Full company details
PFG Precision Optics
733 Bienville Blvd.
Ocean Springs, MS 39564
United States
Optical Glass Selection Is Not Always So Transparent a Choice
Photonics Spectra
Sep 2021The variety of glass materials and grades available for imaging optics can be blinding. Applying a few best practices can bring the optimal material candidate into focus.BILL THAMES, PFG PRECISION OPTICS
Optical designers have many glass types to choose from when developing assemblies for imaging applications. Typically, a variety of these material options is available to meet the desired design specifications of a particular system. The challenge then is to narrow down the selection by identifying materials that can achieve the desired performance while providing other practical benefits, such as reliable availability from the manufacturer and supplier, consistent high quality of the product, and a stable, favorable price point.
Mirrors with a low coefficient of thermal expansion (CTE). CTE is one of many material qualities that can influence the availability, delivery times, and cost of a glass. Glasses with a high CTE value can be more easily damaged due to thermal shocks and thus may require special considerations at several steps in the value stream. Courtesy of PFG Precision Optics.
This may all seem self-evident in theory. In practice, however, it can be challenging to zero in on the optimal glass for a new optical design that calls for new materials. When confronted by a variety of unfamiliar but potentially suitable candidates, a few best practices can help designers identify the best option without stalling the design process.
Availability and pricing
When considering a selection of candidate glass types for a design, it is not always readily apparent which options are more or less available than others. Consulting with the supplier or even the original manufacturer on material availability during the design phase can actually help to expedite a quote from an optics manufacturer by avoiding an unnecessary back-and-forth over alternate options. A consultation may also provide the opportunity to tweak or rethink a design before the development process has begun.
At the very least, designers should visit glass manufacturers’ websites, look up their candidate glass types, and confirm that the manufacturer still melts them. If a desired glass is missing from the list of products, a phone call can ascertain whether the OEM intends to resume melting the material again. Listing acceptable alternate material types in a design drawing can prevent unplanned delays due to the need for additional approvals. Further, even if a glass is available from the manufacturer, some suppliers may not have it on the shelf, or they may offer an alternate type instead. Keep in mind that i-line glasses are typically special melts and can require months of lead time before the materials are shipped from the manufacturer.
Some customers are surprised at the price of their material choice. The standard pricing method applies dollars per pound by glass type plus additional costs for processing of the shaped raw blanks. Most manufacturers have a current price-by-the-pound list or catalog available.
Comparing the price of various glass types early can avoid sticker shock over a particular choice. As when reviewing product availability, it is wise to list alternate materials chosen by price.
Material quality
Stringent requirements for internal purity and highly accurate refractive index targets can be additional sticking points to fast delivery, as well as adding expense. Standard refractive index and Abbe values are typically advertised by the glass manufacturer and are readily available off the shelf, unlike some of the other tightened tolerances. As the material type, tolerances, and preparation become more specialized, delivery times and costs mount accordingly. Table 1 shows typical refractive index values and how the choices may affect price and/or delivery of the material.
Table 1.
Refractive Index Values and Their Effect on Price and/or Delivery
Custom melted strip glass. Certain materials, such as i-line glasses, are typically special melts and can require months of lead time before the material is shipped from the manufacturer. Courtesy of PFG Precision Optics.
Stain-sensitive lenses. Stain factor is another consideration when choosing glass types. Glasses that are sensitive to environmental factors and chemicals can be problematic to manufacture, which may lead to longer delivery times. Courtesy of PFG Precision Optics.
Material characteristics such as Grade A versus Grade B striae content, for example, can influence the price and availability of some glass types. Higher homogeneity levels than offered by standard catalog values are typically tested from a slab, strip, or individually shaped raw blank. These tighter purity values can contribute to a higher price and take longer to acquire than normal.
Annealing cycles can also extend lead times and should only be called for if required. Materials requiring precision annealing should take priority, as their preparation can require extra months to be cycled and tested.
Table 2.
Stain Ratings for Glass Types
Stain factor is another consideration when choosing glass types. Glasses that are sensitive to environmental factors and chemicals can be problematic to manufacture, which may lead to longer delivery times.
