far more efficient than the flashlamp-pumped Nd:glass system described previously. We have identified Nd:GGG (gallium gadolinium garnet) as the laser material of choice, thanks to its high thermal diffusivity (roughly 10 times greater than that of glass), its greater emission cross section (five times larger than glass’s) and its greater fracture stress (five times larger than glass’s). An additional advantage of GGG is that large slabs may be cut from the boule.

Figure 2. In the pump geometry of a diode-pumped Nd:GGG heat-capacity laser, each slab is pumped by four diode arrays. The individual bars in each array are oriented to direct their output at ~45° to the array surface, as indicated by the arrows.
Another potential laser medium, YAG, has a “core” of crystal imperfections running down the center of the boule that severely limits the size of the slab that may be extracted. In the diagram of a “building block” for the diode-pumped Nd:GGG laser (Figure 2), we note that, in contrast to the Nd:glass 10-kW laser (where the glass slabs were oriented at Brewster’s angle with respect to the optical beam), the laser slabs are normal to the direction of the beam propagation. This results in not only a more compact system, but also one in which wavefront distortions caused by thermally induced slab deformations are drastically reduced. To achieve a desired output power, one simply adds on building blocks and/or increases the cross-sectional area of the laser slab.
Of course, what makes it possible to achieve high average power in a compact volume is the use of laser diodes as the pump source (Figure 3). The array consists of nine rows, each comprising 80 laser diode bars operating at 808 nm.
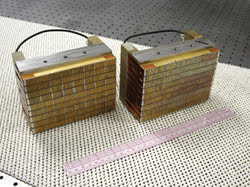
Figure. 3. Typical laser diode arrays produce approximately 75 kW of peak optical power each. A foot-long rule is in front of the arrays. Courtesy of Armstrong Laser Technologies.
Each bar can deliver slightly more than 100 W of peak optical power; the array as a whole can produce a peak of approximately 75 kW. We have operated the arrays for several minutes at a time at a 10 percent duty factor, for an average optical power of 7.5 kW.
To arrive a step closer to a fieldable system, we developed the four-slab test bed (Figure 4), a laser with four Nd:GGG slabs and a maximum square, clear aperture of 10 cm per side. Each slab is pumped by four 75-kW diode arrays, for a total peak pump power of 1.2 MW.
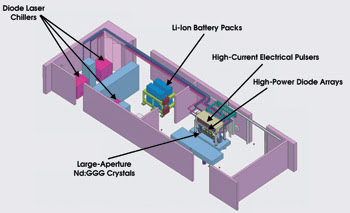
Figure. 4. This test bed is designed to be a laser with four Nd:GGG slabs.
The test bed is envisioned as a workhorse for refining various components of a mobile solid-state heat-capacity laser. As an example, one drawback to the heat-capacity mode is the downtime of the system during laser media cooling. If a hot laser slab could be exchanged for a cooled slab, nearly continuous operation could be achieved.
This is the idea behind the “gain medium exchange” concept developed by General Atomics in La Jolla, Calif. (Figure 5). In this embodiment, two slabs are used. The slab in the lasing cavity is in the center, with four diode arrays (two on each side), as is usual. The slabs are mounted on a motorized linear translation stage that shuttles them from position to position, so that when one slab is lasing, the other is being cooled.
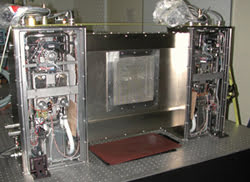
Figure 5. The gain media exchange apparatus holds two slabs, so that as one slab is lasing (center), the other is being cooled at one of the two cooling stations situated on either side.
Downtime eliminated
Cooling is achieved by bringing a cold plate in close proximity (separation of 0.1 mm) to the laser slab. The transit time from the center position to one of the cooling stations (at either end of the apparatus) is less than a second. By translating the slabs back and forth, laser system downtime during cooling is essentially eliminated. This method will be implemented on our four-slab test bed this summer.
The test bed also will be used to examine fundamental physics issues, such as output energy as a function of time during the burst. In an early experiment, using a 6.7-cm clear aperture, we measured the output energy from the test bed as a function of time during the course of a 4-s burst (Figure 6).
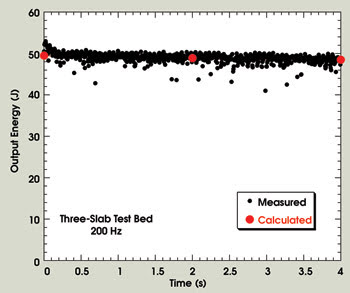
Figure 6. In this plot of output energy as a function of time for three 6.7-cm clear-aperture slabs, the output energy should decrease slightly more than 10 percent over a 10-s burst.
At the beginning of the burst, we achieved an average output power of 10 kW (50 J per pulse at a 200-Hz repetition rate). Also shown on the graph are the results of calculations using our laser oscillator model — the model tracks the fall-off in energy quite well. From these calculations, we estimated that at the end of a 10-s burst, the output energy decreased approximately 10 percent from its initial value.
We also operated the system with four 10-cm slabs. Under these conditions, we achieved an average output power of ~30 kW (150 J per pulse at a 200-Hz repetition rate), confirming our assumption that the output power would scale with slab count and aperture area.
Because the goal is to propagate the beam many hundreds of meters, a high degree of beam quality must be achieved. A beam with a divergence of less than two times the diffraction limit would be ideal. To examine this a bit further, consider the optical layout of our flashlamp-pumped Nd:glass laser (Figure 7).
