Emerging dynamic beam-shaping technology is enhancing the flexibility and precision of lasers used in macromachining, high-kilowatt welding, and cutting applications.
EYAL SHEKEL, Civan Lasers
Automotive electrification is just one of the major trends redefining the requirements for high-volume materials processing in precision manufacturing. From the need to align and connect battery layers, to the expanding deployment of additive metal manufacturing, to the adoption of new metal-alloy-based cooling systems,
manufacturers are searching for the
tools that will help them keep up with demand.
This search helps to explain why
manufacturers are increasingly replacing
traditional mechanical machining and thermal welding systems with laser processing tools. Compared to traditional thermal welding processes, laser-based techniques require less heat input due to the beam’s high energy. Laser welding also minimizes the potential for distortion, while maximizing throughput.
All welding methods involve melt-pool formation and subsequent rapid solidification, which alters the properties and the microstructure of the welded metal. The high energy of laser welding, however, not only melts the material but also evaporates it1. Evaporation during the welding process creates a vapor capillary
in the material. This keyhole, as it is
commonly called, gives laser welding
the advantage of a very high aspect ratio, defined as a high ratio of penetration depth to weld seam width.
Compared to thermal welding methods, which generally provide wider and shallower weld seams, laser welding’s high aspect ratio translates into potentially lower part distortion. The keyhole, however, can also pose challenges,
since its stability is crucial for achieving high weld quality. When welding high-absorption materials such as steel and nickel, the keyhole generally remains
stable and enables laser welding to achieve superior results. However, when welding copper, aluminum, and high-alloyed materials, the keyhole can be inherently unstable, making the process susceptible to irregularities such as
pores and spatter that compromise weld quality.
Beam-shaping approaches fall into three broad categories: static, variable, and dynamic.
Despite these challenges, automotive manufacturers working to electrify their products are increasingly turning to new laser-based materials processing tools to weld, cut, combine, and process complex products with advanced specifications. Laser technology has enabled the industry to keep pace with production throughput as part of an overall, cost-effective
solution (Figure 1). While cost reductions
derive in part from the increased power that laser welding tools deliver, application of this power imposes some additional considerations for manufacturers. Specifically, as laser power increases, it becomes increasingly critical to tailor process parameters to the application to maintain stability of the keyhole as well as the microstructure of the joint being welded.
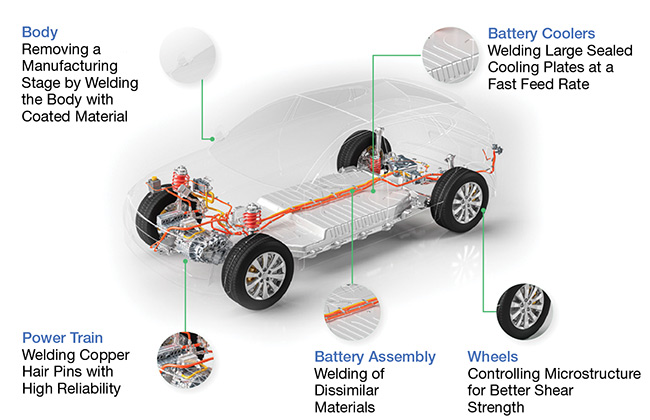
Figure 1. Automotive e-mobility presents several new manufacturing and joining challenges. In addition to introducing entirely new components and systems, e-mobility has also expanded the use of copper and aluminum materials in electric vehicles. Laser welding instruments have enabled the industry to keep pace with e-mobility production costs and throughput, but these tools would benefit from greater flexibility and control of the beam. Courtesy of Civan Lasers.
Maintaining keyhole stability
Manufacturers can tailor laser process parameters such as wavelength, pulse energy, pulse duration, repetition rate, and feed rate, as well as the shape, size, and intensity of the laser beam spot. Common materials processing techniques applied today include wobble welding with a fast scanner, the use of laser sources emitting at green or blue wavelengths, or the use of a variable superimposed intensity distribution with a two-in-one dual-core fiber2.
Beam-shaping approaches fall into three broad categories: static, variable, and dynamic. Diffractive optical elements provide cost-effective beam shaping by emitting a thin pattern on a robust window, which diffracts and modulates the phase of the light passing through it2. For static beam shaping, a variety of diffractive optical elements is available to tailor the laser beam output at the workpiece. The problem with static solutions, however, is that they are only suitable options when the manufacturer has very well-defined process parameters that do not require process flexibility.
Diffractive optical elements can also increase laser flexibility by using adjustable ring shapers that split the beam into
a central spike, or core beam, and a
surrounding ring beam. This option requires a single axis shift or rotation to change the ratio intensity between the core and ring beams. While such beam-shaping solutions can improve the flexibility of a given process by enabling a single machine to carry out specialized tasks in serial production, for instance, they cannot adequately support the frequently changing operations that constitute the daily business of industry3.
