JOSE POZO, EUROPEAN PHOTONICS INDUSTRY CONSORTIUM (EPIC)
Not long ago, laser materials processing was characterized by four basic manufacturing operations: surface treatment, marking, removal and welding. Buoyed by advances in additive materials deposition, the proliferation of laser annealing for thin films, and the evolution of 3D printing for rapid prototyping, the laser materials processing market in 2016 is undergoing seismic change — not only in Europe but in APAC countries such as India, Japan, South Korea and China.
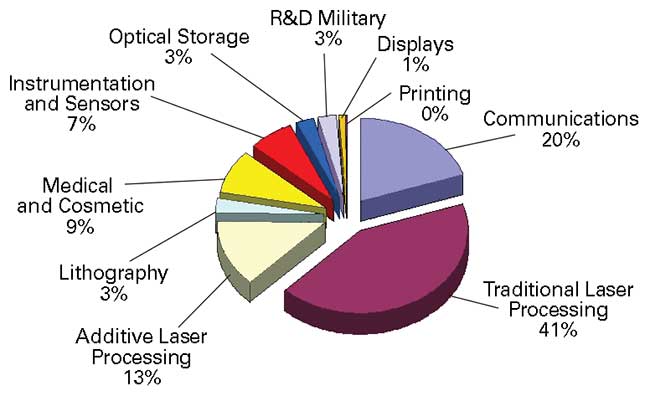
Materials processing accounts for a significant share of the total laser market in research compiled by EPIC. Courtesy of EPIC.
A new generation of lasers suited for cutting metal, diamond and glass, and others critical to the formation of plastics and fibers, have emerged in response to new demands in the health-care and consumer end markets.
High-power lasers dominate the materials processing sector. The umbrella of mature power is broad and complex — nanosecond or picosecond; ultraviolet, green or infrared; CO2, diode-pumped solid-state (DPSS) lasers and fiber lasers. As the dominant market-driven applications in laser materials processing are cutting, ablation, welding, converting, cladding, heat treating, marking and engraving, the golden question is if there is a key laser that can be customized to cover many applications or if there is
only a laser suitable for each of the applications.
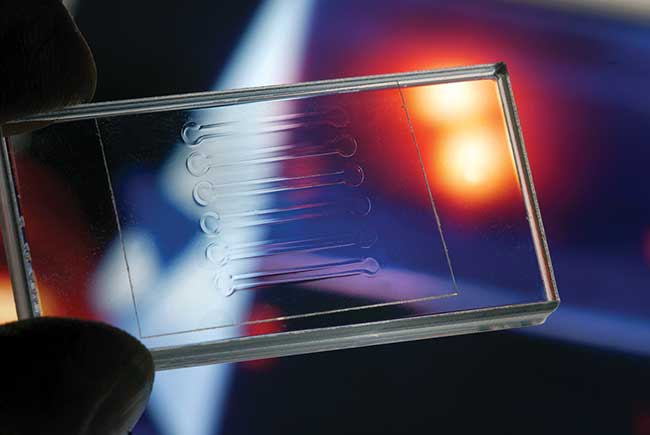
Laser welding of glass requires low thermal conductivity of the material, representing an additional challenge. Courtesy of Fraunhofer ILT.
There’s no easy answer; it’s basically a combination of choosing the right laser and right application-specific customization. Europe has a number of companies focused on high-power lasers for materials processing, from large enterprises such as Trumpf, Rofin and Coherent that mostly develop a full system for each application, to SMEs that develop a limited number of products that are customized to serve several applications.
In fact, the companies that form this sector are for the most part from European countries, and the industry itself is the latest evolutionary development in a long European history of excellence in optics and fine mechanics. Yet the development of laser systems requires competencies and experience in a wide range of disciplines such as optics, electronics, user interface design, material handling, IT interfacing to machine vision for in-line quality inspection, and more.
The strong European presence in laser materials processing is reflected in the broad value chain with many participating companies, from fundamental materials development (such as IQE in Wales, U.K.) through all aspects of laser beam generation, to processing protocols and workpiece handling (like Prima Industrie in Italy). This value chain is supported by R&D funding that tends to encourage the development of process systems based on lasers, rather than laser development per se. In addition, there are a number of open-access laser process development laboratories where potential customers can try out new equipment and processes.