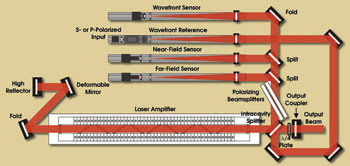
Figure 7. In the optical layout of the flashlamp-pumped solid-state heat-capacity laser, the cavity is a positive-branch, unstable resonator with a magnification of 1.5.
We have adopted the use of an unstable resonator coupled with an intracavity deformable mirror. As is illustrated in the figure, the intracavity beam is sampled by means of the beamsplitter and sent to the Shack-Hartmann wavefront sensor as well as to other diagnostics.
The wavefront sensor and the deformable mirror form a control loop by which the phase front of the beam can be adjusted. In the photo of the adaptive optic end of the laser, with the fold mirror, the deformable mirror and the cavity high reflector visible, the deformable mirror uses approximately 150 actuators with a maximum travel of ±4 μm. We can correct up to 16 waves of fourth-order aberrations. And because there is a large tilt component to the wavefront, all tip/tilt correction is off-loaded to the cavity high reflector. The motorized actuators used to control this mirror also are visible.
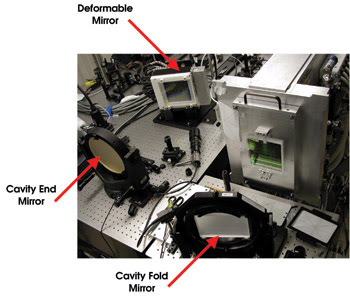
Figure 8. The adaptive-optics end of the laser cavity includes the end mirror, the deformable mirror and the fold mirror. The motorized actuators on the end mirror are used to control the tip/tilt component of the wavefront.
Experimental results
In some recent experiments, we were able to control the beam divergence during the course of a 40-shot, 10-s burst. The energy per pulse for this run is on the order of 400 J (Figures 9a and b). Because of the Brewster-angle orientation of the laser slabs, the wavefront tends to be astigmatic, with more divergence occurring in the horizontal direction than in the vertical. We have found that, averaged over the burst, approximately 65 percent of the beam energy lies within a 3×-diffraction-limited spot. It should be pointed out that, without the deformable mirror, the far-field spot after the fifth pulse becomes so large as to be unmeasurable.
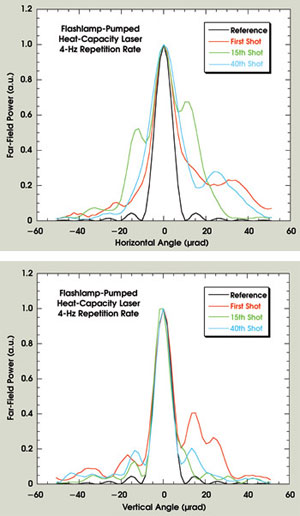
Figure 9. In the results from recent experiments, we can see the horizontal (a) and vertical (b) far-field intensity profiles for the first, 15th and 40th pulses. The reference curve is the profile for a uniformly filled flat-phase aperture.
As mentioned above, one major milestone in the heat-capacity laser program is the construction of a high-power laser system. We used our energetics model for a 10-kW-class laser system to explore the trade-off between aperture size and the number of slabs. In our calculations, we assumed an unstable resonator magnification of 2.0, a peak diode power of 100 W per bar and 550-J output at the beginning of the burst. Our baseline design will use a 13-cm aperture and a total of 10 slabs.
The operation of a solid-state laser in the heat-capacity mode is a novel approach to the development of systems that provide high power, that are compact and, most importantly, that are scalable. We have designed and constructed what we believe is the highest-average-power diode-pumped solid-state laser. This laser produced an initial output power of 10 kW for a 4-s burst and 30 kW for a 1-s burst.
We also have demonstrated that using an intracavity deformable mirror is a viable method for obtaining good beam quality from high-average-power lasers. Finally, by cooling the laser slabs remotely from the laser cavity, and by swapping the hot slab for a cooled one, it is possible to achieve a near-continuous mode of operation.
Acknowledgments
This document was prepared as an account of work sponsored by an agency of the US government. Neither the government, nor the University of California, nor any of their employees makes any warranty, express or implied, or assumes any legal liability or responsibility for the accuracy, completeness or usefulness of any information, apparatus, product or process disclosed, nor represents that its use would not infringe privately owned rights. Reference herein to any specific commercial product, process or service by trade name, trademark, manufacturer or otherwise does not necessarily constitute or imply its endorsement, recommendation or favoring by the US government or the University of California. The views and opinions of authors expressed herein do not necessarily state or reflect those of the US government or the University of California, and shall not be used for advertising or product endorsement purposes.
This work was performed under the auspices of the US Department of Energy by the University of California and Lawrence Livermore National Laboratory under Contract W-7405-Eng-48.
Reference
1. G. Albrecht, S. Sutton, V. George, W. Sooy and W. Krupke (1998). Solid state heat capacity disk laser. LASER AND PARTICLE BEAMS, 16, pp. 605-625.
Meet the authors
Mark D. Rotter is principal investigator for the Solid-State Heat-Capacity Laser Program at Lawrence Livermore National Laboratory in Livermore, Calif.; e-mail: [email protected].
C. Brent Dane was the project leader. He now works for Metal Improvement Co. Inc. in Paramus, N.J.
Scott Fochs is the project engineer at the laboratory.
Kai LaFortune is the lead person for the adaptive optics system.
Roy Merrill is the lead person for system controls.
Bob Yamamoto is the current project leader.