Dynamic beam-shaping methods
To give manufacturers the tools they want and need, and thereby expand the market for laser materials processing, researchers have pursued dynamic beam shaping for decades4. There are currently four approaches to dynamically shaping laser beams. They involve galvanometer scanners, piezo-driven actuators, microelectromechanical systems (MEMS)-based scanners, or optical phased arrays. Galvanometer scanners are available from many suppliers today and deployed across industry. They can be used to oscillate the output from single-mode fiber lasers in the pattern of a circle or a figure eight during the welding process.
Piezo-driven actuators offer a third axis of control to galvanometer scanners
by shifting the focal distance of the laser beam. This technology is currently transitioning from the research arena into real-world industrial applications. MEMS-based scanners, meanwhile, offer dynamic beam-shaping options for low-power applications. Ensuring the stability of MEMS-based scanners in high-power applications, such as continuous welding processes, remains a challenge that has yet to be overcome.
None of these beam-shaping solutions offers a complete solution, which makes it impossible for manufacturers to optimize the cost and productivity of lasers in e-mobility applications. While diffractive optical elements can change the shape of a laser beam, once a new shape is designed and implemented, it cannot be altered on the fly. Additionally, mechanical scanners can solve keyhole instability issues, but they are limited by the maximum speed and power at which they are designed to operate.
Enter coherent beam combining
The reality is that the beam-shaping methods discussed have not allowed laser technology to reach its full potential in materials processing applications. The key problems are the inflexibility of these methods and their speed limitations when modulating beam shape.
Optical phased arrays offer an alternative and potentially more effective solution. Phased arrays are a type of coherent beam-combining technology that merges many single-mode laser beams into one larger beam. Each laser emits its own light, which overlaps with other beams in the far field to create a diffraction pattern (Figure 2). This process unlocks the flexibility to easily manipulate the beam shape in real time to create a dynamic beam laser.
Figure 2. An optical phased array, a type of coherent beam-combining technology that merges many single-mode laser beams into one larger beam. Each laser emits its own light, which overlaps with other beams in the far field to create a diffraction pattern. This allows manipulation of the laser beam’s shape to create a dynamic beam laser. Courtesy of Civan Lasers.
During dynamic beam laser operation, the beam from a single-seed fiber laser divides and passes through a parallel array of electro-optical phase modulators, each of them driving an optical amplifier (Figure 3). Proprietary control technology from companies such as Civan Lasers combines these multiple single-mode beams into a narrow, high-power single-mode beam delivering maximum power density.
Figure 3. During a dynamic beam laser’s operation, the beam from a single-seed fiber laser divides and passes through a parallel array of electro-optical phase modulators, each driving an optical amplifier. Courtesy of Civan Lasers.
This solid-state approach to beam combining and control works like a phased array radar with no moving parts. The phased array directs the radar beam by differentially activating each small antenna within the array. Similarly, in the dynamic beam laser, each of the parallel lasers produces overlapping cones of light.
Differences across each cone’s spot produce a slight phase shift. And between individual laser cones, there are areas in and out of phase, respectively producing constructive and destructive interference. Using the phase modulators to control individual beams results in an interference pattern that can be changed to maximize the beam spot position to inscribe various shapes and patterns based on the beam’s motion. All of this can be performed at speeds up to hundreds of megahertz.
Another advantage that dynamic beam shaping offers is the ability to change the laser’s focal point. Not only does adjusting phase interactions move the beam in a flat xy-plane, but it can also change the beam’s focus in the vertical direction. This maximizes spot energy at various depths, which is beneficial when penetrating thick materials or layers during cutting or welding operations.
Dynamic beam shaping
This optical phased array-enabled dynamic beam-shaping technology enables fiber laser sources that are capable of delivering up to 100 kW of power with a level of control that multimode lasers lack. Recent developments further add the ability to control not only the beam shape but also the shape sequence, frequency, and focal depth as well. Adjusting these four parameters allows for unprecedented laser welding process optimization by managing the melt pool in ways that meet or exceed throughput and that enhance quality parameters for older materials processing technologies, such as brazing alloyed parts.
As discussed earlier, the shape of a laser beam has a direct effect on the ma-terial being processed. Different shapes can achieve specific weld geometries and microstructures. The beam shape required depends on the desired result, and often small adjustments can make a big difference. Existing beam-shaping solutions do not offer the flexibility to choose a wide range of shapes, let alone the ability to design any shape needed (Figure 4).
Figure 4. Dynamic beam lasers allow users to quickly optimize different welding processes by testing multiple setups to determine the influence of beam shapes on weld geometry. Small adjustments in shape can often make a big difference, although, until recently, most beam-shaping solutions offered limited options and no ability to actively design beam shape. The ability to shape a laser beam that can achieve specific weld geometries and microstructures depends on the desired result. SS: stainless steel. Courtesy of Civan Lasers.
In contrast, emerging dynamic beam laser solutions are accompanied by software that empowers users to design beam shapes that are relevant to an application, upload the design to the laser system, and then observe the effect on the weld using cross-section analysis — all within a relatively brief period. The simplicity and speed of this process makes it possible to evaluate multiple shapes and choose the optimal shape for a specific weld. Soon, further advancements will enable real-time monitoring and control of beam shape, allowing on-the-fly optimization of the beam (Figure 5).
