Sean Bergman, Coherent Inc., and Marty Hemenway, Electro Scientific Industries Inc.
Laser-based processing has been a key enabling technology in improving the quality and reducing the size of devices such as cell phones, laptop computers, digital cameras and MP3 players. As manufacturers continue to press for even greater device miniaturization and reliability, the need for greater accuracy and improved process control of laser-based techniques becomes all the more important.
Key to achieving these goals is the ability to make precise in situ measurements of laser output characteristics in real time. For system builders using high-repetition-rate lasers, this requires devices that go beyond traditional laser power and energy measurement instruments.
Via drilling is one example of this trend. Vias are small holes made in multilayer circuit boards that are filled with a conductive material to make electrical connections between the various layers. Laser drilling is currently the method of choice for making microvias for modern, high-density circuit packaging. For example, Electro Scientific Industries Inc. (ESI) has a via drilling system with a UV laser that operates at speeds of up to 70 kHz and that can produce in one minute as many as 44,000 vias with diameters down to 50 μm.
For this system to maintain accuracy and repeatability, it is necessary to precisely control the energy and the average power of each laser pulse in real time. The system uses beamsplitters at several locations to pick off small optical samples for measurement. The detectors and associated pulse-monitoring electronics, which are built in, must be capable of measuring light levels in the nanojoule range and of sampling at repetition rates of up to 70 kHz. The embedded energy sensor must be able to detect pulse-to-pulse energy variations of less than 1 percent.
Photodiode detection
In designing the detection segment for this system, the development team at Coherent Inc. chose to use a customized photodiode and electronics to deliver a 100:1 signal-to-noise ratio at 1 nJ, a 100× dynamic range and a 100-kHz frequency response. A primary driver for this decision was that pyroelectric detectors, commonly used for pulse energy measurement, do not exhibit adequate sensitivity for pulse energies less than 100 nJ at the sampling rates required. Properly designed photodiodes can readily provide this level of sensitivity and performance. The photodiode has performed well in this application, and the entire monitoring system has been successfully integrated into dozens of the company’s via-drilling systems.
Another important laser-based process with needs that extend beyond traditional laser power and energy measurement is semiconductor memory yield improvement. In this technique, redundant circuits are included on 300-mm wafers for DRAM and SRAM memory. During wafer production, the individual memory circuits are tested, and connections to defective or unneeded circuit elements are severed using the laser (Figure 1). This approach has dramatically improved the yields on memory and logic integrated circuits.
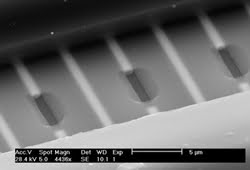
Figure 1. The electron micrograph shows both severed and unsevered links in a semiconductor memory circuit. The scale is indicated in the legend.
The ESI 9825 semiconductor processing system cuts an individual memory circuit link using a single pulse from a Q-switched, Nd:YVO4 laser that operates at 1064 nm and that has a maximum repetition rate of 40 kHz. Accurately controlling pulse energy is also critical to this application. Too much laser energy damages the underlying substrate; too little fails to completely remove the electrical link. An InGaAs detector, which delivers sensitivity down to the nanojoule range at 1064 nm with excellent signal-to-noise and adequate response speed, was selected to monitor the laser energy in this application.
To meet the high accuracy requirements at energies less than 20 nJ, a NIST-traceable customized Coherent measurement system, which has a pulse sampling rate of up to 10 kHz, accurately calibrates the onboard detector for reading pulse energies from nanojoules up to microjoules. The calibration detector can be attached to the instrument whenever it is required, using a mechanical interface that ensures repeatable optomechanical registration.
Pulse picking
The pulse-sampling technique used in the calibration electronics also can be described as pulse picking. Although the measurement electronics record every pulse at the 10-kHz pulse repetition rate, they use only a subset of pulses from which to display the measured information. Therefore, the analog amplifiers, data conversion devices, data sampling rate and measurement system bandwidth must be fast enough to support the full 10-kHz pulse rate.
