New standards could provide positioning and motion systems with higher dynamic path-following capabilities than existing and earlier systems. This may become critical for applications in precision metrology, manufacturing and others, where accuracy and repeatability are key.
As in real estate, in science and medicine, success often comes down to location, location, location. That’s why positioning technology is important. Getting an instrument — or a critical part of it — in the right spot and pointed in the right direction enables a spectrometer on Mars or a microscope on Earth to yield their best results.
Since all positioning technologies have strengths and weaknesses, there’s no single best way to get to every desired spot. But there are some principles that apply generally.
“Smaller and faster is usually better,” said Stefan Vorndran, vice president of marketing at Auburn, Mass.-based PI (Physik Instrumente) LP, a subsidiary of a German firm with the same name. Physik Instrumente supplies precision motion technologies and solutions around the world.
Vorndran continued, “In vacuum applications, size also matters. Smaller equipment can be used in smaller vacuum chambers, saving cost and pump downtime.”

A model of the positioning errors to consider when operating in the nanoscale. Photo courtesy of Alio Industries.
In addition to a push to become smaller and faster, positioning systems are being tasked to offer greater accuracy and repeatability. This leads to better instrument performance and is partly a result of the larger shift from a macro- or microscale world into one that is nanoscale. Where before positioning accuracy and repeatability to a few tens of microns was good enough, more and more often, the comparable figures must now be in nanometers.
A case in point can be seen in microscopes from Grayfield Optical Inc. of Las Vegas. A small company, Grayfield Optical offers microscopes that allow up to 50-nm resolution. Combined with a positioning system that offers better than 2.5-nm accuracy, the devices enable highly accurate size measurements over extended distances, as well as the ability to return precisely to a previously visited location. That positioning technology and the capabilities it offers can be important when examining a sample on a slide or when looking at a computer chip.
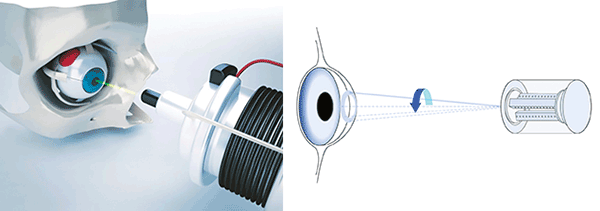
Precise positioning technology is used to steer lasers for eye surgery. Photo courtesy of Physik Instrumente.
“When viewing a computer chip wafer, there are thousands of structures that can be looked at. If, say, someone is looking at the structures for flaws, they can store the locations and then return to those locations to show the engineer what needs fixing,” said Peter Walker, president of Grayfield Optical.
Physik Instrumente’s technology is found in Curiosity, the Mars rover that has been examining the Red Planet for the last few years. Low-power ceramic actuators, validated to perform over 100 billion cycles, power a precision material-delivery system that moves samples in and out of chambers where x-ray diffraction and fluorescence spectrometry are used to analyze their composition. Aside from their reliability, there were other reasons why NASA selected the nanopositioning products, Vorndran said. “Other advantages of this technology are the nonmagnetic and vacuum-compatible nature.”
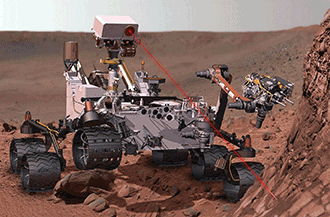
Precise positioning enables instruments on the Curiosity Mars rover to produce valuable science. Photo courtesy of NASA.
For analysis at a distance, Curiosity uses an instrument to perform laser-induced breakdown spectroscopy. In this technique, a laser pulse produces a flash of light from a sample that can be meters away. That light contains material-identifying spectral fingerprints. In the instrument carried by Curiosity, a Physik Instrumente high-precision stepper motor stage moves a telescope mirror to capture the telltale optical signal and to provide an image of the sample in context.
The positioning technology on Mars is also used in scientific and medical applications on Earth. For instance, the same piezo technology found in Curiosity is also used in ophthalmology, where piezo actuators steer mirrors so that laser beams end up in precisely the right spot. According to Physik Instrumente, the position resolution is in the nanoradian range, or less than 600 billionths of a degree. The technology is also fast, with response times of a few milliseconds or less.
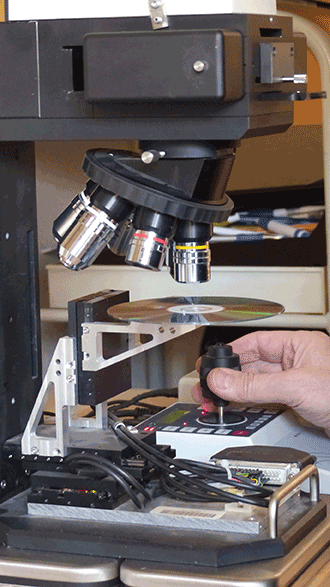
Precise positioning is needed when inspecting silicon wafers. Photo courtesy of Grayfield Optical.
