Myeong Nam, Joseph Washer and Jacob Oh, ISP Optics Corporation
Fabricating optics using chalcogenides can be challenging because of these glasses’ special optical, mechanical and economical characteristics. Diamond-turned machining is a viable option for addressing some of the issues with the conventional molding and polishing process.
Chalcogenide glass has gained attention in the optical engineering community as a versatile material for infrared thermal imaging and sensing applications, as well as for collimation of fiber and quantum cascade lasers.
The optical, mechanical and economical properties of chalcogenide glasses present unique challenges for manufacturing optics. Typical manufacturing steps include blank fabrication (grinding, edging and curvature generation), conventional polishing and/or diamond-turned machining (DTM), and coating. Spherical and aspherical lenses also can be manufactured with some chalcogenide materials using injection molding.
Optical and thermal properties
Chalcogenide glass has attractive optical properties as an IR material because it is widely transparent between the short-wave (SWIR) and long-wave IR (LWIR) regions. Chalcogenide glass composed of the chalcogen elements sulfur (S), selenium (Se) and tellurium (Te) has a glass-transition temperature (Tg) characteristic of amorphous materials, even though its crystalline structure is not a continuous random network as observed in other amorphous materials.
Chalcogenide material properties related to temperature and thermal stress are found to be different from those relevant to other infrared materials. Weak-bonded and less robust crystal structures pose technical challenges, such as low adhesion between the glass and thin-film layers. Figure 1 shows that chalcogenide glasses are good candidates for SWIR-LWIR applications. Their transparency in the IR spectrum is comparable to that in other broadband IR materials, such as zinc selenide (ZnSe) and zinc sulfide (ZnS) multispectral grade.
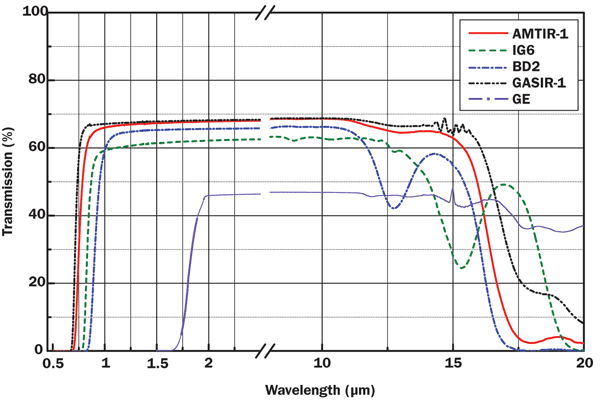
Figure 1. Transmission for uncoated, commercially available chalcogenide glasses.
Chalcogenide glasses exhibit a low rate of change in refractive index relative to temperature change. In comparison to germanium (Ge), which has a thermal change (dn/dt) at 10 µm that equals 39,600 × 10–6/K, IRG24 (Ge10As40Se50) has a dn/dt that is multiple magnitudes lower (dn/dt = 19.9 × 10–6/K @ 10 µm). Optical engineers take advantage of this characteristic when designing athermalized IR lens assemblies. As temperature changes, IR lens assemblies with chalcogenide materials will maintain focus throughout the operating temperature range (typically, −40 to +62 °C).
Thermo-optic coefficients of chalcogenide glasses are significantly lower than that of Ge, as shown in Table 1. Potential applications in high-temperature environments may now be viable if proper thin-film coatings are developed and applied.
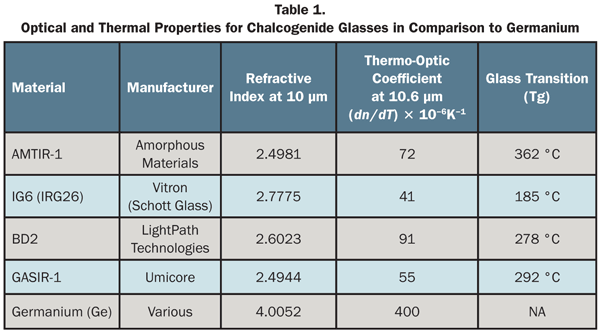
Conventional polishing and diamond-turned machining
The grind and edge processes to control the physical dimensions of the blanks are similar to processes established for Ge. After blanks are shaped and fabricated to the desired dimensions, chalcogenide glasses can be conventionally polished and/or single-point diamond turned. Mounting or blocking of optical lens blanks is done with the use of a special holder and pitch or wax. Chalcogenide glass can handle temperatures below 60 °C (140 °F) without too many difficulties, but at high temperatures, the material is susceptible to cracking and breaking. These temperature issues do not allow for the use of blocking pitch, so other blocking methods are required. Black centering wax can be used for “hard blocking.”
