Success depends on mating the laser with a precision machine tool and control system.
Jürgen Held and Stan Koczera
Aluminum has always been a challenge to weld,
primarily because of its low melting point. But its weight advantage over materials
such as steel has increasingly put the metal in the spotlight.
Forty years ago, apprentice welders had to develop
their own tricks and techniques to weld aluminum conventionally. These included
identifying which shielding gas to use and determining how to reduce the size of
the weld path. In those days, when the aluminum absorbed the plasma, the water vaporized.
The problem was always the same: If the molten material became too hot, it exploded,
producing pores or even cavities.
Today, the issues related to the low
melting point can be overcome by using high-beam-quality lasers. Although there
are competitive welding processes, the laser advantage lies in the capability for
precise beam focus and, hence, energy delivery to the workpiece. The key to successful
processing, though, lies in combining the laser with a precision machining system.
Compared with other materials, aluminum
is far more demanding of the laser, posing special problems for engineers. The material’s
sensitivity to heat can lead to problems with heat-affected zones. One way to resolve
subsequent cracking is to weld with wire, which can change the mixture of the molten
material. The best wire choices combine nonaluminum metals that are easily weldable,
although the selection will also depend on the type of aluminum alloy being joined.

Engineers process aluminum door modules for Audi on a laser welding
system in which each of the two laser welding heads, mounted on its own independently
traversing shuttle bridge, covers a working area of 3 x 1.5 m and welds two doors.
Other critical components of the welding
system include precision control, as well as a system designed to hold work in position
with absolute clamping consistency regardless of material tolerances. It is only
with such features that manufacturers can prevent high scrap rates.
Nd:YAG or CO2?
Using lasers to microweld aluminum probably began
in the 1970s, and early applications relied primarily on Nd:YAG systems. Relatively
low power, pulsed Nd:YAG systems were used mainly for butt and overlap welding.
During the 1980s, applications expanded to include simple, noncritical tasks such
as window frames and doors.
Large-scale applications didn’t
emerge until the 1990s, driven by the automotive industry’s reaction to rising
fuel costs. This major push to reduce vehicle weight focused on the use of aluminum
in place of steel. Aluminum also offered such significant advantages as resistance
to corrosion, formability and ease of painting.
The common belief that the Nd:YAG is
the most suitable laser for this application is supported by physics, because this
laser’s shorter wavelength provides a higher absorption rate. On the other
hand, there is evidence that CO2 lasers of high beam quality can do as good a job
at lower cost. One aluminum manufacturer’s technical staff and some European
technical institutes have acknowledged that, in keyhole welding, once the keyhole
is made, neither source offers a significant advantage. The primary issue is to
maintain high beam quality when piercing the material. Preliminary tests are usually
advisable to determine which laser technology is the better option.
Laser advances that have contributed
to efficient aluminum welding include not only higher power, but also refined beam
quality. Only five or six years ago, the k-factor — which indicates the quality
of mode structure — of 3-kW lasers was 0.4. Welding aluminum with those lasers
was tricky and required proper shield gases. Today’s Nd:YAG or CO2 slab or
high-Q lasers have k-factors of 0.8 or 0.9, making the welding process easier.
Double-focus welding
The development of double-focus beam technology
has made wider molded seams possible. Double-focus welding uses two foci as close
as 0.4 mm to each other. In tailored blank welding, engineers use this strategy
to overcome the disadvantage of a small gap in the joint. If a laser beam with the
highest energy in the middle blows through the gap, it can melt the sides, lose
energy and result in a bad weld. With a double focus, no energy is lost in the gap,
and the system can concentrate 100 percent of the beam energy into the joint. The
melted material flows together. Good root protection prevents the molten aluminum
from dropping away. For instance, with a butt joint, solid material is placed underneath
the butt.
Laser welding systems have become increasingly
flexible. Engineers can weld steel and other materials with the same welding head
used for processing aluminum. With some machines, switching from welding to cutting
involves no more than a few minutes to exchange processing heads.
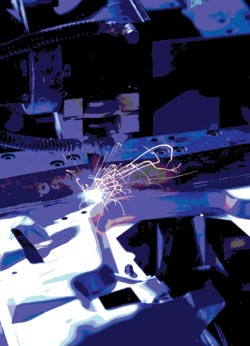
With automated laser welding of door modules, engineers can program
the system to weld up to 110 complete door sets (440 doors) per shift at a rate
of four minutes per set.
Automotive applications
The aluminum welding battle between Nd:YAG and
CO2 lasers is, as expected, being fought first in the automotive industry. One example
of this is a large-scale welding system that Schuler Held Lasertechnik GmbH &
Co. KG created for Dura Automotive Karosseriekomponenten GmbH in Herne, Germany,
to process automobile door modules. Studies conducted early in the design phase
indicated that CO2 lasers with high beam quality could do the job. In fact, the
CO2 proved even more suitable for this aluminum alloy and application than the Nd:YAG.
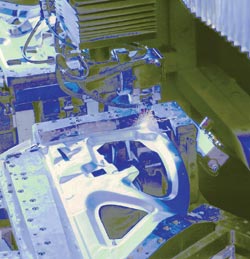
Dura Automotive Karosseriekomponenten welds
aluminum automotive body parts using a dual-head CO2 laser system.
The three-axis system at Dura simultaneously
fabricates a set of four doors on two mirror-image revolving tables with clamp fixtures
for holding the workpieces. Each of the two welding heads, mounted on its own independently
traversing shuttle bridge, covers a working area of 3 x 1.5 m and welds two doors.
The system can weld up to 110 complete door sets (440 doors) per shift with a cycle
time of four minutes per set, or one door per minute. The equipment design ensures
constant production through a beam-switching system. If one of the laser units is
not operative, the remaining unit welds the complete door set. The laser employed
in the Dura equipment is a 2.5-kW CO2 slab laser, the DC 025 from Rofin-Sinar.
Throughout the automotive industry,
Audi may be the most experienced and innovative user of aluminum laser welding.
The body of its Audi A2 vehicle, for example, is fabricated completely of aluminum.
The company robotically welds the chassis, as well as the roof and floor of the
car. The use of robots is made possible by a spring-loaded element that mechanically
maintains the laser focus on the top of the surface being welded.
Future view
Aluminum processing also is gaining acceptance
within the aerospace and shipbuilding industries. One reason involves the potential
cost savings. Consider a single aerospace application — wing construction.
Aluminum welding is perhaps the only way to reduce the time and cost involved. Eliminating
hundreds of rivets will reduce weight, and joints should have equal or better integrity.
However, because of the wing size of modern airliners, aluminum welding using robots
would be unwieldy. Processing will most likely require specially designed and constructed
laser machining systems.
The first application of laser welding
to airplane construction involves joining stringers, or supports, to fuselages.
This process is being tested for Airbus.
Other industries that are expected
to engage in laser welding of aluminum are those concerned about component weight
and corrosion, as well as whether or not welding structural elements or tailored
blanks with complex profiles can reduce production costs.
Meet the authors
ürgen Held is a founder of Held Lasertechnik,
a company acquired in 1999 by Schuler AG (The Schuler Group). He is now president
of Schuler Held Lasertechnik, whose main facility is in Heusenstamm, Germany, near
Frankfurt.
Stan Koczera is manager of US laser
sales at the company’s US headquarters in Canton, Mich.