The company offers a variety of different positioning technologies, with the list including piezo direct drives, piezo motors, stepper motors, servo motors, magnetic linear motors and voice coils, according to Vorndran. He said the reason for the diversity of products is that no one single technology fits all applications. It may even be necessary to switch from one to another as a customer’s product matures due to cost, performance, size or other characteristics of the original technology.

As for the future, the general push to make positioning and motion technology smaller will benefit medical instruments by enabling miniaturization. That, in turn, means diagnostics and surgeries can be less invasive, leading to faster recovery and better patient outcomes overall.
Miniaturization of position and motion methods could also benefit other areas. For instance, in silicon photonics, traditional electrical wiring interconnects are replaced by beams of light. The technique is seen as possibly necessary in tomorrow’s chips because it provides a way to move data for less power per bit than the traditional electron-based method. But production of silicon photonics systems places demands on positioning technology that may require innovative and nontraditional motion solutions.
“When a silicon photonics wafer prober requires several fast, multiaxis alignment systems to increase throughput, the wafer size and the density of the packaging limit the size of the mechanical positioning [and] alignment system that can be used,” Vorndran said.
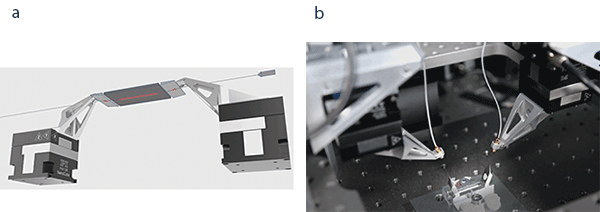
A high-speed X-Y-Z waveguide alignment system (principle, a, and test bed, b) for silicon photonics applications depends on piezo positioning technology. Photo courtesy of Physik Instrumente.
Besides getting smaller, positioning systems are also being forced to improve their precision and accuracy, with some of this effort dedicated to improved repeatability. In the future, as feature sizes shrink, repeatability and performance levels that were acceptable in the past may not be good enough.
As a result, positioning systems need to improve significantly, according to C. William Hennessey, founder and CEO of Alio Industries Inc. of Arvada, Colo. The company makes a range of products for nano- and what it calls ultraprecision positioning applications. The products offer orders of magnitude more precision than any other positioning systems, Hennessey said.
That level of performance is necessary to support improvements in instrumentation. For instance, sensors can currently measure points less than 5 µm in diameter with better than 100-nm precision. Those capabilities force certain requirements on the motion and positioning equipment.
“If a stage cannot travel in sufficient straightness and flatness over a surface, then the sensor is measuring the stage, not the surface,” Hennessey said.
In addition to a need to keep up with improved sensors, greater precision in positioning is also needed in manufacturing, he added. For example, laser cutting of sapphire is used in making smartphones. During such laser cutting, some legacy systems only have a limited repeatability when it comes to following a path; as a result, what should be a smooth circle may actually deviate from the ideal by a few tens of microns.
That difference is big enough for the human eye to see, according to Hennessey. For that reason, as well as the greater sensor sensitivity, positioning systems today may need to have bidirectional repeatability in the nanometers, not the tens of microns that were acceptable previously.
Alio’s specialty is positioning to less than 100-nm accuracy. The company achieves that with a proprietary design, as well as high-precision bearings and other high-quality mechanical components. Those are used in conjunction with a good motion controller and a capable encoder, a device that translates the actual position of a stage or other object into data that a motion controller can understand and, if necessary, use to take corrective action.
A key is that the total package is needed to achieve the desired results. It’s not enough, Hennessey said, only to use a high-resolution encoder with the belief that it will allow the motion controller to make up for all other shortcomings. If a stage, for instance, is not rigid enough or if the movement has some lag in its response, the result can be oscillation, with the system wandering back and forth, around and through the target position.
An important factor is that most positioning measurements and verification are done with reference to a point. In effect, the measurements are being done along one dimension only, with the results being just the distance to a reference point.
The actual repeatability figure is much larger, according to Hennessey and Alio documents, with errors in all three directions and another set of errors due to variations in flatness, straightness and roll. The result is that there are at least six sources of error in positioning repeatability and thus a need to use a six-dimensional reference system.
In addition to tackling this problem through its own products, Alio is also championing industry standards that address these issues.
“The new [National Institute of Standards and Technology] standard will be about point precision at any point within the working envelope, in all degrees of freedom,” Hennessey said of one such effort.
There’s no guarantee that the new standard will become a reality, and no timeline as to when it might happen. It could be years. When and if it does, though, the positioning and motion systems that adhere to it will have a much higher dynamic path-following capability than earlier systems. That, in turn, could be critical for precision metrology and manufacturing. One result for end users could be a metric for measuring position-system performance that is much easier to understand.
Of this, Hennessey said, “Anywhere that the motion system will move in this work envelope, it will have a point precision of ‘x’.”
If so, it may be time to amend the old adage. Instead of location, it’ll be all about “position, position, position.”