In essence, laser materials processing has consisted traditionally of the subtractive: that is, materials are removed from the workpiece. Laser additive processing, otherwise known as 3D printing, is a complement to these operations. For a number of years, laser additive processing was regarded as an artistic curiosity. However, according to internal market research done by EPIC, it is now an important contributor to the laser systems market, and generated 13 percent of total revenues in 2014. Furthermore, laser additive processing has grown 20 percent per year for several years. It is estimated that it will contribute 30 percent of laser system revenues by 2020.
Largest segment of industrial laser systems market
Laser systems are a significant indicator of impact on sector development, because systems are what most companies sell or are trying to develop for sale. This is in particular the case for laser materials processing, which is the largest market segment for lasers. Laser materials processing is the largest part of the worldwide laser systems market sector.
Additive materials deposition by laser is emerging as a new materials processing sector. Manufacturers, primarily European companies, are largely different from those providing solutions for traditional materials processing, such as etching, drilling, cutting and welding. Additive materials processing is currently growing at about 20 percent per year. European laser companies are leaders in numerous other sectors: Zeiss Meditec in medical/cosmetic, Oclaro in communications and EADS in defense. However, coverage of the sector value chain by European companies is nowhere as complete as is the case for laser materials processing.
Laser annealing is widely used to improve the characteristics of materials, in particular thin films, with applications extending from wafer scale to large substrates. This technique is used to activate dopants for advanced CMOS circuitry, sensors, insulated-gate bipolar transistors, 3D integration and more. Laser annealing is also widely adopted for the crystallization of amorphous silicon films used to form the polysilicon layers that provide the electrical functionality for high-resolution displays as used in today’s smartphones and tablets. Laser crystallized polysilicon also provides the stability required to drive OLED (organic LED) displays. Depending on the materials and layer structure of the thin films, different laser wavelengths, pulse widths and power levels are used. Excimer lasers (as the ones from Coherent) are one of the main solutions to anneal the thin (100-nm) a-Si film on large glass substrates that enables production of smartphone and tablet-sized high-resolution displays. DPSS lasers offer longer wavelengths for deeper activation, and the high power available from direct-diode lasers is optimal for the annealing of thicker films and materials.
.Sapphire engraving. Scribing speed 300 mm/s, one pass. Sample thickness about 330 µm. Courtesy of Light Conversion.
Laser cutting: CO2 and fiber lasers dominate
Laser cutting is a mature industrial process with high flexibility, noncontact and stress-free methods that produces finished parts directly from the tool. Laser cutting is a very precise process, with excellent dimensional stability, very small heat-affected zone and narrow cut kerfs. Various technologies are used in this process depending on the type of material to be cut. Plastics, ceramics, fiber-reinforced materials and organics such as leather, fabric, paper, wood and others, are processed ideally with diamond CO2 lasers. Its wavelength of 10.6 µm offers optimal absorption to cut by evaporation or melting nonmetal materials. While the 10.6-µm wavelength from diamond CO2 lasers can cut plastics and metal materials, fiber lasers emitting at 1-µm wavelength are the optimal tool for cutting metals including high reflective materials like aluminium, copper or brass. Other brittle and transparent materials are best matched with ultrashort pulse and UV lasers. For example, the cutting of glass and sapphire with inner/outer contours and bevel is very effective using high-power picosecond laser products.
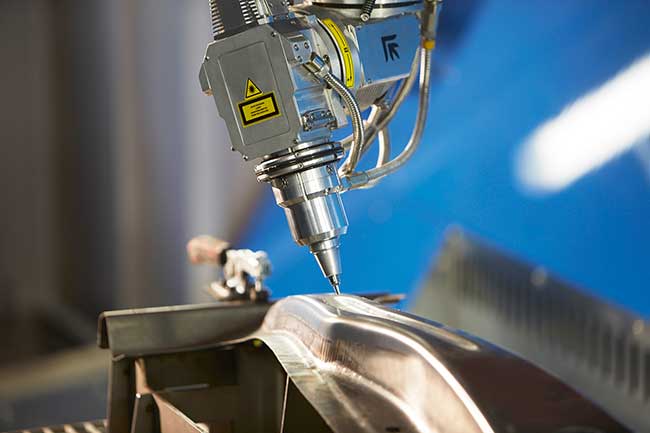
Three-dimensional laser cutting of autobody panels. Courtesy of Prima Power.
