Dirk Müller, Lumera Laser GmbH
Just as CW and quasi-CW lasers have revolutionized the materials processing world, picosecond lasers are poised to change the world of micromachining. The use of picosecond lasers in micromachining was ushered in more than three decades ago because various millisecond and, later, nanosecond lasers had proved that pulsed lasers offer new capabilities.
Today, laser pulses in the millisecond to nanosecond regime are being used for drilling holes in wafers, cutting thin sheet metal and scribing ceramics, and for marking automotive parts, credit cards and passports. In micromachining applications, lasers outperform mechanical tools because of their flexibility, reliability, reproducibility, ease of programming and lack of mechanical force or contamination to the part.
Until the introduction of picosecond lasers, all applications were based on the principle of very fast local heating, melting and vaporization of the target material, which later caused thermal side effects such as burrs, recrystallization and microcracks in a product.
Industrial ultrafast lasers have become available recently. Focused picosecond pulses of appropriate energy are well suited to avoid major thermal side effects and reach a new level of machining quality.
Perhaps equally significant is that picosecond pulses are material-unspecific, making them the universal machining tool because micromachining with picosecond pulses does not rely on an absorption process. Underlying the micromachining is the formation of a surface plasma cloud. The large electric field of a picosecond pulse strips the low mass electrons off the atoms, and the positively charged atoms left behind undergo a Coulomb explosion.
It could be argued that even shorter laser pulses in the femtosecond range would further enhance the micromachining quality. However, femtosecond lasers are significantly more complex, prone to failure and deliver less average power at a much higher price. The electric fields generated in picosecond laser pulses are sufficient to trigger this process, and going to shorter pulses only complicates the system. The high peak power of femtosecond pulses requires careful beam delivery and is prone to unwanted nonlinear effects.
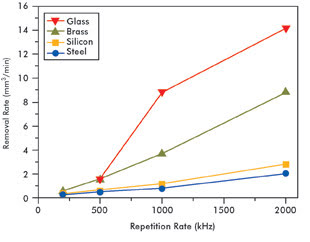
Removal rates increase with repetition rate.
Laser pulses in the picosecond range seem to hit the sweet spot: Picosecond pulses possess excellent beam quality, deliver the right pulse energy level and can be produced in a reliable, industrial package. They reach megahertz repetition rates with more than 50 W of average power, enabling economic industrial scale throughput. If the energy density is slightly above the ablation threshold (~1 J/cm2), most materials will show an ablation of a 10- to 100-nm-thick material layer. The ablation threshold varies only slightly with the type of material (0.1 to 2 J/cm2) and is mostly independent of wavelength, pulse length or other conditions.
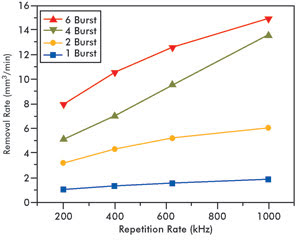
Removal rate substantially increases with burst mode operation.
Most micromachining applications are interested in sculpting a surface structure; i.e., the “cold” micro removal of material to scribe a trench, cut a shape, drill a hole, reveal a material layer or isolate an area.
Mechanical drilling/milling and electron discharge machining are overstretched in reliability and cost when creating structures <50 μm. A high-quality laser beam with an M2 <1.5 can be conveniently focused to a 5- to 50-μm spot size, enabling machine structures of similar size. A typical focal spot diameter of 25 μm will require ~10 μJ of pulse energy to satisfy the 1-J/cm2 ablation threshold criteria.
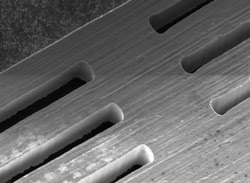
These 15-μm-wide slots are in a 20-μm silver sheet. Images courtesy of Lumera Laser GmbH.
Higher pulse energy densities will not necessarily work better or faster: The ablated plasma cloud gets denser and can no longer dissociate from the surface. Even worse, it may thermally alter the material and destroy the “cold” quality. An ideal industrial picosecond laser source for “cold” micromachining should produce pulse energies in the range of 10 to 50 μJ at a repetition rate of ~1 MHz. At even higher repetition rates, a shading effect from the plasma cloud of the prior pulse eventually reduces the efficiency.
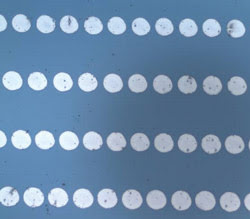
Shown is the removal of a 70-nm SiN layer on silicon, with up to 1 million dots per second. Dot diameter is 50 μm.
Recently, it has been observed that several picosecond pulses with nanosecond-scale separation (burst mode) not only will improve the ablation rate substantially, but also the micromachining quality; e.g., the surface roughness of blind holes.
Experiments with 50-W picosecond lasers operating in burst mode have achieved ablation rates of ±60 mm3/min. Applications with low aspect ratio (depth/diameter) yield in glass up to 20 to 60 mm3/min; in stainless steel, 10 mm3/min; in silicon, 30 mm3/min; and in organics and biomaterials, up to 10 mm3/min.
The cost per photon has dropped by a factor of 10 within the past four years, making the picosecond laser a very economical choice and one capable of competing with many other machining choices on a cost-per-part basis. Although the initial investment for a picosecond laser of adequate power and beam quality is higher than that for a nanosecond one, the total cost of ownership is only about $0.29/min. Within a minute, 20 mm3 or more of any hard or difficult-to-machine material, such as cubic boron nitride or diamond, sapphire, glass or ceramics, can be removed.
An ever-growing number of interesting applications are emerging, where removal of thin, small volumes creates high value in the product: the semiconductor industry (low k materials); photovoltaic industry (especially thin-film technology); display technology (transparent conductive oxide, organic LEDs); micromolds on demand; and precise apertures and electrode structures, large microstructured surfaces for the printing industry, or embossing of rolls or medical implants.
Even large marine vessels are candidates for micromachining. Micron-size features offer antifouling protection and reduce friction. Further, injection nozzles for high-compression cylinders as well as cutting and drilling of thin glass materials are emerging as important high-volume applications. To cater to large-scale industrial applications, picosecond lasers are required to demonstrate more than one year of mean time to failure and <1 h of time to repair. The newest generation of industrial picosecond lasers already demonstrates such performance.
Analysts agree that the market for industrial picosecond lasers will grow tenfold within the next three to four years. Power levels of 500 W will be reached, costs will be reduced and throughput will be increased. Reliability and cost of ownership will be the most decisive metric for any large-scale industrial use.
Meet the author
Dirk Müller is director of business development at Lumera Laser GmbH in Kaiserslautern, Germany. He can be contacted via e-mail at [email protected].