Climatic resistance tests show surface stains on glass samples after the samples have been exposed to high humidity and high temperatures. Stain resistance testing shows the effect on samples of exposure to slightly acidic water, while acid resistance tests measure surface etching of a polished surface after direct contact with more acidic solutions. Alkali resistance can be an important consideration for optics that are likely to encounter cutting coolants; likewise, phosphate resistance is suitable for optics with likely exposure to cleaning solutions.
Some glass types may combine stain resistance for all these conditions. Ideally, the optimal glass would have the lowest stain rating that is still suitable for the application. Examples of stain ratings for select glass types are listed in Table 2. One fast method for identifying the optimal glass for an application is to look for the acid resistance number to be four or lower; the other stain factors will usually scale down as well.
Mechanical values
Knoop hardness values influence the outcome of surface polishing. These values are determined by a hardness test that shows the amount of surface change a material displays after a test diamond is applied to the glass surface with a given pressure and time interval per ISO Standard 9385. Repeated handling and basic cleaning processes of softer materials will increase the probability that they will pick up small scratches or another type of defect during processing. Glasses with Knoop hardness values below 450 are typically considered softer materials. Removal rates for grinding and polishing will be faster for these materials, so close monitoring of their thickness and size is more critical. Hardness comparisons are shown in Table 3, along with glass types that are preferred over others. Hard to moderate materials are usually preferred for manufacture over soft to very soft materials.
Table 3.
Comparison of Glass Hardness Values
Another material quality that can influence the availability, delivery times, and cost of a glass is the coefficient of thermal expansion (CTE). Thermal stability of an optic during manufacture is desirable for optimal processing and handling.
CTE values comprise two scale factors. The first characterizes a glass’s expansion behavior at room temperature when temperature conditions change from –30 to 70 °C. The second evaluates expansion at higher temperature ranges from 20 to
300 °C to provide a standard of comparison for the melting process and for temperature change loading.
CTE values are expressed as 10
−6/K as shown in Table 4. High CTE glass types can be more easily damaged due to thermal shocks and thus may require special considerations at several steps in the value stream. For instance, parts fabricated from high CTE glasses may require additional time to thermally acclimate to a new environment prior to it being tested for surface irregularities. This wait time is often undesirable, but it is required for accurate measurements.
Table 4.
Coefficient of Thermal Expansion (CTE) Values
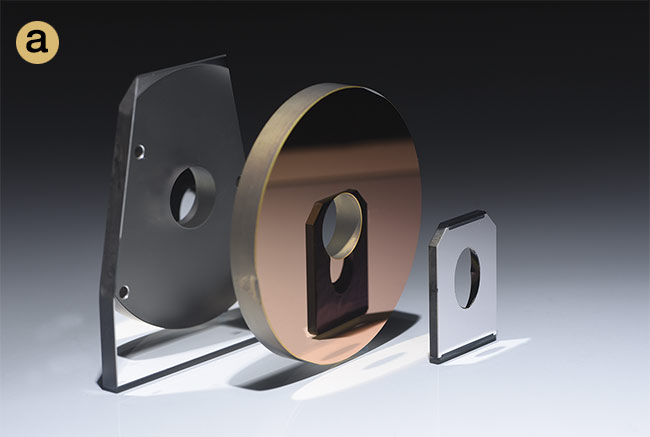
