Sean Bergman, Coherent Inc.
A new type of laser-power detector delivers fast speed and high laser-damage resistance, enabling real-time process control in embedded systems.
Lasers process a wide range of materials in an extraordinarily diverse array of applications that often share a common requirement: the need to regularly measure laser output characteristics such as average power, pulse energy, pulse shape or beam profile to ensure optimum and consistent processing. Furthermore, in several industries, the need for improved process precision and ever-higher yields is making laser characterization even more critical.
Measurement requirements
For most laser processes, no matter what the operating regime – CW (continuous wave), millisecond, nanosecond or femtosecond – or output wavelength, average power is a critical parameter, as it usually directly affects material removal or transformation rates and, therefore, process throughput. Frequently, the average laser power actually delivered to the work surface is subject to fluctuations, because it can be impacted by a number of different factors. These include inherent variations in laser output, as well as changes in optical alignment within a beam delivery system and degradation in the performance of individual beam delivery optics (such as a drop in reflectivity on a mirror).
Pulse shape is also an important parameter, particularly for applications in the thermal-processing regime that commonly utilize modulated CO2 lasers. Real-time pulse-shape monitoring (which can be used to monitor peak power and calculate pulse energy) can provide a feedback loop to the laser, which translates into improved process speed and feature uniformity.
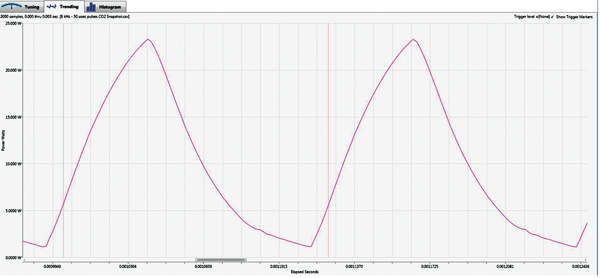
Pulse-shape visualization of 50-µs-long pulses (at 8 kHz) obtained in snapshot mode with a PowerMax-Pro sensor, along with LabMax-Pro electronics and software.
A general move in industry toward higher process precision or increased throughput typically narrows the process window, making it more intolerant of any changes in either delivered laser power or pulse shape. The narrower this window gets, the more frequent the need to measure laser output characteristics to verify that it remains within acceptable bounds.
The frequency of laser measurement also strongly impacts cost because it enables quicker identification of production problems. Specifically, it can find nascent problems or problems that have just occurred and therefore prevent the fabrication of poor-quality parts before they move down the line and become expensive scrap or rework.
If frequent laser-power monitoring is so useful, why are measurements made so infrequently in many industries? The answer is that the power-measurement technology currently available for many laser types is relatively slow and therefore can’t keep pace with the speed of the production line. As a result, laser power is measured only intermittently to minimize stopping or slowing of production. Similarly, real-time pulse-shape monitoring is rarely used, especially for CO2 lasers, due to practical limitations of infrared photodiodes.
Traditional laser-power sensors
Two dominant technologies are in use for measuring the average power of lasers: thermopiles and semiconductor photodiodes.
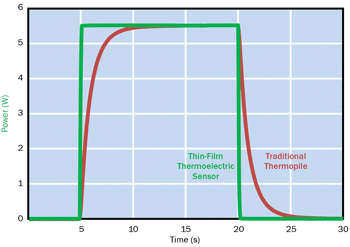
The rise time of a typical mid-power thermopile (30 W) compared with that of a thin-film thermoelectric sensor.
Thermopiles have been used for many years as the detector of choice for high-power lasers. These detectors operate on the thermoelectric principle, in which thermal energy is converted into electrical energy. The typical thermopile consists of a central, light-absorbing disk, a series of thermocouples that surround this disk, and an annular heat sink around the ring of thermocouples.
In operation, incident laser energy falls on the absorbing disk in the center of the detector and is converted into heat. This disk typically is coated with a material that absorbs light over a very broad wavelength range to enhance sensitivity. The heat then flows across the width of the thermopile disk to the heat sink, which is held at a near-constant ambient temperature by either air or water cooling. The temperature difference between the absorber and heat sink is converted into an electrical signal by the thermocouples. Calibrated electronics in the meter convert this electrical signal into a laser-power reading.
Thermopile sensors have several advantages, including an extremely broad spectral range, an ability to work over a wide range of input powers, high laser-damage resistance and uniform spatial response (meaning, insensitivity to changes in beam size, position or uniformity). The limitation of the technology is that the transfer of heat across the width of the thermopile disk makes this technology inherently slow. Specifically, it often takes several seconds before the heat flow induced by the laser reaches equilibrium and the power measurement becomes steady on the display. Physically larger sensors take longer to reach this steady state.
A semiconductor photodiode sensor is essentially a solid-state diode (p-n junction). Incident laser photons are absorbed by the device and converted into charge carriers (electrons and holes). These can be sensed as current or voltage, depending on how the junction is biased. Photodiodes offer high sensitivity, enabling them to detect very low light levels. And several different semiconductor material combinations are available to produce photodiodes that work in the visible, NIR or far-IR. Photodiodes also have a fast response time and thus can be useful for looking at pulse shapes. However, they saturate above approximately 1 mW/cm2, so attenuating filters must be used when operating at higher powers.
The main drawbacks of photodiodes are that they have smaller active areas, a much more limited spectral range and lower spatial uniformity than thermal sensors. The latter can affect the measurement repeatability of non-uniform beams or of beams that wander over the detector surface between measurements. These characteristics make photodiodes most useful for low-power measurements of CW lasers and for pulse-shape characterization of nanosecond pulsed lasers.
