Hank Hogan, Contributing Editor
Niche markets used to be enough for microdisplays, but that is changing. The big picture
for small displays includes several technologies, applications and manufacturing
challenges.
Despite their name, microdisplays are making a big impact, and it’s getting bigger.
The size of a computer chip, a microdisplay employs photonics technology to create
a magnified image large enough to fill a movie screen or a home theater, or small
enough to offer full-color, full-motion video on a cell phone. Because their display
engines are the size of a thumbnail, microdisplays have a cost and visual advantage
over the competition.
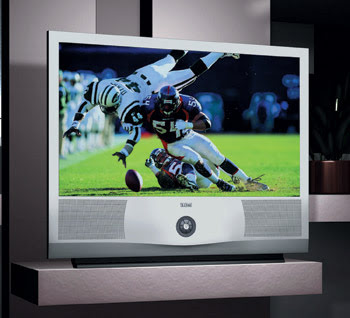
Microdisplay applications are not limited to small screens; they also help power
slim but large-screen high-resolution televisions. Courtesy of Three-Five Systems.
The comparative performance and price of microdisplays
is fundamentally unbeatable, according to Chuck McLaughlin, principal of the
McLaughlin Consulting Group of Menlo, Calif., which provides reports and consulting
services for the display market. With the cost of materials headed steadily downward,
he said, microdisplay-based systems would ultimately be the best and cheapest solution
for a variety of applications.
He’s not the only one who believes
that these devices have a promising future. Last year, the microdisplay market was
worth about $670 million, big enough to attract attention, but small compared with
what’s coming, said Paul Semenza, executive vice president of Stanford Resources
in San Jose, Calif. “We’re forecasting $1.9 billion in 2007,”
he said. The company is the display-market research arm of iSuppli, a supply chain
management company.
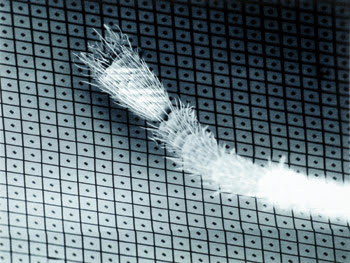
An ant leg on the surface of a Texas Instruments digital mirror device
demonstrates the device’s smallness. Current technology produces mirrors measuring
16 μm2 separated by 1 μm, but semiconductor technology will help shrink
both the size and the cost per unit. Courtesy of Texas Instruments.
Understandably, a swarm of companies
are trying to capitalize on these small displays. They include Japanese giants Sony
and Seiko Epson; semiconductor stalwart Texas Instruments Inc. of Dallas; and smaller
firms, such as Kopin Corp. of Taunton, Mass., Displaytech Inc. of Longmont, Colo.,
Three-Five Systems Inc. of Tempe, Ariz., and the aptly named MicroDisplay Corp.
of San Pablo, Calif.

With microdisplays, it’s really possible to have the whole world — or a high-resolution
image of it — in your hands. Courtesy of Three-Five Systems.
All of these firms are leveraging different
microdisplay technologies. A look at each contender reveals the inner workings,
technological advantages and remaining problems.
Shining through
By far, the leading microdisplay technology is
one that is familiar to many office workers. It’s akin to the liquid crystal
displays (LCDs) found in laptops and small hand-held computing devices. According
to Stanford Resources, this type of microdisplay accounts for 89 percent of all
units shipped. Like laptop displays, it’s an arena dominated by Japanese companies.
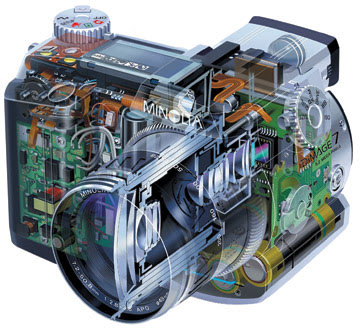
Minolta’s DiMage 7 digital still camera relies on a microdisplay for its viewfinder. Courtesy
of Displaytech.
Like LCDs, these microdisplays sandwich
a liquid crystal material between the circuitry and transparent electrodes. The
electronics allow each pixel to be addressed and manipulated. The circuitry changes
the voltage between the electrodes, and that alters the voltage across the liquid
crystal, which then switches from transparent to opaque. Depending on the approach
used, the result can be either monochrome or color.
LCDs can be classified in a variety
of ways, but an important characteristic is the nature of the driving circuitry.
Single-crystal silicon, which is similar to that found in integrated circuits, offers
predictable transistor performance and consistent yield. Amorphous silicon, which
gets its name from the somewhat disordered nature of its molecular structure, allows
lower manufacturing temperatures.
