The development of a reliable, high-power source of mid-IR laser light gives process developers an important tool with unique characteristics that will significantly impact a diverse range of applications.
Andrew Held, Coherent Inc.
The first carbon monoxide (CO) lasers were built more than 50 years ago. The technology showed promise for several reasons. First, CO lasers are inherently efficient in terms of their conversion of input electrical energy into light. For example, they are potentially about twice as efficient as the more commonly used carbon dioxide (CO2) lasers. Also, CO lasers output in the 5- to 6-µm spectral range, whereas CO2 lasers typically lase at 10.6 µm. This shorter wavelength provides processing benefits in many applications.
Given these advantages, why have CO lasers remained largely a laboratory curiosity until now, while CO2 lasers, developed around the same time, have found widespread use in a diverse range of industrial processing applications? The answer is that CO laser technology could not be made practical, reliable and cost-effective enough for commercial use. In particular, early CO lasers required cooling in order to reach high output power (cryogenic cooling for very high powers). Also, while the first sealed CO2 lasers could operate at high powers for hundreds of hours, early sealed CO laser lifetimes measured in just hours before output power dropped substantially.
This situation has now changed dramatically with the development of new CO laser technology that addresses these practical limitations. This has enabled the production of sealed CO lasers that operate at very high output powers with excellent efficiency at room temperature and which demonstrate lifetimes in the thousands of hours range. This article reviews the technology behind the new generation of CO lasers and examines how their unique output characteristics lead to significant benefits in some important commercial applications.
CO laser development
In order to appreciate the inherent difficulties associated with developing and manufacturing a gas discharge laser like the CO laser, it is useful to examine the challenges met with the more familiar CO2 lasers. The dynamics involved within fully sealed gas discharge lasers are complex, to say the least. Critical chemical dynamic control involves the gas chemistry within and outside the laser discharge volume (including laser on and off), the chemistry between the gas and resonator materials (metals and ceramics), the chemistry between the many different materials used to construct the laser, and the chemistry involved with potential contaminants. Cleaning is critical within the sealed resonator tube.
Over the years, Coherent has learned how to control the chemical dynamics in fully sealed CO2 lasers, enabling higher performance and improved reliability. Today’s CO2 lasers offer higher average powers and peak powers, as well as better power and pulse stability than ever before. At the same time, the reliability of these lasers has increased fivefold over the last 10 years. This can be attributed in large part to the ability to control the complex chemistry involved in CO2 lasers: improved engineering design and development, as well as manufacturing process optimization, such as supplier development (coatings, electronics, etc.). The design improvements and critical manufacturing process optimizations for CO2 lasers, developed over many years, are now being applied to the new CO lasers.
Gas dynamics in a CO2 laser are a carefully controlled symphony of chemical activity. In CO2 lasers, nitrogen gas is vibrationally excited via electron impact in a radio frequency (RF)-generated plasma discharge volume. The nitrogen then transfers its vibrational energy to the CO2 molecules, which can now emit photons (9.6 or 10.6 µm) as they drop to lower energy vibrational states. From these lower vibrational energy states, the CO2 molecules transition ultimately to the lowest energy state through collisions with helium, that is, through vibrational-translational (V-T) energy transfer. From this lowest energy state, they can then be re-excited.
In addition to the “lasing” gas dynamics, there is also the chemical decomposition and recombination of CO2, which is carefully controlled by trace elements in the gas mix. Pressure and resonator geometry optimization also plays a critical role in controlling the gas dynamic and chemistry. Further, contaminants missed through the cleaning process or created in the chemical pool can disrupt the gas dynamic chemical balance and adversely affect the lasers’ performance.
The chemical dynamics of the CO laser are different but equally complex. Vibrational excitation of CO molecules takes place directly via electron impact from the same RF sources used to create the discharge plasma in a CO2 laser. However, CO lasers don’t necessarily need nitrogen. Once vibrationally excited, CO molecules can further excite other such molecules through vibrational-vibrational (V-V) transfer.
Laser emission comes from successive transitions between pairs of populated vibrational levels in the diatomic energy-level ladder. Each transition to a lower energy level then becomes the upper state for a subsequent transition — this is the definition of a cascade laser. As with the CO2 laser, there are many different processes competing with effective lasing that need to be accounted for. Where the helium V-T cooling is critical for CO2 lasers, in CO lasers this can actually compete with the efficiency of the V-V CO pumping process. This is partly why early CO lasers were often cryogenically cooled. Room temperature operation was not practical, until now.
Figure 1. In a CO2 laser, energy transfer from N2 raises the CO2 molecules into an excited state, which then decays into one of several possible lower states by emitting a photon. Nonradiative losses cause the molecule to return to the ground state. In a CO laser, several pumping mechanisms can raise the energy of the molecule to various excited states. It then cascades back down to the ground state, emitting several photons along the way.
Mid-IR wavelength advantages
Much of the interest in CO lasers derives from the fact that its midwavelength-IR output offers two important advantages, in terms of applications, as compared to the long-wavelength IR output of the CO2 laser. The first of these is the fact that many materials exhibit significantly different absorption at the shorter wavelength, leading to disparities in their processing characteristics that can be exploited. Specifically, in cases where the absorption is higher at the shorter wavelength, material can be processed more efficiently using lower laser power and with a smaller heat affected zone (HAZ). This stronger absorption occurs in many metals, films, polymers, PCB dielectrics, ceramics and composites. On the other hand, when the transmission is higher at the shorter wavelength, the light penetrates farther into the material, which is also sometimes advantageous.
