The excimer laser’s shift to commercial applications has created a demand for higher power levels and increased reliability from the laser itself, thus creating a greater demand for industrialized optics to control, redirect, reshape, and focus the intense UV radiation produced.
Michael A. Case, Teledyne Princeton Instruments, Business Unit of Teledyne Technologies
The first high-reflectance mirror coatings for the UV and vacuum UV (VUV) were of the Al + MgF2 type produced in the late 1950s. Coatings of this design are still used today for multigas cavity mirrors and many other applications because they are easily produced and offer good broadband reflectance (Figure 1). One drawback of Al + MgF2 coatings, however, is the high absorption (10% to 14%) in the UV and VUV wavelength regions, which causes these coatings to damage quickly when exposed to certain high-intensity, high-repetition-rate excimer laser pulses. Consequently, they cannot be used in many commercial laser-based systems.
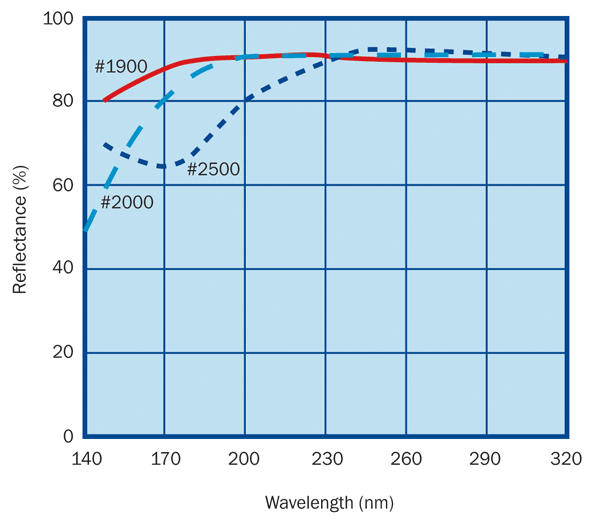
Figure 1. VUV-UV broadband Al + MgF2 coatings.
In 1973, Acton Research developed multilayer dielectric (MLD) thin-film coatings for excimer laser applications. These coatings gained rapid acceptance because they offered low absorption, high efficiency, and damage resistance of at least an order of magnitude greater than the Al + MgF2 coated mirrors.
Excimer laser optics
Excimer laser optics are coated or uncoated optical components designed specifically for use at excimer laser output wavelengths, the most common of which are 157 nm (F2), 193 nm (ArF), 248 nm (KrF), 308 nm (XeCl), and 353 nm (XeF). Typical excimer laser optics include beam-turning mirrors, laser cavity optics, beamsplitters, lenses, windows, and other components.
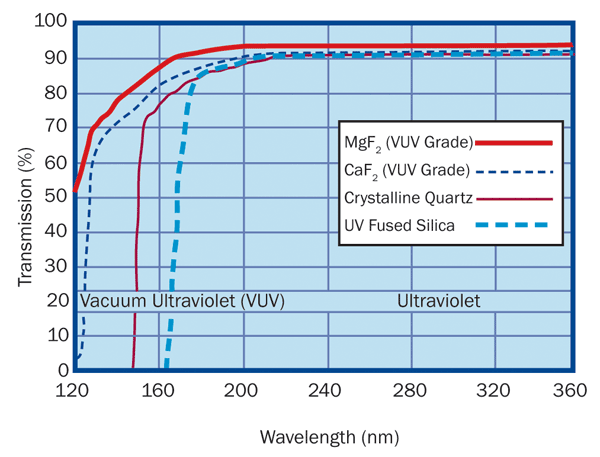
Figure 2. Substrate transmission properties.
Since the early days, there have been significant advances in the performance of 193-nm laser optics. In the pursuit of industrial-strength UV optics, new coatings have been developed with exceptional durability and resistance to laser-induced damage in a variety of emerging applications. This new generation of 193-nm coatings passes MIL-SPEC requirements for adhesion, abrasion, and humidity, allowing for easy handling and cleaning. These optics are also more resistant to laser damage, providing 4× improvement in lifetimes compared with optics produced just a few years ago.
To illustrate this point, laser testing of these new “hardened” 193-nm coatings has produced some excellent results. In addition, 193-nm HR mirrors were developed for the semiconductor industry to provide stable, long-term performance at high repetition rates and moderate average power. Mirrors tested by a leading manufacturer of lasers for semiconductor exposure systems have survived more than 8 billion laser pulses at 10 mJ/cm2, 4-kHz repetition rate with no damage or change in reflectivity.
