As the power of laboratory lasers has increased, aspheric lenses and mirrors have been pushed to deliver exceptionally high intensities.
ARIS KOURIS, OPTICAL SURFACES LTD.
Editor’s note: This is Part 2 of a two-part feature on optics for nuclear research. Part 1 appeared in the September issue and looked at high-power laser facilities and the critical role of aspheric optics in these demanding conditions. Part 2 discusses the technical requirements
and manufacturing challenges of mirrors and lenses in nuclear and other facilities that use high-power lasers. Coatings and materials choices are also addressed.
The challenges of manufacturing a steep, off-axis parabolic (OAP)
mirror are immense. A direct measure of the degree of difficulty in its manufacture is asphericity. Asphericity is a function of the mirror as a whole and depends on the assumed focal length,
off-axis distance, and diameter, compared to a “best-fit sphere.” Generally, OAP
mirrors that display an asphericity of
1 mm or more, which also maintain other high-quality specifications, are considered exceptionally difficult to produce. Key measured specifications include surface accuracy (effectively wavefront error), slope errors, and surface quality (scratch/dig).
For most applications, asphericities are well below 1 mm, and the desired specifications are limited to a good surface accuracy (typically λ/10 P-V at 633 nm). For these less demanding applications, the surface quality of an OAP mirror often serves a cosmetic need, and slope errors will rarely need to be specified because they generally do not affect overall performance.
However, in the case of high-power laser applications, where the intention is to push barriers and deliver a well-defined, intensely focused beam, the
OAP mirror must be fast, and asphericity may be significantly higher than 1 mm.
Consequently, the surface accuracy,
slope errors, and surface quality must
be maintained at the very highest standards.
High asphericity ensures that the focused laser spot will be only a few microns in diameter. Mirrors that demonstrate excellent surface accuracy — having been appropriately mounted and aligned — ensure that a tightly contained, focused spot is achieved. Small slope errors on OAP mirrors hold the spread of light to an absolute minimum around the beam, which is critical as even a tiny local field perturbation may disturb the extraordinary balances necessary during nuclear capsule compression.
In addition, a good mirror surface quality reduces the possibility of coating damage caused by diffraction effects
that are due to fine scratches or digs on the surface. Because of the high intensity and coherence of the light used and the potential for constructive interference that could take place, such effects would increase the chances of local hot spots manifesting in the vicinity of defects.
Performance factors compete with each other during the manufacturing process, and achieving all three factors simultaneously is — especially for a highly aspheric mirror — a demanding challenge. An analysis demonstrates how
rapidly the asphericity (and edge asphericity slopes) grow in an OAP mirror of a given aperture as the focal length decreases (Figure 1).
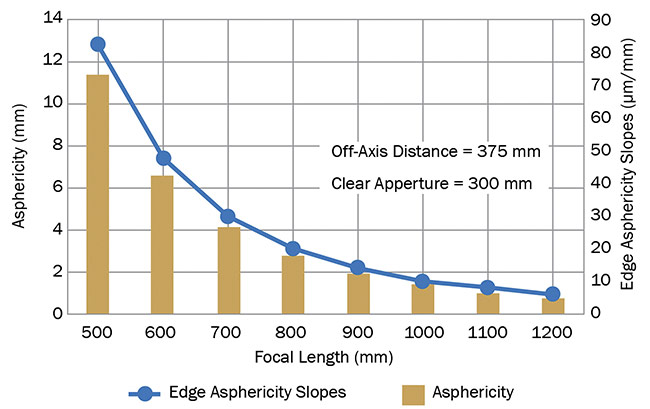
Figure 1. OAP asphericity and edge slopes increase dramatically as focal length decreases. Courtesy of Optical Surfaces Ltd.
If, for example, an OAP mirror with
a focal length of 700 mm is used, its
corresponding asphericity will be in
excess of 4 mm, with rapidly growing slopes as the edges farthest from the optical axis are approached. To improve overall surface accuracy and mirror shape with traditional lap polishing, smaller and smaller tools are necessary. Small tools allow effective work through the rapidly changing slopes, but, during this process, strong local imprints (slope errors) are generated that can only be removed with the use of larger tools. The necessary exchange between small and large tools creates a strong competition between the continuous improvements of either of the two desired parameters. Furthermore, the requirement to keep the surface virtually free of scratches or digs means the risk of prolonged production time significantly increases. The removal of such defects could compromise or even ruin the shape and smoothness of the surface, which
can translate into lost production time
of days or even weeks.