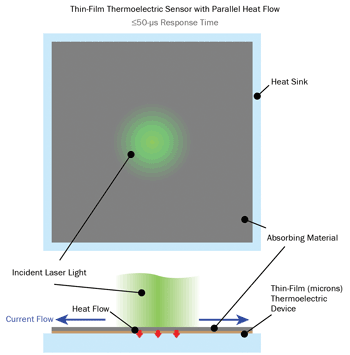
Basic configuration of a PowerMax-Pro sensor: The short heat flow path results in fast measurement speeds.
Thin-film thermoelectric technology
The ideal sensor for embedded power measurement would combine the broad wavelength sensitivity, large dynamic range and high damage resistance of a thermopile with the fast response of a semiconductor photodiode. A new, patent-pending sensor architecture that meets these requirements is based on thermoelectric technology but is constructed and configured very differently than traditional sensors. Specifically, in this device, the heat flows vertically through the detector, and the electrical signal that is generated moves perpendicularly to the heat flow.
The thermoelectric generating materials used in this sensor are a stack of films with layer thicknesses on the order of microns, rather than traditional thermocouples. Incident laser light is absorbed and generates heat, which flows very quickly through these thin layers to the heat sink below the detector, where it is dissipated. The electrical signal from the thin-film layers moves laterally to the edges of the device, where it can be measured by tapping into the sensor electrodes.
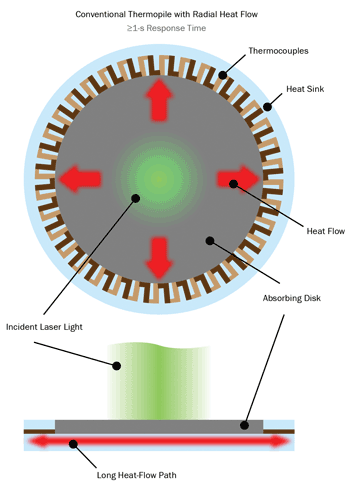
Construction of a traditional radial thermopile leads to slow measurement speeds.
In contrast to the traditional, radial-flow thermopile, which has a sensing time constant value of several seconds, the time constant for the thin-film configuration is in the microsecond range, which enables the sensor to provide an essentially instant power measurement without any overshoot.
The PowerMax-Pro from Coherent is based on this technology but also preserves the main benefits of the traditional thermopile architecture: large active area (30 x 30 mm), wide dynamic range (50 mW to 150 W), high damage resistance (14 kW/cm2) and broad wavelength range (300 nm to 11 µm).
The response speed of thin-film thermoelectric sensors allows users to move beyond just measuring average power, and enables visualization of the temporal pulse shape and peak power of modulated lasers with pulse lengths greater than 10 µs, which can be used to develop better process recipes. These pulses can also be integrated to calculate individual pulse energy for use in active feedback control.
Signal processing
A sensor is just part of a measurement system and can only deliver high-quality data if it is matched with electronics to properly acquire, condition and process the raw signal from the sensor. New processing electronics and software fully capitalize on the inherent capabilities of thin-film thermoelectric detectors. Specifically, an interface module processes the raw signal from the detector; this module connects with a host computer through USB 2.0 or directly to laser-system controllers via RS-232. A new Windows PC application then enables instrument control and displays measurement results, including laser tuning and pulse-shape visualization, on a host computer. The software also performs a wide range of analysis functions such as live statistics, histograms, trending and data logging. A complete set of host commands can be sent through either the USB or RS-232 interface, which is particularly useful for embedded applications.
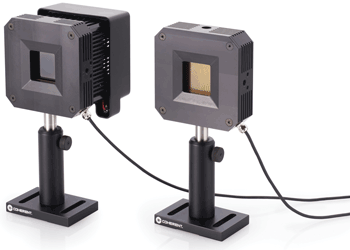
Thin-film thermoelectric sensors are available with a broadband
coating, which operates from 300 nm to 11 µm, and a higher damage
threshold (up to 14 kW/cm2) coating, which covers both 355 to 1100 nm and 9 to 11 µm.
The software is configured to work at three different data sampling rates. A 10-Hz sampling rate is used to provide essentially instantaneous power readings, much as with a photodiode. This operating mode is best used to measure the power of CW lasers or the average power of submicrosecond-pulse-length lasers.
The two other, high-speed sampling modes fully exploit the rapid response speed of these sensors to enable advanced analysis of high-power modulated lasers in a way that has never before been possible. The first high-speed mode uses a continuous data sampling rate of 20 kHz, allowing pulse-shape analysis of modulated lasers with repetition rates of up to 2 kHz. These types of pulse trains are common in many laser-based medical treatments and in some materials-processing applications, such as microwelding.
The second high-speed mode is snapshot mode, which provides burst sampling at a rate of 625 kHz for a period of time up to 384 ms. This mode provides excellent pulse-shape fidelity for pulses greater than 10 µs in duration at repetition rates up to 50 kHz, common in various commercial cutting, engraving and drilling applications.
This type of temporal visualization offers new insight into the true performance of the laser, which was previously masked by slow thermopiles. This information now available to engineers removes some of the “magic” involved in developing recipes for materials-processing applications. It provides developers with more repeatable methods to transfer processes from engineering to manufacturing, and to control and monitor processes once they are up and running. Many thermal-based materials-processing applications can be better controlled with this information, leading to cutting, drilling and engraving with increased speed and higher yield. At the same time, the quality of laser-produced features can be enhanced.
Meet the author
Sean Bergman is product line manager for laser measurement instrumentation at Coherent Inc., and is responsible for market development of the company’s range of laser power and energy meters; email: [email protected].