Following completion of a multiyear project, collaborators on an initiative of the German Federal Ministry of Education and Research (BMBF) have reported their demonstration of a production approach they believe will enable large corporations, as well as SMEs (small- and medium-size companies), to additively manufacture individualized components in medium batch sizes economically.
Project IDEA was launched three years ago with the goal of industrializing additive manufacturing for both OEMs and SMEs. The project brought together partners from industry, two Fraunhofer Institutes (Laser Technology ILT and Production Technology IPT), and RWTH Aachen University. As part of the project, the partners built two automated, additive production lines for metal 3D printing with exemplary performance to produce powerful high-end components such as those for gas turbines.
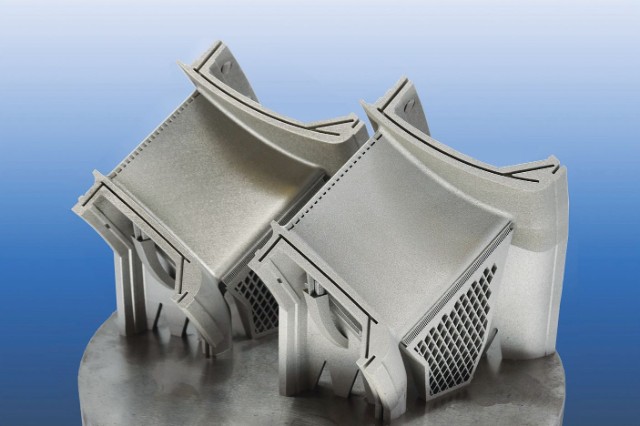
Demonstrator of a turbine guide vane manufactured with continuous-wave (left) and pulsed-wave (right) contour exposure with enhanced detail resolution. Courtesy of Fraunhofer ILT.
The project consortium developed a large-scale industrial pilot production line at the Siemens Energy gas turbine plant in Berlin and a production line for SMEs at toolcraft AG in the municipality of Georgensgmünd.
The digital twin of the factory, developed for SMEs and large-scale series production, was able to significantly reduce product costs even before construction and operation.
Julius Schurb, IDEA project manager, from the Siemens Energy gas turbine plant in Berlin, said, “We were able to demonstrate for our demonstrator component, a turbine guide vane, that the planned reductions in development and throughput times of around 50% can be achieved by taking a holistic view of the production chain from design to finished product. These results will enable us to further advance the industrialization of additive manufacturing and offer key components of our gas turbines at competitive costs, even in small quantities.”
At toolcraft, a medium-size company that uses additive manufacturing processes for series production, the partners reported success in mapping an integrated, end-to-end manufacturing change made up of subprocesses, said Markus Langer, head of Digital Transformation / Technology and Development Promotion at toolcraft.
“Manual work steps were substituted by automation solutions, which helped us achieve higher process stability and quality,” Langer said. “In order to use real data virtually, we also need to highlight digitalization, which must be considered globally for the production of additively manufactured components.
“It was also important, for example, to use VR goggles to transfer analog data, as further developed in IDEA, to digital work plans, to work and test instructions and interactive training. This way we could accompany the employees in the highly complex task environment in the best possible manner.”

The interdisciplinary composition of the IDEA project team brought together experts in turbomachinery, digitalization, automation, aircraft technology, post-processing, laser and 3D printing technology, and other disciplines.
“Since the aerospace industry has very high safety standards, the application of laser beam melting sinks or swims with intensive quality assurance along the process chain,” said Thomas Laag, research associate at Fraunhofer ILT. “Within IDEA, the partners focused particularly on rule-based monitoring of the powder condition, robust process qualification of multilaser machines, and the further development of solutions for automated process monitoring.”
Fraunhofer ILT developed a process control system with pulsed laser radiation for LPBF, a system that can improve the detail resolution and prevent fewer shape deviations. It also reduces the effort required for post-processing and makes it possible, for example, to manufacture complex geometries that have not only greater detail resolution, but also higher combustion efficiency.
In addition, a novel imaging monitoring system was developed and evaluated at Fraunhofer ILT. A high-resolution stereo camera can detect process instabilities such as component distortion or powder bed defects. Since the camera system is mounted on the coater, it can in principle also be retrofitted to existing machines. In cooperation with the partner Jenoptik, Fraunhofer ILT demonstrated an AI-based evaluation of the measurement data.
Despite their different tasks, the two production lines have many things in common. The focus of IDEA was to digitally transform the entire process chain under the heading of digital engineering: Targeted automation, in conjunction with digital twins and modern product control systems, ensured that all relevant production data is recorded and used continuously. In this way, the lines differ significantly from conventional 3D-printing systems since the latter have largely isolated process steps and require many manual interventions, both of which can easily lead to “trial and error” production and high component costs.
“In the field of additive manufacturing, the digital twin is revolutionizing processes along the entire value chain,” said Karsten Heuser, vice president of additive manufacturing at Siemens Digital Industries. “As a virtual image of the additive component, production process, or performance, it enables us to seamlessly link the individual process steps. By using the digital twin, we could consistently increase the efficiency of the two industrial lines, minimize the error rate, and shorten the development cycles.”
A special feature of both production lines is the physical and digital mapping of the additive process chain. This includes automated measurement methods for component geometry monitoring, the additive repair of turbine guide vanes, and the automated finishing of additively manufactured components.