Continued advancements in laser pulse width, output power, and system designs are blazing trails for new applications and growth in laser micromachining.
HANK HOGAN, CONTRIBUTING EDITOR
Driven by demand from automotive, electronics, medical devices, and other end markets, the micromachining market is on track to grow at a 6.9% compound annual growth rate over the next six years to reach a market value of $4 billion, according to a June report from Acumen Research and Consulting.
Micromachining encompasses a number of technologies that are capable of cutting, drilling, and welding miniature components and features. But laser micromachining stands out for the unique combination of advantages that it delivers. The ability to apply various wavelengths, powers, repetition rates, and pulse widths to the task allows lasers to machine a variety of materials, including metal, polymers, ceramics, and glass. Laser machining is also easily automated and, as a noncontact method, can help to prevent contamination of the workpiece.
Microholes laser-drilled into a stainless steel component of an electrospray thruster for a satellite. Courtesy of Potomac Photonics.
The continued success and growth of this type of miniscule manufacturing comes, in part, from the introduction
of new laser-based systems that are
less expensive while offering shorter wavelengths and pulse widths, along
with higher repetition rates, said Mike Davis, vice president of manufacturing
at Potomac Photonics. The company specializes in developing processes for microfabrication and supplying micromachined and other manufactured parts to customers.
According to Davis, the choice of micromachining tools today can involve excimer and diode solid-state lasers operating at wavelengths as short as 193 nm; Nd:YAG lasers emitting at 1064 nm, or, when frequency-doubled, at 532 nm; CO2 lasers emitting at 10.6 µm; or some combination of these various technologies.
Wavelength is an important laser parameter because it determines the smallest achievable spot size, and this, in turn, determines the minimum size of machinable features. CO2 lasers, for example, are suitable for drilling holes through today’s printed circuit board (PCB) materials. However, the minimum hole dimensions required in today’s PCBs are less than a CO2 laser’s 10-µm wavelength, sometimes by a significant margin. So, lasers operating at shorter wavelengths must be used.
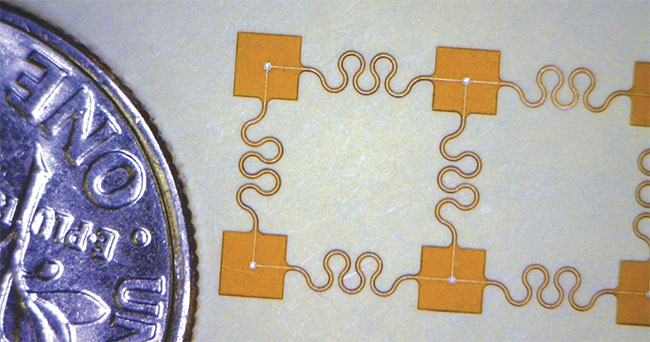
Advancements in laser and beam control technology have enabled the micromachining of feature sizes as small as a micron in flat (top) and 3D (bottom) polyimide polymer parts. Courtesy of Potomac Photonics.
In short, having a wide array of laser technologies in the toolbox is critical to developing a process that meets customer
needs for cost and quality, Davis said. “The first thing we look at is: What
materials are we processing? Certain
materials just won’t process well at certain wavelengths.”
For instance, polymers do not absorb readily in the infrared, so visible or UV processing may be needed. Potomac Photonics has employed UV lasers in systems designed to weld two transparent polymers together. Traditionally, the process of welding polymers together has required at least one polymer material to be dark colored, Davis said. Transparent glass is another material that often requires UV lasers in order to be micromachined.
Conversely, metals, ceramics, silicon,
and similarly opaque nonreflective materials easily absorb IR light. Lasers operating at these wavelengths tend to be higher power and less costly to buy and operate, and they run at higher repetition rates than sources emitting in the UV.
Power and repetition rate are also important parameters when selecting a laser machining solution because they directly affect throughput and cost of the finished part. But running the laser at higher output powers may lead to charring and make it more difficult to achieve specifications for features such as hole diameter.
“Whereas if we slow things down, find the proper wavelength, find the proper pulse spacing, even going with a lower frequency [repetition rate] and processing at a lower speed, then you have very well-defined edges, very controlled and repeatable features,” Davis said.
This approach can also minimize or even eliminate cleanup and other post-processing steps. The result is an overall lower production cost, even if the micromachining process is not the fastest possible option.
This balancing between speed and quality involves other elements of the laser system as well, such as the beam delivery components, steering optics, and other mechanisms. Increasingly, the balancing process also includes controlling the laser’s operation in the time domain, said Herman Chui, senior director of marketing at MKS Instruments’ Light & Motion division.
Pulse power
Laser pulse width is critically important to micromachining, as it ties into peak power and a laser’s ability to selectively melt or vaporize sections of the workpiece. Longer pulses may lead to ragged feature edges, unwanted melting, or other undesirable effects. Ultrashort pulses in the femtosecond or picosecond range minimize this heat-affected zone.
