Old Material Has New Benefits for Photonics
Dr. David S. Stone and Manuel E. Joaquim
Polyphenyl ethers, a group of molecules with a long history of performance in
extreme conditions, are now being used as high-performance optical materials.
Polyphenyl ethers, or PPEs, are
a class of molecules new to optical applications, but with a long history of stability
and robustness in other fields.
These short-chain cyclic compounds are linked
by oxygen atoms. A characteristic formulation has two to eight aromatic groups,
or rings, allowing PPEs to retain their chemical and performance stability against
ionizing radiation, thermal excursions, chemical contamination and pressure changes.
Their optical clarity, high refractive index and ability to be formulated as fluids,
gels or solids have enabled them to meet rigorous performance demands of signal
processing in advanced photonic systems.
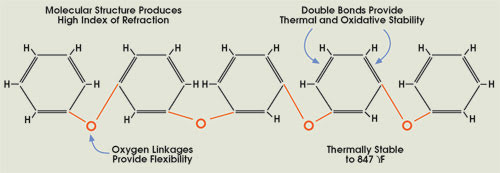
The unusual combination of optical and thermal properties
in polyphenyl ethers (PPE) is derived from their molecular structure, as demonstrated
by this five-ring PPE molecule.
The toughness of PPEs is a combination
of stability and flexibility, qualities that are related to molecular structure.
Resonance energy of the aromatic rings makes them resistant to high temperatures,
radiation and oxidation, while their oxygen linkages provide a local point of rotation
that allows the molecules to flex. The molecular structure also gives the material
a high index of refraction. A subgroup called thioethers, in which sulfur replaces
the oxygen linkages, has similar properties.
PPEs first found commercial application
as high-temperature lubricants and corrosion blockers in the engine turbines of
the SR-71 spy aircraft, where operating temperatures of 316 °C (600 °F)
would oxidize or decompose other hydrocarbon molecules. At the other extreme, they
can remain in liquid form in temperatures below 0 °C, where rigid molecules
would pack tightly and become a solid. Their consistent performance across wide
temperature ranges opened up such applications as lubricants on space satellites
and as fluids in vacuum-diffusion pumps — where they were selected for very
low vapor pressures, in the range of 4 x 10—10 t.
On the pins of electronic connectors,
where they are used as lubricants and corrosion blockers, their lifetime is between
40 and 50 years. Applied to gold, tin/lead and other electronic metals, PPEs virtually
eliminate metal wear and prevent fretting or galvanic corrosion by capturing or
blocking corrosive particles on the connector surface or in the atmosphere.
PPEs have unusually high surface tension,
in the range of 50 dynes per centimeter. The benefit is that they stay in position
when placed against a flat substrate, unlike conventional fluids such as long-chain
hydrocarbons or silicones. Also extraordinarily resistant to ionizing radiation,
they are used as lubricants in nuclear power plants.
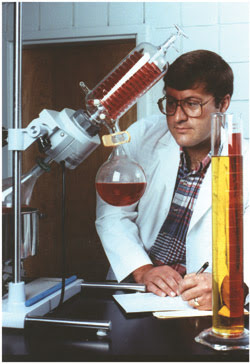
Fluid PPEs have a long history of application in unusual or extreme
situations and can be formulated as gels, coatings or resins.
Fluid PPEs are being used on a small
scale in commercial production as optical coupling media, and gels and coatings
are available for sampling and testing. Synthesis of PPEs for optical and nonoptical
applications is far from trivial, but experience from other fields is useful in
synthesizing optical-grade materials.
The optical clarity of PPEs resembles
that of other optical polymers: propagating wavelengths between approximately 400
and 1700 nm and tending toward opaqueness in the UV and mid-IR portions of the spectrum.
Optical polymers generally have refractive
indices between 1.3 and 1.7. Refractive index is important when matching materials
across whose boundaries light must propagate: The closer the match of the two materials’
indices, the less light is lost at their conjunction. PPEs have refractive indices
from 1.6 to 1.7, near and even above those of other optical polymers.
This makes them suitable for matching
high-index glasses such as LaBSF (refractive index 1.68), optical plastics such
as polyimide (1.66) and photonic semiconductors (2.0 and above). Also, PPEs are
the only fluid-phase optical polymers that combine high refractive indices with
overall robustness for thermal, oxidative and chemical stability; low vapor pressure;
compatibility with other polymers; and nontoxicity.
High refractive index
As the ambient temperature (T) changes, the refractive
index (n) of optical polymers also changes. The thermo-optic coefficient of refractive
index (dn/dT) for optical polymers is typically from 1 to 3 x 10—4 per degree Celsius,
and is roughly one to two orders of magnitude greater than the coefficient for most
optical glasses. Changes in index, both linear and reversible, are used beneficially
in devices such as optical switches, attenuators and filters to enable the processing
of optical signals.
Along with a high refractive index,
PPEs also have high thermo-optic coefficients, generally from 4 to 5 x 10—4 per
degree Celsius. This permits higher thermo-optic phase modulation over a given path
length and temperature range than would be possible with optical materials with
lower coefficients.
