David Henderson, New Scale Technologies
Smart motion technologies can reduce system size and simplify integration, enabling smaller photonic instruments with full performance.
Advances in microactuators, microelectronics and micromechatronics are enabling a new class of all-in-one “smart” positioning modules for photonics system miniaturization. Many of these inventions stem from the mobile phone industry demands to pack more features into smaller spaces while using less power. Now these smart motion capabilities are creating exciting opportunities for reduced size and unmatched performance in handheld, portable and mobile instruments.
For analytical instruments based on spectroscopy and spectrometry, miniaturization requires substantial re-engineering of the optomechanical subsystems to accommodate smaller sample sizes and smaller optics. Battery-powered motion systems for sample alignment, light source wavelength control or optical focus are crucial to achieve high-quality results.
Applications include “near patient” diagnostic blood testing in the home, doctor’s office or remote clinic. Medical workers can diagnose patients more quickly, start the correct treatment sooner, achieve better outcomes and lower the cost of care. The benefits are particularly great in resource-limited areas.
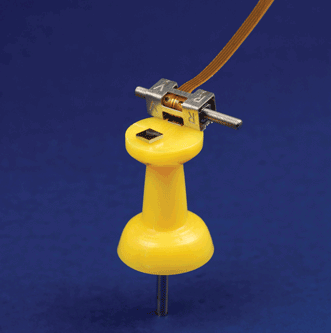
SQL piezoelectric motor and NSD-2101 drive ASIC on a pin. Photo courtesy of New Scale Technologies.
Portable analytical instruments for law enforcement, environmental monitoring and public safety can definitively detect pathogens, illegal drugs, explosives and other hazardous substances. They allow organizations to launch immediate and more effective responses.
Other optical instruments include wearable devices such as assisted-vision headsets with personalized focus algorithms that enable the legally blind to see.
Microactuators to move micro-optics for focus, zoom, tuning or alignment include voice coils, DC motors with gearboxes and piezo motors.
Voice coil motors are best suited for moving masses less than 0.5 grams with a stroke less than 500 μm. DC motors work well for larger devices with greater than 20 grams of moving mass and precision greater than 10 μm. Piezo motors are ideal for moving masses between 1 and 20 grams with submicrometer precision and many millimeters of stroke.
Piezoelectric motors are small. For example, New Scale Technologies’ Squiggle motor is only 2.8 × 2.8 × 6 mm. The introduction of reduced-voltage piezoelectric motors has further facilitated their use in motion modules for portable battery-powered devices.
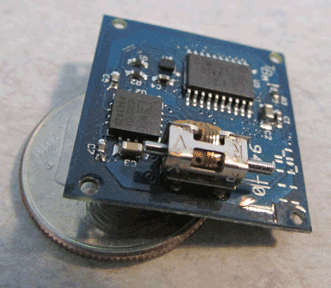
The piezoelectric Squiggle motor in an M3 smart module is mounted on the integral controller board. Photo courtesy of New Scale Technologies.
Each actuator requires drive electronics. Typically, these comprise many discrete components on circuit boards that are many times larger than the actuator or stage. In the past decade, advancements in analog microelectronics have reduced the size of microactuator drive electronics by at least 10,000 times.
Now, application-specific integrated circuits (ASICs) are commercially available to operate tiny piezoelectric motors directly from standard batteries.
Position sensors are needed to achieve precise closed-loop positioning. Miniature single-chip position sensors include Hall effect (magnetic) sensors, optical sensors and capacitive sensors.
Finally, microcontrollers aid system miniaturization. The latest-generation microcontrollers have the tiny size and full features that allow them to be embedded into a micromechatronic module with the drive ASIC and position sensor integrated circuits (ICs). With embedded firmware, the microcontroller enables closed-loop position control. It communicates with the external controller to receive commands, reads the module position from the sensor IC, and sends commands to the drive ASIC to move the micro-optic to the commanded position.
Smaller mechanisms require special handling
Working with very small mechanical components increases the challenges in tolerances, friction, alignment and control. Designing a very small, precise and smooth slide requires new approaches to overcome problems such as friction spikes. Even commercial microstages using traditional bearing configurations exhibit unpredictable friction characteristics that make it difficult to control the motion on a micrometer scale.
