Improvements and affordability have broadened the use of vision systems for inspection, but several factors should be considered before making a purchase.
GLEN AHEARN, TELEDYNE DALSA
Technological advances have resulted in new, higher-quality sensors that enable machine vision cameras to deliver greater features and functionality at a lower cost than ever before. These factors are motivating businesses in a widening range of industries and sizes to pursue these new, improved and more affordable cameras. Regardless of the industry, however, there are a number of factors to consider while pursuing a vision solution.
For decades, companies have been using vision systems for inspection purposes when their products are of high value or have potential liabilities if associated with a defect. Now vision inspection is becoming more affordable for companies that are interested in producing quality products, even if they are neither of high value nor pose a potential risk if defective. Examples include hardware, such as nails and screws, corrugated cardboard and plastic containers.
Line scan or area scan?
The type of camera a manufacturer needs, whether it is a line-scan or area-scan camera, will depend on the application. Most people understand the technology behind an area-scan camera, which is akin to a high-resolution digital camera. Area-scan cameras produce 2D images with horizontal and vertical elements.
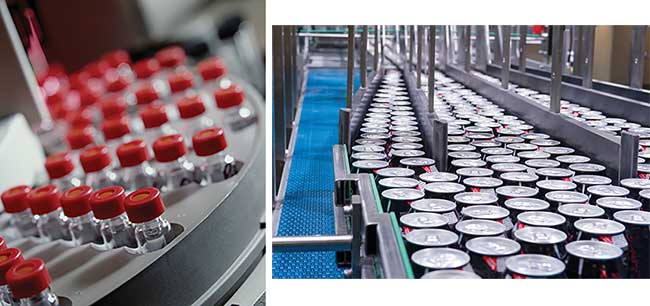
Area-scan cameras are used to inspect discrete components, such as pharmaceutical bottles or soda cans.
Line-scan cameras are more difficult to understand. Line-scan cameras look at one line, and then build a 2D image by moving the object relative to the camera while continually grabbing one-line slices. If the object being inspected cannot be contained in a practical-size field of view, then consider a line-scan camera. The most typical line-scan camera use is for applications that involve the inspection of a “web,” such as large rolls of paper, fabric, aluminum, steel, or sheets of glass.
If the application is to inspect a 50,000-ft roll of paper, it is not possible to do this in a single shot from an area-scan camera. A line-scan camera works in applications like this because the object, such as the roll of paper, is already moving as part of the normal manufacturing process. The line-scan camera compiles lines from the paper roll into multiple 2D images. If each image is 1000 lines tall, the camera will grab 1000 lines into one 2D image, and then pick up lines 1001 through 2000 for the next image, and so forth. The camera breaks the 50,000-ft roll of paper into 2D images, but nothing is lost in this process.
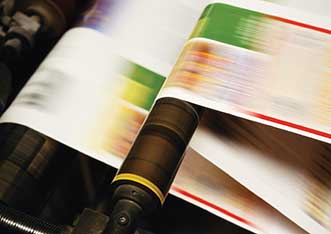
Line-scan cameras are used to inspect a ‘web,’ such as rolls of paper.
The default choice for many machine vision applications is an area-scan camera. If the application involves inspecting aluminum cans, glass bottles, or discrete components, then this is likely the right choice. A line-scan camera is used in cases where an area-scan camera doesn’t make sense, such as when a higher resolution is needed than the area camera can give or the object is something that can’t be captured in a normal field of view.
A 3D laser profiler?
Some inspection tasks require detection or measurement in three-dimensions, not just two-dimensions. These applications might require a 3D laser profiler. These profilers are comprised of two primary components, a laser, which projects a thin laser line across the area to be inspected, and a sensor which the laser light is reflected into. Based on where on the sensor the laser light reflects, the profiler can determine the height of a feature at that location. This is accomplished by fine precision mechanical positioning between the laser and the sensor. Laser profilers are like line-scan cameras in that they need the object being inspected to move under the unit to get information on the Y-dimension of the object.
