KEN BARAT, LASER SAFETY SOLUTIONS
The commonly accepted definition of a cleanroom is a controlled environment that filters out pollutants such as dust, airborne microbes, and aerosol particles to provide the cleanest area possible. Cleanrooms are grouped, or classified, by the number of particles allowed in the air per cubic meter. These work areas control additional variables, such as temperature, airflow, and humidity.
The precise function of a cleanroom depends on its group. Certain cleanrooms are dedicated to fabrication operations. Others support Class 1 products used in automated operations — similar to a manufacturing environment. Cleanrooms that contain a high-power laser system, such as terawatt or petawatt systems, are classified separately.
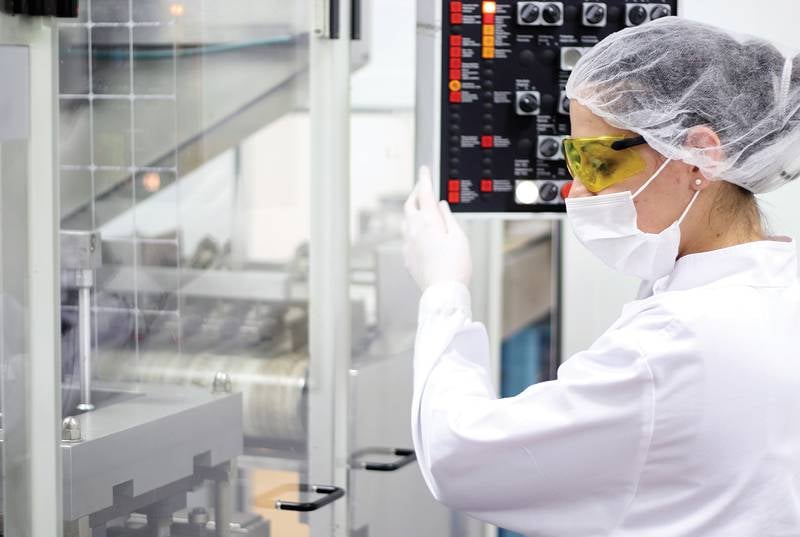
Cleanrooms demand that their users follow a stringent set of rules to keep the environment pure. The Safe Use of Lasers standards do not always mesh well with these rules, presenting a unique challenge for laser safety officers (LSOs). Courtesy of iStock/RGtimeline.
Given these different groupings and classifications, the size of cleanrooms varies. Some are hundreds of thousands of square feet. Others may be only a few hundred square feet.
For these reasons, the cleanroom is inherently an environment that presents unique safety controls and challenges for the use of lasers. For the laser safety officer (LSO) responsible for the cleanroom, there are a number of challenges that extend beyond the scope of those that can be addressed using traditional control measures.
Warning signage
Many of the safety controls that are available to the LSO in a cleanroom environment qualify as preventative measures. Warning signage, for example, is an essential device in this type of controlled setting.
Important factors must be considered when implementing signage: Depending on the size of the cleanroom and location of laser systems, a required laser warning sign at the entrance could be useless to system users. This might be because the actual laser hazard is scattered around the cleanroom, or in an open spot far away from the location of the door. In smaller cleanrooms, the warning sign should be positioned in the vicinity of the laser protective eyewear.
Access control
Measures to be put into place prior to the start of cleanroom operations also extend to access control. Before entering a cleanroom, workers must ensure they are wearing appropriate cleanroom equipment. In some cleanrooms, it is even required that workers go through an airlock station before entering the cleanroom. Although this is a rare case, such protocols for entry commonly accompany added measures for high-power laser systems, such as petawatt or optical accelerator setups. It is rare in most cases, however, that the access control system (interlocks) serves as the access protocol and facility entrance system.
Wearing cleanroom clothing
Cleanroom-appropriate clothing falls under two categories, with the broader of the two, personal protection equipment (PPE), widely known even to those outside cleanroom environments. For laser system users, as well as cleanroom workers who may not actually encounter beam hazards, PPE does inflict restrictions on the wearer: Anyone who has geared up fully can attest to the restrictive and uncomfortable nature of working in such clothing. This clothing is designed to prevent particles generated by the human body from contaminating items in the cleanroom. Such apparel can also be designed to offer a degree of protection to the wearer and other present personnel.
Stopping an errant beam is extremely important, since significant equipment damage can occur in a short time. In this way, an e-stop does offer value.
Cleanroom clothing can include the following articles: bouffant caps, lab coats, shoe covers, face masks, beard guards, and gloves. The American National Standards Institute (ANSI) Z136.7-2020 Testing and Labeling of Laser Protective Equipment standard does not presently address cleanroom clothing from a laser protective perspective.