However, in the digital realm, where the pulse-picking process takes place, the bandwidth requirement is relaxed, enabling the processor to simultaneously keep up with the data flow, user interface, communications interface and display in real time. This is important because 10-kHz sampling represents a large data flow, and the digital sampler must still run at 2 MHz to accurately characterize the pulses. The measurement system automatically switches between the pulse-picking and nonpulse-picking modes.
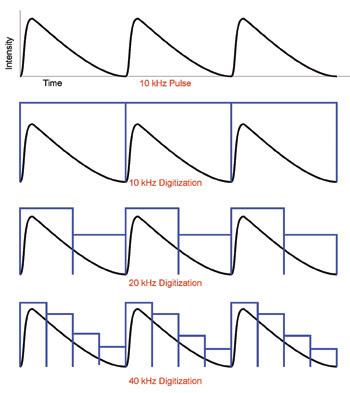
Figure 2. The drawing shows a pulse that is recurring at 10 kHz. As the digitization sampling frequency is increased, a more accurate picture of pulse shape and, most importantly, peak pulse height is obtained.
As an example, if the pulse is digitized at 10 kHz (Figure 2), there is no information on pulse shape and, most importantly, on the precise height of the pulse peak. Cutting the pulse into smaller pieces, in terms of time, reveals its shape. If the sampling rate doubles, the pulse is still only crudely seen. If it goes to 40 kHz (cutting each pulse into four time slices), a shape emerges. At a 2-MHz sampling rate, you can slice each pulse into enough pieces to accurately characterize its shape as well as the height and location of its peak. The Coherent instrument samples at 2 MHz to accurately sample the pulses at a maximum rate of 10 kHz; from this data stream, every 10th pulse is used for display purposes on the meter.
To summarize, laser processing enables miniature electronic components to be rapidly created at market-enabling volumes. But to deliver high yields at these volumes requires reliable, real-time monitoring of several aspects of high-repetition-rate laser tools. Fortunately, laser instrumentation researchers and engineers are meeting this need with innovative, high-speed products. These instruments are often custom-designed and are routinely integrated into systems.
Meet the authors
Sean Bergman is a product line manager at Coherent Inc. in Portland, Ore.; e-mail: [email protected].
David “Marty” Hemenway is a laser and optics engineer at Electro Scientific Industries Inc., also in Portland; e-mail: [email protected].
How They Work
Power meters receive a laser beam and generate a corresponding electrical signal that is converted to a power reading. The challenges that manufacturers of these devices face today include how to increase accuracy as well as tolerance to higher power and to power and energy densities while reducing size and cost.
There are two fundamental approaches to power meters: thermal and semiconductor. The heart of the thermal power meter is an absorber and a thermopile. The absorber heats up when exposed to the beam. The thermopile is an array of thermocouples that converts heat into voltage. A heat sink at the back draws the heat away from the detector.
Semiconductor power meters convert photons directly into electrical current without the heating mechanism. They are much faster, but also much smaller. In addition, they handle much less power, work over smaller bandwidths and have drastically varying sensitivity across their bandwidths. They typically measure very low powers (a watt down to nanowatts).
There are three key issues for any laser power or energy meter:
1. How much average power can the detector take before it overheats? Power is usually expressed in watts.
2. How concentrated can the laser energy be in space and time before it damages the absorber? These criteria are usually expressed as power density in watts per square centimeter and energy density in joules per square centimeter.
3. Within its ability to withstand the laser power and intensity, how accurately does it measure the actual power or energy in the laser beam?
Several parameters can affect the accuracy, including the wavelength of the laser; the size, shape and position of the beam; and temperature (power). After that, there are a number of secondary issues, such as the meter’s response time and sensitivity to small signals. These are the issues being addressed by power meter manufacturers today as they work to keep pace with advances in laser technology.
Alan Chachich, Gentec Electro-Optics