Furthermore, the demand for thin glass used in smartphones, tablet PCs and touch panels is steadily increasing. Mobility is a must in these markets and has driven the need for ultrathin glass, strengthened glass, sapphire, rounded contours, slots, button holes and bevels that enable a sleek bezel-free design. Lasers are playing a pivotal role in bringing cost-effective volume production by providing distinct advantages over traditional mechanical scoring, grinding and polishing. The noncontact laser process is fast, precise and achieves higher bend strength compared to mechanical processes. Also, laser processing uses no water, oil or chemicals and leaves no particle or artifact on the sheets. This ensures high yield and fewer process steps. The range of materials and cutting tasks has led to a variety of processes such as full body cut, laser scribing, ablation and nonthermal processes such as filamentation. CO2 lasers provide the highest speed for straight cuts with perfect edge quality. The nonthermal processing of picosecond lasers comes into play for ultrathin glass, strengthened glass or sapphire with rounded corners, inner holes and slots.
The main benefit resulting from using a laser for this technique is high processing speeds with no tool wear due to a contact-free process. This leaves low heat-affected zones and low part distortion, resulting in small welding seams with very little need for post processing. A high degree of automation manufacturing including process monitoring, control and documentation result in excellent product quality and repeatability. Typically, any metal that can be welded by conventional technology can be welded by a laser. For keyhole welding, materials with a higher thickness-to-width aspect ratio are welded with 1-µm wavelength typically using fiber lasers. Sheet metal up to 2 mm can be heat-conduction-welded using high-power diode lasers.
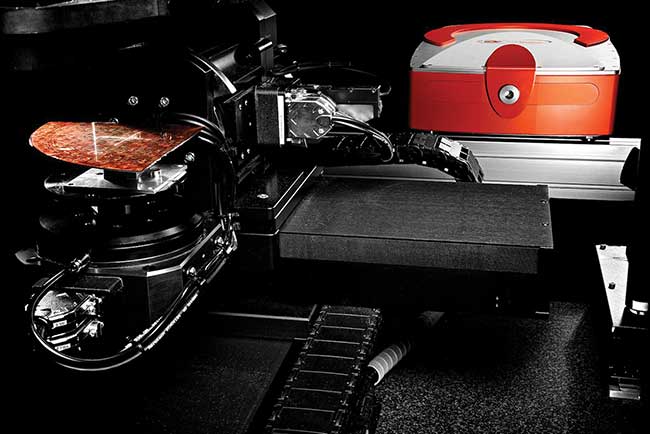
Fiber laser cutting. Courtesy of Amplitude Systemes.
In addition, fiber lasers are also key for plastic and glass welding. A selection of plastics can be successfully welded using a transmission welding process. Glass welding is a growing application in the display manufacturing to provide the perfect hermetic sealing of active-matrix organic LED (AMOLED) displays.
Laser cladding, heat treating: the realm of high-power diodes
Cladding is a well-established process used in a variety of industries for improving the surface and near surface properties of a part (e.g. wear, corrosion or heat resistance), or to resurface a component that has become worn through use. The wavelength of a high-power direct-diode laser (HPDDL) is very well-absorbed by most metals, and offers superior overall clad quality, reduced heat input, minimal part distortion, and better clad deposition control, resulting in reduced dilution, lower porosity and better surface uniformity than traditional technology. The high quench rate of the direct diode laser cladding process produces a finer grain structure in the clad leading to better corrosion resistance. Finally, the line beam shape of the free-space laser can process large areas rapidly with a high degree of control over clad width and thickness, while also delivering lower operating cost and easier implementation than other methods.
In laser heat treatment or case hardening, a spatially well-defined beam from a HPDDL laser is used to illuminate a work piece. The light causes rapid heating that is highly localized to the illuminated area and does not penetrate very deep into the bulk material. The glass marking bulk heat capacity of the material typically acts as a heat sink for the extraction of heat from the surface, therefore enabling self-quenching. Direct-diode lasers enable rapid processing, precise localized control over case depth/hardness, minimal to no part distortion, superior wear and corrosion resistance, and increased fatigue strength. Part geometry and carbon content (minimum 0.3 percent) significantly influence the results that can be achieved with a laser heat treat process.
Rapid prototyping and additive manufacturing
Rapid prototyping is used in applications where design prototypes or a low volume of complex parts are required to be fabricated quickly without the need of complex tooling. The process is differentiated between stereolithography (SLA) using an epoxy polymer and selective laser melting (SLM) using metal or ceramic powder. In both the SLA and SLM processes, a 3D CAD model is sliced into many layers like a stack of cards, then transferred to the SLA or SLM tool. The laser beam is steered by a galvanometric scanner head and builds up the part layer by layer. After each layer is processed, polymer or powder is then deposited on top of the part and the next laser processing step begins. SLA typically uses a low-power UV wavelength laser to selectively harden a photosensitive epoxy polymer in a bath to form a part. SLM builds up a part from polymer or metal powder by using a sealed-off CO2 laser or a 1-µm fiber laser.