Because chalcogenide glasses are so soft, they are susceptible to surface-quality defects such as scratches, so extra care must be taken during the polishing process. Frequently, stains and digs appear on the surface if ultrafine polishing is not done properly. Precautionary steps in the process will result in increased polishing time, however. Polishing of AMTIR can be more difficult; GASIR, IG4 and IG6 are relatively less difficult.
Typical results from conventional polishing of chalcogenide glass can be as low as 0.5 fringes irregularity. Surface-quality results better than 40/20 can be achieved, but this is difficult. Centering (machining the diameters to get final size and fixing any wedge problems) can pose issues due to the heat required in mounting the lenses. It is practically impossible to save parts, as they crack during heating and can easily be chipped and scratched. It is usually better to avoid the centering process and to diamond-turn at least one side to keep the wedge within specifications.
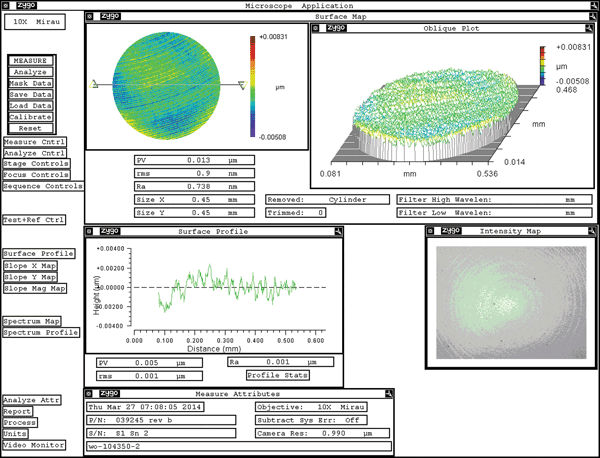
Figure 2. Typical surface-roughness measurement of a diamond-turned BD2 asphere.
The single-point DTM process for materials such as AMTIR-1, AMTIR-2, IG4, IG6 (also equivalent to IRG26), BD2 and GASIR requires a different approach. Chalcogenide substrates are susceptible to fixture problems and inaccuracies, as well as rotational forces which can result in poor surface irregularity or astigmatism, especially on parts with a large aspect ratio between diameter and center thickness. Diamond-turning machines most often use vacuum chucks or precision collets to manufacture standard IR materials.
New specialized fixtures machine chalcogenide materials with excellent surface quality and irregularity. The surface roughness on chalcogenide glasses usually is less than 25 Å rms with irregularities down to 0.5 fringes peak-to-valley at 632.8 nm. The single-point DTM process of chalcogenide glass is an extremely viable option for low to large production quantities (<500).
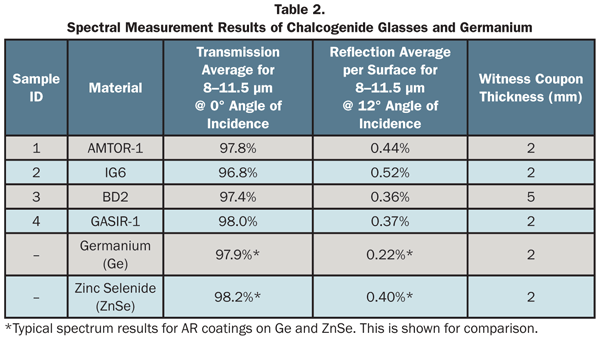
Molding process with chalcogenide glass
Chalcogenide glass is moldable, which adds another dimension to its versatility. For the molding process, a significant initial investment is required to manufacture the master mold. The molding process is rather economically unsuitable for low to medium quantities: Operating the injection molding machines is expensive, as is manufacturing the precision mold master for each lens. These initial setup costs typically are distributed over the thousands of units produced throughout its product life cycle.