Ball or cross-roller bearings in cages typically exhibit “cage creep,” causing friction to increase by more than an order of magnitude. Recirculating ball bearings inevitably touch each other while moving along the recirculating path, causing intermittent high-friction spikes. The nonuniform and unpredictable changes in friction seriously degrade the ability to control the stage’s motion and position at the submicrometer level.
Assembling micromechanical systems requires extremely high tolerances on each component, as well as precision assembly techniques.
For many instrument designers, the specialized skills required to develop miniature closed-loop motion systems are outside their core expertise. The work of miniaturizing and simultaneously optimizing the motor, driver, mechanical guides, support structures, mechanical interfaces, electrical interfaces and closed-loop control systems can significantly delay product development when completed by inexperienced teams.
Motion control companies are solving these challenges by creating all-in-one motion systems where the actuator, position sensor IC, drive ASIC and microcontroller are meshed with the structure, guide bearings, and electrical and mechanical interfaces to create robust and practical smart motion modules. These modules eliminate the large external controllers and address the difficulty of developing micromotion systems from individual components.
One example of a smart motion module is the M3-LS Smart Stage from New Scale Technologies, in which a piezoelectric motor, position sensors, drive ASIC, precision slide assembly and microcontroller with firmware are built into a single, all-in-one miniaturized unit.
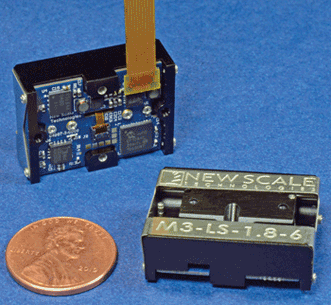
M3-LS all-in-one motion systems include a controller board that is integrated into the module. Photo courtesy of New Scale Technologies.
Developing and optimizing micromechatronic systems requires specialized expertise in piezoelectric motor control and micromechanical integration. These include:
• Optimizing motor drive signals for the specific piezo motor under variable environmental and use conditions. The resonant frequency of a piezoelectric motor is temperature-dependent and varies slightly with manufacturing tolerances. The embedded microcontroller in an M3 smart module stores and uses the unique calibration parameters for each module. The drive ASIC adjusts the pulse drive frequency in real time to maintain optimal drive frequency with changing temperature and duty cycle.
• Designing circuit boards as precision mechanical components in the total assembly. The piezoelectric motor in an M3 smart module is mounted directly on the controller board, which forms one side of the housing and is precisely aligned with and coupled to the moving stage.
(a) AEDR-871x optical encoder. (b) NSE-5310 Hall effect encoder. Photo courtesy of ams.
• Identifying and preventing potential faults in each component. These include over-travel conditions, extended stalls, lost encoder counts and overheating.
• Combining multiple sensors in a single module to achieve absolute position sensing. The incremental position measurements of the magnetic encoder are converted to absolute values by a separate optical sensor. The incremental sensor provides many millimeters of travel, while the absolute position sensor eliminates the need to “home” the stage on power-up.
• Designing guide bearings with low and consistent friction and micrometer-precision movement. A slide design with radial ball bearings in a kinematic “V” guideway has zero clearance, high stiffness and nearly zero friction. Friction is uniform over the entire travel range, even under high direct loads and side loads. It also has low sensitivity to particles, an advantage in portable systems for field use.
By miniaturizing the system components and optimizing the integration of the module, all-in-one systems deliver high performance in the smallest space. The integrated controller reduces overall system size dramatically compared with conventional microstages with separate controllers (Table 1). Overall system size is even smaller than can be achieved with microelectromechanical systems, which also require external controllers.
With all of the closed-loop control processing onboard, all-in-one modules minimize the bandwidth and computational load on the central processor. They greatly simplify the integration, accepting simple high-level motion commands from the central processor over a standard serial interface. With a serial peripheral interface, the module can be treated as a serial peripheral interface slave in the system.
Modules with industry-standard electrical connectors and mechanical mounting of micro-optics further simplify integration.
All-in-one motion modules meet emerging requirements for laboratory-quality results from instruments that must be one-tenth the weight and size. In addition, they must run on battery power, perform reliably in extreme temperatures, tolerate shock and vibration, and be easy to operate with minimal training.
These drop-in motion systems are easy to install in the larger instrument and require no special control engineering skills such as tuning a proportional integral derivative control loop. They free up designers to concentrate on proprietary technologies for their own instruments.
Meet the author
David Henderson is founder, CEO and chief technology officer of New Scale Technologies in Victor, N.Y.; email: [email protected].