Despite their commanding position in
liquid crystal microdisplays, Japanese companies aren’t the only contenders.
Kopin also competes and has taken significant business away from the larger manufacturers.
Panasonic, for instance, incorporates Kopin microdisplays in its camcorder viewfinders,
citing the displays’ small form factor and low power consumption. These sorts
of advantages have helped Kopin’s share of the viewfinder market progress
from essentially zero to 35 percent in the past two years. The company’s approach
is similar to its competitors’ but with a unique twist.
Bor-Yeu Tsaur, Kopin’s executive
vice president for display operations, said that his company produces transmissive
liquid crystal microdisplays using single-crystal silicon technology by inscribing
circuitry on standard silicon wafers with standard technology at a silicon foundry.
It then ships the wafers to the firm’s Massachusetts facility for the next
step in the process.
This involves proprietary technology
that peels off the top layer of the silicon. The result is a thin, transparent,
wafer-size skin of silicon that is loaded with all the needed circuitry. This is
transferred to a glass substrate from which production is completed using standard
LCD manufacturing techniques.
The microdisplay offers all of the
characteristics of a laptop screen: color, fast refresh rates and low power consumption.
The last is a particular advantage in handheld devices, which is one reason why
microdisplays are displacing cathode ray tubes in camcorders and other applications.
Because the company’s devices
are transmissive, their optical design is straightforward: Photons from the light
source simply stream through the display. There’s no need for a beamsplitter
or other gear that a reflective approach requires.
Although the products are optically
simple, the peel-off step is difficult to master in a mass-production environment.
Mirror, mirror on the chip
Other companies are also applying unique approaches.
According to Stanford Resources, competing techniques promise to cut the standard
LCD market share to 59 percent by 2007. The reason is not that LCDs won’t
grow along with the market, but that these other methods will grow faster.
One such innovative approach is digital
light processing technology (marketed as DLP) from Texas Instruments. Started
in the mid-1980s as research, the technique later produced chip-size microdisplays
that now appear in high-end business projectors and home theaters. On the horizon
are high-definition televisions based on flat-screen rear projection.
The company has a technology that many
analysts feel will ultimately dominate the projection market.
“Their overall share today is
about 20 percent. It could easily get to be in excess of 50 percent,” McLaughlin
said.
Texas Instruments’ approach puts
microelectromechanical systems (MEMS) to work at steering light around. At the heart
of its digital micromirror devices is an array of half a million or more miniature
mirrors. Fashioned out of silicon and aluminum, they sit suspended over semiconductor
circuitry. In response to a voltage change, the mirror support flexes and the mirrors
twist. The movement encompasses a 20° swing, enough in a properly designed
system to move an image out of the optical path.
Clearly, the devices work by reflection.
Light shines through a color wheel that rotates hundreds of times a second. This
colored light then hits the chip. The individual mirrors twist and flex according
to electronic commands, and the reflected light, now converted into pixels, travels
through the system and the magnifying optics. The result is a bright, sharp projected
image produced by a lightweight device. The company says that its technology delivers
50 percent higher brightness per pound than liquid crystal competitors.
Peter Van Kessel, manager of the company’s
DLP component design, said that devices based on digital micromirror designs are
both thinner and lighter than cathode-ray-tube systems. Consequently, he said, the
technology is enabling a new generation of large-screen televisions that are characterized
by clear, sharp, bright image quality packaged in slim, lightweight and elegant
housings.
As an example, he cited a new large-screen
tabletop television measuring 43 inches. The digital micromirror version is 16 inches
deep and weighs 70 pounds. That compares with the slightly smaller tube-powered
version, which is more than 24 inches deep and weighs more than 250 pounds.
After extensive research and development,
the company’s devices are manufactured with high yields and high reliability.
It claims that 100 percent of the pixels on a chip work — something LCD proponents
cannot claim — and that its devices have the reliability to function for decades
of use, a requirement for many consumer projection systems.
Although its current products have
proved successful, there is room for improvement. Given the company’s semiconductor
heritage and the technology’s roots in integrated circuit manufacturing, it’s
not surprising that the road map includes plans for smaller digital micromirror
devices.
“The first [devices] featured
a mirror size of 16 μm, with a 1-μm gap between the mirrors. Today the
mirror size is 13.7 μm, with an 0.8-μm gap between the mirrors,”
said Van Kessel.
The result has been that high-resolution
devices have shrunk from 1.1 to 0.9 inches diagonally. That’s an area savings
of a third, which ups the chip count per wafer by a third and cuts the cost per
chip by a similar amount, all other factors being equal. Further reductions in mirror
size as well as movement toward larger wafers should, in Van Kessel’s words,
help his company toward “aggressively reducing the cost of the technology.”