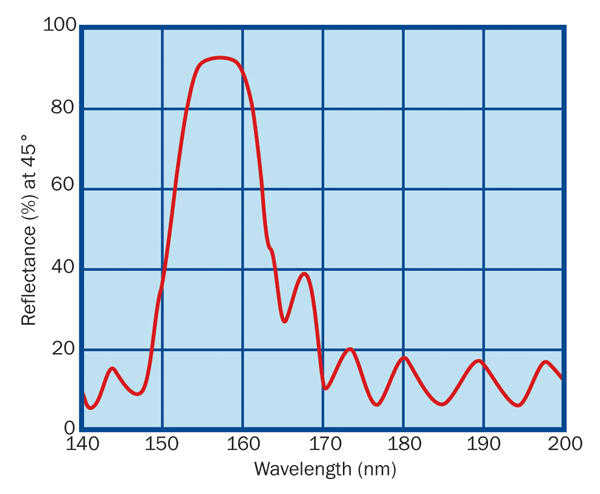
Figure 3. 157-nm (F2) beam-turning mirror.
Laser mirrors for 193 nm were also developed for the medical laser market (lasik) to provide increased lifetimes when exposed to high-fluence laser pulses at moderate repetition rates. These mirrors were certified for more than 2 million pulses when exposed to 300 mJ/cm2, 200 Hz, with no damage or change in optical performance. In contrast, conventional 193-nm mirrors produced a few years ago became damaged after only 24,000 to 120,000 laser pulses, with the best mirrors surviving only 500,000 to 600,000 pulses when operated at 300 mJ/cm2, 200 Hz.
Materials for excimer laser optics
The most frequently used materials in excimer laser applications are high-purity grades of MgF2 and CaF2 crystals, as well as specific types of UV-grade fused silica. Other materials include sapphire, crystalline quartz and BaF2. MgF2 or CaF2 generally are used as the rear reflector and front output coupler optics of an excimer laser cavity because of their resistance to the corrosive effects of the excimer laser gases.
UV-grade fused silica is more widely used for external laser optics such as lenses, beamsplitters, and mirror substrates and is the preferred choice over high-UV-absorption mirror substrates like Pyrex or BK 7 glass because of the slightly transmissive nature of UV multilayer dielectric mirror coatings.
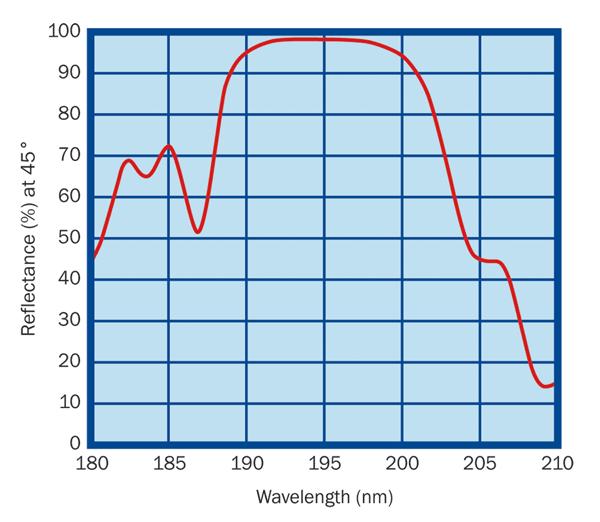
Figure 4. 193-nm laser mirror.
It is important to note that not all grades of these materials are suitable for use in excimer laser applications. Standard grades and even some UV grades, while acceptable for use at UV, visible, and near-infrared wavelengths, may have impurities that lead to low transmittance, high absorption, fluorescence, or color centers when exposed to high-intensity UV radiation. The purity of bulk materials is becoming more significant because of the higher average output power, higher repetition rates, and continuous operation of current laser systems (millions or billions of pulses).
Studies relating to the damage mechanisms under long-term UV exposure have helped material producers improve the purification of these materials. Some of the high-purity grades of MgF2 or CaF2 crystals are now often referred to as VUV or excimer grade. Figure 2 shows transmittance properties of these and other UV-transmitting materials.
