While laser sources and measurement tools are still evolving, photonics solutions are becoming a key driver in accelerating the manufacture of electric vehicle batteries and motors.
JAMES SCHLETT, CONTRIBUTING EDITOR
In 2017, research analysts at UBS Securities disassembled a Chevy Bolt, the world’s first mass-market electric vehicle (EV), and a Volkswagen Golf, Europe’s top-selling internal combustion engine (ICE) car. When the UBS team compared the material compositions of the two vehicles, they unveiled one of the greatest emerging opportunities for photonics technologies in the automotive industry.
Copper’s absorption of blue laser light is several times greater than its absorption of infrared light. Aluminum shows a similar, if smaller, response to blue light. As a result, blue lasers have made significant inroads in manufacturing applications for e-mobility components. Courtesy of Laserline.
The study found the largest deviations in commodity weight shares between the vehicles were seen in aluminum, copper, battery active materials, and rare-earth materials. The Bolt, for example, had
373 lbs of aluminum, which was 74% more than the Golf’s 214 lbs. The Bolt also had 200 lbs of copper, 82% more than the Golf’s 110 lbs.
The electric propulsion of the Bolt, as well as the lightweighting needed to support it, are factors driving the deviations between EV and ICE cars. Copper has become dominant in electric mobility (e-mobility) because it is the second-most conductive metal behind silver. Indeed, 73 lbs of the Bolt’s copper total stem from its battery. Aluminum, meanwhile, is one of the lightest metals, which is critical to maximizing an EV’s range.
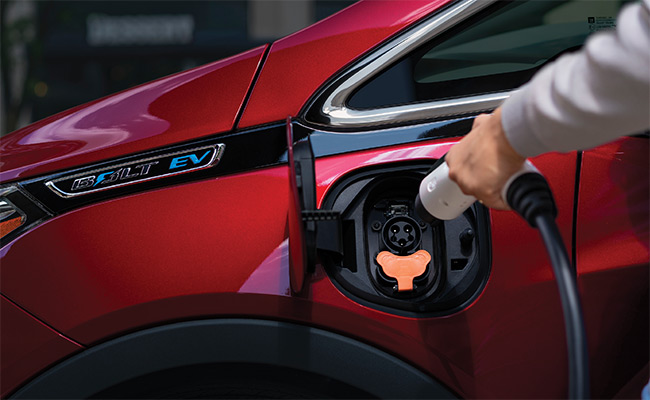
A 2017 study by UBS Securities found that Chevy’s electric Bolt incorporated 200 lbs of copper and 373 lbs of aluminum. In contrast, the Volkswagen Golf relies on an internal combustion engine that incorporates only 110 lbs of copper and 214 lbs of aluminum. The comparative prevalence of these two metals in electric vehicles (EVs) has introduced rich opportunities for laser welding solutions in e-mobility manufacturing. Courtesy of General Motors.
The growing prevalence of copper and aluminum in EVs presents significant opportunities for laser welding, especially for brazing and welding battery packs. Battery cells alone represent the single biggest potential in e-mobility, according
to Jeff Franks, director of strategic marketing for precision manufacturing at laser manufacturer Coherent. However, Ami Spira, marketing manager for Israel-based Civan Lasers, cautioned that lasers will need to overcome problems relating to porosity and spatter, cracks caused by thermal shrinkage, and humping caused by high-speed welding before they are more widely adopted by e-mobility manufacturers.
Part of the issue is that copper and aluminum have higher thermal conductivity and low absorption. These properties lead to low surface tension and viscosity, which causes greater fluidity of the molten pool and keyhole instability, Spira said. Distortions and defects in the final weld can result as a consequence.
Copper welding blues
Around the time that UBS researchers were disassembling the Bolt and the Golf, Laserline, a diode laser manufacturer based in Germany, observed what it considered to be a “paradigm change” in the auto industry. “Some very promising projects in the field of combustion-driven cars were simply dropped and everybody started to look at electrical vehicles,” said Markus Rütering, Laserline’s sales director.
