ERIC CAREY, TELEDYNE DALSA
When the GigE Vision camera-interface standard debuted on the market in 2006, it heralded a new level of simpler and more cost-effective connectivity for machine vision users. Unlike the analog cameras or the Camera Link interface standard that were commonplace pre-GigE, the frame grabber-less GigE Vision offered an accessible interface to GigE ports, cut system costs by eliminating the frame grabber and delivered a transfer rate of 1 Gb/s. Even the earliest frame grabber-less interface standard, FireWire, which offered a throughput of 400 Mb/s (for IEEE1394a) or 800 Mb/s (for IEEE1394b) and, according to a 2013 AIA study, was used on about 25 percent of the machine vision cameras sold, couldn’t keep pace.
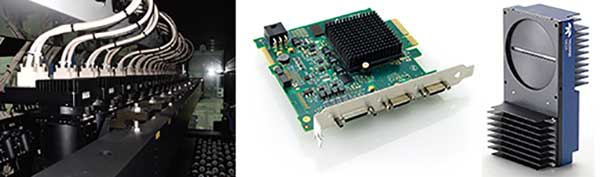
Frame grabbers (middle) and line-scan cameras (right) can be used for many inspection applications in manufacturing. One customer uses the equipment to inspect flat panels used in high-end flat-screen television sets to ensure that all pixels on the panel are fully functional and there are no defective spots in the image (left). Photo courtesy of Teledyne Dalsa.
Today, new machine vision applications and the advent of faster interface standards, including Camera Link HS, CoaXPress and USB3 Vision that allow cameras to transmit pixel information at a rate greater than GigE, are changing the landscape
once again. Yet for many in the machine vision industry, the challenge is discovering how to retain GigE Vision’s
considerable benefits while realizing a higher throughput.
The advantages of GigE Vision take root
Before GigE Vision there was FireWire, an Apple offering that was the first to enable connectivity between a camera and PC without a frame grabber. Eliminating the need for a frame grabber meant that systems using a FireWire interface cost less to deploy — an advantage for users who were willing to accept FireWire’s slower 400 Mb/s performance in exchange for cost savings. In fact, FireWire dominated the frame grabber-less machine vision market for many years with no real competition until May 2006 and the advent of GigE Vision.
With GigE ports common on the motherboards of most PCs, GigE Vision offered the ease of use and lower system cost of FireWire combined with greater bandwidth — speeds of 1 Gb/s — and the ability to transmit images over very long distances using standard Ethernet cables. Since GigE has its roots in networking technology, it works efficiently with cable lengths up to 100 meters; FireWire’s cable length is limited to five meters, and depending on the size and scope of a machine vision system, cable length may be a critical consideration in determining which interface to use.
Still, initial adoption of this for use in machine vision applications was relatively slow, and it took three years for GigE to achieve 14 percent market share in terms of machine vision units sold, according to the AIA study.
In 2009, however, the market for GigE Vision began to expand more rapidly. By this time, GigE had gained greater visibility, proved its robustness, and users recognized that they could achieve the level of performance required for their machine vision applications with a less expensive interface. It’s also possible that acceptance of GigE was spurred in part by the global economic downturn of 2008-2009, which increased the appeal of more cost-effective, frame grabber-less interfaces.
In 2016, GigE remains the leading interface among both manufacturers and users, with some market studies demonstrating market share better than 50 percent. To meet customer demand for high-speed, low-cost cameras, Teledyne Dalsa expanded its Linea family of GigE Vision line-scan cameras and unveiled the Genie Nano GigE Vision area scan camera in 2015. Linea cameras are commonly used in food, web, rail, road and pharmaceutical inspections, while the Genie Nano is seen in industrial inspection, intelligent traffic systems, as well as in entertainment, medical, and food and beverage inspections.
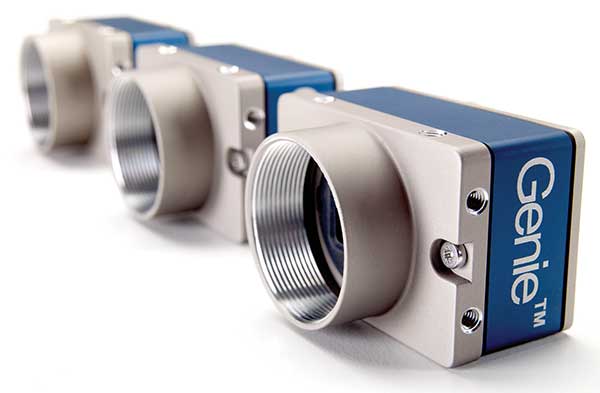
GigE Vision line-scan cameras are used in many industrial inspection applications. Photo courtesy of Teledyne Dalsa.
But don’t count the frame grabber out
A discussion about the advantages of frame grabber-less systems might lead a reader to conclude that the frame grabber no longer has a place in machine vision systems, but nothing is further from the truth. Today’s frame grabbers are engineered to meet the ever-increasing image resolution and faster frame rates common with new, high-speed, high-bandwidth cameras, particularly in systems designed in industries such as color print inspection and flat-panel inspection. For example, a Teledyne Dalsa customer uses the company’s Xtium frame grabbers with Piranha line-scan cameras to inspect the flat panels used in high-end flat-screen television sets to ensure that all pixels on the panel are fully functional and there are no defective spots in the image. Inspections are completed at very high speeds and at the micrometer level, so high resolution and performance are mandatory. Given that the panels are a high-ticket item to produce and purchase, the manufacturer is committed to investing in top-of-the-line inspection equipment to maximize throughput on its fabrication line.
