White LEDs face design challenges.
Jonathan Wafer, Osram Opto Semiconductors Inc.
LEDs, once considered low-flux optosemiconductors, are now finding use in traditional, everyday lighting applications. Substantial increases in power efficiencies have enabled their use in traffic signals, automotive exterior lighting, signage and other illumination applications. Although years away from making major inroads in general lighting, LEDs do enjoy some compelling advantages compared with traditional filament-based light sources, including reduced power consumption, lower warranty replacement costs, increased operational lifetimes, vivid saturated colors and instant-on convenience. In addition, they are environmentally clean.
Applications that benefit from white LEDs are illumination for the interiors of airplanes, trains and buses, lighting systems for harsh environments, and heavy industrial and military signage.
Design challenges
Of course, as with any technology for specific conditions and applications, LED design presents a unique set of challenges. White LEDs, for example, do not inherently produce a consistent white color point as do traditional white light sources. The generation of white from a single chip-based LED source involves conversion of the blue emission by means of a phosphor powder that is mixed into the encapsulating resin. The dominant wavelength of the blue emitter and its variation in phosphor particle size and distribution generate emissions that create a window within white color space, inclusive of neighboring hues in the blue, violet, green and yellow spectra.
These distributed hues are then sorted, or “binned,” into smaller ranges employed to define customer specifications based on the end user’s requirements and the associated volumetric LED yields for the particular groups. Availability of specific color (or intensity) bins is subject to yield, which often is a moving target, and there can be variations within a single color bin. This makes high yields difficult because most designs require multiple bins.
Luminaire subsystems based on this model will exhibit a noticeable variation from one batch of LEDs to another. This scenario is unacceptable in most direct, and even indirect, lighting applications. The challenge is to develop a bin scheme that reduces the variation within a specific bin or range and to steer the production to predict the device yield.
Chromaticity binning
Upon further review of the old binning ranges, the Y-axis range must be reduced to improve the color consistency within a given bin or group. This is defined by the McAdams ellipsoid theory. Within a given ellipsoid, the human eye cannot see differences in hue or color (Figure 1). Consequently, Osram has developed a revised color-binning scheme based on this theory. With improvements in phosphor particle size and tighter control of resin-blending techniques, it’s been possible to reduce the overall spatial Y-axis range from distribution. Under this methodology, any luminaire assembled with devices from the McAdams ellipse-based scheme will not show discernible color variation.
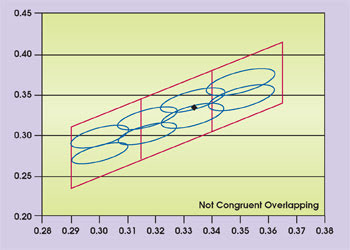
Figure 1. The McAdams ellipses in white color space define the regions of minimal color variation. Red rhombi indicate conventional white binning.
With all of its merits, however, this ellipse-based test scheme does not address the unpredictable yield distribution for white LEDs. Moreover, multiple production lots and excessive testing are required to fulfill customer volume requirements as defined by factory orders. As discussed earlier, the hue or chromaticity of white LEDs is defined by a blue-LED-dominant wavelength component and a phosphor-based size/distribution component. As a result of continuous improvements and refinement in resin/phosphor blending and the optimization of rheological properties and processing, the impact of the phosphor component is reduced. Here the range of dominant wavelength has a direct impact on the area of the phosphor-converted emission, or chromaticity, within white color space.
Custom manufacturing
Production indium gallium nitrite (InGaN) blue wafers exhibit a dominant wavelength spectral bandwidth as high as 25 nm. Thus, white LEDs fabricated in batches with reduced dominant-wavelength dies will produce smaller variations in hue or color. Tighter color binning in mass production allows the manufacture of white LEDs consistent with a McAdams ellipse grouping, but it also enables the production of white LEDs into a prespecified range. The benefit of this is the ability to custom-manufacture in distinct lots, without extensive testing. One of the first high-brightness white LEDs based on this scheme is our white Golden Dragon LED.
High-brightness LEDs are based on 1-mm2 dies assembled in rugged packages capable of high-current operation. Although LEDs are considered cool light sources because of the absence of radiated heat, high-brightness LEDs capable of 25-lumen flux output typically consume more than 1 W. Much of this power is converted to heat that must be removed from the chip junction to enable long LED lifetimes, a key element of the LED advantage in solid-state lighting applications (Figure 2).
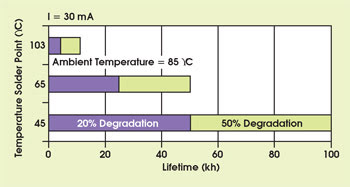
Figure 2. Three scenarios are shown for white LED lifetime as a function of case temperature.
Thermal management
Case temperature control is critical in LED luminaire thermal design and is enhanced by the selection of LED devices with low thermal resistance, thermally dissipative substrate materials and active or passive system cooling methods.
The LED package features a large 1-mm2 chip mounted on a copper slug, which can be soldered to the substrate (Figure 3). In this case, the LED chosen is a true surface-mount device suitable for processing via conventional, industry-accepted, high-volume production techniques.
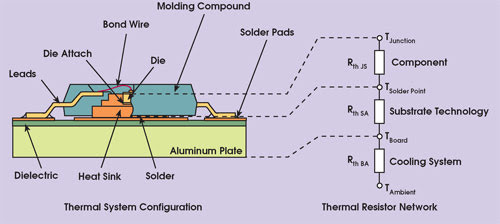
Figure 3. This cross section shows a typical high-brightness 1-W LED and its associated thermal system configuration.
The first postpackage key element of thermal design involves the choice of a suitable substrate material. Factors to be considered in substrate material selection include cost per unit area, thermal conductivity, thickness and processability. Numerous thermal substrate materials are available that feature rigid or flexible laminates typically mounted to aluminum cores (Table 1).
Analysis model
Solder pad design, dimensions and aluminum plate thickness were all standardized for the experiment. The device vehicle-of-choice was the Osram amber Golden Dragon LED normalized to a power dissipation of 1 W. Suppliers fabricated six substrates based on three base configurations: metal core printed circuit board (MCPCB), flex on aluminum and flame-retardant (FR) 4.
The devices were mounted, powered and allowed to stabilize. The LED junction temperature was measured with an infrared camera, and the associated junction to backplane temperature was calculated. It is important to note that the aluminum backplane temperature remained fixed at 25 °C in this exercise (Table 2).
The metal core printed circuit board with thermally conductive dielectric material outperformed all substrate materials in this exercise. However, the FR4 on aluminum with thermal vias will provide the most cost-effective solution. This option is attractive because typical luminaries are basically light-engine modules with no requirement for fine-line or multilayer configurations. Surprisingly, the flex on aluminum with thermal pressure-sensitive adhesive (PSA) is within 20 percent of the performance of metal core printed circuit boards. This provides an attractive option for formable light sources.
The new white chromaticity binning method enables superior color control of white LED-based luminaries. Furthermore, with chromaticity target production, customers can request specific hues. The enhanced color control now paves the way for cost-effective, solid-state fluorescent and incandescent lighting solutions featuring warmer white LEDs and improved color rendering.
Luminaire designs provide a new market for thermally efficient substrate materials once used only in high-end and niche specialty applications. Matched with LEDs based on low thermal resistance, innovative designs are now common. Modular solutions optimized for optical, thermal and electrical performance are a direct result of the convergence of LED light sources and solid-state electronics.
Meet the author
Jonathan Wafer is the visible-LED product marketing manager for Osram Opto Semiconductors in San Jose, Calif.; e-mail: [email protected].