Further reflection
Texas Instruments is focusing for the most part
on winning the projection market, but other companies are vying with Kopin for the
handheld-device display market. One of the most successful of these is Displaytech.
Its technology is based on ferroelectric liquid crystals. They can switch states
10 to 1000 times faster and at a lower voltage than conventional liquid crystal
materials, according to Mark Handschy, the company’s chief scientist.
Liquid crystals are suitable for many
electronics applications, but ferroelectric crystals are better-suited to sequential
color processing. Because they switch states so quickly, the pixels can cycle through
all the colors. That makes the optics simpler and increases the effective resolution
— both advantages in the commodity consumer market.
The disadvantage is that ferroelectric
crystals are difficult to master in production. Displaytech, however, claims to
have solved this problem and holds a number of patents on the production technology.
Another technology in the microdisplay
arena that has garnered a lot of attention is liquid crystal on silicon. Unlike
standard LCDs, the liquid crystal on these devices is placed directly atop silicon
circuitry. Light travels in through the liquid crystal, reflects off the surface
and travels back out. Because there’s no need to transfer the silicon to a
glass substrate, the manufacturing process is theoretically cheaper. The optical
path is more complicated because the light is reflected, but the hope is that the
advantages will outweigh this aspect.
The operative word is “hope.”
Up to now, liquid-crystal-on-silicon microdisplays have shown more promise than
they have production. A number of fledgling liquid crystal microdisplay companies
have disappeared in the last few years, several of them swallowed up by Three-Five
Systems.
Al Davis, the company’s vice
president of sales and marketing for microdisplays, said its products have an edge
over the competition because of their high resolution. However, that advantage must
be translated into commercial products, and that is where the problems lie for liquid-crystal-on-silicon
devices.
“It’s just a matter of
getting the yields where they need to be to make it cost-effective. So that’s
been the biggest challenge,” Davis said.
MicroDisplay Corp. is another liquid-crystal-on-silicon
contender. Sandeep Gupta, chief executive officer, said the company has optimized
its devices to transfer 3 GB/s of data from the electronics to the liquid crystal,
which is critical in high-resolution display applications.
Whatever the approach, microdisplays
no longer are a solution in search of a problem. With camcorder and high-resolution
projector products on the market, the future, like the displays, looks bright.
As Gupta noted, “This is an exciting
time, although a lot of microdisplay companies have gone through a lot of pain in
the last decade. In the next decade, I expect it will be a little bit different.
Markets Far and Near
Microdisplays are finding
a home in business-presentation projectors and high-definition televisions. They’re
also appearing in electronic viewfinders in camcorders and digital still cameras.
Microdisplays are expected to play a large role in the coming full-color, high-resolution
cell phone screens.
The market can be broken down into two large categories:
devices that project the image, such as in televisions, movie and business projectors,
and near-eye viewing devices. Examples of the latter are the camcorder viewfinders,
cell phone displays and the futuristic eyeglasses of wearable computers.
The split between the two categories
is not equal, in terms of either units or dollars.
“Most of the units are the near-eye,
and most of the dollars come from the projection,” said Paul Semenza, executive
vice president of Stanford Resources.
He puts the current division at about
a 75:25 ratio; i.e., near-to-eye applications account for 75 percent of the units
but only 25 percent of the revenue. The numbers are reversed for projection applications.
That and some technical advantages explain why Texas Instruments is concentrating
so much on the projection market. Although other microdisplay companies are battling
back fiercely, some companies cite the attention given to and the brutal competition
offered by projection applications as reasons to focus elsewhere.
Near-to-eye applications will get a
boost with the advent of 3G wireless mobile phones, some of which will have small,
high-resolution color screens — a perfect fit for microdisplays. However,
such phones need a wireless infrastructure in place to support them. They also cannot
include the same kind of high-dollar display found in a large-screen television
or business projector.
Looking ahead, Semenza doesn’t
expect the ratios for near and far applications to change. Both will grow, but cost
pressure linked to consumer devices will keep the price down for near-eye applications.
The numbers may change, however, if advanced near-to-eye applications, such as eyeglasses
that act as computer screens, ever take off.
When or even if that might happen is
unclear. As Sandeep Gupta, chief executive officer for MicroDisplay Corp., commented,
“Something will eventually emerge, but I don’t know if that will happen
that soon. The killer device hasn’t been invented yet that I’ve seen
— the one that everyone has to have.”