Like line-scan cameras, 3D laser profilers are subject to the same resolution and speed considerations. In addition, there is an optical consideration. Laser profilers are typically offered as different models with different field-of-view and resolutions. For optimal performance, choose a model profiler that has enough field-of-view to completely cover your inspection area, but not much more. The smaller the field-of-view the higher the image resolution will be.
There are some applications that may require a 3D laser profiler for one type of inspection and a camera (area or line-scan) for other types of inspection.
Resolution requirements
Resolution is a key consideration in the process of choosing a machine vision camera. Calculating the resolution requires knowing the size of the field of view and knowing the smallest feature that needs to be resolved. The term “features” usually refers to defects in a product or a very small element on the object. The feature might be something that is supposed to be there, such as a tiny hole in a printed circuit board, or it could be something that is not supposed to be there, such as a scratch on an aluminum sheet. In these cases, there is a need to detect what that feature is, whether it is a defect or something that is meant to be there.
For many, when considering how small a feature is necessary to detect, the knee-jerk reaction is to get a camera that detects “everything.” This approach is not always realistic or necessary. Resolution is one of the main elements driving camera costs. It is important to get as much resolution as needed, but not to overdo it. Typically, the rule of thumb is this: To be able to accurately detect a feature of a certain size, plan on at least three pixels covering that area. It is not always possible to detect a feature by interpreting a single pixel. Several pixels across the feature can ensure it is not an aberration. For example, to detect a feature as small as 1/100 of an inch, choose a pixel size three times smaller than that, or 3/1000 of an inch.
The higher the resolution, the easier it will be to identify features, but now is the time to weigh the cost of the system against how much resolution is needed. Before committing, do some testing. Borrow a camera from a manufacturer or use a high-resolution photography camera to get an idea of how much resolution is required to see what needs to be seen.
Imaging rate
If the application is to inspect a discrete component, such as a can, bottle, or piston, how many of these components must be inspected per second? How many components are going to be moving past a single point in space in a given time period? Is it three per second? Fifty per minute? The camera will need to acquire at least at this rate. It is preferable to have a little extra margin. If the application calls for a camera that acquires at 25 fps, choose a camera that acquires at 30 fps. This will give some room for error.
Line-scan cameras require a bit more math to determine the appropriate acquisition rate, but it is not terribly difficult. Once you have determined your resolution, figure out how fast the object is moving and decide how many lines need to be grabbed in a second in order to have the necessary resolution. If a pixel resolution of 3/1000 of an inch is needed, and the object is moving at 100 inches per second, that would require a minimum line-scan camera speed of 33,333 lines per second, or a 33.3 kHz line rate.

Interconnect standards
There are different interconnect standards to choose from and that choice is based on a couple of requirements: speed and the distance between the camera and the computer. If speed is a priority, then find an interconnect that has speeds high enough to transfer data from the camera to the host computer at the rates that are required. Some of the higher-speed standards are Camera Link, Camera Link HS, 5 or 10 GigE, and USB3 Vision. Camera Link HS is one of the highest speed interconnects available, but it requires a frame grabber. USB3 Vision is not quite as fast as Camera Link HS in terms of speed. However, the USB connection typically is built right into the computer, so it doesn’t require a frame grabber or additional piece of hardware to acquire the data.
Some people choose GigE Vision because it is based on the Gigabit Ethernet specification and can go long distances between the camera and the computer. If the camera needs to be a long distance away from the computer — more than 10 to 15 m — GigE Vision is a good choice. A 1 GigE connection is slower than Camera Link and USB3 Vision standards, but it may be the only choice if the camera is far from the computer. The speed can be increased by choosing 5- or 10-GigE devices, but the faster GigE speeds will have an impact on maximum cable length and will also require higher-performance Ethernet cables to maintain data integrity.
