Laser Machining Drives Improvements in Medical Devices
Lynn Savage, Features Editor, lynn.savage@photonics.com
Increasingly, the medical devices used
to support good health and provide emergency and long-term care are not being designed
to sit on a rack or table next to a patient’s hospital bed. Instead, they
are being made small and light enough to be clipped onto clothing, to be worn like
a bracelet or badge, or to be implanted directly into the body. Ultimately, the
aim of medical device design is to provide doctors and nurses with better tools
that are always within reach, to improve the overall health of patients with treatments
that have fewer side effects, and to keep people out of hospitals altogether, thus
reducing health care costs.
Some of the most common medical devices today are sensors that
detect and read out biometrics such as blood pressure or sugar/insulin response
and implants such as stents for helping keep open clogged or damaged arteries or
tissues.
Once upon a time, medical device manufacturing consisted mostly
of stamping sheet metal and pouring molten metal into molds. This type of manufacturing
has not gone away, but it is being supplanted by new techniques – such as
laser-based machining – that promise to achieve two chief goals: reducing
the size of the apparatuses and increasing the use of novel materials inside them.
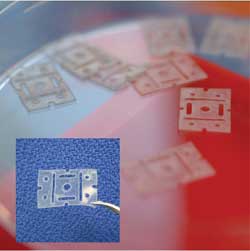
A wide variety of lasers are available to manufacturers, meaning that materials ranging
from 1/4-inch sheet metal to thin-film polymers can be processed to precise tolerances.
Courtesy of Laser Micromachining Ltd.
Efforts are under way to design sensors that can closely track
health-related patient biochemistry and the effectiveness of pharmaceuticals and
other treatments. Similarly, stents, novel artificial bone and other tissues, and
inserts such as catheters and artificial retinas are continuously being redesigned.
To make these sensors and inserts smaller, stronger and more effective, materials
such as the shape-memory titanium-nickel are being tested and used. Manufacturers
are finding that lasers can effectively work a wide variety of novel materials.
Contract manufacturers such as Resonetics LLC of Nashua, N.H.,
work with a multitude of materials, including polymers, glass, ceramics and ultrathin
sheets of metals and alloys. They drill, cut, scribe and mark tiny device components
and turn them into catheters, stents, dental implants and biosensors that help track
diabetes and heart health. A relatively simple catheter once took weeks of tooling
by hand or with large industrial machines, but now it can be created in a fraction
of the time, using lasers to prepare the major components and finish the final product.
According to Nadeem Rizvi, co-founder and managing director of
Laser Micromachining Ltd. in St. Asaph, UK, polymers and thin metals are the core
materials used in most medical devices, but they don’t paint the whole picture.
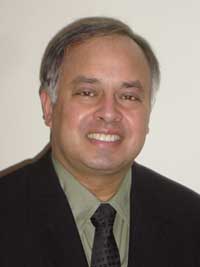
“The standard requirements of high quality, high tolerances and repeatable results have
not changed and are not likely to.” Nadeem Rizvi, Laser Micromachining Ltd.
“There seems to be a trend toward thinner materials with
finer features and also a growing demand for devices with precision structures in
combinations of materials (e.g., polymers on glass or thin coatings on different
base materials),” he said. “There is also quite a lot of interest in
completely new materials, such as biodegradable polymers for implants and tissue-engineering
applications.”
Drill, laser, drill
Among the multitude of steps that comprise medical device manufacturing,
the key ones are forming the basic shape of each part; drilling or punching holes,
notches and other shapes where needed; attaching the parts together; and marking
all or some of the parts for later identification. Where large mechanical presses
once were used to stamp out shapes from 1/4-in. sheet metal like a cookie cutter,
lasers now can cut and trim ultrathin sheets of metals and polymers to very close
tolerance. The difference between techniques has enabled metal tubes to shrink to
such a small size that stents are now ubiquitously used in patients’ arteries,
ureters or similar tubular structures.
Similarly, laser-based welding, ablating and structuring, and
marking or scribing all take the place of traditional manufacturing methods, while
improving the form and function of the final product.
Drilling might be the most common manufacturing step improved
upon by laser machining. Tiny holes in many medical appliances – for example,
the via holes that transport fluids from one chamber to another in a portable sample
analyzer – can be made microns in diameter and millimeters long. Traditional
drilling techniques cannot match the performance of lasers in this regard.
Sintering, a process in which a material in powdered form is shaped
and turned into a solid part via applied external heat, also is being matched up
with lasers. Laser sintering, the 3-D equivalent of 2-D laser printing, can create
medical components of very tiny size to very small tolerances.