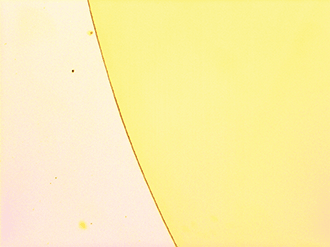
Figure 2. A CO laser with only 9 W of output power produced a clean, curved cut (6-mm radius circle) in thin glass (50-µm thick).
The other major difference is that shorter wavelengths can be focused to smaller spot sizes than longer wavelengths due to diffraction, which scales linearly with wavelength. The final spot size depends on working distance and the numerical aperture of the focusing lens. The theoretical, diffraction-limited spot size for 10.6-µm CO2 lasers is about 55 µm, while the minimum spot size achieved in practice in industrial applications is 80 to 90 µm. The 5-µm CO laser can reach theoretical spot sizes of about 25 µm under the similar focusing conditions, with practical spot sizes in the 30 to 40 µm range. As a result, the CO laser spot can have a power density (fluence) that is four times higher than the CO2 laser. The higher power density, when combined with stronger absorption in some materials at 5 µm, enables these materials to be processed with a CO laser at significantly lower powers.
Diffraction also dictates that a shorter wavelength spreads more slowly over distance, leading to improved depth of focus. Specifically, depth of field — the distance over which the beam size increases by a factor of √2 — is related to laser wavelength (λ) and input beam diameter (D) by:

Thus, for a given input beam diameter, depth of focus increases as wavelength decreases. The benefits of a longer depth of focus include higher aspect ratio processing and an increased process window, especially for materials with uneven surfaces and/or variations in thickness.
Glass cutting
CO2 lasers are already employed in cutting thin (< 1-mm-thick) glass sheets, namely the specialty glass (strengthened and nonstrengthened) used in many smartphone and tablet displays. The 10.6-µm output of the CO2 laser is strongly absorbed by glass, whereas absorption around 5 µm is much lower. But this actually leads to significant potential advantages in this application.
In CO2 laser-based glass cutting, the light is absorbed strongly at the surface, generating heat that must then diffuse into the bulk material. After laser exposure, a jet of water or air is used to thermally shock the material and create a precisely controlled scribe or vent. Mechanical means are then employed to actually break the glass along the laser-scribed line.
Figure 3. A 50-µm-thick glass substrate drilled with successively more pulses from a CO laser demonstrates the ability of this source to drill glass interposers, as well as drill micro dots on light guide panels used in display backlights. CO2 drilling of this material typically results in heat-related cracking.
The overall process is much the same with the CO laser; however, the lower absorption allows the light to penetrate much further into the bulk material. Heat is introduced to the glass directly and does not rely on diffusion from surface. Coherent has performed tests indicating that this eliminates surface melting, avoids the creation of cracks and produces no residual stress in the glass. The results are a better quality scribe yielding a stronger cut piece, together with a wider process window, for the manufacturer.
The other exciting aspect of CO lasers in glass cutting is their ability to support the cutting of curves. This is of particular significance in smartphone display applications, as curved or shaped corners are often required to accommodate buttons, controls, LEDs and camera lenses. CO2 lasers are typically limited to cutting glass in straight lines because their round output beam must be reshaped into a long, thin line in order to distribute the intense heat generated at the surface. In contrast, the lower absorption of the CO laser allows its round beam to be used directly without adverse heat effects.
The CO laser also enables processing of very thin glass (below 300-µm thick). This material is almost impossible to cut mechanically and is also challenging to process using the CO2 laser. In this case, the CO laser can cut completely through the glass, eliminating the need for a subsequent mechanical breaking step, which is particularly difficult to accomplish with very thin glass.
Figure 4. Polyethylene cutting speed of CO lasers of various output power levels as compared with a CO2 laser. A 20-W CO laser cuts at about the same speed as a 150-W CO2 laser.
Drilling glass holes
Another important glass processing application is drilling for glass interposers used in 2.5D and 3D advanced circuit packaging techniques. This application takes advantage of both the superior focusability and lower absorption of 5-µm light in glass. Specifically, it enables very small holes to be drilled in glass with precise depth control and no heat damage or cracking.
Film cutting
Polyethylene (PE) has strong absorption at 3.5 µm, with mild transitions at 7 µm and ~14 µm. Unfortunately, no high-power lasers are available at any of these wavelengths, so laser cutting of PE has not been practical in the past.

Figure 5. Top view of the edge of a 20-µm-thick polyethylene sheet (at left), cut using a 164-W CO laser at a feedrate of 3000 mm/s. The laser produced a clean cut edge, with a heat affected zone of about 29 µm.
While low-level absorption can always be driven with high powers at CO2 laser wavelengths, the residual heat generated by the unabsorbed light creates unacceptable collateral damage. But the higher focused fluences achievable with the CO laser avoid this problem, enabling PE to be effectively cut.
Testing at Coherent has shown that thin (20 µm) PE can be cut at speeds beyond 3000 mm/s with a limited HAZ (30 µm). CO2 laser cutting of this material at similar power levels reaches 500 mm/s at best and creates 500 µm of HAZ. At 60-µm thickness, the CO2 laser simply cannot cut the PE without destroying the material, whereas the CO laser cuts with acceptable speed and cut quality.
Meet the author
Andrew Held holds a PhD in physical chemistry from University of Pittsburgh. He is director of marketing at Coherent for the company’s CO2 laser products; email: [email protected].