Pushing past GigE Vision to new horizons
Even in the frame grabber-less space, demand is increasing for higher resolution and speed, and technology does exist that allows cameras to transmit pixel information at a rate that exceeds the 1 Gb/s available with GigE. For example, Teledyne Dalsa’s Linea and Genie Nano line- and area-scan cameras now incorporate the company’s TurboDrive data encoding technology. This technology enables GigE Vision systems to push past current bandwidth limitations and increase image throughput by as much as 150 percent while accurately transmitting all image data. TurboDrive delivers GigE’s longer cable lengths and lower price point, and ensures compatibility with existing equipment.
Introduced in 2013, USB3 Vision takes advantage of the ubiquitous USB interface. Like GigE Vision, USB3 does not require a frame grabber. However, USB3 delivers transmission speeds that are significantly higher, up to 5 Gb/s. Also unlike GigE Vision, USB3 relies on cable lengths of two meters or less with “passive” cables using USB3’s micro-B connector. Machine vision cable companies are working to push past this limitation with “active” cables that boost the signal and enable transmissions over lengths as great as 20 meters.
Those in the industry are watching the rate of market acceptance for USB3 Vision to see if it follows an adoption trend similar to that of GigE Vision. They’ll also pay close attention to which interface may be displaced by USB3 if market share increases considerably. While a battle between GigE and USB3 may be brewing, it is also possible that USB3 will pose the greatest threat to Camera Link. One of the earliest standards, Camera Link still plays a vital role in many systems designed to use frame grabbers, but offers a maximum bandwidth of 255 Mb/s in its single cable configuration. By transitioning to USB3 Vision, users could benefit from higher bandwidth and lower systems costs.
Alternatively, users looking for extremely high bandwidth could move to Camera Link HS, a standard released in 2012, which offers greater cable lengths and increased bandwidth when compared to traditional Camera Link — and virtually every other interface standard. Camera Link HS uses “off the shelf” components to create an exceptionally fast camera interface. Included in these components is a nonproprietary FPGA chip that implements the logic of the camera and serves as the interface to the cable. Camera Link HS relies on a frame grabber and supports bandwidth of up to 22 Gb/s over a single cable.
Like Camera Link HS, CoaXPress, which was introduced in late 2010, requires a frame grabber and is designed for those applications that require higher transmission rates than those found in frame grabber-less interfaces, commonly in the inspection of products where speed is more important than cost. One key difference between Camera Link HS and CoaXPress is that CoaXPress relies on specialized chip technology. Depending on the diameter and length of the coaxial cable used, CoaXPress can transmit data from the camera to the frame grabber at up to 6.25 Gb/s over a single coaxial cable. Multiple coax cables can be bundled to increase that rate, typically in a four-cable configuration leading to 25 Gb/s.
CoaXPress uses the coaxial cable typical in many buildings — the same basic cable used by analog cameras — which provides some migration path for analog camera systems; a user can replace just the analog camera and frame grabber and gain CoaXPress transmission rates.
Two additional Ethernet interface standards, which are used by a very small segment of the market, are 10GigE and NBASE-T and could be used as a physical interface by GigE Vision. 10GigE might have been a natural evolution from GigE but was hampered by an expensive chip set, higher power consumption and the need for unique, higher-quality Ethernet cables. The number of cameras that use the 10GigE interface is extremely limited and the standard’s market share is very low with little likelihood of growth in the near future.
The standard for NBASE-T, also an Ethernet technology, has just been released and chip sets are reaching the market. It is too soon to predict whether NBASE-T will be adopted in machine vision, but transmission rates of up to 5 Gb/s over cable used by GigE Vision today hold promise. If NBASE-T becomes mainstream, expect manufacturers to bring new machine vision cameras to market within the next two years. This could serve as a transition step to 10GigE.
Like NBASE-T, USB3.1 offers a faster transmission rate than current generations of camera interfaces; in the case of USB3.1, the speed is 10 Gb/s, although this is over short cable lengths. USB3.1 incorporates a reversible “type C” connector, which may help to drive USB3.1 adoption, particularly for transmissions between smartphones, tablets and PCs. It is too early to predict the impact of USB3.1 on machine vision, but it holds great potential.
System design remains a king
As the machine vision industry recognizes that its customers want to exceed current bandwidth limitations — without affecting the integrity of their image data — there will be a move to push beyond the boundaries of established camera interface standards. New technologies will continue to help customers respond to the ever-present need for their inspection systems to become faster and more efficient, yet system design and machine vision requirements remain the most important factors in determining every component used — including the camera interface. Choosing the camera and frame grabber, if needed, that are best-suited to the application and considering existing cabling or required cable lengths to align with the system design should take place before specific discussions about which interface standard makes the most sense. Understanding the system and application will help determine whether the resolution required for detailed inspection and high yield is more important than transmission rates, or if the need to slash system costs trumps the desire for the fastest possible speed.
Meet the author
Eric Carey is director of Area Camera and Frame Grabber Technology at Teledyne Dalsa in Montreal. You can reach him at [email protected].