The mechanical energy from pulsed lasers offers a highly versatile tool for improving the performance, reliability, and lifetime of turbine blades, airplane wings, and other metal parts.
Laser shock peening is a process that adds beneficial residual stress points in materials commonly used to develop a wide range of parts and components. These residual stresses effectively increase the materials’ resistance to surface-related failures such as fatigue, fretting fatigue, and corrosion cracking.
A thin flow of water confines laser-generated plasma at the component’s surface, pushing as much energy into the material as possible. Courtesy of Curtiss-Wright.
Combining lasers, robotics, water, and software, laser peening systems extend the life of components used in aircraft, power plants, nuclear reactors, fuel canisters, and other applications where mechanical wear is common. In some cases, laser peening can improve resistance to fatigue and cracking by as much as an order of magnitude and allow a corresponding tenfold increase in component lifetimes.
Current advancements are only enhancing the promise of this materials processing capability and will rely, in part, on getting the most out of the laser tools involved.
Better blades
Laser shock peening is fundamentally a mechanical process, similar to using ball-peen hammers on a finished weld joint to strengthen it.
“When you peen something, you’re hitting the surface to do plastic deformation,” said Lloyd Hackel, vice president for advanced technologies at the Metal Improvement Co., a subsidiary of Curtiss-Wright Surface Technologies. The objective is to create compressive stresses in the peened material that effectively make a fabricated component more durable and resistant to cracking. The technique has been particularly effective, for instance, for improving the lifetimes of turbine blades for aircraft.
An operator laser peens a large blade for a Rolls-Royce jet engine, selectively creating areas of compressive stress to enhance the blade’s resistance to fatigue and cracking. Courtesy of Curtiss-Wright.
Curtiss-Wright sells laser shock peening as a service and has processed the large fan blades used in the engines that power Boeing’s 777 and 787 commercial aircraft, as well as Airbus’ A340, A350, and business aircraft. The use of laser peening partly explains why these aircraft have not seen any failures from blade fretting fatigue in 20 years, according to Hackel.
Lockheed Martin also uses Curtiss-Wright’s services to laser shock peen components for its F-22 and F-35 fighter jets. In addition to peening the base of the fan blades, which experience the most stress, Curtiss-Wright peens the leading edges of the blades to prevent the cracking that can occur when small debris are sucked up into the engine and strike the blades.
The laser peening process works by causing plastic deformation that is greatest near the surface of a component
material, which is also where a component is likely to crack. The energy from the pulsed laser initially expands the material at a localized point, which subsequently causes the surrounding material to compress inward, leading to denser sections that are more crack-resistant.
The use of laser peening on the engine fan blades that power commercial and business aircraft has helped prevent failures caused by blade fretting fatigue. Courtesy of iStock.com/the_guitar_mann.
The pulsed laser energy does not directly cause the plastic deformation, Hackel said. Instead, the laser strikes the surface of the material, forming a plasma that absorbs further incoming energy.
The excited plasma, in turn, bombards and peens the surface.
The plasma, however, is ineffective at peening by itself. The continued laser pulses in the peening process create an ionized cloud of heated and vaporized plasma, which flies away from the surface into the surrounding air. Therefore, insufficient laser energy is transferred into the mechanical forces acting on the target. To minimize energy loss, peening techniques often involve covering the target surface with a thin layer of water. At only 1 or
2 mm thick, the water layer is transparent to the incoming laser beam, which is typically emitted in the NIR range.
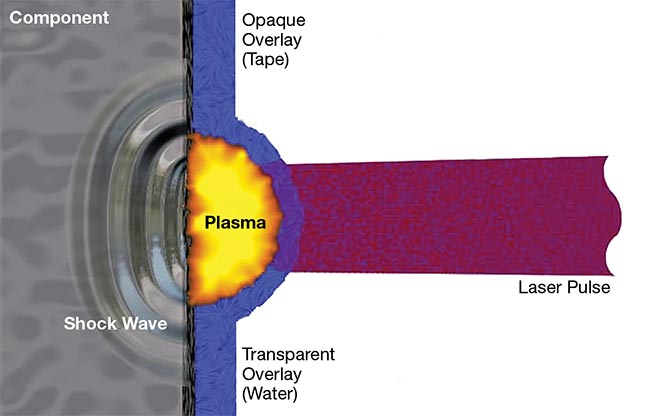
A schematic of the laser peening process. A laser pulse strikes a material to create a plasma. A thin sheet of water confines the plasma energy to the material’s surface so that the resulting mechanical force can selectively create beneficial compressive stresses that help the material resist cracking. Courtesy of LSP Technologies.