Within the 270 EPIC members, one can find most of the European companies that are actively successful in the field of high-power lasers. The scope of EPIC is to keep communicating to potential users in the automotive, avionics, consumer electronics, medical, jewelry and many other sectors. It is through addressing the unmet needs of those applications that the technology can successfully develop.
Acknowledgments
EPIC wishes to thank the members of EPIC who constantly share their vision and ambitions; in particular, we would like to thank
Donatas Podenas (Light Conversion), Eric Mottay (Amplitude Systemes), Philippe Metivier (Eolite), Alexander Olowinsky (Fraunhofer ILT) and Maurizio Gattiglio (Prima Power Laserdyne). Furthermore, we acknowledge and reference Thomas Pearsall (former director/manager of EPIC) and author of the report “EPIC Laser Market Report 2015, a European Perspective,” and the “Lasers for Materials Processing” brochures by the company Coherent. Please note the article only reflects the opinion of the author and not necessarily each contributor’s individual views.
Meet the author
Jose Pozo is director of technology and innovation at EPIC (European Photonics Industry Consortium). He has 15 years’ background in photonics technology, market knowledge, and a large network within the industrial and academic photonics landscape. Jose is a member of the board of the IEEE Photonics Society Benelux. He holds a Ph.D. in electrical engineering from the University of Bristol in the United Kingdom and a M.Sc. and B.Eng. in telecom engineering.
From Scoring Soup Cans to Engraving Trophies, CO2 and DPSS Lasers Are Proven Workhorses
Lasers are an established tool in converting lines and are widely used in the food industry to score soup, coffee or beverage pouches creating an easy-open function. They are also used to drill foils for vegetable packages, making them breathable. And cigarette strength is controlled through the drilling of cigarette paper. Other applications for lasers are in the medical industry where they are used to cut components like blood testers. Digital printing or production lines also use lasers for kiss cutting of labels and for grinding paper. In most laser converting cases, organics and plastics are the materials being processed, thus making a diamond CO2 laser, emitting a wavelength of 10.2 µm, the ideal laser source.
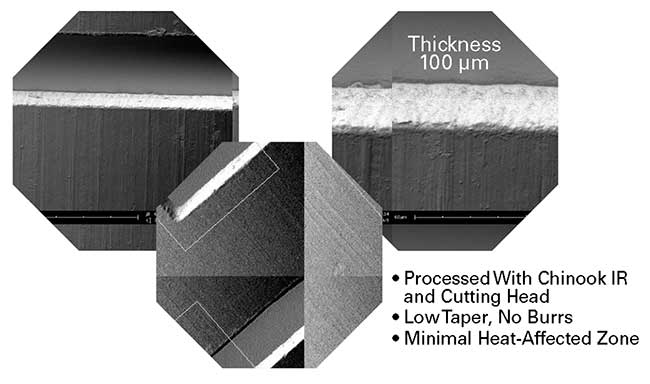
Metal foil laser cutting. Courtesy of Eolite.
Lasers are also commonly used for marking and engraving of materials. There are a wide range of applications found in the automotive, electronics/semiconductor, aerospace, medical, consumer products, gift and trophy, and food/beverage industries. It is a very flexible, basically maintenance-free process, and the results are very precise, creating sustainable marks on a large variety of materials. It is also low in consumable cost. When marking metal surfaces, the high peak power of a 1-µm laser, typically from DPSS lasers, engraves into the metal surface and creates the desired contrast. When marking plastics, the exact color of the mark is highly dependent on the additives found in the plastic. If a high-quality mark with high contrast or color change is required, a 1-µm, 532-nm or 355-nm wavelength laser should be used. A CO2 laser emitting at 10.6-µm wavelength can, in most cases, engrave without color changes based on the melting of the material. Typically a CO2 laser with 10.6 µm is used for marking organic materials like wood, paper, cork, leather and marble, and creates a dark contrast. The CO2 laser also removes paint or discolors fabric effectively. Glass marking is supported by DPSS lasers, as well as excimer lasers, depending on the characteristics of the mark being made inside the glass or etched onto the surface.