Full company details
MKS/Newport
8 East Forge Pkwy.
Franklin, MA 02038
United States
Phone: +1 508-528-4411
Fax: +1 508-520-7583
Toll-free: +1 800-598-6783
Reflective Optics Improve in Durability as Applications Increase
Photonics Spectra
Jun 2024Manufacturing trends and product advancements are combined to highlight one of industry’s most versatile and widely used optical components.ROBERT BOURDELAIS, MKS/NEWPORT
The range of optical systems in which reflective optics appear is an appropriate indicator of the importance of these components. Mirrors are ubiquitous in the optical bench setups that enable laboratory research across disciplines. Industrial and health and life sciences applications, as well as large-scale optical systems used for astronomy and high-energy physics, also rely on reflective optics. Reflective optics’ ability to ensure that a system executes its desired function establishes their role as one of industry’s most used optics.
The gold-coated primary mirror of the James Webb Space Telescope comprises 18 individual mirrors. High-reflectivity coatings ensure that reflective optics achieve high levels of
performance — such as enabling the measurement of light from extremely distant galaxies — in the most demanding conditions. Courtesy of NASA/DrewNoel.
In terms of their parameters, reflective optics are also one of the most critical components to optimize for designers and engineers. Users of systems that include these components must be certain that geometries, as well as the selected materials and substrates, align with the target application. When deployed properly, reflective optics cater to diverse applications — both common and cutting-edge — while delivering high performance.
Currently, mirror technology, much like the applications that it supports, is evolving to meet the increasing needs that industrial, aerospace and defense, and consumer applications place on high-functioning optical systems. In addition to new trends, the ongoing innovation in this technology area extends to capabilities and legacy optical systems that are often overlooked.
What is a mirror?
Simply, mirrors are reflective components. Reflection is broadly defined as the change in direction of a wavefront at an interface between two different media, so that the wavefront returns into the medium from which it originated. According to the law of reflection, when a ray of light hits a surface, it bounces in a predictable way. The incoming angle, called the angle of incidence, is always equal to the angle leaving the surface, or the angle of reflection.
Though all mirrors offer reflective capabilities, the type of reflection in a mirror depends on the mirror’s shape and, in some cases, the distance between the mirror and the position of the reflected object. For high-functioning optical systems, the mirrors of choice and those that are used most often, especially for precision optics applications, are “first surface.” These components feature a high-reflectance coating that is deposited
onto the front surface of a variety of
different types of glasses, metals, or
semiconductor substrates.
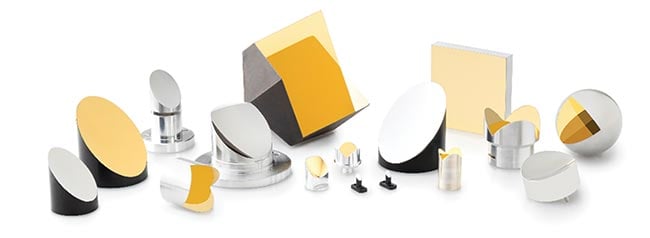
Optimizing parameters such as materials, substrates, and geometries is critical to ensure the desired performance of a mirror, especially in precision applications. Courtesy of MKS/Newport.
Though second surface mirrors can be manufactured using a similar coating technology, the incident light passes through a transparent substrate material before it is reflected by the coating. This geometry helps protect the coating layer from scratches and oxidization but leads to several issues, such as image distortion, that make this type of mirror unsuitable for most applications in precision optics.
Beyond the shape and surface, configuration is another determining factor of mirror performance. Not all mirrors are flat. Since mirrors can be produced in a variety of configurations, they can be used to provide important reflection characteristics that may benefit certain applications. For example, concave mirrors, commonly found in the largest optical telescopes, are used to collect the faint light signals emitted from very distant parts of the universe. The curved surface concentrates parallel rays from a great distance into a single point, delivering enhanced measurement intensity.
Coating considerations
Several factors must be considered to select the proper mirror for an application, including the application itself. Many characteristics of a mirror, beyond purely physical parameters, depend on the optical coating, substrate, and surface quality. Factors that influence the mirror and system performance are coating durability, thermal expansion of the substrate, wavefront distortion, and scattered light. Measures of reflectivity and laser damage resistance must also be considered.
Military and warfighter applications, such as night vision, are among the extreme-environment applications that use mirror and reflective coating technology (above). Courtesy of MKS/Newport.