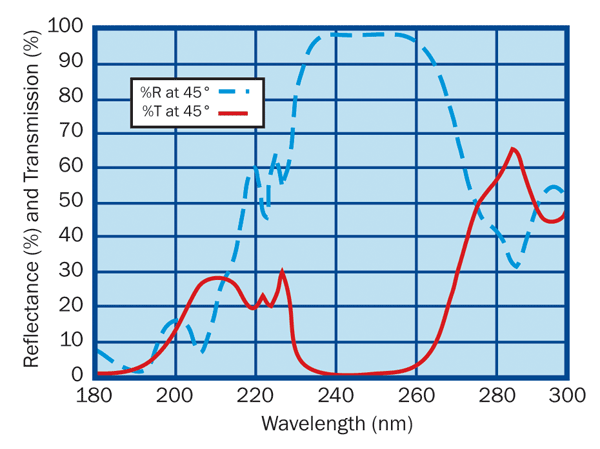
Figure 5. 248-nm (KrF) beam-turning mirror.
Specifying optical surfaces
Along with selection of the proper substrate material, actual damage threshold and long lifetime can greatly depend on the surface preparation of the optics. Most excimer laser optics are specified by surface figure and surface quality. Surface figure is a measurement of the deviation from an ideal surface, in terms of peak-to-valley waves. This is specified as λ/10 or better at 633 nm for most surfaces of excimer optics. For some special applications, surface figure specifications can be even greater, in the range of λ/20 or better.
Surface quality is defined as the number of flaws in an optical surface in terms of the scratches and digs, based on military specifications. Surface quality of excimer optics is most often specified as 20 to 10 or better for optimum, low-scatter performance of the optics. Precise fabrication techniques used to produce these types of surfaces, especially on crystalline materials such as MgF2 and CaF2, can contribute greatly to the overall optical performance of the excimer laser.

Figure 6. 353-nm (XeF) beam-turning mirror.
Typical UV, VUV, and excimer laser multilayer dielectric mirror coating materials include MgF2, sapphire, quartz, and a limited number of other fluorides and oxides. Each coating company has its own proprietary thin-film coating designs; therefore, mirrors from two coating companies are rarely the same. This, of course, leads to mirrors with varying degrees of performance and resistance to laser damage. A typical mirror is produced by carefully depositing layers of high- and low-refractive-index dielectric materials. The number, thickness, and types of materials deposited determine the reflectance and transmittance of the mirror.
It should be noted that because of the fundamental properties of available UV coating materials, especially at shorter wavelengths, the amount of achievable total reflectance can be limited. Some of the incident UV radiation can be absorbed or scattered by the coating. Therefore, careful selection of coating materials is essential. Also, because of the lack of nonabsorbing high-index coating materials for deep-UV wavelengths, a small amount of incident laser light can be transmitted through the coating into the substrate. The typical choice of a nonabsorbing, UV-transmitting substrate is important to avoid the potential of laser damage at the substrate surface.
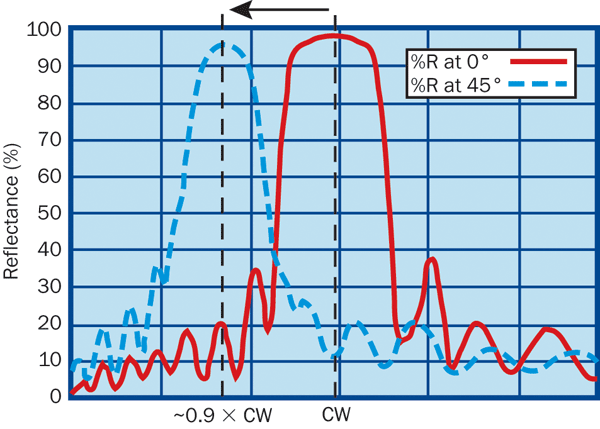
Figure 7. Angle of incidence effect for UV MLD reflector.
Reflectance and transmittance
Depending on the design, mirrors can be produced with more than two materials to yield higher reflectance, damage resistance, and durability. Work is ongoing on methods of evaporating thin films to improve damage thresholds and to reduce scatter. Whatever the method or coating design, optimum performance and long lifetime are directly related to certain considerations in the design and production of mirrors. These considerations include substrate material selection, final polish, surface preparation, coating design and materials, coating deposition technique, meticulous quality control, and accurate calibration.