Molding of glass lenses, unlike DTM, is restricted to diameters typically smaller than 25 to 30 mm. DTM also allows for much better form accuracy, and it produces better-quality aspheric and diffractive surfaces than the molding process. The mold masters for high-temperature press machines, which are made by single-point diamond turning, have good irregularity, but the molding process itself cannot duplicate the mold surface perfectly and exaggerates the irregularity on the finished glass surface.
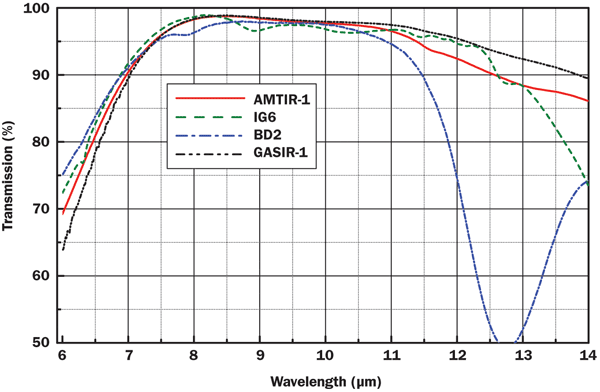
Figure 3. Transmission of AR-coated (both sides) chalcogenide samples for LWIR.
The single-point DTM process has the advantage of a relatively low nonrecurring engineering charge. On the other hand, the disadvantage of DTM is the longer man-hour requirement per piece. Each part is individually processed in DTM while an experienced technician continuously monitors its progress. The economical feasibility of DTM is maximized when the quantity is less than 1000 per batch. When the quantity in a project is larger than 1000, the high initial nonrecurring engineering charge to manufacture the metallic mold for the molding process becomes a less significant factor for the price estimates.
SWIR and LWIR antireflection coating development
High-efficiency antireflection (AR) coatings for chalcogenide glasses were designed and developed to meet two important design goals: low reflectivity and high durability. The optical performance of the coatings (reflection and transmission) is demonstrated in Figures 3 and 4.
AR coating designs on chalcogenide materials are customized film stacks based on a typical five-layer design (LHLHL).
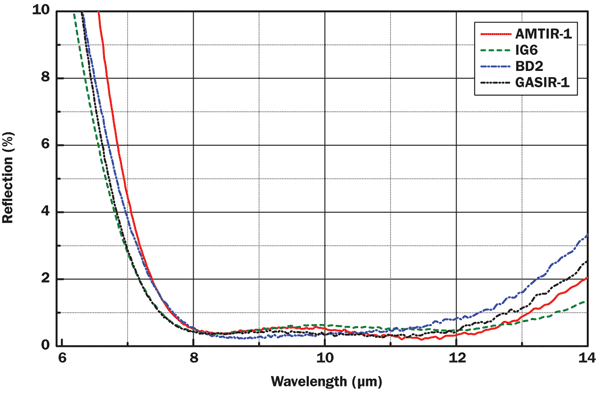
Figure 4. Single-surface reflection of chalcogenide glasses with AR coating for LWIR.
Radioactive thorium fluoride (ThF4) shows excellent environmental durability and less tensile stress as the top layer when used as the low-refractive-index material. Unfortunately, ThF4 has many limitations in both defense and commercial applications because of its radioactivity. An alternative low-index material was selected to replace the radioactive ThF4. Overall transmission and reflection were measured with a PerkinElmer Spectrum 100 FT-IR spectrophotometer; the coatings on chalcogenide glasses were comparable to broadband AR coatings on Ge and ZnSe.
AMTIR-1, IG6, BD2 and GASIR-1 witness coupons were subjected to the film-durability tests performed in the sequence specified in Table 3. After the durability tests were performed per MIL-F-48616 and MIL-C-48497A, the coatings showed no evidence of flaking or peeling. All samples passed the cellophane tape test after being subjected to the 24-hour humidity cycle. This additional test confirms good film adhesion to the chalcogenide glass substrates in a high-humidity environment.
