Compiled by Photonics Spectra staff
A polymer-based material that can heal itself when exposed to ultraviolet
light for less than a minute has been developed for use in automotive paints, floor
and furniture varnish, and more.
The team involves researchers from Case Western Reserve University,
Adolphe Merkle Institute of the University of Fribourg and the Army Research Laboratory
at Aberdeen Proving Ground. Their findings appeared in the April 21, 2011, issue
of Nature (doi: 10.1038/nature09963).
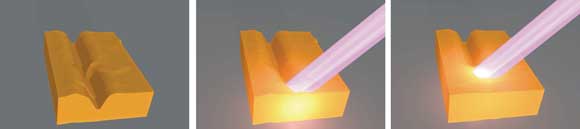
A schematic representation of the optical healing of metallo-supramolecular
polymers developed by the CWRU/AMI/ARL team. Where irradiated with ultraviolet light,
the originally solid material is liquefied and can quickly fill up cracks. After
the light is switched off, the material solidifies, and the original properties
are restored. Courtesy of Marc Pauchard for Adolphe Merkle Institute, Case Western
Reserve University, US Army Research Laboratory.
Although the polymers are not yet ready for commercial use, the
team has shown that the concept does work.
The molecular design of the polymers allows them to change their
properties in response to high doses of UV light. The materials were created by
a mechanism known as supramolecular assembly. Unlike conventional polymers of long-chainlike
molecules with thousands of atoms, these materials are composed of smaller molecules,
which are assembled into longer, polymerlike chains using metal ions as “molecular
glue.” These “metallo-supramolecular polymers” act much like normal
polymers, the researchers said.
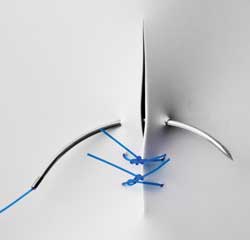
An artist’s illustration of the concept of healable polymers. The new polymers
mimic biological tissue’s unique ability to repair itself. Unlike human skin,
the polymers don’t need stitches, though. Courtesy of Dominique Bersier and
Gina Fiore for Adolphe Merkle Institute, Case Western Reserve University, US Army
Research Laboratory.
However, when irradiated with intense UV light, the assembled
structures become temporarily unglued, transforming from an originally solid material
into a liquid that flows easily. When the light is switched off, the material reassembles
and solidifies again, and its original properties are restored.
Using lamps much like the ones dentists use to cure fillings,
the team repaired scratches in their polymers. Wherever they waved the light beams,
the scratches filled up and disappeared. The researchers also showed that they could
repeatedly scratch and heal their materials in the same location.
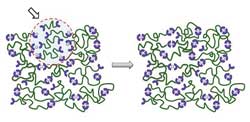
Schematic representation of the molecular design of metallo-supramolecular
polymers. The new materials were created by a mechanism known as supramolecular
assembly: comparably short, stringlike molecules (green) with sticky end groups
(blue) are assembled into much longer chains using metal ions (gray) as “molecular
glue.” Courtesy of Gina Fiore for Adolphe Merkle Institute, Case Western Reserve
University, US Army Research Laboratory.
Although they could use heat to heal the materials, by using light
they have more control, which allows them to target only the defect and leave the
rest of the material untouched.
In addition to testing certain polymers, the researchers systematically
investigated several new ones to find an optimal combination of mechanical properties
and healing ability. They discovered that metal ions driving the assembly process
via weaker chemical interactions served best as the light-switchable molecular glue.
In addition, they found that the materials that assembled in the most orderly microstructure
had the best mechanical properties. But, healing efficiency improved as structural
order decreased.
Up next: The team hopes to use the concept to design a coating
for industrial settings.