In response, the company launched a new blue laser with a 60-mm milliradians (mrad) at 500 W. Milliradians is an angular measure of how a laser beam’s diameter increases with the distance from its aperture, and it helps to determine the energy density that a laser can focus on a weld. Since the launch of its initial blue laser, Laserline has increased the power capacity of its technology to 2 kW and lowered the beam parameter product (BPP) to 20-mm mrad. Its blue lasers proved viable not only for the welding
of copper to copper but also for the
welding of copper to stainless steel,
copper to nickel-coated steel, and copper to aluminum.
Ytterbium fiber lasers offer stable sources for welding copper using IR light. Courtesy of IPG Photonics
A blue diode laser welds EV battery parts. Blue lasers provide high-speed and spatter-free welding of copper. Courtesy of Laserline.
Blue is an ideal wavelength for
e-mobility welding applications due to its high absorption in the metals commonly used, said Jean-Michel Pelaprat, co-founder and chief marketing and sales
officer of NUBURU. “For instance, copper absorption in the blue is 13× higher than infrared. For aluminum, the absorption difference is 3× better. As a result, blue lasers provide high-speed and spatter-free welding of copper and aluminum. Blue light also solves inherent problems with IR sources, including spatter, defects, and slow speed,” he said.
However, copper’s high absorption, when coupled with its high thermal
conductivity, poses challenges to the ability of blue light to penetrate deep into the material. This can be countered with a more tightly focused beam, but the increased intensity can introduce spatter problems.
Rather than narrow the focus of its blue laser, Laserline favors applying a more moderate energy density on the surface, which makes it possible to weld with lower or even no spatter, Rütering said. The company aims to further increase the output power of its blue lasers, maintain medium spot sizes, and have enough power in reserve to feed power more quickly than it can dissolve into the material. “This will increase the overall process efficiency, [and] we will be able to weld faster,” he said.
Two years after Laserline introduced its blue laser to the e-mobility market, NUBURU introduced its own. In 2019, the Colorado-based manufacturer debuted a 500-W blue semiconductor laser, which was initially designed for fabricating lithium batteries. Since then, according to Pelaprat, NUBURU has introduced several additional laser instruments for welding copper in e-mobility applications beyond the battery, such as in hair-pin stators and power electronic components.
IR lasers
IPG Photonics and its laser automation group, IPG Genesis, in Davenport, Iowa, entered the e-mobility manufacturing market about two years ago with a focus on two technologies. The first involved the use of 1070-nm IR lasers for stable welding of copper and aluminum. The second employed adjustable mode beam lasers for spatter reduction during
welding of electric motor windings,
battery enclosures, and battery modules.
IPG battery welding solutions typically include real-time weld depth measurement to ensure correct penetration into the battery cell terminal, according to Leonid Lev, the senior director of IPG’s materials processing applications.
Adjustable ring mode fiber lasers embed a center beam within a ring beam. The design helps to control spatter during welding operations and improves penetration depth by modulating the two beams independently. Courtesy of Coherent.
Lasers are challenging traditional wire bonding technologies for battery pack connection applications. Wire bonding attaches a copper wire to a cell terminal and bus bar using ultrasound technology. Single-mode fiber lasers delivering power up to 5 kW offer an alternative approach to creating metallurgical bonds between the cells and the bus bar. Multimode fiber lasers delivering up to 6 kW can also be used. Current battery laser welding systems are about 2× faster than wire bonding, with next-generation laser systems providing even greater productivity gains, Lev said.
To make laser welding for e-mobility more cost-effective, IPG Genesis is focusing on beam monitoring, sequential laser welding, improved integration of lasers with automated machines and production lines, and post-weld control techniques. There are challenges to this goal, however, including the emergence of new cell designs, variability in cell manufacturing processes, and the physical limits impeding laser power density, Lev said.
Better beam control
In an effort to counter the spatter and other challenges associated with welding copper using IR sources, Coherent developed its adjustable ring mode (ARM) fiber laser, which embeds a center beam within a ring beam. In addition to controlling spatter, the technology enables better weld preparation through independent modulation of the laser’s two beams.