Microroughness
Microroughness is another critical quality factor in OAP mirror production that must be considered and controlled.
It concerns features even smaller than slope errors and is often expressed in root mean square (rms) terms after integrating over spatial periods, usually less than
0.25 mm. Such features, when pronounced, tend to create effects similar
to mild scattering.
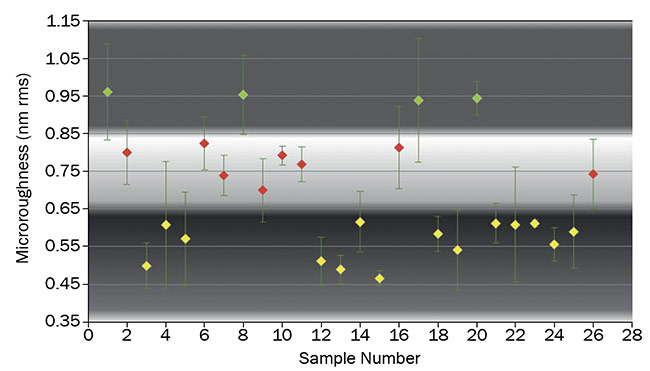
Figure 2. Microroughness distribution using pitch polishing. Note: Color bands help with visibility and assist with conceptual dividers between clusters. Courtesy of Optical Surfaces Ltd. Courtesy of Optical Surfaces Ltd.
Although it is not well understood how microroughness can be intentionally controlled during manufacturing, the pitch-polishing technique has been found to produce very good results that consistently do not exceed 1 nm rms. From data collected on OAP mirrors, it can be postulated that some of the higher microroughness values close to the 1 nm rms mark may relate to higher asphericity.
When looking at microroughness data, a correlation to material chosen for the OAP mirror substrate has not been found. A randomly selected distribution of several microroughness measurements performed on a selection of precision optics has been produced over the past few years (Figure 2). A typical surface map measurement obtained using white light interferometry (WLI) is shown for comparison (Figure 3).
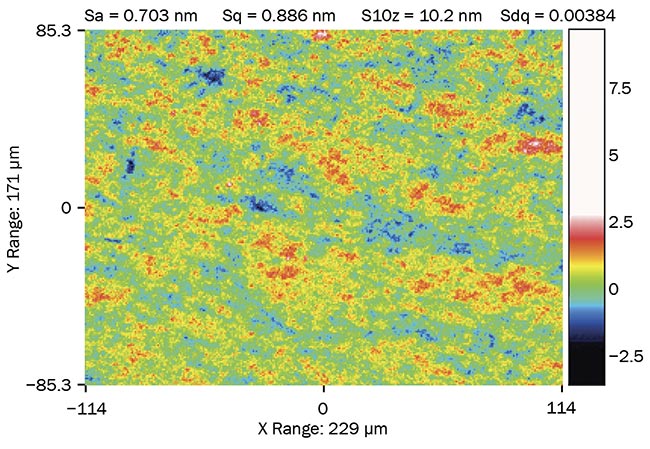
Figure 3. Typical microroughness surface map obtained using WLI; 50× magnification. Sa: arithmetical mean height of the surface; Sq: rms height of the surface; S10z: 10-point height; Sdq: density of peaks. Courtesy of Optical Surfaces Ltd.
Materials and coatings
In terms of material selection for OAP mirrors for high-power laser applications, a zero- or near zero-expansion substrate such as ZERODUR, CLEARCERAM-Z (HS), Corning 7980, or NIFS-I would be appropriate. Some high-power laser facilities are showing preference for fused silica for extremely short, very high-peak power pulses because of a presumed better response against “neutron activation” effects despite its slightly poorer (though still excellent) thermal response. Additionally, some coating suppliers suggest that coating adhesion on fused silica OAP mirrors may be better, although not all suppliers agree.