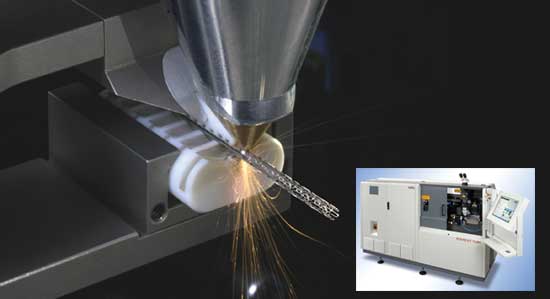
Systems such as Rofin-Baasel’s
Starcut Tube (inset) are used to manufacture precision-cut parts, including slender
cylinders for stents and catheters. Courtesy of Rofin-Baasel.
“Lasers are quite a flexible tool, especially compared with
stamping and other manufacturing technologies,” said Dieter Mairhörmann,
international sales manager (medico) for Rofin-Baasel of Starnberg, Germany. “Fiber
lasers and CO2 lasers are common for sintering.”
Prototyping
Besides fulfilling the steps required for manufacturing mass quantities,
the other major service offered by laser micromachining companies is rapid prototyping
– the creation of model components (or whole devices) in time frames typically
shy of a week. This service offers the ability to audition several design options
for a single device idea without large expenditures of either time or cash. Designing
and building prototype medical devices previously took much longer, discouraging
the pursuit of either big new ideas or subtle design tweaks.
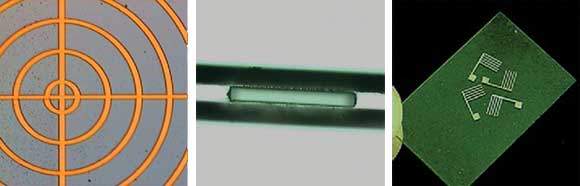
Laser-based manufacturing can perform nearly all of the tasks required
to build medical devices, including drilling, structuring, cutting, trimming and
marking. Courtesy of Laser Micromachining Ltd.
“One of the main benefits of using laser machining for product
development,” Laser Micromachining’s Rizvi said, “is that different
design ideas can be tried quickly and the results used to develop the most effective
product solution.”
Norman Noble Inc. of Highland Heights, Ohio, is one of several
companies that offer prototyping services, working with materials ranging from nitinol
to thin metals to bioabsorbable polymers. Companies such as Norman Noble and Laser
Micromachining provide the manufacturing prowess, while laser makers provide the
base technology.
Mairhörmann said that implant makers and other medical technology
clients are fairly knowledgeable about lasers because they know the parameters required.
The manufacturers’ customers – the device designers – are, on
the whole, still catching up with the possibilities of laser machining for both
prototyping and mass production.
“Clients who are not so aware of laser technology nonetheless
are very quick to appreciate the benefits of laser machining, once they see how
it can help their businesses quickly and cost-effectively,” Rizvi said. “Still,
from time to time, we will get an inquiry about drilling a 1-µm-diameter hole through
10 mm of metal, and we have to explain that lasers can’t do everything.”
Next up
Despite the learning curve that some device designers still must
experience, laser machining equipment and services are largely commoditized. No
sea changes are expected. Rapid prototyping services likely will increase, especially
as new powderized base materials are developed. Rizvi and others believe that sintering
and structuring – using lasers to shape or deposit materials into 3-D parts
– also will gather steam. Increasingly, innovations will be coming from startups
and other small, nimble companies.
According to Terry Young, Julie Eatock and Dorian Dixon in a recent
article in the Journal of Manufacturing Technology Management (Vol. 20, Issue 2,
pp. 218-234), the majority of innovative, new-to-the-world medical devices are being
developed by small companies. To the authors, large, more established companies
seem complacent, spending their energies on incremental upgrades to existing devices.
And these derivative products are less likely to exceed expectations of success
than are novel items.
Technological improvements likely will be incremental, especially
concerning lasers themselves. The use of fiber lasers likely will continue to increase,
while wavelengths will shrink further into the ultraviolet as customer demand for
finer, smoother features increases. Because shorter laser pulses mean that less
heat is transferred to the material, femtosecond lasers will get a close look as
successors to picosecond systems.
In all, the growing demand for better and more widely available
health care in the US and globally will drive the design and manufacture of small
devices that preserve, protect and monitor the health of nearly everyone. Those
who make lasers and those who use them to make medical devices have a long road
of success ahead of them.
/Buyers_Guide/Resonetics_LLC/c12724