“The ring beam acts to preheat the
copper, which improves the absorption
of the IR wavelength, enabling the high-brightness center beam to couple into
copper effortlessly,” said Coherent’s Franks. “The ARM technology provides precise and stable penetration depth
control, which is critical for all EV
battery welding applications, including deep keyhole copper welding and thin
foil copper welding.”
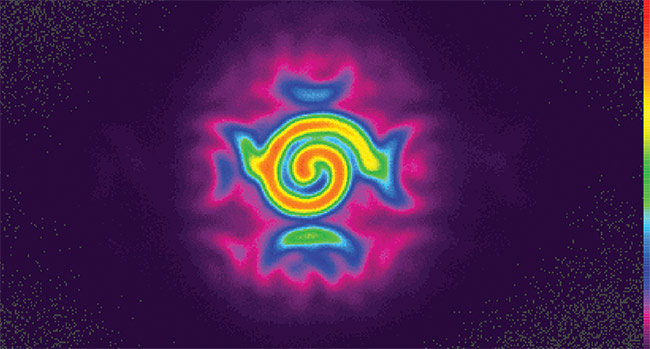
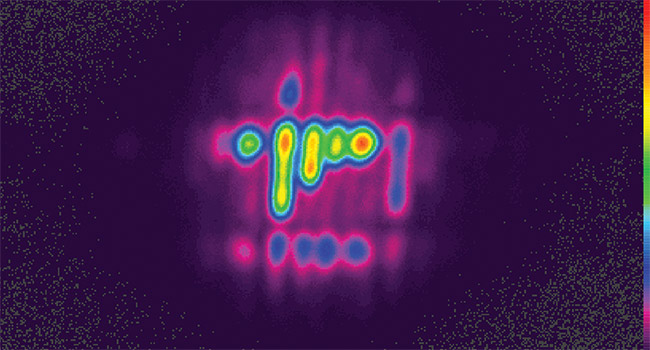
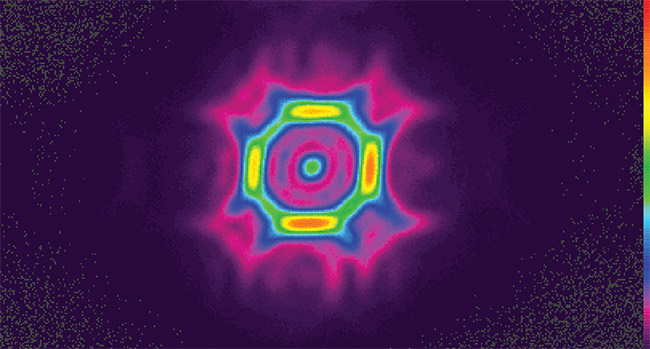
Various configurations that coherent beam combining can achieve for the same laser. The technology allows for coherent recombination of laser emissions, ramping up the output power to a degree unobtainable by in-series amplifiers. Courtesy of Civan Lasers.
Last year, the company launched its CSM-ARM laser that supports a center beam with extremely high brightness (a nominal 0.6 BPP). Designed for welding thin conductive materials, the CSM-ARM instrument has a spot size that is smaller than its multimode counterpart, and it is designed to reduce heating of thin conductive materials, such as copper and aluminum, or foil stacks.
Civan has introduced another promising beam control solution based on coherent beam combining (CBC) and optical phased array (OPA) technology. “CBC is a parallel amplification of a single seed signal, which allows for coherent recombination, ramping the output power to a degree unobtainable by in-series amplifiers,” Civan’s Spira said. By individually regulating the phase of a 2D output array, OPA supports arbitrary beam shaping, live beam correction, and focus steering.
The CBC-OPA combination results in a high level of beam control, including an easily designed beam shape, frequency regulations from 400 Hz to 50 MHz, shape sequencing, and the ability to shift the single-mode beam’s large depth of focus to up to 50 MHz.