With regard to coating selection for very high-power applications, the most obvious choice is an ultrahard multilayered dielectric (MLD) coating. This is because of the coating’s high reflectance over a selected spectral range, but more importantly because it can be designed to withstand very high-power loads and therefore it exhibits high laser-induced damage thresholds (LIDTs). For very fast pulsed lasers it is also important to achieve low GDD (group delay dispersion) values. GDD is used to characterize
layered mirrors when group velocity dispersion (GVD) is not particularly well defined, yet the chirp induced after bouncing off the mirror can be well characterized. Expressed in fs2, GDD provides a measure of the chromatic dispersion induced by the coating stack. The substrate properties have no impact as the concern here is with the mirror’s reflection rather than transmission characteristics.
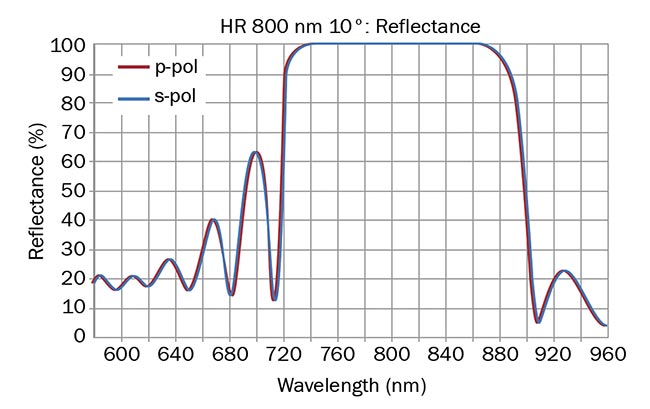
Figure 4. MLD coating, center wavelength 800 nm (top); standard type: S-shape GDD (fs2) response (bottom). R: high reflectance; p-pol: P-polarization (tangential component); s-pol: S-polarization (sagittal component). Courtesy of Optical Surfaces Ltd.
The ultimate goal for a top-quality OAP mirror is to keep GDD as low as possible — within ±50 fs2 for all wavelengths within the bandwidth around the center wavelength. Even better is to keep GDD as constant and low as possible across all wavelengths. The latter is more difficult to achieve in nonmetallic coatings such as MLDs because these require a carefully designed stack composed of more layers than usual, as well as tight manufacturing tolerances. Balancing these demands with fluctuations in reflectance as a function of wavelength results in a considerable rise in coating cost. Figures 4 and 5 show two possible options in coating design.
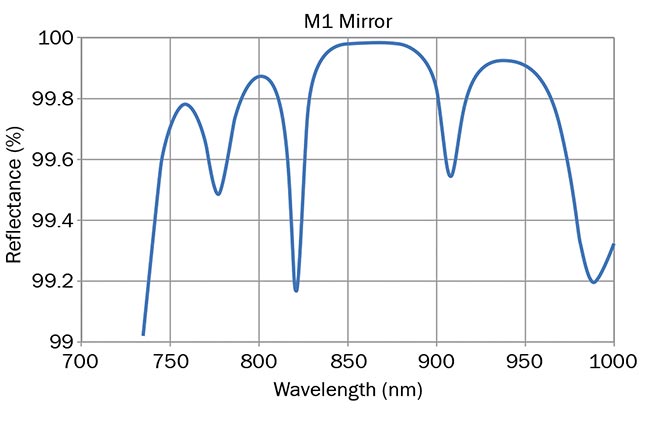
Figure 5. MLD coating, center wavelength 800 nm (top); special type: flat GDD (fs2) response (bottom). Courtesy of Optical Surfaces Ltd.
Focusing lenses
Many of the considerations and challenges described for OAP mirrors apply to focusing lenses for high-power applications, with a few notable differences. For focusing lenses, the required levels of asphericity, and hence degree of manufacturing difficulty, are often significantly less than the corresponding OAPs, but there is still a catch.
Focusing lenses are typically used with multiple beam lines, and in the case of the U.S. National Ignition Facility (NIF), as many as 192. As a result, these demanding lenses must be manufactured simultaneously (in contrast to one very difficult OAP). Figure 6 shows a plot of asphericity versus lens focal length at 351 nm, for illustrative purposes, and for a direct comparison with the OAP examples described earlier.