As formulated for nonoptical applications,
PPEs are a low-viscosity colorless or yellowish fluid. A five-ring PPE has a viscosity
of 360 centipoise (cP) at 100 °F; a four-ring PPE at that temperature has a
viscosity of 70 cP. Water, by comparison, has a viscosity of 1 cP, and light oils
are around 100 cP.
Fluid PPEs used in current optical
applications are contained mechanically within the optical device by seals or other
enclosures. However, emerging optical PPE gels, coatings and resins will appear
in a form that will not migrate from a device’s optical interface.
The thermal and oxidative stability
of PPEs is much higher than that of other optical polymers. As measured by an isoteniscope,
a five-ring PPE has a thermal stability of 453 °C, and a four-ring, 441 °C.
By comparison, most conventional hydrocarbon polymers begin to degrade in the 100
to 200 °C range. Silicone polymers are somewhat more stable, but they, too,
must be analyzed closely for stability behavior above
200 °C. The low-temperature service limit for these materials is the point
at which a sudden nonlinear change occurs in thermal expansion, analogous to a glass
transition. Various PPEs exhibit glass transition points in the range from 25 to
below —40 °C.
Manufacturability
Thermal stability is also a significant consideration
during manufacture, particularly when an optical polymer is briefly exposed to the
temperatures of solder reflow ovens or, less frequently, of wave soldering in optoelectronics
manufacturing. Temperatures in these environments are trending upward. For decades,
the solder used almost universally in electronics manufacturing has been an alloy
of tin and lead, with a melting point around 183 °C and requiring reflow temperatures
of around 225 °C.
In the past few years, however, environmental
concerns and marketing strategies have gradually phased out lead-based solder. This
movement began in Japan, spread to Europe and is only beginning to cause manufacturing
changes in the US.
A frequent replacement for lead is
a tin-silver-copper alloy with reflow temperatures up to 260 °C, roughly 35
°C above the temperatures required to reflow conventional tin-lead. As optical
components become more highly integrated through optical board-level assembly, their
internal optical polymer materials will be pushed to survive these higher surge
temperatures.
The stability of PPEs at temperatures
far above reflow heat means that they can be incorporated into devices that will
undergo soldering without significant concerns about evaporation, oxidation or decomposition.
Yellowing is the most common symptom of failure for conventional polymers under
these conditions.
As with other polymer chemistries,
one can select PPE formulations that are the most favorable mechanically for a given
application. The fluid, gel and solid versions permit control of the tensile modulus
over a wide range, from a pure fluid (zero modulus) to a hard coating (high modulus).
This allows the selection of a consistency that minimizes stress buildup in an assembly
— a key parameter for ensuring thermal and mechanical reliability of a design.
Optical applications
The volumetric coefficient of thermal expansion
of PPEs is in line with that of other optical polymers, which range from 20 ppm/°C
for hard plastics up to 1000 ppm/°C for the softer gels and fluids. These considerations
help avoid mismatch of coefficients at material interfaces, where thermal changes
can create mechanical stress. Selection of a particular formulation may provide
the solution for a specific design problem — for example, using a PPE in gel
form to reduce mechanical stress at an interface while maintaining optical properties.
Their extreme resistance to ionizing
radiation gives PPEs an advantage in the manufacture of solar cells and solid-state
UV/blue emitters. Solar cells are exposed to the full range of the solar spectrum,
including the UV. Incorporating a coating or layer of PPE can permit index matching
to the cell and thereby increase the cell’s photoconversion efficiency.
Outdoor flat panel displays, like solar
cells, are subjected to direct sunlight. A layer of PPE between the display emitter
array and the high-index cover glass can improve image contrast in ambient light
because they have higher indices of refraction than silicones and hydrocarbons.
Also, their superior UV-hardness renders them less susceptible to delamination and
yellowing with age.
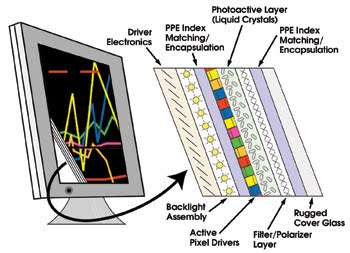
Index-matching capabilities
make PPEs useful in high-performance backlit flat panel color displays.
Projection display systems for next-generation
digital theater are a rough environment for hydrocarbon, fluorocarbon and silicone
lens coatings. Before the high-intensity light beam projects onto a screen, it travels
through a sequence of image manipulation optics. The light flux includes the shortest
wavelengths in the visible spectrum and can even be marginally ionizing. The intense
radiation flux at longer visible wavelengths heats even high-quality glass lenses
and prisms to elevated temperatures. A fluid PPE used as a lens face coolant can
transfer more heat and do it more quietly than forced-air cooling. It can also keep
dust particles out of the image field and improve the optical efficiency between
elements.
The exotic high-index glasses or semiconductors
from which many optical signal processing components are fabricated for telecommunications
require media with high indices of refraction for index matching of adjoining materials.
PPE coatings in fluids, gels or in hard resin form are useful — particularly
resin coatings, which provide the advantage of serving as radiation-hardened antireflection
coatings at air interfaces.
Meet the authors
David S. Stone and Manuel E. Joaquim are the
founders and principals of SantoLight JV, a unit of Findett Corp. in St. Charles,
Mo.