A layer of porous silica spin-coated over the widely used MgF2 antireflection coating produces a lower-reflectance coating over a considerably increased bandwidth.
James Stilburn, National Research Council of Canada
The technology used to apply antireflection coatings to glass is well-established. In its simplest form, the coating has one layer of material, usually a dielectric, with an optical thickness of λ/4, where the lowest amount of reflection at the surface is desired. The addition of a secondary spin-coated silica layer enhances these properties for specific applications.
Ideally, an antireflection coating should have a refractive index equal to the square root of the index of the glass substrate; for example, an index of 1.22 for glass with an index of 1.5. The most common material for a single-layer coating is MgF2, which has a relatively low index of about 1.38 at visible wavelengths. It is easy to apply by vacuum deposition and forms a hard, durable coating. Whereas typical uncoated glass reflects about 4 percent of the incident light at each surface, the MgF2 coating will reduce this to 1.3 percent (Figure 1). No other known material combines a lower index with the same degree of durability.

Figure 1. The transmission curves for single- and two-layer coatings illustrate the enhancement produced with sol-gel added to magnesium fluoride.
It has been known for the better part of a century that depositing porous silica will produce a coating with very low reflectance; however, problems with durability and water absorption have limited its usefulness. Recent research indicates that these problems are resolvable for certain applications. For example, if the density of the layer can be reduced to about 50 percent of solid silica, the refractive index can be made close to 1.22, yielding a near-zero reflectance at the wavelength of interest. Experiments of note have deposited silica sol (a suspension of small silica spheres) onto glass for use as an antireflection coating. A 1.5 percent stock solution of 100 g is produced using the following recipe:
ETHYL (anhydrous="" alchol="" denatured)
93.2 g
Tetraethyl orthosilicate (TEOS)
5.2 g
Ammonium hydroxide (30 to 37 percent)
1.6 g
The recipe can be varied to produce different concentrations, which will change the thickness of the deposited layer. To retard coagulation, the stock solution must be stored at –5 °C.
Formation of the silica suspension occurs in the ethanol solution from the following reaction, which requires about three days to reach completion at room temperature:
Si(OC2H5)4 + 2H2O m SiO2 + 4C2H5OH
The process produces spherical silica particles with a diameter of about 20 nm.
The coating can be applied with either a dip- or a spin-coating apparatus. Dip coating is the preferred method for large pieces, such as windows having an aperture of half a meter or more. This apparatus requires considerable effort to operate and the use of a cleanroom to produce good results. Spin coating is much simpler, particularly for circular optics with 8- to 12-in. diameters.
A spin-coating device is a large turntable on a vertical ball-bearing-mounted spindle driven by a DC motor and power supply, with a digital tachometer. The National Research Council of Canada designed and produced a device that can accommodate optics up to 22 in. in diameter and weighing up to 25 lb in an in-house machine shop (Figure 2). It also developed two others for smaller work.
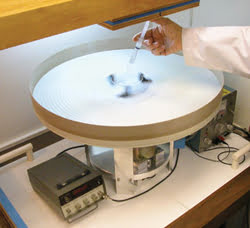
Figure 2. This spin coater is applying sol-gel solution to a glass disk.
Ethanol dilution
A working solution for use with the instrument is prepared by diluting a stock solution with ethanol. With a silica concentration of 0.8 percent, the reflectance minimum occurs at about 550 nm with a spin speed of 250 rpm. The optic is held in a chuck in the center of the spinning turntable, and the coating solution is applied with a filtered syringe to the center of the piece until the surface is saturated and the liquid is being flung from the edge. The liquid dries in less than a minute, leaving a coated surface.
The interplay of surface tension, centrifugal force and gravity produces a coating that is very uniform from center to edge (Figure 3). The largest disk that we have coated so far was 30 in. in diameter and showed excellent uniformity.
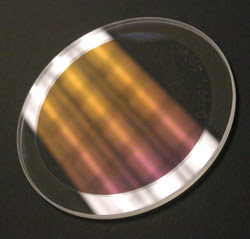
Figure 3. An overhead light shows the difference in reflection from a 4-in. glass disk coated with sol-gel and a 1/2-in. zone at the edge that has been left uncoated.
