A long-established technology, CO2 lasers are finding new applications in an ever-changing world, making them a capable workhorse for industries worldwide.
Louise May, Rofin-Sinar UK ltd.
Sealed CO2 laser sources are useful in many manufacturing applications — from cutting, drilling, and perforating to marking, engraving, scribing, and welding. They can process a diverse array of materials — including textiles, polymers, rubber, composites, glass, wood, ceramics, and metals — and are used in various industries worldwide.
Robotic laser processing
3D parts are commonplace in a wide range of applications, notably in the automotive industry. Typical materials include metals, plastics, fiberglass, and composites; parts may be painted, coated, or covered with fabric. Products range in size from the smallest interior trim components to large automotive pillars, bumpers, and exterior panels. Mechanical processing methods tend to be inflexible, with tooling too costly to modify. Tool wear may also become an issue, as it causes inconsistent edge condition and high rejection rates.

CO2 lasers are able to process a wide variety of materials, from paper products to textiles. Courtesy of Rofin-Sinar UK Ltd.
To avoid these issues, CO2 lasers are used in conjunction with robot systems. Several processes can be automated in a single robot cell, including using robots to transfer parts in and out. Processing of plastic parts can be optimized by selecting the best laser wavelength for each particular material. Cutting heads are generally used for cutting and trimming, although galvo systems may also be employed for applications that involve ablation or surface texturing.
Laser processing has numerous advantages. Tool wear is eliminated and laser maintenance is infrequently required, aside from routine cleaning operations. Productivity and throughput can be improved, with automated robot cells often performing multiple laser processes. Laser systems produce consistent quality and low rejection rates, and have the flexibility to adapt easily to new designs. Products are thus brought to market more quickly.
Nonmetal process quality
Twenty years ago, sealed CO2 technology enabled lasers to move into the high-precision processing of nonmetallic materials. Today, such lasers have proven themselves to be the ideal tool for automotive interior applications.
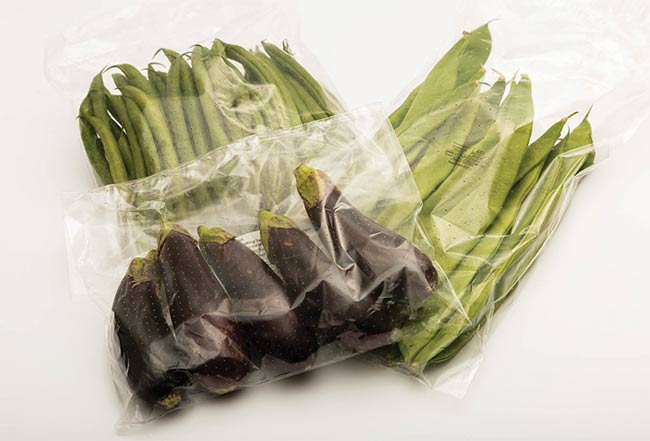
CO2 lasers can perforate holes in packaging to extend the shelf life of vegetables and other foods. Courtesy of Rofin-Sinar UK Ltd.
The noncontact nature of CO2 laser processing eliminates mechanical stress on the workpiece and makes downtime for tool replacement unnecessary. CO2 lasers are effective on a range of materials — including textiles, natural leather, synthetic skins, and plastics — that are all commonplace in automotive interiors. Composite and multilayer materials can also be handled with ease.
Laser processing delivers the tight tolerances demanded by the industry, and the fast rise time of the pulses minimizes the heat-affected zone (HAZ). This, together with the high power-to-size ratio delivered because of the slab principle, provides consistently superior cut quality and production efficiency.
Modified atmosphere packaging
Consumers are buying increasing amounts of prepacked foods that include meats, breads, fruits, and vegetables. Modified atmosphere packaging (MAP) technology ensures that these products remain fresh for as long as possible by regulating the levels of oxygen, carbon dioxide, nitrogen, and other gases inside the packaging. Optimum conditions vary according to product type, along with the mechanism of decay and the respiration rate for each particular product. Packaging must therefore be tailored accordingly.

High-speed laser coding is a reliable means for marking ‘best before’ dates and other information in the beverage industry. Courtesy of Rofin-Sinar UK Ltd.
A CO2 laser can be used to perforate holes at regular intervals across the packaging film. The laser can be integrated into the packaging machinery, where hole size can be monitored continuously and adjusted on the fly. The film is thus perforated accurately and reliably, in accordance with the respiration rate of the produce inside. Laser perforation has been proven to increase the shelf life of certain fruits and vegetables by several days, when compared to unperforated or mechanically perforated films.
Thanks to the laser-processed packaging, the color, taste, and nutrient content in food is preserved. Mold growth is inhibited and the shelf life is increased in a controlled and predictable manner. This means distribution territories can be extended, restocking frequency and associated labor costs are reduced, and waste is cut down dramatically.
Laser coding
As food labeling legislation becomes more stringent, a requirement exists for a fast, flexible means to mark packaging with a multitude of variable information. Information that is unvarying, such as ingredient lists and allergen warnings, is generally incorporated into the printed packaging or label design. However, lot numbers, batch codes, and “best before” dates must be frequently updated as they are applied to each item.