Mirrors are used for laser-based satellite-to-satellite communications — one of several aerospace sector trends permeating reflective optics technology. Courtesy of MKS/Newport.
Metallic coatings are used in lithography systems that etch precision circuit patterns onto semiconductor wafers. High-reflectivity coatings are also used in semiconductor manufacturing to increase the efficiency of inspection processes. Courtesy of MKS/Newport.
Because the optical coating dictates reflectivity and durability, it is the most critical element that influences how a mirror performs in application. High-performing mirrors are commonly coated with a thin film. These thin-film coatings are typically comprised of either metallic
or dielectric materials, though certain coatings use both types of materials.
Metal coatings consist of thin layers of silver, gold, aluminum, and/or other metals, coated onto the surface of a substrate. The metal layers interact with the incident light, causing it to reflect off the surface. The result is a mirror-like surface that reflects light with high efficiency, which is crucial for applications, such as space communication and semiconductor lithography, that require very precise light control.
In most circumstances, metal coatings are very delicate, especially without the addition of a protective layer. They also require extra care during handling and cleaning; clean, dry air is typically the material that must be used to clean the surface of an unprotected metal coating, though certain contact methods may be acceptable.
Fabricators can overcome this drawback with the application of a dielectric overcoat on a metallic mirror, which allows for improved handling of the component, increases the durability of the coating, and provides protection from oxidation — all without inducing any qualities that could negatively affect the performance of the coating. The dielectric layer(s) can also be designed to enhance the reflectance of the metal coating in specific spectral regions. Isopropyl alcohol or acetone can be used to clean the protected metal-coated mirrors.
Dielectric thin-film coatings consist of a stack of numerous thin layers. Often, the thickness of each one is one-quarter of the wavelength of the material in use. Typically, the layers alternate between two or more materials of varying refractive index.
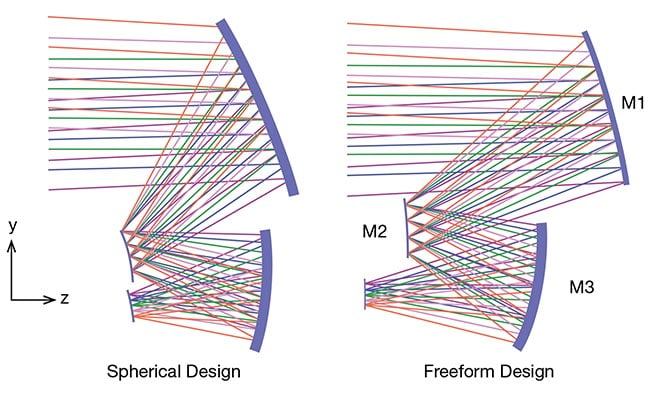
The differences in freeform mirror design compared to the conventional spherical design: A freeform surface lacks rotational and translational symmetry (top). In contrast, spherical surfaces are rotationally symmetric in all axes. Aspheric mirror optics typically have a singular axis of rotational symmetry. Telescopy and space applications are core use cases for reflective optics, such as those used in the James Webb Space Telescope’s primary mirror (bottom). Courtesy of MKS/Newport.
Optical interference is the mechanism by which dielectric thin-film coatings reflect light. Constructive interference of all the reflected light at each material interface combines to yield high reflectance at the desired wavelengths. In fact, the materials themselves may not be reflective at all.
In addition to advantages in durability and accessibility, such as being easier to clean, mirrors with dielectric coatings are also more resistant to laser damage. However, because of their dispersive and predominantly real indices of refraction, dielectric mirrors have a narrower spectral reflectivity and are most often used in the visible and NIR regions. Still, the design of dielectric coatings offers greater flexibility than the design of metallic coatings. Compared with metallic mirrors, a dielectric mirror can offer higher reflectivity relative to certain spectral ranges and can offer a customized, tailored spectral response.
Substrate fabrication
Various techniques are used to apply mirror coatings, and the specific approach is selected based on the required performance of the mirror and the envisioned application. Commonly used techniques include physical vapor deposition, chemical vapor deposition, and sputter deposition. These processes create thin, uniform, defect-free layers of metal on the substrate, enhancing the highly reflective coating on the surface.