Newly deposited sol-gel on glass has little more durability than a layer of fine dust, so it is very susceptible to damage and cannot tolerate any wiping. Although the spheres can be lightly fused to each other and to the substrate by heating the optic to above 300 °C, this is risky and impractical for most optical glasses.
Another method exposes the surface to mild chemical attack, which will cause fusion at the points of contact among the spheres and substrate. This must be done with a gas or vapor, which will not sweep away the coating. Placing the coated optic in a small sealed container with an open beaker of 30 percent ammonium hydroxide for at least 20 hours will cause sufficient fusion to render the coating hard enough to withstand wiping with a dry tissue without damage. Hardening also slightly shrinks the coating so that the point of minimum reflectance is shifted toward the blue by about 15 percent.
Water absorption
Another issue is water absorption. The surface area of a λ/4 sol-gel coating is about 35 times the area of the substrate. If the coated optic is left in a humid environment, the silica will gradually absorb water, causing the refractive index to rise and degrading the performance of the antireflection coating.
Several hydrophobic agents can be applied to the coating on a spin coater to render it immune to the effects of humidity. One easily applied coating is a 5-ppm mixture of dichlorodimethylsilane (DDMS) in ethanol. A disadvantage of this is that the DDMS will wash away if the lens is cleaned with alcohol. Thus, the 5-ppm solution must be used for cleaning.
Another treatment, Flutec LE12 from F2 Chemicals Ltd. in Preston, UK, is effective, is easy to apply and does not wash away with organic solvents. A mixture of 1 g of LE12 and 40 g of FC-77 solvent from 3M Co. of St. Paul, Minn., is applied on a spin coater. All hydrophobic agents must be applied after the coating has hardened.
Some of the chemicals used in the above procedures are flammable and toxic. All Material Safety Data sheets should be read in advance, and the procedures should be done in a facility with basic safety equipment, such as an eyewash station, a fume hood, a fire extinguisher, and protective eyewear, gloves and clothing.
Enhanced coating
The sol-gel process described above produces an excellent single-layer antireflection coating. However, the low index of sol-gel can be exploited to even greater advantage when used with one or more other materials. Adding a λ/4 thickness of sol-gel can enhance the MgF2 coating, resulting in a considerable broadening of the transmission curve while sacrificing just a small amount of peak transmittance.
For the best result, the sol-gel should have a thickness of λ/4 close to the same wavelength as the MgF2 λ/4 thickness. Deviations of up to 100 nm in the visible region will not degrade the broad response. As with a single layer of MgF2 or sol-gel coating, these materials have indices below that of the glass, so the transmission cannot fall below that of the bare glass at any point. Theoretically, the single- and two-layer coatings can have even higher transmissions than those shown in Figure 1; however, variations in temperature, humidity and technique typically produce coatings with 0.3 percent less transmission than models predict.
Same techniques
The same hardening and waterproofing techniques apply to the added layer. Sol-gel does not adhere as well to MgF2 as it does to glass, a problem that is the focus of ongoing research. The addition of another thin layer on the MgF2, such as SiO2, prior to the sol-gel application would improve the adhesion greatly but would be less desirable than a simple chemical treatment. Without such an improvement, it is still possible to clean the coated surface by wiping with a cotton swab soaked in ethanol. Because the coating is porous and is not as adherent as vacuum-deposited coatings, it would not be suitable in applications where the surface is exposed to harsh weather or to less-than-gentle handling. This would include equipment such as eyeglasses and consumer optics, where frequent cleaning is often necessary.
The coating is sufficiently robust to be used on optics in the interior of assemblies, as in scientific apparatuses, laboratory equipment and even in vacuum optics. To date it has been applied as a permanent antireflection coating on the interior optics of many astronomical instruments in service at observatories in Hawaii, Arizona, Chile and Australia.
The deposition process is simple enough — and the outlay in equipment and effort small enough — that the enhanced coating can be used as a temporary high-performance antireflection coating in experimental optical bench work.
Meet the author
James Stilburn is a research officer specializing in optomechanical design and testing with Herzberg Institute of Astrophysics of the National Research Council of Canada in Victoria, British Columbia; e-mail: [email protected].