“The goal is to confine that plasma and push as much energy into the material as possible. So, we use a water layer,” said Micheal Kattoura, materials research engineer with LSP Technologies, a laser peening system and services vendor.
According to Kattoura, LSP Technologies uses diode-pumped lasers from Cutting Edge Optronics, a subsidiary of Northrop Grumman. He said it is important to achieve the right power density by using an optimal combination of pulse energy, duration, and spot size. One system from LSP Technologies, for instance, employs a laser that emits 20 1053-nm pulses per minute, with each pulse lasting from 10 to 20 ns. Too high a power density results in material damage, while too low a power density fails to achieve the peening effect. Soft materials such as aluminum or magnesium require lower power densities than hard materials such as high-strength steels. The maximum energy per pulse rarely exceeds 10 J,
Kattoura said.
According to Hackel, Curtiss-Wright relies on in-house manufacturing to produce the coherent sources for its laser peening systems. The company’s laser tools utilize master oscillator power amplifiers along with stimulated Brillouin scattering phase conjugation that together allow Curtiss-Wright to perform real-time wavefront correction. The technology cancels out distortions in the beam and enables nominal output powers of up to 20 J per pulse at rates of up to five pulses per second.
Factors affecting throughput
As with power density, a lower laser output can be used when peening softer materials such as aluminum, which may only need pulse energies of one or two joules. Hard steels may require 10× this energy. However, energy output optimization is influenced by more than the material being processed.
“Large-energy laser peening and low-energy laser peening are not equally effective,” Hackel said. “High energy per pulse matters because it impacts the depth to which the peening can penetrate.”
The penetration depth is proportional to spot size, he said. One way to achieve a power density that is sufficient for the peening process to occur is to focus the beam into a small enough spot size. This has the advantage of requiring less power in each laser pulse. But spot sizes of
1 mm or less also mean the peening effect will have a shallower depth. Thus, if a crack forms in the material and begins to spread, it may spread more easily.
Reducing spot size can sometimes
affect throughput because more laser shots are required to process a given area. But again, a smaller spot size often allows
reduced energy per pulse, which, in turn, allows a higher repetition rate. This capability to fire shots faster can help offset the greater number of shots needed, netting the same throughput despite the smaller spot size used.
Future directions
Laser shock peening continues to evolve in both its capabilities and scope. The technology’s efficacy has traditionally been limited in applications where the temperature of a laser-peened part remains well below 50% of the base material’s melting point. Operating above these temperature thresholds leads to annealing, a physical and sometimes chemical alteration of the material’s properties that can reduce or eliminate the beneficial compressive stresses that laser peening provides.
A potential new solution under development by Curtiss-Wright combines laser peening with heat treatments that create microstructural changes in the base material to lock in protective stresses. Hackel and his collaborators at the University of Alabama showed that this benefit occurs due to the formation of precipitates, which are deposits that act like anchors to prevent high temperatures from annealing out the peening effects. Applications that benefit from this combination of laser peening with microstructure engineering techniques include the blades for jet engines and the turbines in land-based electric power generators. This approach could also benefit emerging technologies such as supercritical CO2 power generators that are specifically designed to operate at higher temperatures than conventional steam-based generators, and thereby to produce minimal or no greenhouse gas emissions.
These cutting-edge generators must be constructed from materials that can withstand high temperatures and large mechanical stresses for extended periods of time, which the combination of laser peening plus thermal microstructure engineering is helping to achieve.
Another field that is helping to expand the scope of laser peening is robotics. It enables engineers to design systems that can process very large parts onsite. For example, LSP Technologies has developed a system consisting of two robots. The first robot moves a component in front of a fixed laser, thereby placing the laser beam onto spots that need peening. The beam is on only during peening; it is off while the component is positioned. The second robot flows a stream of water over the target and coordinates its moves and the water dispersal with the actions of the first robot.
LSP Technologies’ system is designed to bring the benefits of laser shock peening to components that are not easily transportable, such as the wing of an airplane.
Robotics is also enabling laser peening systems that can process complicated shapes and components. These systems may selectively apply the technique only over the small parts of a large structure while still increasing the structure’s overall lifetime and reliability.