Most substrates on which the coatings are deposited are made of dielectric materials, and these substrates control the thermal expansion and transmission properties of mirrors. Certain materials, such as borosilicate glass or fused silica, have lower thermal expansion coefficients than other optical glasses, which, while favorable for certain applications, may not always supersede or outweigh considerations to the cost of the substrate material and ease of polishing, for example. If it is not required to transmit light through the substrate, the back side of the substrate is usually ground to prevent inadvertent transmissions. However, for transmissive
mirrors, a substrate material, such as fused silica, with a homogenous index
of refraction, becomes an important
material.
Reflective optics are typically either directly machined into the substrate using diamond turning or are thin-film coated. Single point diamond turning is the mechanical machining of precision elements using lathes or other machines equipped with diamond-tipped tool bits. Diamond-turned reflective optics may also require post-polishing to achieve the required surface finish. Five-axis diamond turning machines are a relatively recent advancement and have been instrumental in
helping to meet customer demand for freeform products.
Surface roughness measuring <100 Å can be achieved for high-precision diamond turning. With a lower surface roughness, an optic will display minimized scatter in the visible spectrum. However, if an application uses light from the lower end of the visible spectrum, 100 Å may be an unacceptable level of scatter. The roughness of the highest precision diamond-turned components can be brought to <50 Å and can be further improved by post-machining plating.
Mirror substrates can also be ground and polished to a desired shape, either planar or curved. The surface quality and flatness determine the fidelity of the mirror performance, and the target application dictates the requirements for these parameters.
Surface flatness is often specified in wavelengths, for example, λ/10, over the entire usable area of the mirror. In instances in which it is critical to preserve the wavefront, a λ/10 to λ/20 mirror should be selected. Less demanding
applications can tolerate a λ/2 to λ/5 mirror with the associated reduction in cost.
The severity of random localized defects on the surface often dictates overall surface quality, which itself is often quantified in terms of a “scratch and dig” specification. Typically expressed as a numerical set, a lower value — 20-10, for example — indicates improved quality and lower scattering as a result.
For high-precision surfaces, such as those found within the cavity of a laser, a scratch-dig specification of 10-5 may be required. Such a value would yield very little scattered light. Other measurables, such as surface polishing tolerances in terms of irregularity, surface roughness, and cosmetic imperfections, are verified using the latest iterations of advanced metrology equipment. These same parameters and procedures are used to assess the quality and flatness of other optical components, such as lenses or windows.
Driven by application
As much as reflectivity and other design considerations influence mirror technology, the end use or application is typically the core determinant of the type and quality of the mirror found in any system. Several main mirror types, all of which are structured to meet the general yet varying needs of current optical systems, include flat mirrors, off-axis mirrors, Nd:YAG laser mirrors, broadband dielectric mirrors, laser line mirrors, ultrafast laser mirrors, focusing mirrors, infrared mirrors, and hot/cold mirrors. Each option offers distinct advantages for applications spanning industry sectors.
For example, in the health and life sciences market segment, particularly in biomedical technology, metal-coated optical components are found in laser devices used for surgery and diagnostics. For these applications, mirror coatings help to direct laser beams during various surgical procedures. At the same time, high reflectivity coatings enhance the performance of diagnostic equipment, such as microplate readers, Fourier transform instruments, and flow cytometry systems.
In the aerospace/space industry, metal-coated optical components play a similarly vital role. Mirrors are a critical component for laser-based satellite-to-satellite communications. Also, high-reflectivity coatings are used in space telescopes, such as the Hubble, to observe distant astronomical objects. The primary mirror of the James Webb Space Telescope, for example, a collaboration between NASA, the European Space Agency, and the Canadian Space Agency, features an enormous, gold-coated component. The mirror comprises 18 smaller mirrors that allow mission teams to use the scope to measure light from extremely distant galaxies located billions of light-years from Earth.
Reflective components are also embedded in systems that support a range of advanced military technologies in the defense sector. These include tracking and sighting systems as well as other laser systems. Mirror coatings are often used in periscopes, night-vision devices, and laser guidance systems. Such robust metallic
coatings can withstand the rigors of battlefield conditions and provide reliable performance.
The extreme environments encountered in defense applications are not the only ones in which metallic coatings deliver the necessary capabilities for demanding
applications. In the semiconductor industry, metal-coated components are essential for chip production. Specifically, metallic coatings are used in lithography systems that etch small precision circuit patterns onto semiconductor wafers. High-reflectivity coatings are also used to increase the efficiency of the many inspection processes in semiconductor manufacturing.