For applications that require a 1-GigE connection for distance, manufacturers are working to reduce or eliminate this speed barrier. Some manufacturers have found ways to transfer data more efficiently by using methods similar to compression in order to increase the effective rate of GigE Vision while maintaining the advantage of long distance between camera and computer. If the application requires GigE Vision, be sure to talk to the manufacturer to see what they have to offer that might improve efficiency.
Light wavelength
Light wavelength is not an issue of concern for every application. Some applications, though, will require the camera to be sensitive to certain wavelengths of light. For example, with currency inspection, there may be security features that are only visible in UV or infrared light. In this case, be sure the camera has enough sensitivity at that wavelength to execute a successful inspection. There will also be a need for a light source with corresponding wavelength properties in order to allow the camera to visualize the feature in question. For a majority of applications, white light, or broadband light, is used, and any standard camera should suffice. If the inspection involves any special lighting, be sure that the camera choice is appropriate for the light wavelength required.
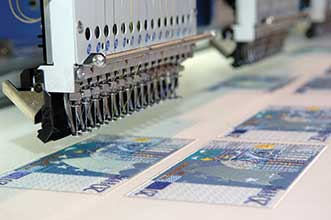
In some instances, such as for the security features on currency, UV or infrared light is used as part of the inspection process. In such cases, the camera needs to be sensitive to the light wavelength required.
Environment
Many vision systems are installed in sites that are very warm. Cameras are composed of sensitive electronic equipment and are impacted by temperature. Every camera manufacturer supplies operating temperature specifications for its products. Usually, if the environment exceeds these specifications, it doesn’t mean the camera won’t operate. Instead, it means the camera’s performance may diminish as the bounds of these specifications are exceeded. The most common way that performance diminishes in a hot environment is that the camera will become “noisier,” meaning there are unintended brightness variations in the image. Also, exceeding the temperature specifications usually has a negative impact on the life of the camera.
In order to keep the camera within its operating temperature specifications, many manufacturers have heat sinking methodologies. Therefore, when considering which camera to buy, be sure to assess the operating environment temperature, investigate the camera operating specifications, and discuss options the manufacturer can provide, if necessary, to keep the camera working as it should.
Camera customization
If there are plans to include purchasing a large quantity of cameras over time, manufacturers may be willing to offer some customization. If only one or two vision systems are needed for one or two lines in a plant, purchasing options will likely be limited to cameras available with off-the-shelf features and capabilities. However, if there is a need for 1000 vision systems annually for several years, some manufacturers will offer a high degree of customization. In such situations, it may be possible to remove costly and unnecessary features — or add a feature that is not included in the standard product. If long-term plans include purchasing a large volume of cameras, it is worth mentioning that to the manufacturer to see if any of these options can be negotiated.
Budget
Just like resolution and speed, cost is an essential factor in your purchasing decision. If, at this point, the decision has been made to buy and install a vision system, there has likely already been a determination on the technology’s cost-effectiveness and return on investment (ROI) projections. These assessments will dictate the camera budget.
Just as when considering resolution, cost is going to dictate what can be accomplished with a vision system. While it would be appealing to inspect a product down to the atomic level, that degree of resolution might be cost-prohibitive. Buyers have to weigh the vision system’s cost against the ROI.
One way to approach the camera selection process is by working backward, with cost being the first consideration. That will keep buyers from going down a road with a camera purchase that is going to make the cost unwieldy.
Quick Camera Selection Tips
• Determine a budget first, because that will set the bar for resolution.
• The camera’s resolution should provide for — at a minimum — a three-pixel coverage of a feature’s area.
• Select a camera with an imaging rate slightly higher than what is needed.
• Let speed and the distance between the camera and the computer dictate the camera’s interconnect standard.
• Make sure the camera can properly function in the lighting and environmental conditions where the inspections will occur.
• See if the manufacturer is willing to customize the camera.