Peter Niedzielski, PerkinElmer Inc.
On a pharmaceutical production line, it’s not enough to inspect random samples of material. In response to stringent health and safety standards, such as those being proposed by the Food and Drug Administration, drug companies are seeking to examine every pill, blister pack and assembled package that comes down the line.
Machine vision enables managers to check that pills aren’t chipped or broken, that bottles and lids are properly sealed and that glass vials aren’t cracked. But the trend toward faster production speeds and on-the-fly line changeovers has placed higher demands on vision systems: The images must be clearer, and in many cases, color applications are required.
As a result, many drugmakers have turned to pulsed xenon illumination for their machine vision systems. Emitting from the UV to the infrared region of the spectrum that ranges from 200 to 1100 nm, these devices work by flashing 100,000-cd bursts of light. (By comparison, LEDs typically offer intensities measured only in the tens of candelas.)
Because they are so bright, xenon lights enable cameras to capture images in very short flashes — a pulse lasts only 1 to 20 μs — resulting in clearer, more detailed images and more complete inspection of each tablet or package. In a pharmaceutical plant with hundreds of thousands of pills rolling very rapidly down a production line, that can mean the difference between spotting a broken pill and letting it go by. Moreover, xenon lamps are less expensive, more compact, longer-lasting and less apt to generate heat than high-intensity continuous light sources.
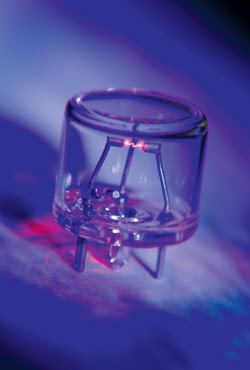
Pulsed xenon lights emit 100,000 cd of illumination in bursts lasting only 1 to 20 μs, making them ideal light sources in high-throughput pharmaceutical applications.
Their broad-spectrum light offers the advantage of more accurate color recognition — an important tool in some pharmaceutical applications, in which different kinds of pills must be identified on the same line. A xenon flashlamp provides a strong continuum of optical energy in the visible region that also is relatively flat in terms of spectral distribution. This is especially true when comparing xenon lights to tungsten-halogen and LED-based lighting systems. And additional color-balancing filters are generally not necessary with xenon-based lighting systems.
Indeed, many pharmaceutical companies are already using pulsed xenon lights, particularly for inspecting packages. The technology’s high intensity enables the use of higher magnification, so that human inspectors can search for hairline cracks in vials or for missing logo stamps on pills. Its broad spectrum allows users to filter the light for particular wavelengths to produce fluorescence in cap seals, allowing them to ensure that the seals have been properly applied.
Meet the author
Peter Niedzielski is a lighting applications engineer for PerkinElmer Inc. in Wellesley, Mass.