We have found that one of the best means of ensuring the performance of a mirror is to measure the reflectance and transmittance at the laser wavelength and at the angle of design before using it in an application. For example, a mirror produced for beam-turning applications at 193 nm (ArF) should be measured for percent reflectance and percent transmission at 193 nm at a 45° angle of incidence. A measurement of transmittance alone is not enough to detect absorption that can lead to failure of the optical component when exposed to intense UV radiation. Figures 3 through 6 show typical mirrors for excimer laser applications. These mirrors were produced using different materials to ensure maximum performance. In addition, the mirrors at 157 and 193 nm were measured under vacuum conditions. This is done because air begins to absorb most of the radiation below ~200 nm, and accurate percent reflectance and percent transmission characteristics are difficult to measure using conventional nonvacuum UV-VIS spectrophotometers.
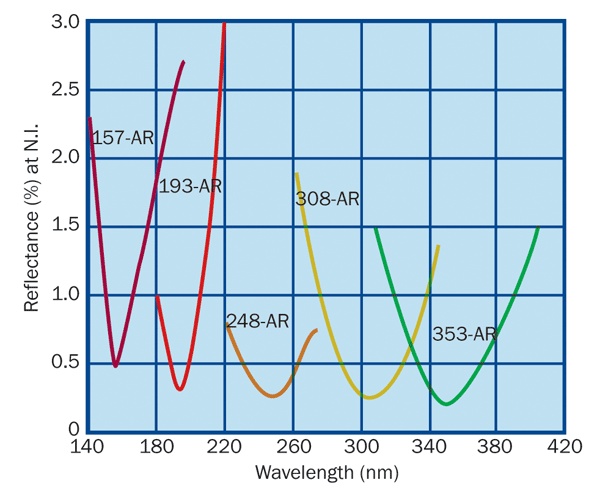
Figure 8. Antireflection coatings for 157 nm (F2), 248 nm (KrF), 308 nm (XeCl) and 353 nm (XeF).
Angle of incidence effects
When a mirror designed for normal incidence is used at 45°, this typically causes the reflecting band to shift toward shorter wavelengths and to narrow, while the reflectance drops slightly (Figure 7). Of more importance, the reflecting band may shift sufficiently so that the mirror transmits rather than reflects the desired laser radiation. If multiple angles are required from one multilayer dielectric mirror, it is best to discuss this with the coating manufacturer. In some cases, a mirror can be designed for both 0° and 45° use, but this varies with materials, wavelength, and the multilayer dielectric design used.
Antireflection coatings shown in Figure 8 are applied to transmitting optics such as windows, lenses, or the second surface of beamsplitters. The desired effect of an antireflection coating is to reduce unwanted reflections that normally occur from the surfaces of uncoated components and to ultimately increase the transmission of the components. The coatings shown were applied to fused silica windows (except for the 157-nm coating, which was applied to CaF2) to reduce the reflectance from 4.8% per surface at 193 nm to 0.3%, and from 4.1% per surface at 248 nm down to 0.25%.
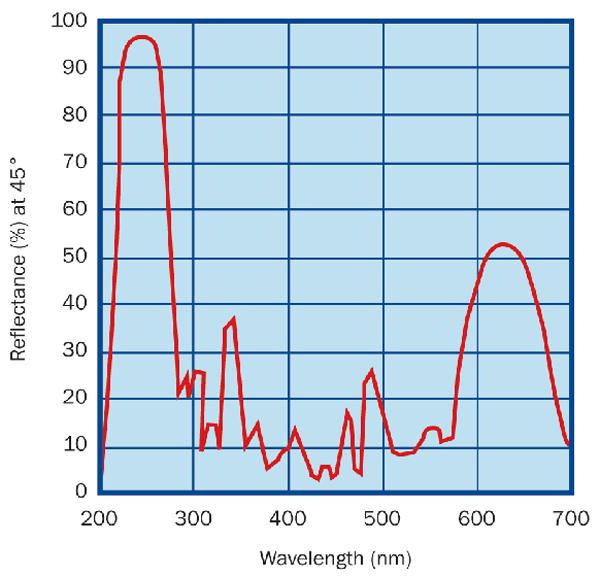
Figure 9. All-dielectric dual-wavelength laser mirror.
The various designs of multiwavelength reflective coatings for UV and excimer laser wavelengths are shown in Figures 9 through 11. These coatings were designed to permit using visible light sources for setup and alignment of the optics in the laser system prior to turning on the source of invisible UV radiation.