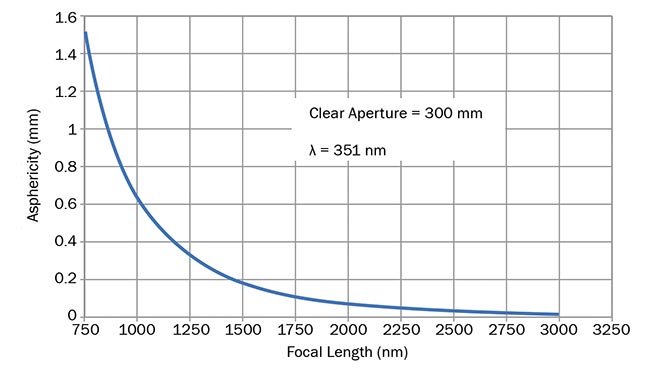
Figure 6. A focusing lens’ asphericity against focal length. Courtesy of Optical Surfaces Ltd.
High specifications for the wavefront error (WFE) in transmission, slope errors, surface quality, and microroughness below 1 nm rms are as important for focusing lenses as for OAP mirrors.
Figure 7 shows the WFE and slope errors (in terms of waves) on a high-power laser focusing lens produced using a traditional pitch-polishing technique and tested at 633 nm. The focal length of this lens is around 1200 mm, with a diameter of 350 mm and an asphericity around
0.4 mm.
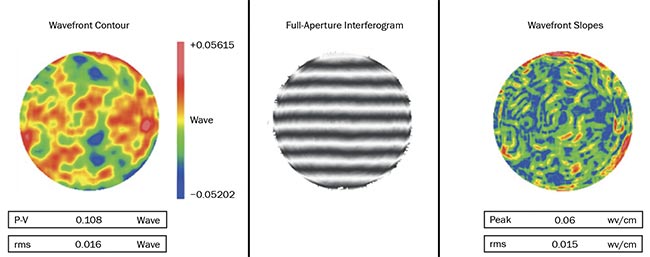
Figure 7. Focusing lens, f ~ 1200 mm, diam = 350 mm, asphericity ~ 0.4 mm.
Despite the similarities in performance
requirements with OAP mirrors, additional care should be taken during the
manufacturing of focusing lenses for high-power laser applications. For example, since these optics are used in transmission, an extra precaution should be taken to prevent microcracks from developing underneath the polished surface (subsurface damage).
These microcracks may extend to as little as a few microns underneath the surface and are not directly visible unless the surface is chemically etched to remove the upper layer and reveal the damage. Even then, their structure and extent can only be observed under a microscope. It is very important to keep these to a minimum.
If subsurface damage is extensive,
the lenses may shatter when the high-intensity pulses go through the glass. Alternatively, the lifespan of the focusing lenses may be significantly reduced. To avoid subsurface lens damage, it is important to proceed gradually through the smoothing grades, and with progression to finer grades, to ensure that sufficient material is removed to undo the potential damage caused by the previous grades.
Finally, while a hard dielectric coating is commonly used for OAP mirrors,
high-power laser facilities often prefer to use a sol-gel type of coating for focusing lenses. It has good antireflective (AR)
properties and high LDT, and most importantly it is relatively easy to remove if damaged, which allows for recoating. Recoating is not possible with hard AR coatings, but these surfaces can withstand laser impacts for much longer periods of time.
Many leading laser facilities such as the NIF and Orion have developed their own sol-gel coating processes. Their
internal facilities have the ability to recoat within a few days, thereby providing improved flexibility and greater autonomy. In short, this coating process requires the immersion of the lens within a suspension solution, drying and forming a gel-like substance on the surface. The coating is chemically processed to enhance its properties and make it harder.
Meet the author
Aris Kouris (DPhil, MSc, BSc) has been sales director for the past 11 years at Optical Surfaces Ltd., a Surrey, England-based company that specializes in the manufacturing of large and demanding optics and instruments for fundamental physics, astronomy, space, and defense. He has a doctorate in optical engineering from the University of Sussex.