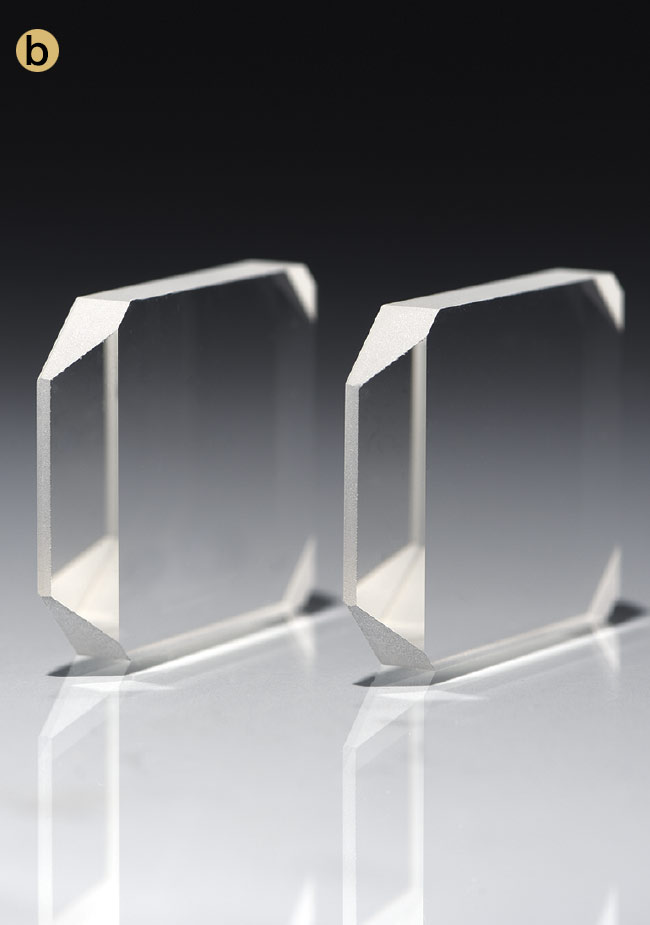
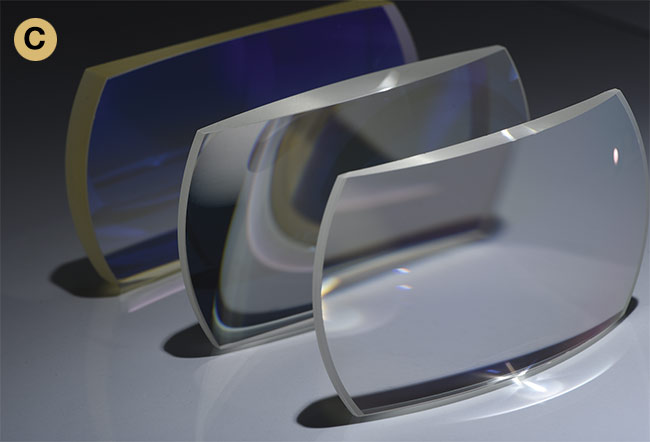
The polishing complexities of intricately shaped parts can extend delivery times for imaging system designers (a, b). Lenses that have notched step cuts in their spherical surfaces (c), or truncated sides (d), can add to cost and should be avoided if not absolutely required by the application. Courtesy of PFG Precision Optics.
Another important consideration arises when using a high CTE lens as part of a cemented doublet. Doublet lenses with mismatched CTEs can lead to cement defects if the doublet is used or tested where thermal swings are involved. If such doublets are tested for thermal shock, they can result in a cracked lens. For mirrors that require exceptionally low expansion, low-CTE-value materials such as fused silica, Zerodur, and Borofloat are used. Low to moderate CTE values are often the best choices for lenses.
Demand for optics with a particular shape can influence polishing times, which have some bearing on the selection and therefore the cost of the raw material used. As an example, the surface flatness of a so-called flat optic is influenced by the shape of the optic. Circular shapes, for example, tend to achieve flatter surfaces than elliptical shapes, and this pattern continues respectively through square and rectangular formats and odd custom shapes such as trapezoids. These unusual shapes can run up the cost of raw materials if purchased as pre-shaped or near-next form blanks. The polishing complexities of oddly shaped parts can
also drive longer delivery, especially if the required flatness is on the order of 1/10 wave or better. Lenses, of course,
are usually circular. But sometimes they have notched step cuts in the spherical surfaces or truncated sides. Some of these features can add to cost and should be avoided if not absolutely required by the application.
Circular optics. The surface flatness of so-called flat optics is influenced by the shape of the component. Circular optics, for example, tend to achieve flatter surfaces than elliptical shapes, and this pattern continues respectively through square and rectangular formats and odd custom shapes such as trapezoids. Courtesy of PFG Precision Optics.
Designs that call for optics that combine one or more of the considerations discussed can impose extreme demands on the manufacturability of the parts. In some cases, there is no way around asking for tighter specifications and specialized glass types. However, examining the choices and determining where flexibility is available in terms of material quality, surface treatments, and chemical and mechanical properties can help designers to achieve goals, as well as lead to more sustainable availability, lower costs, faster delivery, and higher-quality components.
Meet the author
Bill Thames is the senior manufacturing engineer at PFG Precision Optics. He holds a
Bachelor of Science degree in physics from
the University of Southern Mississippi. Thames has over 40 years of experience in manufacturing and testing optics; email:
[email protected].