Dual-wavelength reflectors are manufactured using two basic designs. The first incorporates an all-dielectric design with two regions of maximum reflectance (Figure 9). This is normally manufactured using a base multilayer dielectric reflector optimized for visible wavelengths combined with a UV-enhanced multilayer dielectric reflector as the top portion of the coating. Since the UV reflectors are highly transparent at visible wavelengths, this combination can be an efficient dual-wavelength mirror coating with moderate to high damage resistance (Figure 9). One drawback is the inherent stress that can be created when depositing the many layers of coating materials in this stack. Too many layers can cause the coating to develop stress cracks, ultimately limiting its efficiency.
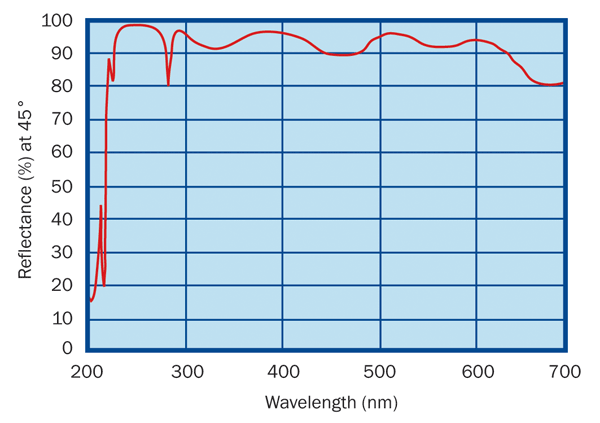
Figure 10. Multiwavelength mirror (aluminum + MLD).
The second type of multiwavelength mirror starts with a base layer of aluminum followed by a multilayer dielectric or modified multilayer dielectric thin-film coating (Figure 10). Basically, aluminum replaces the visible coating of the mirror described above and reflects broadband visible wavelengths (Figure 10). A narrow band of UV wavelengths is highly reflected by the multilayer dielectric coating deposited on the aluminum base layer. Modified multilayer dielectric coatings can broaden the UV reflecting band of this design with some sacrifice in total UV reflectance, as shown in Figure 11. Uniformity considerations make this modified design more suitable for large optics than multilayer dielectric or Al + MLD coatings.
Al + MLD multiwavelength reflective coatings are not transmissive, so unless absorbed by the top layer, unwanted radiation striking this reflector can reflect through the optical system. Likewise, radiation outside the UV reflecting band may damage the aluminum base layer if it is of sufficiently high power, because of high absorption of aluminum thin films. On the other hand, Al + MLD mirrors provide excellent broadband visible reflectance; therefore, the selection of visible alignment light sources is not limited.
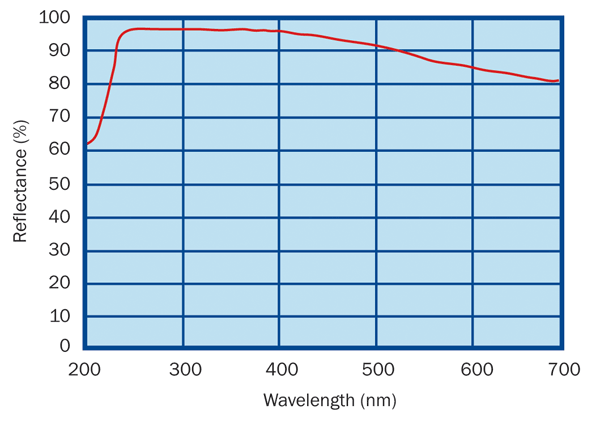
Figure 11. Multiwavelength laser mirror (modified MLD + aluminum).
Summary
This information is provided as a brief overview of what types of UV, VUV, and excimer laser optics are available. However, when shopping for excimer laser optics, it is best to deal with an optics company that specializes in these difficult-to-produce components to ensure the highest quality possible. Specify the application, power levels, repetition rate, beam size, and other conditions of the application that might affect the optical components.
Experienced companies have probably run into these conditions before and, in many cases, have developed optics or coatings suitable for your application. Of more importance, experienced companies can save you time and money by suggesting alternative approaches to the optics you require, or by advising you about what is realistic to expect when using UV, VUV, or excimer laser optics.
Reference
1. B.K. Flint and G. Callahan (1998). Characteristics of deep-UV optics at 193 nm and 157 nm. Proceedings of SPIE, Vol. 3578. doi:10.1117/12.344438