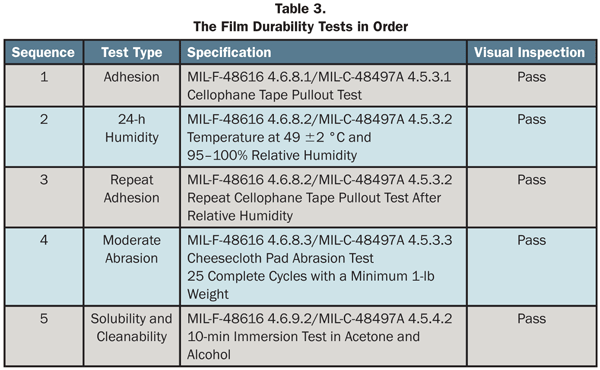
In addition to the development of an AR coating for LWIR applications, the design of a multiwavelength coating to accommodate the increasing number of SWIR needs also was carried out. SWIR film structure is different from the LWIR design, and coating materials must be transparent from SWIR to LWIR. Figure 5 shows single-surface reflection measured on witness coupons coated with various multiband AR coatings.
Common adhesion issues arise in relation to poorly cleaned surfaces and thermal shock. Chalcogenide glass materials are susceptible to oxidation and hydrolysis over time; a proper adhesion layer should be used between substrates and thin films to promote the bonding mechanism. The use of a binder layer is a well-established practice for a standard IR antireflection coating.
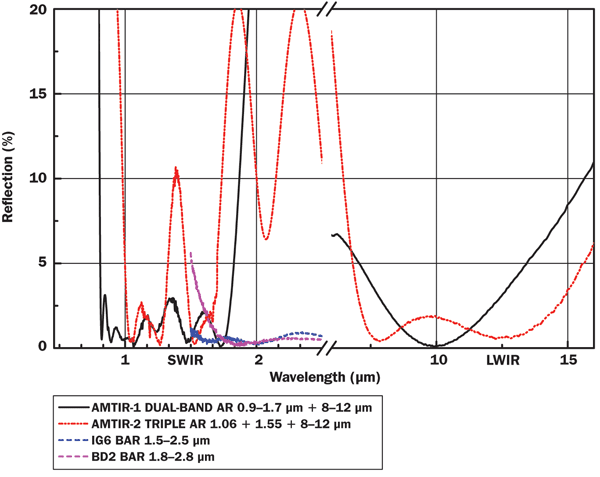
Figure 5. Single-surface reflection of chalcogenide glasses with AR coating for SWIR and LWIR.
For this task, ZnS and fluoride films were prepared in a 45-in. optical coating system manufactured by Vacuum Process Technology LLC. The system consists of an electron beam, thermal resistance, a Mark II ion source and a cryopump system. A quarter-wave thickness of [ZnS/fluoride]2 films at 1 µm was deposited on 25-mm-diameter × 2-mm-thick GASIR-1 witness coupons. The deposition rates for both materials were kept at 1 nm/s on Inficon IC/5 deposition controller with a quartz crystal sensor. Argon ion cleaning was performed before the deposition process started. The ultimate vacuum pressure was 4 × 10−6 Torr at a temperature of 140 °C. The 20-nm MgO or 20-nm Y2O3 materials chosen as an adhesion layer were found to be an improvement over other commercially available materials, which showed the delamination of entire films after coating. It is shown that deposited films, along with adhesion layers, are still partially delaminated from the substrate when thermal shock is applied to witness coupons. When hot films were cooled rapidly to room temperature, film adhesion was poor and left random holes on the substrates.
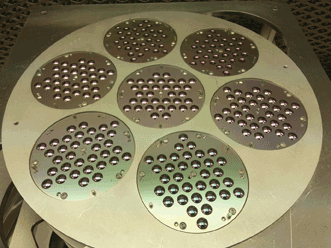
Figure 6. BD2 lenses are loaded onto a coating fixture.
Various test experiments were performed to find the effects of thermal shock on film lamination. After multilayer films were deposited at 140 °C as described above, GASIR-1 witness coupons were maintained in a vacuum chamber at 140 °C for the first test, at 100 °C for the second test and at 60 °C for the third test. They were suddenly vented to room temperature and visually inspected after the cellophane tape test per MIL-C-48497. Witness coupons kept at 60 °C (third test) prior to air venting passed several adhesion tests in a row, while other witness coupons kept at higher temperatures (first and second tests) showed slight peel-off. It was also noticed that ion-assisted deposition improved film structure by minimizing OH− absorption bands significantly at 3 and 6 µm.
Meet the authors
Myeong Nam is director of coating at ISP Optics Corporation in Irvington, N.Y.; email: [email protected]. Joseph Washer is production manager at ISP Optics; email: [email protected]. Jacob Oh is sales manager at ISP Optics; email: [email protected].