Laser protective eyewear
For cleanroom workers, laser protective eyewear is no different from the standard laser protective eyewear used in a traditional laser laboratory. However, consideration to storing and cleaning the eyewear may necessitate extra attention, due to the stringent need to prevent contamination from entering the workspace. This consideration will depend on the rating of the cleanroom.
Training
The potential for a beam hazard to cause serious harm to a cleanroom worker or to equipment intensifies during times of operation. Proper training is vital to reducing risk in cleanrooms where this may be a concern.
Two groups should receive training when working in cleanrooms. First are those with access to the laser or laser system. Members of this group should be considered the traditional laser users — and fundamental institutional training is imperative. These workers should receive documented on-the-job training (as referenced in Z136.8). And after a predetermined length of time, these workers should receive a refresher lesson spanning all necessary training and instructions.
Next are those who may work in the cleanroom, but who have no hands-on contact with the lasers. These may be staff members who are delivering parts or picking up completed work for the next step in a fabrication process. For these individuals, awareness training is an important requirement, serving to not only ensure that any control measures are respected but also to remove inaccurate perceptions of concerns.
Standard operating procedure
Standard operating procedure (SOP) should function in tandem with proper training and instruction. Too often in cleanrooms, outside of the science laboratory cleanroom, SOPs exist as operational work documents that do not qualify as a laser safety SOP. In a cleanroom that contains Class 1 laser systems with embedded Class 3B or Class 4 lasers, effective SOPs must address requirements for service and/or maintenance.
In the absence of an SOP, a temporary control area document can be an acceptable, similar alternative, and can be considered acceptable. In this case, if temporary or mobile barriers are to be used during service, the chosen barrier or curtain must be cleanroom compatible. The same must be true for any temporary signage that is used. Space to properly store these barriers when not in use also needs to be planned for.
Emergency stop
Due to the nature of laser use in cleanrooms, a master emergency stop button is rarely used and may not be helpful as designed. In a fabrication cleanroom that consists of individual workstations, for example, each station might have an “off” button on the power supply — but little more. Further, in a cleanroom containing Class 1 products, such as semiconductor tools, each unit may have its own emergency stop. And, while some cleanrooms may feature such units with an “e-stop” at the exit, these devices or mechanisms are far less effective than a control room that oversees operations for cleanrooms that contain terawatt, petawatt, or similar systems. The control rooms for cleanrooms that contain these systems must have a way to stop procedures. These systems all have defined and precise beam paths; these beams are not like a rouge firehose spraying in random directions.
Stopping an errant beam is extremely important, since significant equipment damage can occur in a short time. In this way, an e-stop does offer value. The questions are how many are needed, and where they ought to be located.
Many important factors must be considered when answering these questions. E-stops that are put into place too early in the design process ensure that access issues presented by the equipment are not considered. I have also observed e-stops placed on walls but never connected to the laser equipment, which presents an obvious absence of effectiveness.
Traffic
Traffic must also be considered. In the traditional laser control area, spectators and visitors are discouraged or restricted from entering. Cleanrooms that contain multiple workstations will have staff members who circulate in the area but who are not involved in direct fabrication or testing that involves laser use. It is not uncommon to have only the system operators wearing laser protective eyewear. This causes the appearance of a lack of safety. To some degree, issues here can be resolved by adding to the training section.
Area warning device, visible warning light
Warning lights and/or devices also offer tangible benefits to cleanroom workers and systems, although they are rarely found at the entry points of fabrication cleanrooms. This is because many of these lights are tied to the power supply and may be on at all times.
In a cleanroom that contains Class 1 laser systems with embedded Class 3B or Class 4 lasers, effective SOPs must address requirements for service and/or maintenance.
Also, warning lights may indicate equipment status and be a cause of confusion to staff members, even after training. In cases in which multiple laser workstations are in the cleanroom, it is rare to find a laser warning light or indicator at each station. And it should go without saying that one must consider how such lights look when wearing protective eyewear.
For the laser safety officer
It is clear that laser use in cleanrooms does not easily mesh with the general guidance found in the existing Z136: Safe Use of Lasers standards. These laser standards give the LSO considerable leeway to apply controls and modify
required controls (termed “alternate control measures”) based on hazard evaluations.
LSOs given the responsibility of overseeing Class 3B or Class 4 lasers should work in a cleanroom environment “gown up” and spend time in the shoes of its users. Alternative controls, or any rationale to deviate from the requirements of the laser standards, must be documented. Hopefully, laser safety in the cleanroom will be specifically addressed within the laser standards or as an appendix in future editions of the laser user standards.