Trends and markets
Optimized systems reside at the intersection of optical component design and application knowledge. Working with an experienced and knowledgeable optical component partner often yields outsized results, enabling superior systems-level performance.
This dynamic is critical; often, standard catalog mirrors are not sufficient for meeting the needs of highly functioning optical systems. Proper design and application of individual components in an optical measurement system ensure the highest level of instrument performance.
There are other benefits stemming from this intersection. Currently, for example, freeform mirrors are beginning to find use in commercial and lower-cost optical systems that retain high levels of performance. A freeform is a surface that lacks rotational and translational symmetry. As shown geometrically in the first figure on the previous page, this sharply contrasts most traditional optics that employ spherical surfaces — which are rotationally symmetric in all axes (a sphere has no vertex) — and aspheres, which typically have a single axis of rotational symmetry.
This lack of symmetry in a freeform enables more sophisticated control over ray paths than what would otherwise be achievable. This feature allows freeform surfaces to correct aberrations more
effectively than traditional optics, such as the off-axis aberrations that are common in wide-field and high-resolution imaging systems. This capability translates into higher throughput and superior image quality, with increased sharpness and contrast across a wider field of view. Applications from microscopy and spectroscopy to imaging and advanced surveillance are among those that benefit as a result.
The efficacy of freeforms in diverse
applications has contributed to a heightened focus on manufacturing, and replication techniques in particular. Newport uses advanced precision replication processes that center on the use of a high-fidelity master from which exact copies are made at high levels of quality and efficiency. In the replication process, the master is produced with a very high degree of fidelity in terms of overall
surface accuracy and surface roughness. This replication process serves to erase any tooling marks and midspatial frequency surface errors that may be originally present on the replica substrate surface. Typical specifications for these replica parts are λ/8 surface figure and a scratch-dig of 40-20.
The rise of adaptive optics technology is furthering another trend into the realm of reflective optics. Liquid mirrors, which gained favor for their use in telescope systems, are poised to return to mainstream use due to a series of developments that allow them to act like adaptive optics
systems — while bypassing the price tag that is associated with adaptive optics. Using a ferromagnetic liquid, instead of mercury, multiple research groups have demonstrated deformable liquid mirrors.
Adaptive optics use state-of-the-art, deformable mirrors that are governed by computers that can adjust, in real time, for the optical distortion caused by turbulence in the atmosphere to create images of celestial objects. These images are almost as sharp as those captured in space. Adaptive optics enable a reflective telescope to see much finer details than what would otherwise be achievable from ground-based telescopes.
Elsewhere, computer superpolishing fabrication and precision ion beam sputtered technology are increasingly enabling the design of high-energy laser mirrors. These components are designed to provide a combination of high laser damage threshold, ultralow scatter, excellent wavefront performance, and rugged mechanical durability.
High-energy laser mirrors are highly reflective and environmentally stable.
As a result, they are used in demanding applications, such as military targeting and micromachining, industrial materials processing systems, intracavity lasing, and high-energy research lasing. Mirrors used in the Advanced Photon Source (APS), for example, face the most demanding conditions in the world. To preserve the qualities of the beam, the mirrors must be almost perfectly smooth. This requirement exceeds traditional
mechanical chemical polishing and necessitates that atoms are removed from the mirror surfaces one by one.
High-energy laser mirrors are custom
fabricated and coated with typical specifications of >99.5% reflectivity, λ/20 flatness (measured at 633 nm), and a scratch-dig of 10-5. In the case of the mirrors used in the APS, only a handful of companies currently manufacture these optics.
One of the most active areas of product development involves multispectral
narrowband and broadband (UV through IR) applications, such as fluorescence and spectroscopy. Broadly speaking, markets such as biomedical instrumentation and semiconductor processing are fueling the use of the UV spectrum. The nature of UV applications has changed dramatically during the past decade, primarily due to the availability of higher-power light sources at shorter wavelengths. The result is a wave of product development in UV reflective optics that relies on the latest design, analytical, and production techniques to optimize performance.
Designs for these UV applications can either be refractive (lens-based) or reflective (mirror-based), though reflective systems are drawing more interest. Reflective systems are fully chromatically corrected by nature, making them a cost-effective option for extremely broadband transmission. A drawback is that these systems can correct for only small angular fields.
Meet the author
Robert Bourdelais is senior global business manager for MKS/Newport. He has more than 30 years of industry experience, including in engineering, R&D, operations management, and product management. He is also the author of more than 200 issued patents; email:
[email protected].