Figure 5. Emerging dynamic beam lasers are accompanied by software that allows users to design beam shapes that are optimized for their welding application. By clicking on a software interface grid, for example, users can set up a postulated beam shape and sequence to easily evaluate different shapes to find the optimal shape for a specific weld. Courtesy of Civan Lasers.
Frequency, sequencing, and steering
Once the desired beam shape is designed, the speed at which the laser creates the shape can be set. The time it takes to create a shape is called shape frequency, and it can affect weld characteristics because a less-than-optimal speed can cause defects such as spatter. Fast frequencies — for example, 50 MHz — are so fast that shapes behave as a quasi-static shape that produces a completely different result than would be created at a frequency in the kilohertz or hertz range.
As with beam shaping, the frequency can be easily changed to determine what works best for the needs of the material being processed. In some cases, a difference in frequency may be the only change needed to drastically improve a weld.
Beam sequencing adds another layer of flexibility to laser welding processes by providing the ability to switch between beam shapes within a microsecond. Beam sequencing creates a series of different shapes, each with a specific processing goal, to achieve several desired results. The laser can be programmed to run through each shape successively, at different speeds, and at set intervals. For
example, if one shape stabilizes the keyhole and avoids sputter while a different shape avoids cracking, then a well-designed sequence of these two shapes can achieve both goals in a single pass of the laser.
Beam-sequencing programs also enable the laser to change from one beam shape to the next as the beam moves through the stacked material layers to process different materials, such as a coating and substrate. In this way, the process can be tailored for each layer.
Standard lasers have a short depth of focus that results in inconsistent weld depths in the workpiece. Single-mode lasers have a larger depth of focus, and dynamic beam lasers are single-mode
lasers that can also steer focus. This means the focal position on the z-axis can be changed within the material at any time and at any speed during the process.
Lasers that apply a constant focus throughout the welding process produce vastly different and more jagged results than those that are able to steer the focus of the beam. Focus steering creates a much smoother, stronger, and more consistent weld.
Putting it all together
The advantages of dynamic beam lasers can be leveraged in many ways to speed up and improve output in industrial applications. A narrow Gaussian beam offering greater control over focus depth, for example, allows the laser to weld and cut at angles other than the strictly vertical plane, even if the laser is positioned close to the workpiece. Conversely, there are potential benefits to working from a large distance and using a mirror to move the beam over an object or a surface.
The ability to move the beam and its focus point at speeds of up to hundreds of megahertz enables tracing various beam-shape patterns over the workpiece to distribute energy as needed for a multitude of applications. For example, when welding two pieces with a gap between them, a high-power-density narrow beam can quickly inscribe a large shape across the gap to achieve a solid joint.
During welding operations, dynamic beam shaping controls the melt pool of the material and the hot plasma keyhole in the pool. As the beam moves down the weld line, material goes from solid to liquid to gas and then reverses. By precisely controlling the melt pool and reducing collateral splattering, resolidification
occurs in the desired phase of the material, resulting in a high-quality weld.
Such beam control allows the welding of dissimilar materials, such as aluminum and copper, that vary in reflectivity, heat capacity, and melting point. Beam control further allows lasers to join together crack-sensitive materials or to supply the precise amount of energy where needed to tack a thin wire to a bulk material. When penetrating several layers of different materials in drilling applications, the ability to quickly sequence successive beam shapes tailored to each layer within microseconds will produce a more uniform hole.
Dynamic beam laser technology allows
users to take advantage of powerful laser tools while avoiding some of these tools’ inherent rigidities. Dynamic beam laser systems offer the flexibility to adjust beam shape and frequency quickly and easily, as well as to create beam sequences and steer the focus of the beam — all of which make dynamic beam lasers a potential game changer in materials processing (Figure 6).
Figure 6. The ability of dynamic beam lasers to design an optimal sequence of beam shapes offers an effective tool to avoid humping — the periodic occurrence of bead-like protuberances — when welding 1-mm-thick aluminum 5052. Courtesy of Civan Lasers.
Meet the author
Eyal Shekel, Ph.D., is founder and CEO of Civan Lasers. He earned a doctorate in physics from New York University and a Bachelor of Science degree in electro-optics from Jerusalem College of Technology; email: [email protected].
References
1. P. Ferro et al. (2018). A review on melt-pool characteristics in laser welding of metals. Adv Top Mater Sci Eng, ISSN 1687-8434, www.doi.org/10.1155/2018/4920718.
2. E. Punzel et al. (2020). Comparison of different system technologies for continuous-wave laser beam welding of copper. Procedia CIRP, Vol. 94, pp. 587-591, ISSN 2212-8271, www.doi.org/10.1016/j.procir.2020.09.081.
3. C. Goppold et al. (May 2017). Dynamic beam shaping improves laser cutting of thick steel plates, www.photonics.com/articles/dynamic_beam_shaping_improves_laser_cutting_of/a62070.
4. D.D. Leavitt (June 1990). Dynamic beam shaping. Med Dosim, Vol. 15, No. 2, pp. 47-50, www.doi.org/10.1016/0958-3947(90)90033-e.