Fortunately, 100-W femtosecond lasers have replaced the standard 5-W models of a few years ago, said Brennan De-Cesar, manager of advanced technology at Amada Weld Tech. Such solutions offer end users a roughly twentyfold increase in peak power. Further, 50-W femtosecond lasers are priced comparably to earlier 5-W models.
When machining a part with tight tolerances, managing the heat load to maintain the load’s consistency is important, Chui said. The laser needs to uniformly deliver energy to a workpiece despite moving from one location to the next and targeting at varying speeds. Controlling pulse width, pulse shape, and repetition rate can all help to achieve this goal, as can splitting up a single pulse into a burst.
Chui cited the example of a recent collaboration between Hewlett-Packard and Spectra-Physics (now part of MKS’ Light & Motion division) to explore ways to optimize the micromachining of inkjet nozzles. The research leveraged a laser emitting at 532 nm to compare the effects of a 47-ns pulse width and 135-kHz repetition rate versus a different output setup that comprised three 20-ns pulses separated by 30 ns at a 275-kHz repetition rate.
Tunnel magnetoresistance sensor wafers that were processed with a laser annealing system to selectively heat up parts of a material and enable more efficient programming of the finished sensor. Courtesy of 3D-Micromac.
The study found the latter configuration increased the power on the target by 50% while tripling throughput and improving the quality of micromachined trenches.
Such an increase in manufacturing efficiency comes from the effect of each individual pulse. The first pulse can help to alter the surface of a workpiece to allow a second pulse to transfer its energy more effectively.
Not all pulses of the same supposed duration are equal, DeCesar said. The effects of a 400-fs pulse, for instance, may actually unfold over a much longer duration of time, effectively allowing the delivery of energy to take a picosecond or more.
At sufficiently high peak powers, an ultrashort pulse can produce multiphoton effects that increase a material’s photon absorption.
The continued success and growth of this type of miniscule manufacturing comes, in part, from the introduction of new laser-based systems that are less expensive while offering shorter wavelengths and pulse widths, along with higher repetition rates. Courtesy of Potomac Photonics.
“This can, for example, make an IR wavelength laser more capable of processing highly reflective metals or polymers — materials that have traditionally required shorter wavelengths for effective processing capabilities,” DeCesar said.
When manipulating pulse width and shape, maintaining beam quality becomes more important, Chui said, because this helps to ensure consistent results.
Balancing act
Engineers must take many aspects into consideration when devising a solution to a particular set of micromachining requirements, said Uwe Wagner, CEO of 3D-Micromac. The laser, beam delivery, motion control, and software all play a role in enabling a finished system to hit its cost, feature size, throughput, and quality targets.
“Quite often it’s an optimization triangle,” Wagner said.
“You can’t bring everything to an optimum at the same time. You have to balance things out.”
In general, more power equals higher throughput, and today’s lasers produce ample power for most micromachining tasks. This was not always the case five years ago, Wagner said.
Consequently, the laser component rarely causes processing bottlenecks. Instead, it is often the beam positioning system that limits throughput. Splitting a single laser beam into several beams and applying advanced beam shaping methods can help
to overcome this problem.
For some applications, two lasers are better than one. For instance, one micromachining application that 3D-Micromac tackled required rapidly removing a polymer coating from semiconductor chips before the system could machine smaller features. The solution involved first
applying a low-cost CO2 laser to remove most of the polymer material, followed by using an excimer laser to perform fine polishing.
A scanning electron microscope image of laser micromachined features on a sample stainless steel injector. Courtesy of Amada Weld Tech.
A similar multistep approach can be applied when drilling holes that change diameter at various depths, such as an opening that is wide at the top and narrows in steps as it goes deeper. Rather than using two lasers, changing the shape of a single laser beam as it drills can
yield holes with such stepped profiles.
While many micromachining processes may require shorter-wavelength lasers in order to achieve tight tolerances, 3D-Micromac generally tries to use longer wavelength sources in its final production system for cost reasons, Wagner said.
Future machining
Surface or material modification is a growing application for laser micromachining technology, Wagner said. Representative uses may include preventing soiling materials from sticking to solar panels; or selectively altering magnetic
or other properties in small spots on a
material. These types of laser micro-
machining applications may require
production of fine features over large areas that measure as much as 6 m on a side, he said.
Amada Weld Tech’s DeCesar said that, while ultrashort pulse width lasers are less expensive than they once were, they still contribute to a significant portion of overall system costs for micromachining
solutions. Beam delivery systems also contribute substantially. Complex multiaxis heads may cost as much as, or more than, a midpower femtosecond laser.
Further cost reduction in these components could pave the way in the future
for wider use of precision laser micro-
machining systems.
“A high-quality ultrashort pulse laser that is priced similarly to modern fiber lasers would truly disrupt the market,” DeCesar said.