This type of dynamic beam technology is suitable for the overlap welding applied to the manufacture of battery coolers. Brazing is currently utilized for overlap welding, but larger components are affecting costs and creating an opportunity for coherent beam combining. Civan’s technology could also be beneficial when welding copper at depths greater than
1 mm using green and blue lasers. “The dynamic beam could improve welds by combining high powers with beam shaping,” Spira said. “This combination could reach deep penetration with improved melt pool control.”
A further opportunity for Civan’s technology involves the welding of parts coated by materials that protect electrical components against corrosion and moisture. The controlled intermetallic mixing enabled by the dynamic beam allows manufacturers to skip the step of having to remove the coating before welding.
Before coherent beam combining
technology is more widely adopted by
e-mobility manufacturers, further advancements in simulations and monitoring will be crucial, Spira said. Simulations would reduce process development time, and real-time monitoring would enable users to change the laser’s param-eters during welding, as the laser can be controlled in megahertz frequencies. “This can revolutionize the way we weld,” he said.
Civan recently formed partnerships with Bosch — to develop automotive dynamic laser processes for e-mobility — and with BBW Lasertechnik to further develop Civan laser technology for the welding of copper and aluminum for
e-mobility applications.
Monitoring the beam
E-mobility manufacturing applications often require the welding of highly reflective and/or dissimilar materials, a requirement that is also creating opportunities for laser beam measurement providers, such as Ophir-Spiricon.
“The power density range required to join these materials is tighter than with other materials,” said John McCauley, Ophir’s business development manager. “This is why automotive manufacturers are taking a closer look at beam diagnostics products: to better ensure that their lasers are performing consistently over time.”
The shift of a laser beam’s focused spot from its designated position, for example, can result in a loss of weld penetration due to the slight increase in beam size. This can be avoided by laser monitoring systems designed to track such shifts.
McCauley said the debate over which laser wavelengths are best suited for welding copper battery components has put Ophir at something of a crossroads: Should the company enhance its current products that are designed to measure IR lasers, or instead focus on accommodating green and blue laser solutions?
Ophir decided to do both. In 2019, the company combined its laser power measurement product with Spiricon’s BeamWatch product, which can capture and analyze a multikilowatt laser beam’s caustic in real-time images. Ophir’s BeamWatch Integrated product provides operators of NIR lasers that emit between 980 and 1100 nm with a comprehensive periodic check of the overall health of their system so that consistent processing can be achieved, McCauley said.
Beyond batteries
While welding and brazing applications for battery packs hold the greatest potential for photonic solutions, laser makers also see opportunities to solve processing issues for other EV parts. One example is the welding of hairpin-shaped stators that form the core of an EV’s motor. More specifically, Laserline sees potential for laser welding solutions targeting hairpins with a high cross section (for example, 8 sq mm per pin). The company does not currently offer a blue diode laser for this application but believes that such a solution could be achieved by a system able to deliver 3 to 4 kW of output, Rütering said. Blue lasers could also play a greater role in connecting thinner wires in a variety of electric motors beyond EVs, such as automotive windshield wipers, power windows, sunroofs, and seats.
Civan’s Spira similarly sees potential for lasers in hairpin welding. Hairpin parts are made of a coated copper. The coating is partially removed before welding the hairpins together. If improved laser control could help weld coated contacts, it would eliminate the additional step of coating removal. Civan’s beam steering technology could also help to
accommodate processes in which the
target weld location might shift from hairpin to hairpin.
Franks said, “The entire e-powertrain beyond the battery pack could be described as relatively underserviced.” Though he is less optimistic about the immediate opportunities in traction motor applications versus other e-powertrain components, he said many tier one automotive suppliers have been retooling their traction motor technologies for e-mobility platforms. However, these retooled motor opportunities are developing quickly, and not all of the new configurations lend themselves to laser welding, he said. Other e-powertrain components — such as power control units, the battery management systems, and inverters — will meanwhile require new lightweighting solutions, to which laser welding could definitely contribute.
Beyond batteries, IPG Genesis’s Lev sees laser welding of stator hairpin windings as rapidly becoming the standard approach, displacing alternatives such as micro-TIG (tungsten inert gas) welding. He said the next untapped opportunities for laser solutions in e-mobility are stator lamination, cutting, and welding.