Jeans with special effects — from stonewashing to bleaching — are being produced with the help of CO2 lasers because such technology can do it faster and more
precisely. Courtesy of Rofin-Sinar UK Ltd.
Inkjet coding technology is messy and costly to run, so lasers offer an attractive alternative. Indelible and tamper-proof marks can be applied to a wide range of materials and surfaces, including some where ink would be unsuitable.
Laser coding also makes sound economic sense. After the initial investment to purchase a laser coder, consumable costs are effectively reduced to zero. Laser technology also presents an environmentally sustainable option. Eliminating ink from the process removes risk of chemical contamination for both the product and the environment, and the laser process generates no plastic waste, such as used ink cartridges that must be disposed of.
A laser coder can be integrated in a packing, bottling, or labeling line, as well, to mark products on the fly. The laser mark may be discreet or bold, depending on the nature of the packaging material. For example, a lot number could be engraved discreetly on a plastic container for traceability purposes, without detracting from the product’s appearance, while a “best before” date could be marked with high contrast on a printed cardboard box, where it would be easily visible to the consumer.

Schematic of the inner workings of a CO2 laser. Courtesy of Rofin-Sinar UK Ltd.
The low-maintenance nature and reliability of a laser system minimizes downtime and increases productivity. Laser coding is now commonplace across the food and beverage industry worldwide, appearing in market sectors that include breweries, dairy, cereals, and soft drinks.
High-speed marking
The beverage industry presents a special case that requires a reliable means to mark information on bottles and labels, sometimes at incredibly high speeds.
Beverage marking systems must be able to operate in hostile environments, and must be able to withstand regular washing down to comply with strict hygiene legislation. Marking systems must be able to keep pace with the high-speed conveyers and labelers that operate throughout the brewing and beverage industry today, while still producing high-quality, legible marks.
CO2 laser markers are useful across various sectors of the beverage industry. These highly versatile systems can mark onto a variety of surfaces, including paper labels, plastic bottles, painted metal cans, and hot glass bottles. The CO2 laser marker really comes into its own in the brewery industry, where quality codes must be marked on labels on the fly at extremely high speeds; modern labeling machinery can run at speeds of up to 70,000 bottles per hour (20 bottles per second).
Meat industry laser marking
Many meat products that appear to be served fresh from the grill are actually not grilled at all; such products include chicken, fish, and burgers. Grill cooking would not be practical on a production scale. Instead, meat is usually oven baked and later branded with a crisscross pattern of lines. This creates the impression that the meat has been seared over a hot grill, presenting an attractive product to the consumer.
Grill lines are applied using a system that incorporates a laser and galvo scanner. A 100-W laser is typical and usually sufficient to achieve a high throughput of products. The laser process is cleaner and more efficient than conventional branding techniques. As a noncontact method, the need for frequent cleaning and maintenance of tools is eliminated. As the product is not pressed, moisture is retained in the meat so the product is not only tastier, but more visually appealing.
High yields are possible by integrating laser workstations into an existing production line and locating them downstream from the actual cooking process. Various grill patterns can be implemented with ease, and even text, logos, and graphics can be applied to a wide range of foods. All of this is achieved through simple programming and with no associated tooling costs. Grill marking is extensively used in the fast-food and prepared-food markets worldwide, with laser technology being established as an attractive alternative to mechanical means.
Textile industry
Lasers are increasing in prevalence within the textile industry, where they are often used to apply patterns onto fabric. Clothing manufacturers use lasers to finish jeans with special effects — such as fading, tearing, and patterning — that are fashionable on denim today.
Once again, lasers present an environmentally friendly solution, allowing manufacturers to drastically reduce the use of harsh chemicals and water required by the traditional finishing process. Furthermore, a pair of jeans can be finished every 90 seconds instead of every 20 minutes — a significant advantage for an industry faced with increasing competition and a fast fashion cycle.
By comparison, other surface-altering techniques — stonewashing and bleaching among them — pose problems such as nonreproducible designs, an inability to apply the design to different fabrics, and reduced fabric quality after processing, not to mention the toxic nature of the numerous chemicals used.
CO2 laser finishing systems transfer a grayscale design to the jeans by varying the intensity of the focused laser beam as it scans rapidly across the garment. The laser beam selectively removes pigment from the denim, creating shading without damaging the texture or compromising the strength of the fabric. The same laser can be used to introduce rips, abrasions, and other effects according to the latest fashion.
Compared to traditional solutions, CO2 lasers offer a wide range of benefits. Laser systems enable flexibility and functionality, combined with low maintenance and operational simplicity, and can yield significant improvements in process speed, product quality, running costs, and environmental impact.
Meet the author
Louise May is an applications engineer at Rofin-Sinar UK Ltd. She is responsible for testing and qualifying industrial laser processes in the lab, and has 10 years of experience with CO2 laser applications, preceded by five years in CO2 laser R&D. She studied applied physics at the University of Hull in England, where she received a doctorate in the optical characterization of semiconductors; email: [email protected].